Firm plans recycled corrugated venture
In late May, CorrVentures LLC, a private development firm based in Wilmington, Delaware, that specializes in strategic project development in the pulp and paper and corrugated packaging markets, announced its plans to build and operate a 300,000-ton-per-year, 100 percent recycled lightweight containerboard mill about 9 miles south of Albany, New York.
Stephen Read, president and CEO of CorrVentures, has partnered with Charles Klass, managing member of CorrVentures; Jan Lambert, executive vice president of CorrVentures and president and CEO of Greater Philadelphia-based First Fiber Corp. of America; and Eric Lawrence, executive vice president and treasurer at CorrVentures, to form the new business.
“We’ve all been business associates and friends dating back to the 1980s and 1990s,” Read says. “We’ve participated in a variety of strategic projects and operated converting facilities. The four of us have different expertise. It’s a combination of talent to get this up and running; we think we have a great team in place.”

Lambert adds, “We’re a unique team. We have exceptional experience in banking operations and in the integration of supply.”
The CorrVentures team says it plans to start a containerboard mill in the Northeast to consume old corrugated containers (OCC), mixed paper and other recycled fibers generated in the area. The business just made investments in a facility near Albany.
“There are a variety of reasons why people would welcome a project like this,” Read says. “The recycling aspect is one. Also, corporations want to advance sustainability for a cleaner environment. Our facility and end products are 100 percent recycled. Aspects in that area alone should be attractive to have some of our products used for packaging.”
CorrVentures says it plans to construct a new, state-of-the-art containerboard mill at the site. Read says construction will commence in early 2020, with completion estimated for the fourth quarter of 2021.
The mill will produce containerboard, linerboard and corrugated medium. Klass says it will consume 330,000 to 350,000 tons per year of recycled fiber in the form of postindustrial OCC and OCC from material recovery facilities (MRF).
“Source-separated OCC is cleaner than what you get at MRFs,” Klass says. “Our design is if we need to run 100 percent MRF [materials], we do it. From a process design standpoint, I’m designing [the mill] for the worst-case scenario, which is MRF-generated materials.”
Lambert adds, “We’re not asking providers to bring us China spec [OCC]. We’re an American market. Our machines are designed to receive material and process it as we know it in terms of ISRI (Institute of Scrap Recycling Industries) definitions, not China’s definitions.”
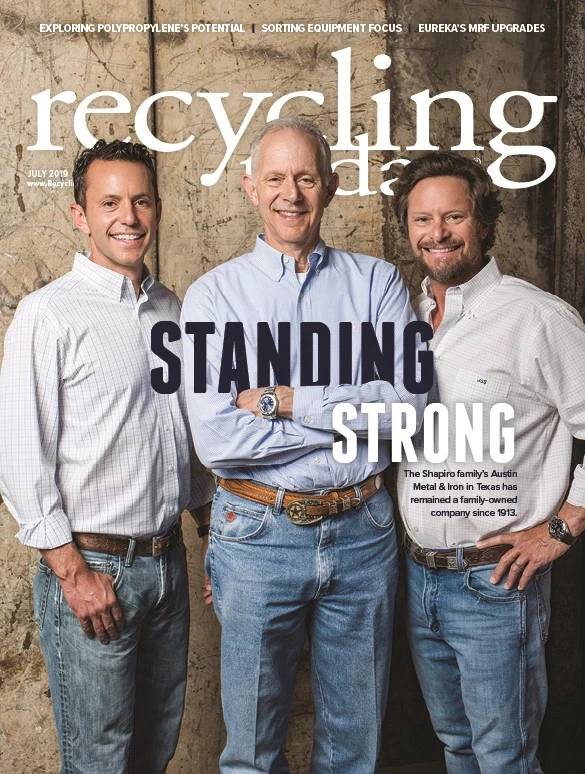
Explore the July 2019 Issue
Check out more from this issue and find your next story to read.
Latest from Recycling Today
- NWRA announces 2025 Driver of the Year, Operator of the Year winners
- The Scrap Show: Nanci Schuld of FE Trading Group LLC
- Call2Recycle Canada partners with RLG to advance battery collection
- Report delves into recovery opportunities for food-grade polypropylene
- Reimagining Supplier Payments in Metal Recycling: A Digital Leap Forward
- STEINERT Lithium Battery Detection and Removal from Waste Streams
- Driving the Future: Innovations in Waste & Recycling Technology
- Robin Wiener recognized for recycling leadership