It may be difficult for North Americans to think of paper as a rapid growth industry, but in China substantial investment capital is being plowed into new, high-production paper mills.
One company that is putting considerable new capacity online is Lee & Man Paper Manufacturing Ltd., a Hong Kong-based publicly traded firm with three large factories in the People’s Republic of China.
The company, which sources much of its recovered fiber feedstock from North America, has focused on containerboard and other paper packaging grades that are in high demand within China’s booming industrial sector.
Ramping Up |
Lee & Man Paper Manufacturing Ltd., Hong Kong, is currently churning out linerboard and corrugating medium at three factories near China’s coast, with another factory on the drawing board to be located in the country’s interior. Each of Lee & Man’s current plants has been built as a largely self-contained unit that turns baled scrap paper into a finished product, produces its own power and, to a large extent, handles its own waste stream. The company’s three factories share several similar characteristics: Huangyong Plant—The company’s oldest production facility is in Zhong Tong, Dongguan, in southern China. The Huangyong mill has four paper machines capable of producing up to 650,000 metric tons of paper products annually. The integrated facility includes extensive warehousing space, a large stacking area, its own water supply plant and wastewater treatment facility and a power generation plant providing stable supplies of electricity. Changshu Plant—This plant, located closer to the Shanghai market, was built in 2002 in Changshu, along the Yangtze River. The Changshu mill is also an integrated facility and currently has two paper production machines with an annual capacity of about 550,000 metric tons. HONGMEI Plant—In 2004, Lee & Man began expanding its southern China production by purchasing land in Hongmei in Dongguan Province. Also fully integrated, this third production plant will house a total of four paper production machines when finished and bring Lee & Man’s total production capacity to about 1.6 million metric tons annually. |
COMPLETE PACKAGE
One consistent component of China’s manufacturing boom has been the need for boxes and other forms of packaging in which to ship finished goods.
Even though China’s manufacturing growth has shifted or spread out into new segments—from toys and textiles to consumer electronics and appliances—through each step of the evolutionary process the need for boxes has come along for the ride.
The need for the proper packaging for China’s goods to reach the rest of the world has created tremendous opportunities for the makers of containerboard grades, and Lee & Man Paper Manufacturing Ltd., was formed in 1994 to take advantage of that opportunity.
With confidence that demand for its product was strong and rising, the company and its CEO Raymond Lee were able to plan big, with the company’s first plant in Dongguan in southern China soon churning out 650,000 metric tons per year of containerboard.
That plant has since been joined by another in Changshu, closer to the booming city of Shanghai, that was churning out more than 550,000 metric tons annually by the end of 2004. Additionally, the company is modernizing and expanding its presence in Dongguan with the opening of the Hongmei plant, which will soon house three of the Lee & Man’s newest and highest-volume paper machines.
According to Ross Li, executive director and assistant general manager of Lee & Man Paper Manufacturing Ltd., the company has continued to add paper machines at both of its coastal China locations while also breaking ground on a new mill location in Chongching in central China.
Capacity has been added at both plants as China’s economy and demand for containerboard has boomed unabated. "Demand is really great," says Johnny Tse, operations manager for the Lee Kwok Trading Ltd. arm of Lee & Man.
The company has a total of 11 paper machines running or planned at its three existing mills in China.
The booming demand allows Lee & Man to pour capital into its expansion projects—building new mills in less than a year and installing new paper machines on six-month schedules—while knowing it will quickly recoup its investments.
The mill complexes are substantial properties that include much more than the papermaking lines alone.
The company’s Changsu mill includes its own coal-fueled power plant, a water treatment plant, a harbor facility on the Pearl River, surrounding bamboo plantations to help yield pulp and fiber, and a large warehouse area to store the bales and bales of scrap paper that arrive to provide the pulping stock for the majority of the company’s fiber needs.
Li estimates that only 10 percent to 15 percent of the company’s fiber needs are met by wood pulp and other forested material, while the rest of its feedstock is scrap paper, with the old corrugated containers (OCC) grade being by far the most prominent.
OLD TO NEW
With scrap paper providing 85 percent to 90 percent of Lee & Man’s raw materials, the company’s operating and trading philosophy is based around recovered fiber on the supply side.
At all of its massive mill complexes, receiving, storage and sorting areas for incoming bales of OCC and other recovered fiber grades are an integral part of the operation.
Li estimates that as of mid-2006 about 60 percent of its secondary fiber is being sent from North America.
He says Lee & Man appreciates the quality of North American OCC, both in terms of fiber length and lack of contaminants. The company has long had a trading arm in the United States, Ralison International Inc., Diamond Bar, Calif., to procure fiber on its behalf.
In order to feed its increasingly hungry stable of paper machines, the company has also established Mark Lyndon International B.V., based in Rotterdam, to obtain more recovered fiber from Europe as well.
"We’ll more or less try to keep the North American percentage at 60 percent," says Li. "We want to keep our good balance of a mix from throughout the world. North America has the best fiber but also the highest prices," he notes, adding that the North American and European markets both have "strengths and weaknesses."
While demand for containerboard to make boxes for everything ranging from backpacks to microwave ovens continues unabated, the bigger challenge for Lee & Man can be finding the raw material to feed the front end of its production lines.
Li says that finding enough raw material to feed its plants in 2007 is "definitely a challenge."
Traditionally, Lee & Man has not been active in procuring domestically generated material, in part because average fiber length is not as good and also because domestic recyclers may not make bales with the same quality as experienced recyclers in North America or Europe.
But as the company continues to grow and as China’s domestic fiber sources improve, Lee & Man may well begin to expand its presence in the domestic scrap paper market. "It’s a very interesting topic," says Li.
He says that among the two ways Lee & Man could do this would be to either become a collector and packer within China itself, or it could rely on existing local Chinese recyclers. As of right now, Li says the company is more inclined to rely on existing companies. "It may not be cost-effective for us to take part in OCC collection in China," says Li.
In terms of working with existing recyclers, Li says that the company’s "network is improving, but not well established." Part of the problem, he says, is that existing recyclers are used to collecting and shipping smaller quantities to government-controlled mills that may not have the same quality standards as private companies such as Lee & Man.
ROLLING ON
In 2006, Lee & Man’s ability to produce roll after roll of linerboard and corrugating medium has gained speed and kept the company on a steady growth path.
Demand for the Lee & Man’s finished paper remains strong—and it does not have to travel far. "Eighty percent of what we produce in southern China stays here and goes to local converters," Li estimates.
Although it is possible that Lee & Man could produce paper and ship it to overseas markets and still make a profit, Li says the company has "kept it to a low percentage." He adds, "If local consumption is absorbing all that we make, there is really no need to ship to the outside world."
Ultimately, a great deal of what Lee & Man produces is converted into boxes and packaging that does make its way to North America and Europe, where it becomes scrap paper and may well find its way back inside a bale of OCC that will be pulped at one of the company’s mills.
To a great extent, the near-term growth prospects of Lee & Man will not rely on its end markets as much as on the ability of its overseas buyers to procure the scrap paper raw material it needs. "I don’t think China can match the scale of OCC recycling internally in the next few years to keep up," says Li. "It will take a lot of effort and monumental encouragement on the part of the government to accomplish that," he says.
Li and most of Lee & Man’s other top managers are spending a considerable percentage of their time ensuring that the company is exploring all possible supply lines to keep its paper machines fed.
"It makes no sense to put all of this new manufacturing capacity in place if we don’t plan ahead on the OCC buying side," he states.
"We’ve already grown fast, and in the second half of 2006 and through 2007 we are nearly doubling our capacity," Li says. "We quite simply need OCC to be successful."
The author is editor of Recycling Today and can be contacted at btaylor@gie.net.
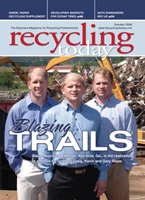
Explore the October 2006 Issue
Check out more from this issue and find your next story to read.
Latest from Recycling Today
- Nucor expects slimmer profits in early 2025
- CP Group announces new senior vice president
- APR publishes Design Guide in French
- AmSty recorded first sales of PolyRenew Styrene in 2024
- PRE says EU’s plastic recycling industry at a breaking point
- Call2Recycle Canada, Staples Professional expand partnership
- Circular Services breaks ground on north Texas MRF
- Tariff uncertainty results in choppy nonferrous scrap flows