
Any single electronic device—a mobile phone, a laptop computer or a microwave oven—consists of numerous components made from a wide range of metallic and polymer materials.
Disassembling just one of these devices requires knowledge and proper technique to separate and prepare those basic materials for recycling. Combine that task into the hundreds or thousands of such devices streaming into a waste electrical and electronic equipment (WEEE) collection center, and the chore facing electronics recyclers is evident.
In the previous two decades, as diverting WEEE materials from landfill and recovering the resources within has become a higher priority, recyclers and their equipment suppliers have devoted more attention to performing this work more efficiently and more effectively.
At industry conferences in late 2015, several presentations offered updated information on how recyclers and technology providers are exploring new ways to turn the chaotic WEEE material stream into marketable secondary commodities.
AUTOMATION ADVANCES
Investments in materials separation and processing are ongoing around the world at facilities that handle end-of-life electronics. A roster full of equipment vendors employs researchers and plant installation engineers who continue to devise new ways to create marketable scrap metals and plastic from shredded WEEE materials.
At Electronics Recycling Asia 2015, held in Singapore in mid-November, several presenters offered overviews of the recent efforts of their companies. Ted Pak of the South Korean regional office of Germany-based TOMRA Sorting Solutions GmbH said the wide variety of sorting and separating equipment available from the company has increased the quantity and quality of secondary commodities recoverable from obsolete electronics.
Among the equipment available from TOMRA are NIR (near infrared), XRT (X-ray transmission) and XRF (X-ray fluorescence) devices that can conduct automated metals and polymer sorting of shredded e-scrap, Park said.
He offered an example of a refrigerator shredding and recycling plant where a TOMRA retrofit created a system that now produces 97%-to-99% pure aluminium and copper fractions; a 97%-to-99% pure ABS (acrylonitrile butadiene styrene) fraction; and a 94%-to-96% pure polypropylene product. “Their bargaining power has increased” when selling materials, Park said of the company, which earned a return on investment in the system in less than one year.
On the problematic side for electronics recyclers has been processing cathode ray tube (CRT) monitors and televisions. The lead and leaded glass contained in CRT units has diminishing end market options.
Dr. Alexandre Comino of the recycling division of Italy-based Hellatron told event delegates his company has a “breakthrough innovation in CRT lead glass treatment.”
Hellatron’s process involves initial manual disassembly and cutting to remove the glass cathode tube from the unit. This glass is then ground and purified into marketable silicates by way of a downstream process.
The lead from the funnel glass is recovered in what Comino called a “pure cold hydrometallurgical process” involving an electrolytic cell. He added that it is “an environmentally friendly process with no emissions.”
Camino said the overall Hellatron process entails the “transformation of a problem, the CRT lead glass, into three valuable raw materials: lead, soluble silicates; and insoluble silicates.”
NOT JUST PLASTIC
When nonrecyclers see pallets or bins full of discarded electronics, they most likely see plenty of plastic. Recyclers are all too aware that having a bin full of plastic brings little benefit until each type of plastic is subdivided by polymer type and colour.
At the Singapore event, Sreepadaraj Karanam from the Singapore office of Saudi Arabia-based SABIC said his company is working with OEMs (original equipment manufacturers) to explore the “opportunity for upcycling” the stream of plastic scrap that comprises part of the overall WEEE sector.
The company has developed several exclusive recycled-content resins, Karanam said, that offer a “cradle-to-cradle” mechanical recycling option for plastics derived from the e-scrap stream. He said SABIC’s goal is “to be a global supplier of choice of recycled resins.”
The custom resins SABIC produces include one made from polystyrene compact disc and DVD jewel cases and others made from polycarbonate and ABS plastic scrap.
Barriers remain, Karanam said, including achieving sufficient economies of scale and convincing buyers to overcome some aesthetic objections, including comparatively restricted color choices versus virgin resins. But “if we do this right,” he said, “we believe there is an opportunity for innovation along the entire value chain.”
The Germany-based ALBA Group has been vertically integrating to reprocess and blend its own recycled resins. In a presentation at the 2015 Plastics Recycling Conference Europe, which took place in Madrid in late October, the company’s Dr. Manica Ulcnik-Krump said ALBA handles a variety of plastic scrap materials and has created some of its own resins to help ensure adequate end markets.
Plastic is a “miracle” material, Ulcnik-Krump said, but its many different properties also means it is used in multiple applications, making recycling more complicated.
Krump said the ALBA Group and its Interseroh subsidiary handle some 600,000 tonnes of plastic scrap each year, and the company has made a commitment to “upcycling instead of recycling.” She said, “We strongly believe mechanical recycling is the future [not energy production]. We should try to give [plastic scrap] a second life.”
As part of that commitment, ALBA has invested in reprocessing equipment to produce two trademarked grades of plastic pellets: Procyclene and Recycthene. The grades can be used in injection and blow molding processes and come in a variety of colours.
“You have to go all the way,” Krump urged fellow plastics recyclers considering becoming reprocesors, which can mean finding customers to use the products and then creating products “that can be recycled multiple times.”
EVERY OUNCE OF METAL
For recyclers to invest in automation they need to be convinced of a reasonable return on investment (ROI) and the likelihood of a long-term market for their products.
At Electronics Recycling Asia 2015, Professor Ma Hsiao-Kang of National Taiwan University described a mobile hydrometallurgical tin and gold stripping process offered by Taiwan-based Uwin Nanotech Co. Ltd. The process is designed to collect tin and gold from obsolete circuit boards in a way that will not cause worker safety issues. The product can recover 99.9% pure gold and 99.96% pure tin oxide from printed circuit boards in a safe and environmentally sound way, Ma said. Uwin also is developing other products, he said, including a system to recover copper from mixed materials.
Dr. Sophie Purser of United Kingdom-based PhosphonicS Ltd. told delegates her company marketed liquid solutions containing “loaded scavengers,” or silica-based powders that are “surface-coated with multifunctional ligands.” (Ligands are ions or molecules attached to metal using a coordinate bonding method.) The PhosphonicS powders are “designed only to recover precious metals,” Purser said.
The recovery of rare earth metals is the focus of a process described by Dr. Wolfram Palitzsch of Germany-based Loser Chemie GmbH. Palitzsch listed indium, gallium and selenium as rare earth metals used with increasing frequency in display screens, mobile devices and other electronics products that are gaining market share.
Flat display panel glass treated with a hydrometallurgical process can recover these rare earth metals as well as any copper, cadmium and molybdenum contained within. The glass cullet resulting from the process also has been deemed “useful for new flat glass production” by a Pilkington Glass laboratory in the U.K.
Loser Chemie also has devised a liquid solution-based treatment process for solar panel scrap that contains silicon and photovoltaic materials (Si-PV scrap). The system also can recover the gold, silver and aluminium within.
Electronics recyclers and their customers who are focused on zero waste and complete recovery have a considerable number of new systems and techniques to research designed to help them reach their goal.
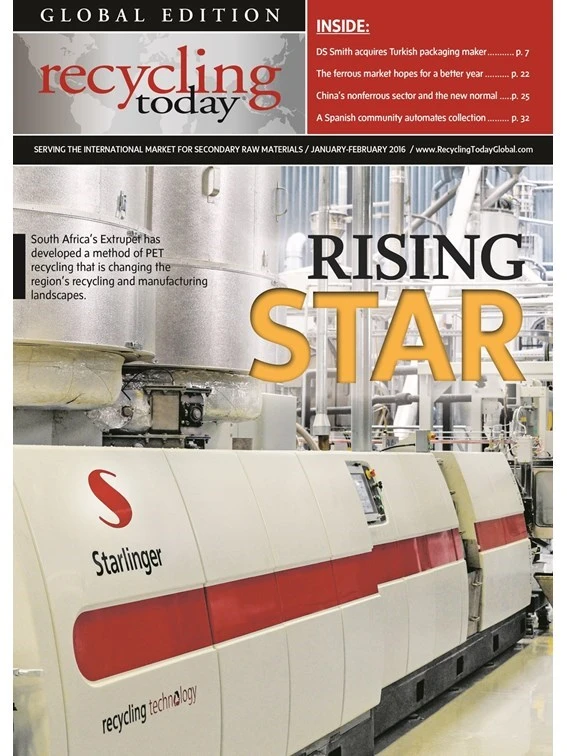
Explore the January 2016 Issue
Check out more from this issue and find your next story to read.
Latest from Recycling Today
- Aqua Metals secures $1.5M loan, reports operational strides
- AF&PA urges veto of NY bill
- Aluminum Association includes recycling among 2025 policy priorities
- AISI applauds waterways spending bill
- Lux Research questions hydrogen’s transportation role
- Sonoco selling thermoformed, flexible packaging business to Toppan for $1.8B
- ReMA offers Superfund informational reports
- Hyster-Yale commits to US production