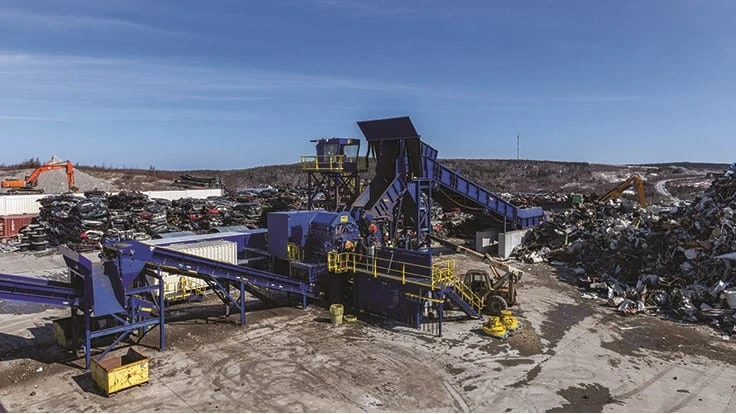
Photo courtesy of Wendt Corp.

The key to any shredding yard is the auto shredder itself. The shredder is the heartbeat of the yard, setting the pace for the incoming feedstock, downstream equipment and the outbound products. Therefore, it is of the utmost importance to keep the shredder operating as regularly and as efficiently as possible. Optimizing your auto shredder will allow you to maximize production and product quality while also reducing downtime and operational costs, in turn maximizing revenues and margins.
Throughout Wendt’s 40-plus years in the shredding industry and 40-plus shredder installations, we’ve had the opportunity to analyze and experiment with a wide range of shredder makes, models and designs. This experience has allowed us to establish a large knowledge base that is invaluable when optimizing the performance of existing shredders and new shredder installations.
When we’re on-site at an auto shredding operation, we look at many areas to understand the shredder’s current performance and potential for improvement, including:
- the types of feedstock and the loading procedure employed;
- the feed roll speed and the response time (hydraulics);
- the rotor type;
- the shredder’s internal geometry;
- the hammer pattern and rotation schedule; and
- automation and operator training.
Types of feedstock and loading procedure
The type of feedstock and the way it’s loaded onto the infeed conveyor play a big role in the performance of the shredder and the quality of its output.
In general, it is best to feed a shredder in a consistent pattern that mixes light feedstock with heavy feedstock. The heavy feedstock helps to push the lighter feedstock into the mill, making feeding easier and producing a more consistent output. By establishing a feed pattern, the operator can create a more consistent output flow and quality while reducing the peaks and valleys that increase electricity costs.
Feed roll speed and Response time
Along with feedstock types and patterns, the feed rolls are another critical element in ensuring optimal shredder performance.
The feed rolls are the last line of defense for the operator to control feed into the shredder. Feed rolls that are too slow or underpowered make it difficult for the operator to control the material in the feed chute, which can create gaps in the shredder’s feed. This reduces the operator’s ability to keep the mill at a “full-box” state, which can lead to high variability in electricity consumption, decreased casting life and poor throughput and separation downstream.
The theory of “full-box” shredding is that if the shredder is full of material at all times, the material will begin to shred on itself in addition to shredding on the castings within the shredder. This, in turn, increases the life of the shredder castings by reducing the amount of wear they see. It also results in more consistent throughput and product quality. Appropriately designed feed rolls are critical in giving shredder operators the greatest chance of achieving “full-box” shredding while still having the ability to hold material back to prevent stalls.
The performance of the feed rolls largely is dictated by the design of the hydraulic power units used to rotate and lift them. Because of this, we have focused much of our product development resources over the past few years toward optimizing the hydraulic design for the feed rolls. Our latest design allows for better feed roll speed and response time, giving customers more control over their shredder feed. This new design comes standard with our newest shredders and can be retrofitted on existing shredders, as well.

Rotor type
Rotor type is another component that can affect a shredder’s performance.
The best type of rotor to use in an auto shredder has been a long-standing debate in the shredding industry. In the early years of the industry, the spider rotor and disc rotor both saw similar success in shredding.
For spider rotors, their success was attributed to their throughput and ability to extend their lives through routine maintenance and their tolerance for unshreddables. That being said, in recent years, the auto shredding industry has moved toward using disc rotors.
It is important to understand the procedures and costs associated with rotor maintenance. To appreciate the operating cost of a rotor, an operator should track and understand the capital cost of the rotor, maintenance hours spent on the rotor and wear part costs (such as spider caps). By tracking these costs over time and with countless examples, Wendt has noticed a strong argument for using a disc rotor over a spider rotor. We’ve seen a significant reduction in operating costs and increased consistency in shredder performance when this type of rotor is used.
Retrofitting a shredder equipped with a spider rotor to use a disc rotor can be a valuable step in optimizing a shredder’s performance while minimizing its operating costs.
Internal geometry
Directly related to the rotor type is the internal geometry of a shredder, which has undergone a slow evolution throughout the last 40 years to maximize throughput and minimize operating costs.
When analyzing a shredder’s geometry, it’s important to understand the issues that are currently happening within the mill. For instance, if the operator is seeing an excessive volume of pokers discharged out of the mill, he or she may want to consider adding a few solids after the anvil or blocking the first row of holes on the top grate. If the operator is having trouble feeding the machine, and the feed rolls are sufficiently powered, he or she may want to look at anvil position or hammer clearances.
The list of problems that can be fixed by adjusting some of the geometry or castings within the mill is extensive and why it’s critical to understand the problems and the geometry inside the shredder.
Hammer pattern and rotation schedule
A few rules of thumb should be used when optimizing the hammer pattern and rotation schedule, but every shredder and operation is different. It’s important for operators to experiment with their patterns to find one that fits their specific operational requirements. The hammer pattern should spread the wear across the entire width of the shredder, maximize throughput and fit well within a company’s maintenance schedules.
Hammer patterns and rotation schedule are easy ways for operators to optimize their operating costs. Sometimes a simple change in pattern or schedule can affect the wear pattern within the mill, extending the life of the shredder’s castings.
Automation and training
Many shredders in operation today are still running using their original control systems. Operator controls have come a long way in reducing the burden on the operator and improving the performance of the shredder and the business.
Upgrading an operator control system is an easy way to optimize any shredder. Today’s latest systems allow for near complete autonomy of the shredder’s operation, significantly reducing the need for operator intervention when compared with older systems.
In addition, control systems now can generate sophisticated statistics and reports, giving operators more visibility into their daily operations. This allows for better tracking of performance and maintenance procedures to identify problem areas and address issues proactively.
Finally, the operators themselves are important variables to consider when optimizing shredder performance. Even with the growing autonomy of shredders, shredder operators still play a key role in the entire plant’s performance. Investing in the proper training of operators is invaluable to ensure maximum uptime, maximum throughput and minimum operational cost.
Although the shredder is the focal point of most shredding yards, it also is important to ensure the equipment downstream of the shredder is optimized to maximize the efficiency of any operation. Optimizing a shredder and its downstream starts by being proactive in your maintenance routines and training your operators on the process and the equipment.
One major problem operators face is the amount of time it can take to clean in and around the equipment. Simple adjustments, such as adding proper transitions and skirting or adding pull trays in strategic areas, can help to reduce cleaning time.
Understanding how each piece of the shredder and downstream works and the role it plays in the process is crucial to optimize a system. Hiring a company to train operators and analyze the process can be a cost-effective and quick way to optimize a shredding operation.
Get curated news on YOUR industry.
Enter your email to receive our newsletters.
Explore the April 2020 Issue
Check out more from this issue and find your next story to read.
Latest from Recycling Today
- European project yields recycled-content ABS
- ICM to host co-located events in Shanghai
- Astera runs into NIMBY concerns in Colorado
- ReMA opposes European efforts seeking export restrictions for recyclables
- Fresh Perspective: Raj Bagaria
- Saica announces plans for second US site
- Update: Novelis produces first aluminum coil made fully from recycled end-of-life automotive scrap
- Aimplas doubles online course offerings