
Quality counts, particularly in rubberized asphalt applications that use recycled rubber. The ability to provide a fine, high-quality terminal blend material opens the door to marketing to a range of highway engineers who require something better than the typical site blend.
State Rubber & Environmental Solutions recently upgraded its processing system to allow it to produce high-volume, high-quality recycled crumb rubber for use in terminal blend rubberized asphalt (RA). In doing so, the company has broadened its footprint.
“One of State Rubber’s strengths is the ability to custom manufacture specific crumb rubber blends for the various asphalt design mixes used by most states, as well as several other products’ specifications,” says Jerry Woosley, vice president of the Denver City, Texas, company.
State Rubber was born of the need of tire dealers in west Texas and eastern New Mexico to dispose of scrap tires. Today, about 90 percent of the plant’s production goes to RA. With the price of oil being low, Woosley says he expects the demand for rubber modified asphalt products to increase accordingly.
“State agencies will want to take advantage of cheaper asphalt prices,” he says.
Texas and New Mexico currently are using rubber-modified asphalt in various applications in the states’ highways.
A New Mexico task force studying RA in 2009 strongly recommended that a scrap tire processing operation be developed in the state. It pointed to the benefits of eliminating the growing stockpiles of tires dumped or landfilled. It encouraged assistance from the New Mexico Economic Development Department in this endeavor.
New Mexico developed specifications for several tire-rubber-modified asphalt products for use in its roads.
Texas has used crumb-rubber-modified asphalt in terminal blend and wet process applications, including chip seal, fog seal, crack seal and hot-mix, for many years.
State Rubber has been expanding its production capabilities over the past five years. That expansion is projected to culminate in a doubling of the plant’s original production capacity over the next three years, according to the company.
“Our plan is to increase the capacity of the plant to meet a slow but steady increase in crumb rubber sales,” Woosley says.

State Rubber has two main seasons. In the winter months, the company accumulates material. In the summer months, prime highway construction season, State Rubber ships its crumb rubber for RA like there is no tomorrow. Its challenge is to accumulate enough material from roughly November until April to allow it to keep up with demand through the summer months.
Most systems to produce crumb rubber from used tires are either three-stage or four-stage plants. State Rubber uses a four-stage process that allows the company to produce a consistent, high-quality product of the size required for terminal blend, which is less than 40 mesh.
A LOOK AT THE PROCESS
“Our expansion began downstream and is progressing upstream to the granulator and will culminate with the addition of a second mill line,” Woosley says.
The expansion began by addressing material screening and storage. “We knew those would have to be in place to accommodate added production,” he says.
State Rubber currently is designing the granulator phase of its expansion. It will incorporate a Super 80 Grizzly manufactured by Granutech Saturn Systems, Grand Prairie, Texas.
While many tire processing facilities sort and sell used tires as an additional revenue stream, State Rubber has chosen to forgo the liability and the added expense of sorting to focus on providing a clean crumb rubber product instead.
The plant is divided into four size reduction processes and their related support equipment, starting with a twin-shaft hybrid-drive shredder.
That primary shredder is a 72-44-BGHT Saturn shredder that was modified to include a direct-drive power unit to increase the machine’s performance. Whole tires are reduced to chunks roughly the size of a fist, or a 4-inch-nominal chip, in this process and are conveyed into a walking floor bin to supply the secondary process.
Next, a Granutech Grizzly M-80 performs primary granulation. The M-80, which features 300 horsepower at 320 rpm, will take material down to the ¾-inch or 5/8-inch chip at the rate of up to 5 tons per hour. As the material exits the machine, it passes along a wire reclaimer and is conveyed to a walking floor.
The Grizzly performs the bulk of the required wire separation and some fiber removal. State Rubber also will recycle the steel fraction.
Secondary granulation is accomplished with a G-3 granulator. Material is reduced to ¼-inch minus (less than 0.6 millimeters) in this phase of the process. The 200-horsepower, 1,800-rpm Granutech G-3, with its two fly knives and three bed knives, is the key component in producing high-quality, fine rubber, according to State Rubber. At this point, residual steel is removed and almost all of the fiber is separated using air and screeners so it does not show up in the powder. The ¼-inch material is then conveyed into a storage bin.
The fourth and final size reduction system is a Refiner Mill and a closed-loop system that will process, clean and classify the crumb rubber before sending the material to a bagging system for packaging. Material can run through an 18-to-20-mesh screen or down to a 30-mesh screen. All of this runs at warp speed and still maintains specifications, according to the company.
It is not unusual for State Rubber to produce 40-mesh size, and some of the material produced can be as fine as an 80 mesh for specialty operations.
TIGHT TOLERANCES
At State Rubber, the upgraded tolerance requirements required for crumb rubber for use in RA applications put a double burden on the machinery.
While most size reduction mills at tire recycling operations use roller bushings, those at State Rubber have been replaced with roller bearings. This allows operations at tolerances down to 0.0025 inches versus 0.005 inches, or five times tighter than those with bushings.
Bearings have the advantage of producing less heat than bushings, and therefore can use captured greasing system to keep things cool without constant concern about lubrication.
The design change has been successful for State Rubber, the company says.
Granutech is expected to change future mill models to use bearings rather than bushings. Look for an announcement on this topic at the Institute of Scrap Recycling Industries 2016 Convention & Exposition in Las Vegas April 2-7.
State Rubber says it is pondering a move to a Granutech Saturn Systems Super-80 grinder that would allow the company to further expand processing, doubling its output.
BRIGHT FUTURE
One cloud associated with RA is cost. A New Mexico study found RA products tend to be more costly than traditional asphalt, with material and application costs varying from 10 percent to 16 percent higher. However, the same study’s life cycle cost analysis shows that Arizona, Texas and California realize greater efficiency in meeting comparative costs as a result of economies of scale.
Market generation by major asphalt users, such as state departments of transportation and larger municipalities, could produce similar economies-of-scale savings, the study group says.
Los Alamos County, New Mexico, trucks scrap tires to State Rubber for recycling at a cost of $1.50 per tire. The county passes that fee onto customers at its solid waste facility. The county recycles approximately 80 tons of tires per year.
Other communities in New Mexico also recycle tires at State Rubber at costs ranging from 82 cents to $1.41 per tire, depending on the number of tires recycled and the method of transport.
The New Mexico Department of Transportation Rubberized Asphalt Task Force felt strongly that the benefits of recycling should be factored into the overall cost of the use of RA. This adds to the appeal of RA’s performance and reduces long-term maintenance costs.
While highway asphalt products markets fight pricing issues, Woosley says the turf and playground markets have been under assault from news media and governmental agencies over the safety of crumb rubber use in those surfaces.
“If crumb rubber were toxic, then the millions of pounds of rubber worn off of tires on United States highways each year would be devastating to all of our health,” Woosley says. (While “white line fever” might be a staple of country songs, it certainly is not a tire-caused disease sickening drivers.)
State Rubber has a solid supply chain furnishing it with used tires. The company has placed 140 containers within a 300-mile radius of its plant for tire collection at landfills and at tire dealers of various sizes. It also has several transporters who haul tires they collect to its facility.
The entire chain—from suppliers through processing to highway departments—is based on sourcing, producing and paving with a high-quality RA product.
With its expanded processing line, State Rubber & Environmental Solutions says it is well-positioned to meet the needs of RA producers for the future.
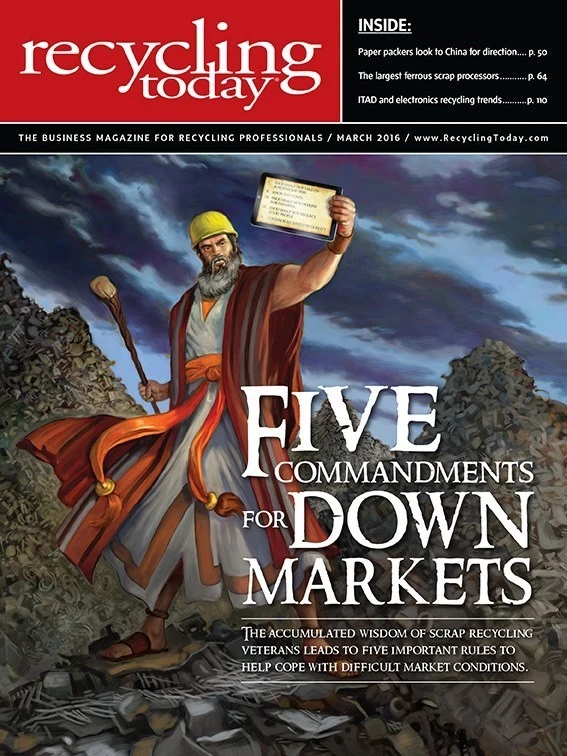
Explore the March 2016 Issue
Check out more from this issue and find your next story to read.
Latest from Recycling Today
- Nucor receives West Virginia funding assist
- Ferrous market ends 2024 in familiar rut
- Aqua Metals secures $1.5M loan, reports operational strides
- AF&PA urges veto of NY bill
- Aluminum Association includes recycling among 2025 policy priorities
- AISI applauds waterways spending bill
- Lux Research questions hydrogen’s transportation role
- Sonoco selling thermoformed, flexible packaging business to Toppan for $1.8B