
According to the Washington-based Recycled Rubber Coalition (RRC), which operates with support from the Recycled Materials Association (ReMA), most end-of-life tires were dumped in landfills or illegally discarded in the 1990s. Additionally, Stratton Kirton, vice president of government affairs at Pittsburgh-based Liberty Tire Recycling, says the U.S. had 1 billion tires sitting on the ground by the end of that decade.
Since then, states have implemented tire recycling programs, and, now, most of those 1 billion tires have been recycled or properly disposed of. However, tire recycling and illegal dumping will remain a challenge until proper and tested markets are available for recycled tires, Kirton says.
“The challenge for states is thinking about laws that were put in place to address a problem 20 to 30 years ago. How can we modify those laws to handle the current challenge, which isn’t cleaning up historic tire piles; it’s finding more markets for recycled rubber as the number of tires [grows],” Kirton says.
But some companies handling end-of-life tires lack the infrastructure and funds to properly dispose of and recycle them.
“[With] a certified, sustainability-oriented company ... you can be assured those tires aren’t going to end up anywhere other than where they are supposed to go, which is recycling and responsible disposal,” says Andrew Meurer, president and chief operating officer at Liberty Tire Recycling. “When you have startup companies that charge way less, they typically don’t have the invested capital in machinery we have.”
Liberty works to responsibly recycle end-of-life tires by collecting, processing and manufacturing its own products from the recycled tire rubber it produces. The company also works with states to help clean up tire piles and illegal dumps through amnesty days.
ReMA, based in Washington, works with member companies like Liberty and other stakeholders to ensure state laws for tire recycling reflect industry needs.
“The tire recycling industry in the U.S. has been one of the most successful recycling industries in the history of the entire country, and we want to continue that success and make sure we are staying ahead of emerging trends that may be bringing more tires off the road,” Kirton says.

Rise of electric vehicles
To combat CO2 emissions, many companies are introducing electric vehicles (EVs) to the market. EV production also is influenced by government-set sustainability goals aimed at reducing CO2 emissions and pollution.
Sales of EVs jumped 54 percent from 2022 to 2023, but with their rise comes a potential issue: increased tire waste.
A white paper issued by the RRC, which is comprised of companies focused on innovations in recycled rubber such as Liberty Tire, Ecore International and Regupol America, all based in Pennsylvania, demonstrates just that. According to the paper, the U.S. will produce about 352 million scrap tires per year by 2030, up from the current 315 million. Of that 2030 total, 37 million are expected to come from EVs.
“We wanted to make sure there wasn’t an unintended environmental consequence that made EVs less desirable,” Kirton says of the RRC white paper. “Our vision for this was making sure we are putting a spotlight on it, not because we think EVs are a problem, but because we want to get ahead of a potential side effect of greater EV adoption.”
EVs are about 20 percent heavier than typical internal combustion engine vehicles because of their batteries. This added weight results in additional wear and tear on the tires. EVs also have instant torque and acceleration, which adds friction wear to the tires. Tires on internal combustion engine vehicles typically last 50,000 miles, while EV tires last about 20,000 to 40,000 miles.
“EVs obviously add to the wear of tires,” ReMA Senior Economist Bret Biggers says. “Whatever manufacturers do to increase the longevity and safety of EV tires to account for the vehicle performance changes, they [should] do so with recycling in mind.”
Addressing tire manufacturing
In “The ReMA Position on Scrap Tire Design for Recycling,” the association looks to balance tire manufacturers’ needs for safety and quality with recyclers’ need to maximize their yields of recoverable materials, calling for tire manufacturers to embrace design for recycling.
ReMA maintains relationships with the U.S. Tire Manufacturers Association and the Tire Industry Association, sharing the need for sustainable tire design.
“We encourage recyclers and tire manufacturers to work together to come up with a way that tires can be recycled [at] end of life even though we understand that safety and longevity are at the forefront of a tire manufacturer’s goals,” Biggers says. “In doing so, we hope they also can make it so those new ingredients that are added are also recyclable at the end.”

Raising the rate
The RRC reports that the tire recycling rate decreased from 96 percent in 2013 to 71 percent in 2021.
“That will need to be addressed by developing new markets and expanding any existing markets to ensure that the materials are properly recycled rather than going to disposal,” Biggers says of the tire recycling rate. “We have to make sure there’s a market for that extra rise.”
The RRC calls for several solutions, such as establishing policies that support market expansion, federal grants to expand recycled rubber uses and ensuring all 50 states have fees on the purchase of new tires, which the organization says are critical for reducing illegal tire dumping and encouraging more end uses for recycled rubber.
One proposed solution is using recycled rubber in rubber-modified asphalt (RMA). The RRC says RMA benefits transportation departments’ budgets, motorists and the environment, noting that it increases the lifespan of roads, produces 32 percent fewer emissions and reduces costs by 43 percent.
The RRC white paper notes, however, that the current market for RMA uses only 3 percent of the total scrap tires generated annually in the U.S.
RMA is one of the most recognized markets for recycled rubber, and this mix of asphalt and ground tire rubber is financially and environmentally sustainable, Kirton says. It is beneficial in new road construction and can be used as chipseal, which makes existing roads last longer.
“A 2-inch-thick RMA resurfacing project uses about 2,000 scrap tires per lane mile; that means that a project on a four-lane highway uses 8,000 scrap tires per mile,” the RRC writes. “With an estimated 8.7 million miles of road lanes across the U.S. and recent federal investment in infrastructure, there is ample opportunity to put scrap tires to use and expand the use of RMA.”
Expanding end markets
A variety of recycled rubber products is available, and many others are in different stages of development. These products, such as RMA, tire-derived aggregate, sound barriers, rubber mulch and rubber flooring, represent important investments in expanding the market for recycled rubber, tire recyclers say.
Recycled rubber can be used to make sound barriers for public transportation. To grow that market, Liberty works with Canadian company Eco-Flex, which manufactures Eco-Wall and HD Eco-Wall panels from 100 percent-recycled rubber.
Meurer says most sound barriers are made of concrete and can weigh up to 1,200 pounds. But Eco-Flex says the company’s recycled rubber sound barriers are proven to provide privacy and reduce nearby noise, improving the quality of life for people who live adjacent to commercial areas, industrial parks, parking lots, shopping centers and playgrounds and along highways and railways.
To expand end markets such as rubber mulch and flooring tiles, Liberty works with large retailers it collects tires from to close the loop. These tire retailers often make use of rubberized asphalt in their parking lots, recycled rubber tiles for their flooring and rubber mulch in their landscaping, Meurer says.
“They’re not only committed to making sure the tires they take off customers’ cars are going to responsible disposal, they are actually closing the loop by purchasing and utilizing those products within their stores as an excellent way to demonstrate circularity,” he adds.
Educated solutions

Additional research is needed to fill gaps in the marketplace, Kirton says, adding that for RMA to be competitive in federal infrastructure projects, it needs to show it lowers emissions by a certain percentage. Kirton says the government is creating an environmental product declaration (EPD) for that purpose and to be used industrywide to fill the knowledge gap.
Industries must think differently about incorporating recycled content in their products as it can produce a product that is similar to or better than virgin material and offers environmental benefits, too. Manufacturers using virgin rubber can use recycled rubber, and recycled rubber also can be used to replace virgin plastic, concrete and wood in products.
Sponsored Content
Still relying on manual sorters?
Let AI do the heavy lifting. Waste Robotics delivers reliable, high-performance robots tailored for complex waste streams. They require minimal maintenance, are easy to operate, and are designed to boost your recovery rates. Smarter sorting starts with the right partner. Waste Expo Booth #1969 & REMA #2843
Click here to see our robots in action!“I think it’s getting people to think differently,” Kirton says. “‘We’ve always manufactured a product this way, [but] how can we replace what we are using with recycled content?’”
Large retailers might often support sustainability and circularity, but they generally are not manufacturing their own products and instead purchasing them from different suppliers.
Kirton says, “Our job is not only to convince big retailers but also to try and reach their suppliers and convince them [they can lower emissions and still be price competitive].”
The RRC says a health misconception continues to surround the use of recycled rubber in poured-in-place surfacing for playgrounds, rubber mulch and artificial turf after an associate soccer coach at the University of Washington an associate soccer coach at the University of Washington claimed in the 2010s that athletes developed cancer from playing on synthetic turf.
According to the RRC, no chemical change occurs when recycling rubber and more than 100 scientific studies, including government reports, show recycled rubber poses no health risks.
“Somehow, we have to get education out there to the state lawmakers that this is not an issue,” Biggers says of the health concerns surrounding synthetic turf that contains recycled rubber. “Laws and policies are still coming forward from the states addressing the negative aspects of recycled rubber, but there are none.”
Implementing policy
Recycling regulations mostly are governed state by state, creating a variety of laws. Some states have efficient systems for tire recycling, while others don’t pay much attention to it until an issue arises.
Three policy standards need to be normalized for local and state legislators to combat illegal tire dumping and irresponsible recycling, Biggers says, adding that the fee most states assess on the sale of new tires must cover the cost of end-of-life management. Next, dedication to tire transportation, recycling, cleanup and enforcement is crucial. Finally, Biggers says, policymakers must ensure oversight so that all end-of-life tires that are generated make it to tire recyclers.
Many states have implemented registration requirements and tire manifest systems for haulers, though enforcing these requirements can be a challenge when law enforcement agencies must prioritize resources.
“Part of my job is educating lawmakers on this,” Kirton says. “Lawmakers have many different issues that they have to handle, and this is a technology that a lot of them aren’t familiar with, so part of my job is to go to them and make sure they understand it.”
According to the RRA, to meet the projected increase in end-of-life tires, state legislatures must establish programs, whether in the form of grants to help establish projects or rules to ensure collected tires end up at approved recycling facilities. The industry also must share the economic and environmental benefits of tire recycling with policymakers.
Get curated news on YOUR industry.
Enter your email to receive our newsletters.
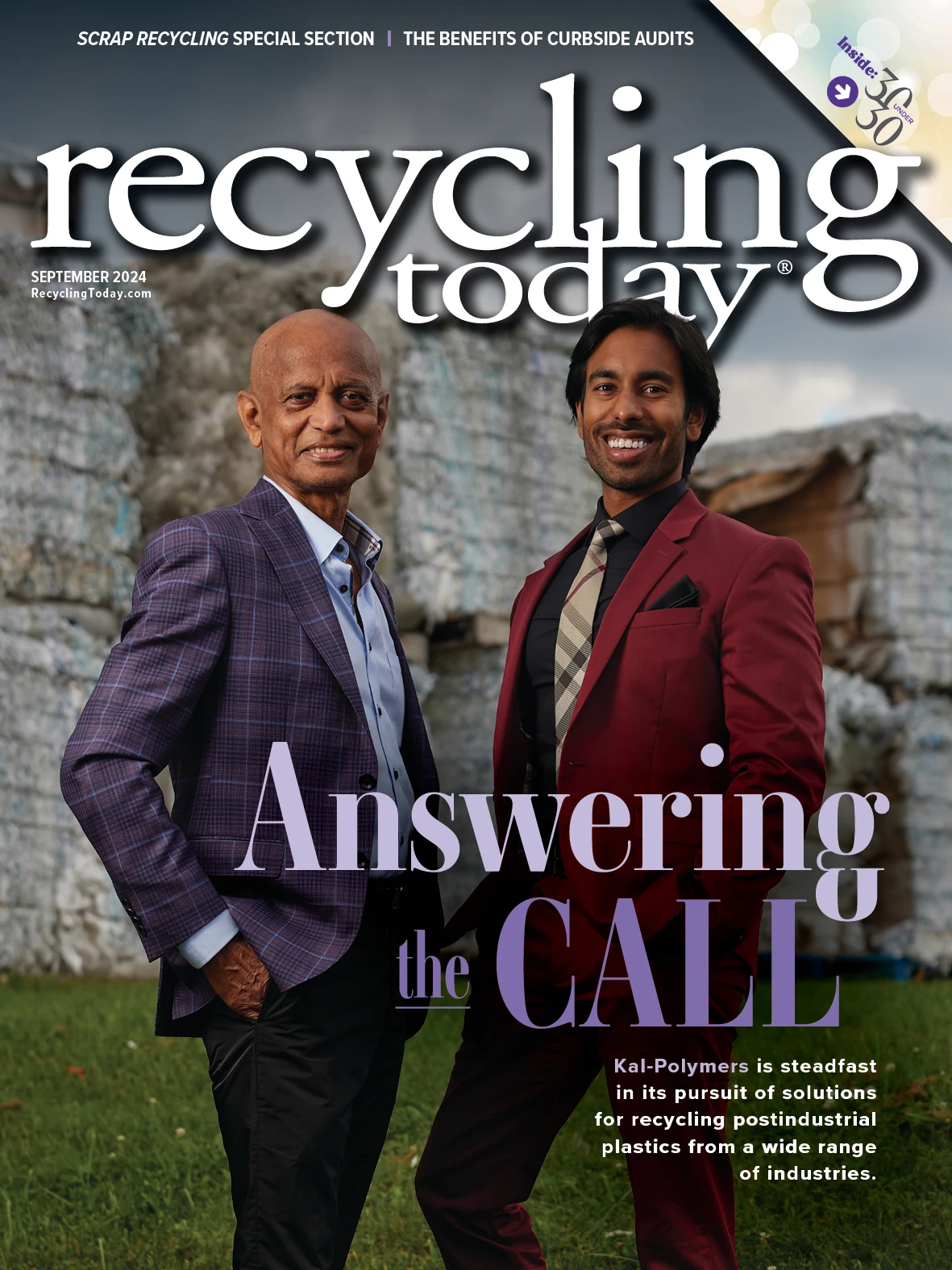
Explore the September 2024 Issue
Check out more from this issue and find your next story to read.
Latest from Recycling Today
- Call2Recycle Canada launches program in Alberta
- The history of SAS Forks: Celebrating 50 years
- SAS Forks partners with NED at Green Recycling in Houston, Texas
- DRKhorse’s RCC series at Gorick Construction in Endicott, New York
- Balar Equipment to operate under Enviro-Clean Equipment name
- Li-Cycle reports 2024 financials
- Wisconsin Aluminum Foundry acquires Anderson Global
- PureCycle, Landbell Group working to advance PP recycling in Europe