The finer points of tuning up an engine until it is just right are as well known in the Detroit area as probably anywhere else in the U.S. The cradle of the automotive industry has also turned out to be a pioneer in northern U.S. single-stream recyclables processing, thanks to Great Lakes International Recycling, Roseville, Mich.
Sandy Rosen, a vice president with the company, notes that when the company installed its single-stream processing system three years ago, it was one of the first to do so away from the West Coast, and probably the first in a place with a harsh winter climate.
Although some experimenting and tuning up has had to take place, Rosen says the company is proud of the marketable paper grades and other products leaving its highly-automated plant, and its future plans call for even further processing automation to handle curbside recyclables collected in traditional compactor refuse trucks.
MAKING THE SWITCH. Great Lakes International Recycling and the Rosen family have secured a multi-faceted place for themselves in the metro-Detroit recycling industry. When the company installed its system to sort single-stream curbside recyclables in 2000, it marked the most recent of several stages for the company.
BEYOND CALIFORNIA |
The days of considering single-stream processing a West Coast phenomenon might be well past, considering the experiences not only of Great Lakes International Recycling in Michigan, but also the recycling program in Grand Forks, N.D. Residents in the Grand Forks region, which straddles the North Dakota-Minnesota border, are among the latest to be part of the single-stream trend, according to a news item earlier this year in the Grand Forks Herald. Households in the region that are served by Waste Management Inc., Houston, have been encouraged to switch to single-stream collection by the company, which forwards the material to its Minneapolis materials recovery facility (MRF). According to the news report, local Waste Management Inc. manager Mike Miller urged the adoption of the method to make recycling easier for residents and to increase the overall volume of material heading to the MRF. The City of Grand Forks council also spurred the single-stream development by strongly urging Waste Management to find ways to improve the curbside participation rate by 6.6 percent or risk a switch to a drop-off program. The switch to single-stream processing will mean the end of any sorting done by Waste Management in the Grand Forks region, as all recyclables will be shipped "as is" to the 118,000-square-foot Minneapolis MRF for automated sorting. The unsorted recyclables will face a long haul from Grand Forks to Minneapolis, but increased collection of materials that are easy to recycle for residents (because of less source separating, less label peeling and less rinsing out) should make the longer trip worthwhile for packer trucks. In this scenario, the residential recyclables can also be combined with commercial paper grades picked up for recycling by Waste Management from commercial accounts in the Grand Forks region. |
For several decades, the late Burt Rosen ran the operations at Great Lakes and helped turn the company into one of the Detroit area’s foremost paper recyclers. After Burt’s death in 1992, the company’s reins were handed to Burt’s brother Ben and Ben’s son Sandy Rosen.
Ben, who is now semi-retired, and Sandy, who has a background in computer science and business administration, have helped build the company’s business not only in the paper recycling industry, but also in the scrap metal markets; as a wire, cable and electronics recycler; and as a recycler of containers and other commodities collected curbside.
The company’s operations have branched out into several buildings to form a veritable recycling compound in Detroit’s northern suburb of Roseville. Among the activities at the complex:
• The paper operations remain the largest in terms of volume. The company has a rail spur that includes an indoor section where two cars can be loaded at once. There are also 13 truck loading docks at the 70,000-square-foot paper and mixed municipal commodities recycling plant.
• A 25,000-square-foot building houses metals recycling operations, where the focus is on nonferrous metals. This building was constructed in 1999 and features two truck wells and six other doorways where trucks can be loaded. An adjacent 10,000-square-foot building hosts wire and electronics recycling operations.
• Another building, located across a set of railroad tracks from the other Great Lakes operations, shreds steel and urethane foam products such as automobile seats. The company ships the clean steel as a ferrous grade and the foam is baled and shipped for use as carpet padding feedstock.
While many of the company’s goals have involved expanding into additional recycling markets, in terms of pure volume, the company’s installation of sorting and baling equipment to handle the curbside stream has been a point of emphasis.
THROUGH THE LOOP. Technically, Great Lakes operates a mixed recyclables materials recovery facility (MRF) separately from an adjacent paperstock recycling plant. But the two facilities literally work in tandem thanks to a conveyor system that brings paper grades from the MRF over to the paperstock plant.
Much of the material running through the paperstock plant is tipped separately and never sees the inside of the MRF. Most of this material is from corporate, commercial and industrial accounts served by Great Lakes, and much of it is separated at its source by paper grade.
Incoming material is pushed onto a pit conveyor and either diverted to a sorting system or led directly to a high-volume Bollegraaf 110F baler.
Material that needs further sorting runs by a five-person sorting line whose pickers can pluck out contaminants and brown grades that need to be removed to produce a high-grade stream of recovered paper.
Most material also passes over a Lubo StarScreen. This "fines" screen sifts out dirt and grit from the feedstock so that baled paper grades can meet the quality expectations of consumers.
At the same time the Great Lakes paperstock facility is receiving commercial loads in one tipping area, another conveyor coming from a second tipping floor is bringing in old newspapers (ONP) and other grades from the MRF next door.
The MRF, equipped with a system designed and installed by CP Manufacturing, National City, Calif., has been designed to sort and process commingled, single-stream material, often collected in packer trucks.
According to Sandy Rosen, the system has been designed to be at its best when loads are thoroughly mixed, as the combination of mechanical and manual sorters are accustomed to handling mixed loads. In fact, when material coming from drop-off boxes makes its way onto the line, it can overwhelm parts of the system, while others may perform below capacity.
The system’s initial tasks include using hand sorters to remove brown grades before disc screens separate paper from containers. The discs in the screen are configured to cause paper to "peel" forward while containers tumble backward for additional separation. This initial sorting step is 99 percent successful, says Rosen.
After passing through fans and blowers and a final inspection station, the resulting paper stream is a number eight ONP grade.
The containers travel through a separate process that includes a trommel screen, which is used to separate crushed glass from the plastic, steel and aluminum containers.
Magnetic and air separation systems, as well as quick and accurate hand sorters, help further separate this stream by its steel, aluminum and numbers one and two plastic component parts.
The company is in the process of installing further automation steps to upgrade its plastics and glass output in particular, says Rosen. CP Manufacturing, the company that designed its single-stream MRF, has recently acquired MSS Inc., a maker of automated optical sorting equipment that can be used to separate plastics by color and resin and other materials by color as well.
Currently, the resulting glass product at Great Lakes is clean enough to go to a glass processor for eventual shipment to the cullet market, says Rosen, while the resulting paper grades are clean enough to avoid rejection and downgrades, which single-stream detractors say can be the result of single-stream processing.
"I have seen broken glass on sort lines at dual-stream plants," notes Rosen. "The difference in single-stream is that the paper separation process makes it virtually impossible for any glass to remain in the paper stream." This can differ from dual-stream plants, he adds, saying that in a dual-stream paper mix, "once broken glass gets in the paper, it has no opportunity to get out."
MEETING VOLUME GOALS. For many paper recyclers, entering the curbside fray can be daunting. But, as Great Lakes has learned, tapping into this market can help add critical volume to one’s shipments.
Sandy Rosen estimates that ONP shipments now comprise about one-third of its overall paperstock business, split evenly with OCC and with high grades collected from commercial accounts.
Successfully procuring this household-generated material has been critical for Great Lakes to secure the volumes necessary to compete in a consolidating paperstock marketplace.
The company receives much of its material from the solid waste and recycling companies that serve Detroit’s suburbs—even from those companies that may operate their own MRFs in cases when the Great Lakes MRF makes the most sense logistically.
As somewhat of a cold weather pioneer in the single-stream arena, the company had a few trial-and-error incidents concerning its operations.
A spray-mister is used to ensure that there is enough friction to keep materials moving forward over the rubber discs of the screen when mixed recyclables first enter the MRF. The volume of water emitted, however, must be adjusted depending on the moisture content of the recyclables entering the stream. (Recyclables picked up on a rainy day, in other words, do not need additional water.)
Great Lakes found that January and February sub-freezing conditions can also affect operations of the mister and other parts of the plant.
Now that most weather-related hurdles are cleared, Sandy Rosen and the other officers of Great Lakes Recycling are convinced the addition of a single-stream plant has been the correct decision.
"Single-stream is not going away; it is the most efficient way to collect the material," says Rosen. He adds that if consuming mill companies move back to wood chips as a means of protesting single-stream collection (as at least one has threatened to do), "economics will provide the upper hand to the mills that have prepared for this new recycling stream."
The author is the editor of Recycling Today and can be contacted via e-mail at btaylor@RecyclingToday.com.
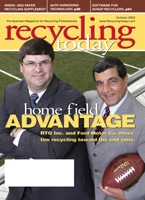
Explore the October 2003 Issue
Check out more from this issue and find your next story to read.
Latest from Recycling Today
- Nucor receives West Virginia funding assist
- Ferrous market ends 2024 in familiar rut
- Aqua Metals secures $1.5M loan, reports operational strides
- AF&PA urges veto of NY bill
- Aluminum Association includes recycling among 2025 policy priorities
- AISI applauds waterways spending bill
- Lux Research questions hydrogen’s transportation role
- Sonoco selling thermoformed, flexible packaging business to Toppan for $1.8B