
Check valves and flashback arrestors are safety devices for protecting workers using oxyfuel cutting and welding equipment. A check valve is a device that is designed to prevent the unintentional backflow of gases. A flashback (flame) arrestor is a device that prevents the propagation of a flame upstream. Note that these devices reduce the volume of gases available at the tip/nozzle.
Nature of the hazard
Always be sure enough fuel is in both cylinders to complete the operation before starting a job. Reverse flow of a gas generally happens when one cylinder goes empty during operation, creating an imbalance of pressure in the system. A clogged or blocked tip also can cause a backflow. An extremely hazardous situation can develop when oxygen and fuel gases are mixed inside the hoses. Reverse flow check valves alone will not stop a flashback in the system. When conducting oxyfuel cutting and welding operations, operators can experience backfires or flashbacks.
A backfire is defined as the momentary recession of the flame into the torch, potentially causing a flashback or sustained backfire. It is usually signaled by a popping sound, after which the flame may either extinguish or reignite at the end of the tip. The user hears a “pop,” and the flame is extinguished. This can happen at high gas exit velocities at the nozzle/tip or if the nozzle/tip gets too close to the work piece. The flame may reignite automatically, or the use of an igniter may be necessary. This is not normally a safety concern and, in fact, many manufacturers induce backfires during design and production tests to ensure flame integrity of torches and tips.
A sustained backfire is defined as the recession of the flame into the torch body with continued burning characterized by an initial popping sound followed by a squealing or hissing sound, potentially burning through the torch body.
A flashback is defined as the recession of the flame through the torch and into the hose, regulator and/or cylinder, potentially causing an explosion. This is a potentially hazardous situation, particularly if the flame reaches the hoses where an explosion would result in rupture or separation of the hose. A flashback is generally caused by the reverse flow of gases upstream into the hoses or other equipment. This is usually the result of: 1) improper shutdown and/or startup procedures; 2) allowing cylinder pressures to become too low; or 3) a check valve that is not functioning properly.
As with any cutting or welding operation, workers need to be aware of their surroundings where work is performed. Always have approved fire extinguishers nearby and have all personnel trained in their proper use. Flashbacks can damage equipment and cause injury to nearby workers and equipment. Proper workplace precautions, such as barriers and other protections, should be used to minimize fire hazards and injury.
How to avoid the hazard
Operators can avoid backflows and flashbacks by following these suggestions:
- Equipment with integrated check valves and/or flashback arrestors is available.
- Check valves and/or flashback arrestors can be added to existing equipment. Properly maintained and operated systems are safe.
- Inspect the system before use, repairing or replacing defective or damaged parts.
- Have only qualified people make any needed repairs.
- Be sure enough gas is in both cylinders to complete the job.
- Follow the manufacturer’s recommended procedures for proper startup and shutdown of the equipment used.
- Don’t allow the tip to touch the work.
Flashback arrestors and check valves are not intended to replace proper practices for safe operation. They can provide an increased level of protection in addition to the manufacturer’s recommended operating procedures. Check valves and flashback arrestors should be installed at the location specified by the manufacturer. Manufacturers have begun incorporating flashback arrestors and check valves as a standard item with all of their torches sold.
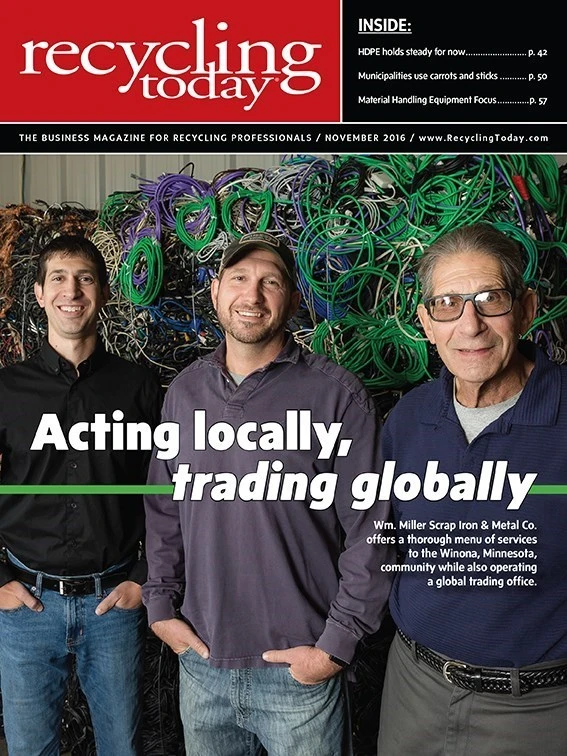
Explore the November 2016 Issue
Check out more from this issue and find your next story to read.
Latest from Recycling Today
- Magnomer joins Canada Plastics Pact
- Electra names new CFO
- WM of Pennsylvania awarded RNG vehicle funding
- Nucor receives West Virginia funding assist
- Ferrous market ends 2024 in familiar rut
- Aqua Metals secures $1.5M loan, reports operational strides
- AF&PA urges veto of NY bill
- Aluminum Association includes recycling among 2025 policy priorities