If you are in the market for new or used Mobile Document Shredding (MDS) equipment, you need to understand your options. In the last decade, the MDS industry has gone through some major advancements. This alone makes it very important to consider all the features and capabilities of today’s MDS equipment.
HIPPA'S EFFECT |
Existing and upcoming privacy deadlines for medical records keepers are gaining publicity, and paper shredding firms can profit from organizations complying with them. That’s the message of M. Jason Meyer of WorkSmart MD Inc., Ormond Beach, Fla., who spoke to attendees of the National Association for Information Destruction (NAID) conference in Orlando earlier this year. At the federal level, information destruction requirements in the health care field are part of the Health Insurance Portability and Accountability Act of 1996 (HIPAA). Although the centerpiece of the act focused on medical records standardization, parts of the legislation also address maintaining the privacy and security of medical records. Insurance companies, hospitals and doctors are obligated to protect individually identifiable health information, interpreted to mean any records that include a patient’s name, address or Social Security number. This privacy portion of HIPAA took effect April 14 of this year. Additional security measures effective in 2005 are focused on electronic data transmission, although the standardization of electronic forms has a deadline nearing in the fall of 2003. When these forms become standard, many older, existing records could become obsolete, opening up another avenue of opportunity for information destruction companies. According to Meyer, many physician practices may still be unaware of the looming Oct. 16, 2003, deadline for electronics forms standardization, as well as some of the privacy and security requirements. Based on a survey conducted by WorkSmart MD, health care companies and paper shredding firms may soon be conducting even more business together. "Based on our research, we think they are really going to be turning to document destruction companies . . . during this two-year window before the security requirements take effect," said Meyer. —Brian Taylor |
REACHING CAPACITY. The most common mistake made by consumers when selecting MDS equipment is putting too much emphasis on the rate at which paper can be shredded, better known in the industry as capacity. Although capacity is very important, many manufacturers attempt to equate shredder capacity directly to revenue generation.
This line of argument is in fact misleading and hurtful to your business success. For example, MDS equipment that can shred 6,000 pounds per hour does not generate twice the revenue stream as equipment that can shred 3,000 pounds per hour. Shredding productivity, and hence revenue generation, is offset, or equalized, in light of driving time, the collection process, payload capacity restraints, payload unloading time, etc.
To further add to the capacity dilemma, or the "More is not necessarily better" argument, equipment operating costs need to be evaluated. Keep in mind, that higher capacity MDS equipment is more costly to operate because of increased wear and tear on the shredder and other system components. Fuel consumption also increases significantly, as does noise and dust generation.
The net effect of all these factors may in fact be different then what you were initially led to believe. As a buyer, be diligent in drilling down past the capacity argument. As an operator, you need capacity, but you should also expect a whole lot more from your MDS equipment.
GENUINELY DESTROYED. Shred size is often a topic of concern and confusion, but it should also be part of the selection process. Although there is a lot of terminology in the industry describing shred types, generally there are only three types of shreds.
The first type is a shred that tends to be long, slender strips the full length of the document being shredded. This type of shred tends to be easily reconstructed. The second type is smaller and has been smashed, ripped and torn. Although difficult to reconstruct, it is very dusty and has a poor recycling value in light of paper fiber damage. The third and most accepted type is a 5/8-inch-wide, random- length shred. This type of shred is difficult to reconstruct, but still has good recycling value.
The safety, security and method of introducing the paper into the shredder are also important. Traditionally, paper was feed by hand into the shredding equipment. Today there are other options, such as feeding the shredder with an enclosed, two-wheeled bin from ground level or from within the unit. Today’s methods create a much more secure image because the operator does not see the paper being shredded.
When feeding a shredder from ground level, it is important to consider safety and environmental factors. A fully enclosed bin tipper will contain a bin in the event of a bin failure, thus protecting the operator from injury. An enclosed bin tipper also protects paper from being blown away by the wind.
MERGER MANIA? |
Entrepreneurs have gravitated toward the document destruction industry in the past few years, but the movement toward consolidation in this segment has gained steam. That’s the opinion of investment banker Michael R. West, who spoke to attendees of the National Association for Information Destruction (NAID) Conference in Orlando, Fla., in May of this year. West, whose company Starboard Ventures LLC, Greer, S.C., has helped arrange acquisitions within the document destruction business, says that some small shredder firms may have already missed their best opportunity to sell their companies at peak value. "It’s hard not to make money in this business right now," West said of the document destruction industry. But, he warned, pricing competition is beginning, as is competition from growing national firms, such as Iron Mountain Inc., Boston. "In reality, a lot of people in this room will not be here in four years," he predicted, after mergers and a competitive marketplace set in. West said that many service industries claim their market is unique or their service does not lend itself to larger, national management, but he said that he is seldom persuaded by these arguments. "There are no protectable niche markets," he stated, adding that industries can take 20 to 25 years to consolidate before reaching the point where a couple of players (such as Coke and Pepsi in soft drinks or Alcoa and Alcan in aluminum) dominate the market. As consolidation sets in, "size begins to matter," said West. "Major players emerge, pricing is more competitive and profits smaller," during the consolidation phase until a final "Balance and Alliance" phase is reached. In this stage, "a very few large companies protect their market positions," noted West, often to the point where the government might take an interest from the anti-trust perspective. In all likelihood, the information destruction industry is a very long way from reaching the consolidation level of the aluminum or soft drink industries. In fact, West remarked that it’s possible that some of the most active consolidating in the document destruction industry may already have occurred. According to figures offered by West, cash paid for acquired document destruction companies may have peaked as early as 1999 after three years of heavy activity. He advised smaller independent companies to carefully consider the consolidation activity occurring around them. —Brian Taylor |
There is a long list of types and sizes of two-wheeled bins available on the market today. In the shredding industry, there are basically two types and two sizes that have been widely adopted: the North American two bar and the European single bar, both in the 64 to 96-gallon size range. It is important to review the capabilities of the bin tipper before selecting the equipment.
RELIABILITY. Another area that tends to be completely overlooked is the Original Equipment Manufacturer (OEM). It may be important to check that the heart of the system, the shredder, is actually designed and manufactured by the MDS equipment supplier.
In some cases, the MDS equipment supplier will subcontract the shredder portion to another OEM. A buyer should ask if the future supply of replacement parts and service support will be at risk. The risk of the misapplication of product also becomes a concern. The MDS equipment supplier should also have an engineering staff that can select and apply components best suited for the application.
Serviceability is a key factor when selecting MDS equipment. The old rule of K.I.S.S. (keep it simple stupid) still applies today. Less moving parts generally mean the less maintenance and repair required.
Equipment selection should include a review of daily, weekly, monthly and yearly maintenance along with an estimated time for each task. Availability of OEM parts and professional round-the-clock service support must also be considered.
And last, but certainly not least, your MDS equipment must be reliable and durable. Your equipment generates zero dollars in revenue when in the shop for repairs. Ensure the equipment you purchase has a proven track record concerning reliability. Your business cannot afford to be a guinea pig for someone else’s "flavor of the month!"
The author is Mobile Products Manager for Shred-Tech Inc., Cambridge, Ontario, Canada.
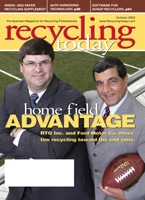
Explore the October 2003 Issue
Check out more from this issue and find your next story to read.
Latest from Recycling Today
- Nucor receives West Virginia funding assist
- Ferrous market ends 2024 in familiar rut
- Aqua Metals secures $1.5M loan, reports operational strides
- AF&PA urges veto of NY bill
- Aluminum Association includes recycling among 2025 policy priorities
- AISI applauds waterways spending bill
- Lux Research questions hydrogen’s transportation role
- Sonoco selling thermoformed, flexible packaging business to Toppan for $1.8B