Handling and recycling 3,000 pounds of aluminum chips daily is a big task for most precision machining operations. For many, it’s a back-of-the-plant operation that’s a messy inconvenience with limited payback for the recycled chips. It often doesn’t get the attention it deserves because it contributes little to a company’s bottom line and is mostly a housekeeping chore. Until now, that is, for one Minneapolis company.
Production Engineering Corp., based in Minneapolis, and a growing number of the company’s peers have embraced new chip recycling technology and the role that chip production plays in the manufacturing process.
"For Production Engineering, the 1.5 tons of chips we generate daily are an important by-product of our manufacturing operation," says Clint Emmert, vice president of manufacturing for the company. "No longer considered scrap and certainly not waste, we handle these chips judiciously as a serious profit center."
The precision parts manufacturer has taken steps to recognize chip handling and recycling as an extremely important function of the entire manufacturing process. The importance is not just in the added value for the aluminum briquettes it generates, but also in a number of better manufacturing practices Production Engineering now adheres to that indirectly adds more profit to its bottom line.
WHEN THE CHIPS ARE UP
Production Engineering Corp. is one of the originators of the Midwest’s precision machining industry, starting in 1957 to serve the needs of an emerging computer industry and quality conscious defense contractors. Today, the company is a leading provider of complex precision parts for the military and aerospace industries.
Production Engineering views its aluminum chip generation, handling and disposition as a key revenue factor in the projects it handles. To be as competitive as possible, this facet of the company’s business gets priority attention on an ongoing basis, according to Emmert.
"We’ve always been very conscious of the chips we generate because by the nature of our projects, we do a lot of metal removal," Emmert says. However, the company began to pay more attention to this area in the last two years as the cost of aluminum soared and scrap paybacks didn’t always keep pace, Emmert says.
Minneapolis-based Kurt Manufacturing approached Production Engineering at that time with its new chip recycling technology, the Kurt Chipmunk Chip Compactor.
"Looking back, a new era was beginning for companies like ours generating aluminum chips, not just because their value was increasing, but also because new technology was being developed to meet those needs plus all of the emerging environmental and worker safety issues that had to be addressed as well," Emmmert says.
RAISING THE STAKES
"We were being paid a flat rate per pound for our aluminum chips," Emmert says, "which was customary for precision machine operations such as ours. Our scrap dealer picked up our wet chips in barrels every day and paid us by the pound. However, we heard how Kurt Manufacturing improved its method of dealing with aluminum chips and its new Chipmunk compacting system, so we had them pay us a visit to discuss options."
Chip compacting and recycling has been around for decades. It’s a process that has appealed primarily to larger machining operations, but has received more attention lately from mid-size and smaller operations because the value of aluminum has increased dramatically.
"Kurt told us how it had realigned its own chip processing operations by compacting chips and removing coolant from them on a big heat sink job they were machining," Emmert says. "Like us, Kurt previously handled its aluminum chips by loading them up in luggers and having a nearby scrap dealer haul them almost daily. Payment was made at a flat rate, by the pound, and not at prevailing market rates that were traceable. Plus they were being penalized on the scrap price because the chips were wet with machine coolant that had to be removed before the smelting process could begin. There was also a $90-per-trip charge," he adds.
As Kurt demonstrated to Production Engineering, when the company began its own chip compacting and coolant removal operation, it gained $180 per hour in higher profit yield for the compacted chips vs. the loose material. The company also reported saving $8,000 per month in coolant costs by recovering, filtering and reusing its coolant.
Kurt studied the precision machining market and saw that only a small percentage of machine shops like Production Engineering were compacting chips, and those that were did not always employ a cost-effective method. Kurt says it recognized this opportunity and focused on developing new chip compacting technology based on its own experience rather than replicate what was already being sold to the market.
NOTING THE DIFFERENCE
"The big difference we saw with Kurt’s Chipmunk compactor over what was out in the market was its simplistic design and its kinetic energy drive, which produces a very high 8-to-1 compaction ratio," Emmert says. "We wanted to produce the densest chips possible for the best payback and lowest cost of operation, so the density quality of the briquettes was very important to us. Plus the Kurt Chipmunk itself was a high-volume machine for its compact size and was simple and easy to operate, and we were confident in Kurt’s service support since we used its Anglock vises for many years."
Kurt Manufacturing claims the Chipmunk can compact chips more consistently and efficiently than conventional hydraulic compactors that require twice the horsepower. It has a single auger feeding design that operates from a powerful, but simple, compression plate that forms and compresses the wet chips into 3.5-inch-by-1.25-inch continuous extruded briquettes. The Chipmunk uses a power-saving 30-horsepower main motor that is about half the size required in conventional compactors, which often produce less than half of the Chipmunk’s output. Also, this patented compactor design wrings out up to 98 percent of residue coolant, producing neat, firm briquettes that are dry to the touch and require no further coolant removal. The recovered coolant collects in a separate reservoir at the base of the Chipmunk system, ready for filtration and reuse. According to Kurt Manufacturing, the Chipmunk has a payback of one year or less on most installations.
STREAMLINING OPERATIONS
"Upon arrival of the new Chipmunk compactor, we partnered with a new local recycler and changed our entire method of chip pickup, weighing and payment," reports Emmert. Instead of 55-gallon barrels, he says the new recycler provided Production Engineering with Gaylord boxes measuring 40 inches by 48 inches by 48 inches, accommodating 3,000 pounds of compacted briquettes. "The empty boxes are delivered to us in a truck trailer that is left parked at a loading dock in the back of our plant," Emmert says. "The Chipmunk compactor is located near that dock. As chips are produced in our various machining centers, they’re immediately placed in movable carts that hold a cubic yard of chips and are lined up for loading into the Chipmunk compactor. It takes just a few minutes to load a day’s worth of chips, which are compacted into briquettes long before the shift is over that day."
He adds that once the compactor’s hopper is loaded, the system operates unattended, automatically filling each Gaylord with dense, dry briquettes. "When a Gaylord box is filled, it is weighed and then loaded into the truck trailer. An empty box is substituted for it, with the process repeated until the trailer is filled," Emmert says.
This process really is much more efficient than the old method, according to Production Engineering. A fork truck stacks the fully enclosed briquette-filled boxes neatly inside the trailer. When filled, a replacement trailer load of empty boxes is delivered, and the full trailer is driven to the recycler. None of the chips accumulate inside Production Engineering’s facility, either on the plant floor or at the back of the plant. All chips are processed through the Chipmunk compactor the same day they are generated, and the recovered coolant is filtered and readied for reuse. This new method eliminates any chance of wet chips draining coolant onto the floor or parking lot surfaces that could necessitate cleanup.
"When the recycler receives the trailer full of loaded boxes, they are emptied and the briquettes are weighed as a unit," Emmert says, "We know ahead of time what each full box of compacted briquettes weighs, give or take a few pounds, so there are no ‘short weighing’ problems. A settlement report and check is sent to us by mail based on market prices for compacted 6061 aluminum chips every 30 days," he continues. "The settlement report is verified against the weight of briquettes sent out to make sure we are getting full credit."
The trailer pickup/drop-off cycle—filling a truck and then starting over with an empty one—typically occurs every 15 days. Emmert says, "There is no deduction for coolant residue in the briquettes because it’s all been removed." In fact, the recycler only charges Production Engineering $90 for pickup of each trailer load, he says.
"We improved the sale of our aluminum chips on average by 10 cents a pound using the Kurt Chipmunk compactor," Emmert says. "At 3,000 pounds of chips a day, that’s very important to our profitability. And the higher return gets better as the price of aluminum increases. However, our using the Chipmunk system is as much about improved plant processes as it is about getting more money out of scrap dealers."
Emmert continues, "Having a rigid, flow-through process for chip handling improves a lot of things. Our workers, for example, understand that chips are a by-product and must be treated with as much care as finished parts. Nothing is wasted or discarded. All chips and coolant are saved."
The Chipmunk system takes up no more space than a standard-sized machining center and certainly less space than the old barrel method of accumulating chips required, he says. "Everything is a lot neater and cleaner. We’ve always had clean floors, but now we have immaculate floors with not a trace of spilled coolant or stray aluminum chips," Emmert says.
"Floors are coated with a high gloss sealant making them very attractive and non-slip, so they’re safer and easier to keep clean," he continues. "Also, our customers appreciate top-notch housekeeping because they know it contributes to a more positive worker attitude that contributes to quality and efficiency."
This feature was submitted on behalf of Kurt Manufacturing, Chip Solutions Division, Minneapolis. The company can be contacted through its Web site at www.kurtchip.com.
Get curated news on YOUR industry.
Enter your email to receive our newsletters.
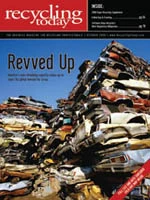
Explore the October 2008 Issue
Check out more from this issue and find your next story to read.
Latest from Recycling Today
- CP Group announces new senior vice president
- APR publishes Design Guide in French
- AmSty recorded first sales of PolyRenew Styrene in 2024
- PRE says EU’s plastic recycling industry at a breaking point
- Call2Recycle Canada, Staples Professional expand partnership
- Circular Services breaks ground on north Texas MRF
- Tariff uncertainty results in choppy nonferrous scrap flows
- CATL, Ellen MacArthur Foundation establish battery partnership