The question of how many magnets are needed in order to achieve a clean, marketable grade of shredded scrap has been asked for years. Twenty plus years ago, the question wasn’t quite as important because most shredder systems often had extensive "z-box" cascade air systems that ensured a clean product. Many of these old systems would even draw material directly from the shredder, often proving catastrophic to the fan after an explosion in the mill. As environmental concerns increased regarding the exhaust of these systems, operators looked for ways to eliminate the air system all together.
One initial idea was to produce a "wet" system that virtually flooded water into the shredder, which greatly reduced the amount of airborne dust the system produced but also did a fair job of "cleaning" nonmetallic contaminants from the shred. However, these systems made for extremely poor working conditions due to mud, not to mention problems created by extremely cold temperatures. Water run-off soon became an environmental issue for these systems as well.
Later, some downstream designers tried to eliminate the need for air systems by placing three and even four magnets in line. These systems were short-lived as it was discovered through experimentation that the third magnet often did little to improve the cleaning process of two magnets, much less spur the need for a fourth magnet.
All of which brings us closer to today’s designs. First of all, with the introduction and fine tuning of water injection systems, dust control, cleaning and explosion reduction (not elimination, of course) have all been greatly improved.
The current debate has drawn down to whether two magnets are best or only one.
The answer is actually quite simple and it comes back to the air system variable. If it is decided that only one magnet is going to be used, then an air system will almost certainly have to be used to obtain a relatively clean product. This is supported by the fact that there are virtually no "one magnet" systems operating without a z-box. The down side of this method is that the air system supporting one magnet has to aspirate harder to achieve a clean product. This results in more losses of ferrous and nonferrous metals through the air system.
Two drum magnets in line are extremely successful in various systems throughout the world. They can generally match or exceed the performance of a single magnet plus z-box system, although their success relies on one major variable: the volume and speed of material as it is exposed to the magnets. Simply speaking, if you flood material to the magnets without allowing the magnets adequate time or space to do their work, the less cleaning capacity they will have.
The two drum magnet systems have of course become more successful due to the development of the electro-magnetic alternating pole drums that provide extremely vigorous agitation of the material as it travels over the magnets. For some but not all operators, the effectiveness and strength of some magnets have actually eliminated the need for the first vibratory feeder in front of the first magnet, reducing cost and maintenance of the ferrous system. Eliminating the first vibratory feeder before the first drum is also advocated by some because at no time is the material to be cleaned more spread out than it is on the take-away conveyor immediately following shredding. The argument is that a vibratory feeder before the first magnet only increases the depth of the material because it is much slower than the speed of the take-away conveyor. The correct rotational speed of the drums is also important to consider.
Two-drum systems are even used successfully in high capacity shredding systems that clean in excess of 250 tons an hour, simply by splitting the stream and having individual sets of two drum magnets in each line. If it is decided a z-box is still needed to achieve maximum cleanliness of the shred, the z-box does not have to work nearly as hard after two magnets, greatly reducing the amount of fines lost through the air system, as can happen with one-magnet systems.
The old argument by some that a system loses more ferrous into the nonferrous line when exposing it to the second magnet has largely been proven false by operators simply placing an over-belt electro magnet prior to nonferrous separation. The volume of ferrous material lost is extremely minimal.
Bottom line? While one magnet with a supporting z-box air system is viable as proven by a couple of manufacturers, the advantages of two magnets (with or without air) make this system a more effective and often a less costly approach to clean shred.
The author is president of U.S. Shredder & Castings Group, www.usshredder.com.
![]() | The Garden Center Conference & Expo, presented by Garden Center magazine, is the leading event where garden retailers come together to learn from each other, get inspired and move the industry forward. Be sure to register by April 17 to get the lowest rates for the 2025 show in Kansas City, Missouri, Aug. 5-7.
|
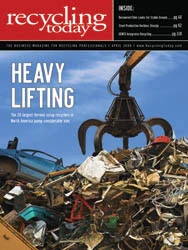
Explore the April 2009 Issue
Check out more from this issue and find your next story to read.
Latest from Recycling Today
- ReMA board to consider changes to residential dual-, single-stream MRF specifications
- Trump’s ‘liberation day’ results in retaliatory tariffs
- Commentary: Waste, CPG industries must lean into data to make sustainable packaging a reality
- DPI acquires Concept Plastics Co.
- Stadler develops second Republic Services Polymer Center
- Japanese scrap can feed its EAF sector, study finds
- IRG cancels plans for Pennsylvania PRF
- WIH Resource Group celebrates 20th anniversary