
The success of our global economic system depends heavily on the intelligent use of raw materials. Faced with global resource depletion, manufacturers are increasingly turning to recycled raw materials.
The total production of plastics topped 311 million tons worldwide in 2014. Plastics are in almost everything we use. Yet even at the end of their service, plastics still are far too valuable to just throw away. Some can be recycled into the same or a different product. Others can be used for energy recovery or as a substitute for fossil fuels. About one-third of the world’s countries already recycle or recover more than 80 percent of their plastics, whereas many lag far behind, and some fall short of their own legislative targets.
Today, recycled plastics already make a major contribution to meeting resource efficiency targets. Interseroh Dienstleistungs GmbH, a subsidiary of German recycling firm ALBA Group and one of the leading environmental services and raw material providers worldwide, converts recycled plastics into high-quality plastic granules.
The process exclusively uses secondary resources from household collections and industry and turns them through upcycling into materials with a quality comparable with the properties of new materials. Interseroh’s award-winning plastics recompound, Procyclen, matches virgin material in properties and quality and is a fully customizable, safe, sustainable and cost-effective secondary raw material suitable for quality plastics products.

CLOSING THE LOOP, NOT ENDING IT
Though plastics often are touted as recyclable, in reality many of them are “downcycled” and end up in low-end applications. Such materials perform poorly in reprocessing, and the end product can age faster when exposed to heat and weathering.
On the other hand, today’s manufacturers most often demand materials that meet high quality standards and boast competitive or even better properties than virgin material. This demand created a need for innovative recycling technologies that guarantee the development of high-quality, tailor-made products derived completely from recycled material as a substitute for virgin plastic.
With its unique closed-loop method called “recycled-resource,” Interseroh took a new approach and implemented a recycling process that turns impure, low-quality mixed plastic packaging scrap into high-quality, tailor-made compounds without compromising quality, thereby lending plastic material a second lease of life.

This unique upcycling method produces a high-quality plastics recompound named Procyclen, made of nearly 100 percent mixed postconsumer plastic packaging scrap. Procyclen’s technical specifications match the properties of virgin material. The technology itself is safe, sustainable and efficient and boasts high economic, social and environmental added value.
MULTIPLE STEPS AND STAGES
Generally speaking, used plastic material cannot simply be reused because it is sourced from mixed municipal waste streams of unknown origin.
The Interseroh recycled-resource process follows up high-tech sorting with a unique recompounding sequence featuring extrusion, restabilization, molecular structure rebuilding and chemical modification. A key final step is to achieve material performance that exactly conforms to the customer’s strict specifications.
Additives and modifiers are combined to obtain specific complementary effects and interactions for a top-quality end product with enhanced structure and properties. Unlike lower-quality reclaimed plastics, Procyclen is a full match to virgin material in properties and quality.
More and more producers are selecting Procyclen for their new products. One of the first product lines Interseroh developed, together with a leading European manufacturer of resin household products, was a line of boxes, baskets and bins.
In 2014 Interseroh developed a renewed correction and glue roller packaging where the back of each case consists of customized Procyclen produced from polystyrene. As best practice examples, these products show that producers are willing and able to manufacture responsibly—and to use high-quality recycled-content materials that meet their strict specifications as a sustainable resource.
In the case of declining natural deposits for some raw materials, the development of such uses for scrap materials is without alternative. In Germany alone, each year companies process raw materials to the value of $565 billion (€500 billion).
This figure reveals the savings potential through efficiency raising measures: a 20 percent rise in material efficiency would lead to a savings of $113 billion (€100 billion).

Entrepreneurs already count the development of energy and raw material prices as one of the biggest risks over the next years. The recycling of discarded materials is one necessary answer to this, and its importance will rise in the approaching years.
Taking this development into account, new technologies such as Interseroh’s recycled-resource process will become more and more important to a sustainable, competitive economy and society.
RESOURCE EFFICIENCY IN EVERY RESPECT
Plastic products account for just 4 percent of fossil fuel consumption. Paradoxically, using more plastics actually would cut overall fossil fuel consumption and greenhouse gas emissions—and contrary to popular belief, using less would boost overall fossil fuel consumption and greenhouse gas emissions.
Interseroh’s recycled-resource upcycling process not only offers an economically sound option of high-quality plastic raw material supply but also protects natural resources and the environment.
Additives and modifiers are combined to obtain specific complementary effects and interactions for a top-quality end product with enhanced structure and properties. Unlike lower-quality reclaimed plastics, Procyclen is a full match to virgin material in properties and quality.
Compared with primary products, plastic recompounds such as Procyclen have the advantage that no crude oil is used during the production process, the energy input is significantly reduced and the emission of climate damaging and ecologically harmful greenhouse gases is cut by up to 50 percent.
The first new products made from Procyclen, including laundry baskets and transport crates, already bear this label. This is a visible sign of environmental protection and resource efficiency.
Interseroh’s innovations for high-quality recycled materials show that a closed loop for plastics is indeed possible—and that far from being a low-grade surrogate, recycled-content plastics can be a new resource with increased market value. By constantly doing more with less, using plastics also tends to lower the consumption of raw materials. Not only does this boost resource efficiency, it also provides consumers with increasingly cost efficient answers to their needs.
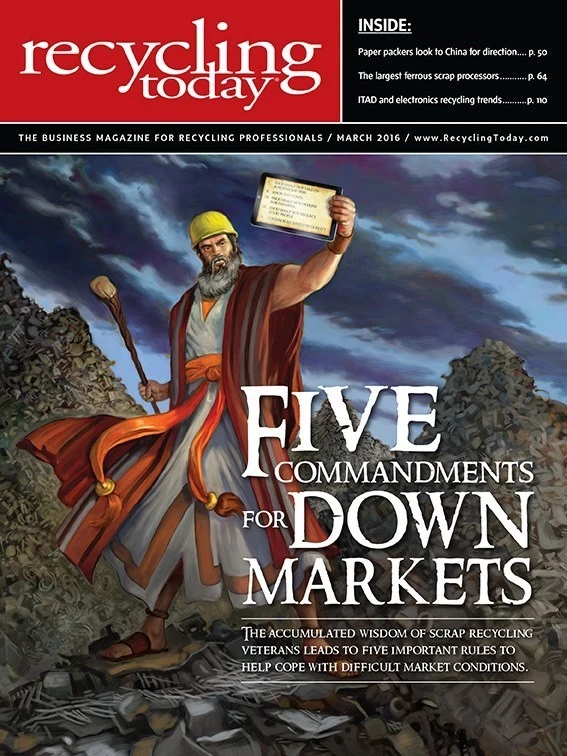
Explore the March 2016 Issue
Check out more from this issue and find your next story to read.
Latest from Recycling Today
- BlueScope, BHP & Rio Tinto select site for electric smelting furnace pilot plant
- Magnomer joins Canada Plastics Pact
- Out of touch with reality
- Electra names new CFO
- WM of Pennsylvania awarded RNG vehicle funding
- Nucor receives West Virginia funding assist
- Ferrous market ends 2024 in familiar rut
- Aqua Metals secures $1.5M loan, reports operational strides