
Mexico’s Corporacion Durango operates in two geographic regions (Mexico and the Southwestern U.S.) where harvested timber is a relatively rare commodity.
For this reason, the paper and box making company has worked hard to tap into the "urban forest" of secondary fiber in both nations.
In the United States, the Durango McKinley Paper Co., acquired by Durango in 1997, operates three recycling plants that help provide fiber to one Durango McKinley mill in the United States as well as send additional fiber to mills in Mexico.
Durango McKinley Paper’s three U.S. plants have recently been combined with Durango’s FMT (Fiber Management of Texas) fiber trading operation to help both Durango subsidiaries maximize their ability to collect fiber and supply it to their family of mills.
NORTH OF THE BORDER
In the years following the North American Free Trade Agreement (NAFTA), the most common form of cross-border investment involved American-owned companies establishing increased operations in Mexico.
But commercial opportunities created in the post-NAFTA environment have not been a one-way street.
Mexico’s Corporacion Durango (formerly Grupo Durango) purchased the McKinley Paper Co. in 1997, acquiring a containerboard mill in Prewitt, N.M., and a small network of recycling facilities. Additionally, Durango has also purchased box-making capacity in the United States, including a plant it owns in Mesquite, Texas.
Corporacion Durango, based in the Mexican city and state of Durango, has significant market share in that nation, with seven mills producing a variety of finished paper.
Throughout most of the post-McKinley buyout period, the U.S. recycling plants worked separately as part of Durango McKinley Paper Co. (with a focus on supplying the Prewitt, N.M., mill), while the FMT trading division would source secondary fiber from within North America to ship to Durango’s mills in Mexico.
Frank Sanchez, GM of fiber operations for the newly combined FMT and Durango McKinley Recycling divisions, says the Albuquerque, N.M., Phoenix and El Paso, Texas, recycling plants provide nearly 60 percent of the furnish needed for the Prewitt mill.
At a Glance: |
KEY MANAGERS: Pule Calderon, president; Mark Mikkelsen, vice president for commercial operations; Frank Sanchez, GM for fiber operations; Ricardo Isaac, business development manager; Rogelio Silva and Sofia Welsh, procurement managers; Martha Reyes, Cliff Roberts and Carlos Ruiz, plant managers. LOCATIONS: Containerboard mill in Prewitt, N.M. Recycling plants in Albuquerque, N.M.; Phoenix; and El Paso, Texas. Trading office in Arlington, Texas. Transloading facility in Rio Grande City, Texas, for cross-border fiber shipments. Box plant in Mesquite, Texas. Parent company Corporacion Durango operates seven paper mills in Mexico. NUMBER OF EMPLOYEES: Approximately 40 at U.S. recycling plants; another 110 at Prewitt containerboard mill; 160 at McKinley Container in Mesquite, Texas. PRODUCTION EQUIPMENT: Sorting systems at the Albuquerque and Phoenix plants; horizontal auto-tie balers at all plants, as well as vertical balers distributed to key customers. SCRAP GRADES PURCHASED: Specialize in OCC, ONP, mixed paper, SOP, SWL, MWL and DLK to furnish mills in the United States and Mexico. Also handle and broker additional fiber grades and some types of plastic scrap. |
That mill, he notes, runs entirely on old corrugated containers (OCC) and needs about 20,000 tons per month.
Additionally, the U.S. recycling plants send fiber to four of the seven Durango mills in Mexico, according to Rogelio Silva, a procurement manager for the company. Two containerboard mills in Mexico (one in Monterrey and one in Durango) run entirely or predominantly on the OCC grade, while a mill in Veracruz produces printing and writing papers using a combination of old newspapers (ONP), sorted office paper, sorted white ledger and manifold white ledger. The fourth Mexican mill that accepts secondary fiber is in the Mexican state of Oaxaca and has two paper machines: a newsprint machine that is fed with ONP and rolls and a kraft grocery bag machine that accepts the DLK grade as part of its furnish.
With one very productive mill in the Western United States and four equally productive mills in Mexico, the fiber procurement specialists of Durango McKinley Paper Co. operate with a sense of dedication to keep the mills supplied.
CLEAN AND TIMELY
The challenge for the traders and plant operators extends beyond acquiring adequate volume. As suppliers to a mill company, the recycling plants are reminded daily that the mills they serve expect clean loads with minimal contamination. Additionally, the Prewitt mill operates on a "just-in-time" inventory basis, meaning deliveries promised must be shipped on time.
"We need to be juggling different factors," says Silva. "In addition to the quality of the fiber and the timing needed to get it to the mills, there are also freight rates and the factor of cost. Our job is to get supply to the mills in sufficient volume, in a timely manner with the correct quality at the proper cost."
The good news for Corporacion Durango is that its staff members have been working hard to meet all of these objectives. Its Phoenix recycling plant is handling about 5,000 tons per month, with some 4,400 of those tons being OCC, according to plant manager Cliff Roberts.
In Albuquerque, two sorting lines help that plant ship about 4,000 tons of OCC per month to the nearby Prewitt mill, part of a total of 4,500 tons per month of secondary fiber and other recyclables handled at the plant, Plant Manager Martha Reyes says.
The newest Durango McKinley Recycling plant is in El Paso. "We started six years ago and in the first month handled only 700 tons of material," recalls Plant Manager Carlos Ruiz. "But we’re now handling 4,100 tons per month, with basically 90 percent of our production being OCC for Durango mills."
Obtaining adequate volume in Albuquerque is especially critical, says Sanchez. "This plant is basically the inventory depot for our Prewitt mill, because it is only about 90 minutes away," he says. "The recycling plant in Albuquerque has the capacity to hold up to 8,000 tons of OCC in storage."
The El Paso plant does not have automated sorting equipment, but its rich yield of cardboard comes in largely from clean industrial and commercial sources. The industrial sources along the U.S.-Mexico border are particularly valued, according to Procurement Manager Sofia Welsh, who says the long fibers help improve the pulping yield at the Prewitt mill.
PATHS TO GROWTH
Although the need to find furnish for hungry paper mills could be seen as a burden for Durango McKinley’s procurement and plant managers, it also means that there is an organization behind them willing to lend support.
The need to act as the purchasing arm for the larger paper company is one of the two engines driving Durango McKinley Paper’s growth.
"The concept of a mill group having packing plants for its internal consumption is not a new or unique idea," acknowledges Sanchez. "However, as far as I know, we’re the only mill group that has its own internal packing operations providing 60 percent of its furnish," he adds.
Maintaining or building on the figure will be difficult, say Durango’s managers. "Growing the tonnage in the U.S. will be a challenge for FMT. To be more effective in purchasing the tonnage, we are currently buying closer to the border, minimizing our freights and reducing levels in the ladder of supply, "says Silva.
And getting more tonnage through Durango’s existing recycling plants in the United States may also prove difficult. "In the last few years, we’ve seen a lot more Pacific Rim buying in our markets," notes Roberts. "They’ve been very consistent buyers, and we’ve even seen Pacific Rim companies building or funding packing facilities in the Western U.S."
Ricardo Isaac, business development manager for Durango McKinley Paper Co., is conducting research to see whether additional plant locations in the Western United States will be feasible. "I am doing research in certain areas to see whether new locations can make sense, and ideally the research will yield new plants similar in size to the ones in Phoenix, Albuquerque and El Paso," he says.
As recyclers seem to inevitably find, another way to spur growth and to better serve generating customers is to handle additional materials. Even though the Durango mills require a limited range of secondary fiber grades, the recycling plants have begun to cultivate business in other areas.
"We have certainly expanded into other commodities, including plastics," says Sanchez. "We are looking at developing a brokerage arm to help market the portion of the 60,000 tons per month of materials we handle that do not go to our own mills."
Sanchez acknowledges that the company’s recycling plants that have always had a mixture of different priorities are now also faced with having two important philosophies. "We are always encouraged to provide manageable tons to our own mills, but we are also very much looked at as a profit center, to create revenue streams from other materials."
Although the challenges and priorities may seem intimidating, Durango’s managers are confident in regard to the future.
"This combination of facilities is generating leverage and it’s generating brokerage opportunities. We have all sorts of operating efficiencies between Mexico and our packing plants here and we see that growing. It’s all very exciting," Roberts says.
The author is editor of Recycling Today and can be contacted at btaylor@gie.net.
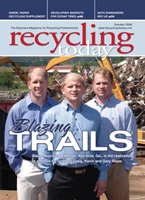
Explore the October 2006 Issue
Check out more from this issue and find your next story to read.
Latest from Recycling Today
- CP Group announces new senior vice president
- APR publishes Design Guide in French
- AmSty recorded first sales of PolyRenew Styrene in 2024
- PRE says EU’s plastic recycling industry at a breaking point
- Call2Recycle Canada, Staples Professional expand partnership
- Circular Services breaks ground on north Texas MRF
- Tariff uncertainty results in choppy nonferrous scrap flows
- CATL, Ellen MacArthur Foundation establish battery partnership