If shredders and grinders were sold in the supermarket, the number of choices available is enough to take up far more than just one aisle.
Ranging from large-volume tub grinders to smaller shear-shredders, manufacturers are offering a host of equipment of varying throughput and flexibility.
After considering what end products they are going to produce and how much material they are likely to process in a given operating hour or day, recyclers will then be able to compare and contrast a variety of size reduction equipment.
IN THE TUB
Tub grinders have been downsizing material for the forestry and recycling industries for decades. The machines can be built to mammoth proportions, with the larger ones having the ability to chew through tree stumps and other sizable pieces of debris.
Larger tub grinders can be powered by engine combinations creating more than 1,600 hp, and make claims to handle tree stumps up to nine feet in diameter. The specs for one such model claim it can process up to 130 tons per hour of pallets and construction debris.
GETTING THEIR FILL |
Landfill operators have been another key market for shredders, and many of them diversify into recycling once they have their machines in place. John Foote, vice president of sales and marketing with Morbark Inc., Winn, Mich., says most landfill managers are eager to enter recycling markets if they see an opportunity. "When they buy a shredder with a magnetic end pulley, they are recycling," he notes. Tim Griffing of Continental Biomass Industries Inc. (CBI), Newton, N.H., sees metals recovery as the top priority for many landfill operators. "The primary recyclable they seem to want to get into is the metals. Often, they get the metals out while the rest of the material is ground up and reduced in size to extend the landfill life," he remarks. Beyond metals recovery, many also start to explore the potential markets for wood chips and shreds. "Many landfill operators are turning their end products into saleable, recycled products such as compost, mulch or colored mulch," he adds. "What they choose to do with the end product determines if they have a profitable recycling program or not," Foote continues. "Even if they are just using the shredded end product for daily landfill cover and they are reducing their cost of trucking in [out-sourced] daily cover, then they have a successful recycling program," he contends. John Dorscht, president of SchredMax, Petrolia, Ontario, Canada, notes that fine materials (soil and other small particles) can represent as much as 30 percent of a mixed C&D stream and that this represents another potential end market in the form of lower-grade soil markets such as for berms or as a sloping and grading material. Whether separating metals, making mulch or looking into other markets, Dorscht believes most landfill operators are more than willing to take a look at recycling. "It’s to their benefit to find markets for their product and not just landfill it," he states. |
But they can also be built to smaller specifications with an eye on operating efficiently. DuraTech Industries, Jamestown, N.D., makes models in several sizes. "We’ve been building tub grinders since 1966," notes Bob Strahm, industrial division sales manager for DuraTech.
The company’s newest machine, the Model 3010, is powered by a 463 hp Caterpillar electronic engine with features that include a heavy-duty hammer mill, a fluid clutch with push-button start-up, a 3-inch wide oscillating stacking conveyor and a self-cleaning radiator screen.
LONGER LIFE |
Just because a grinder can hammer away at a 5-feet-in-diameter tree stump doesn’t mean that it should, many manufacturers agree. Looking for unshreddable contaminants as well as pre-processing larger pieces that could slow down a grinder or shredder are two of the important production and maintenance tips passed on by manufacturers. Even though new models are increasingly designed to eject hard metal objects that don’t belong in their hoppers, recyclers should not take a lax attitude that pre-sorting is a thing of the past. In addition to sorting out the unshreddables, manufacturers such as John Dorscht of SchredMax, Petrolia, Ontario, Canada, say that while their machines can handle brick and block, doing so comes with a price tag. "You’re better off not putting masonry-based materials like brick, concrete and rock through, because they’re so abrasive." Tim Griffing of Continental Biomass Industries Inc. (CBI), Newton, N.H., says masonry dust and soil can wear down the teeth of a grinder. "It causes the highest amount of wear—it sandblasts the rotor," he comments. Pre-screening of fines is the most common way to reduce the amount of fine material hitting the teeth of a grinder or the wear parts of a shredder. Tub grinder operators may be tempted to throw thick tree stumps and long tree limbs into the tub because, well, they can. But John Foote of Morbark Inc., Winn, Mich., recommends doing some pre-processing with a shear on such large pieces in order to keep grinder productivity higher. |
"We think people in the wood-grinding industry will really be excited about this machine when they see its capabilities," says Strahm, who calls the Model 3010, "a heavy-duty, reliable machine using the latest in technology — a machine that can handle any wood grinding job efficiently and cost-effectively."
Medium-range models such as 800 hp units are still powerful enough to work in large-volume applications.
A case study prepared by Vermeer Manufacturing Co., Pella, Iowa, describes how a Florida contractor used a Vermeer TG800 machine to clean up several stockpiles of oak land-clearing debris, including pieces more than four feet long. "With the TG800, we finished the job in just over four weeks," notes Steve Lubbers of Consolidated Resource Recovery Inc., Sarasota, Fla. "We hit goal and earned our money because we finished ahead of schedule."
The ruggedness of the tub grinders makes them a first choice among recyclers who want a machine in which they can place a large but often varying volume of material. "For companies whose businesses extend across a broad range of grinding requirements, the tub grinders are still the most versatile machines on the market," says John Foote, vice president of sales and marketing with Morbark Inc., Winn, Mich.
The major drawback of the machines for recycling applications is their tendency to shoot out pieces of debris in the grinding process. While more often than not these are smaller chips that are more of a nuisance than anything else, occasionally larger pieces can be hurled from the machines.
Several years ago, a recycling company near Fort Lauderdale, Fla., was operating a tub grinder when a piece of debris shot out of the tub and traveled several dozen yards, landing in a residential front yard and, in fact, knocking the wooden leg off of a man who was sitting on his patio.
In part to avoid such incidents, recyclers have been increasingly looking both at safety modifications for their tub grinders and at grinders and shredders using other configurations and technology to downsize material.
Equipment makers such as Morbark have monitored and responded to this trend, and now offer horizontal and vertical-feed grinders as well as slower-speed shredders that process materials in a different way altogether.
ON THE HORIZON
Recyclers who still want grinding power and throughput without the risks of a tub have helped popularize horizontal grinding mills. "The companies involved in high-traffic areas are moving into horizontal machines," says Foote. "The production and safety of those machines make them very popular."
Similar to the enclosed horizontal mills are vertical-feed models, where material is fed to the grinder rotor through an enclosed metallic chute that moves upward until dropping materials onto the spinning rotor.
The Fort Lauderdale recycler who experienced the tub grinding accident eventually switched to a large-volume enclosed-rotor mill made by Continental Biomass Industries Inc. (CBI), Newton, N.H.
Tim Griffing of CBI says the company’s Grindall horizontal and vertical-feed mills remain popular with recyclers. "Our number one unit is the vertical-feed 5060 Grindall. It’s powerful—with a rotor that weighs 19,000 pounds," notes Griffing. He says the machine can "easily handle" 70 tons per hour of material.
West Salem Machinery, Salem, Ore., is another company that touts its machines as durable pieces of equipment. The company’s Model 4064BR features what it calls a "severe-duty" rotor with tungsten carbide hammer tips that can be reversed for maximum wear life. The machine’s interior is lined with bolt-in wear-lines that can have a thickness of up to two inches.
Griffing notes that the mixed C&D market is a growth market for these types of machines. "We can handle the metal contamination—our high-inertia rotors with shear pin protection are built to be heavy and solid." The Grindall machines also feature a ballistic chute that safely re-directs unshreddables (such as manhole covers and steel rail) that might enter the machine.
The machines are built by several manufacturers in several sizes, meaning recyclers should be able to find a model that suits their production requirements. The machines can also be modified to address a specific application.
The HC 2400-B by Peterson Pacific Corp., Eugene, Ore., can be equipped with either a 450-hp or 580-hp engine. The larger engine offers throughput of up to 337 cubic yards per hour, according to the company.
While wood and mixed materials are among the most common C&D materials to enter such machines, Peterson Pacific has also found a niche with asphalt shingle recyclers.
One California recycler endorses the HC 2400-B (customized for the application) as the machine that has best met his need for turning scrap asphalt shingles into half-inch-minus shreds at a rate of 75 tons per hour.
SLOW AND STEADY
For recyclers who want quieter production, lower energy costs and yet need a machine that can handle a mixed material stream, slow-speed, high-torque shredders are providing an alternative.
Other recyclers are using such machines not as an alternative to grinders, but as a primary machine that prepares material for further size reduction in a grinding mill.
Long-time grinder manufacturer Morbark is debuting its first slow-speed, high-torque shredder at this year’s WasteExpo event. Many manufacturers advise recyclers not to be turned away by the adjective "slow-speed," because these machines can still be made to shred material at a productive clip.
John Dorscht, president of Schred-Max, Petrolia, Ontario, Canada, has spent several years working with and designing shredding equipment.
His current company makes high-torque shredders elevated to allow material to fall directly into a bin or container. They are marketed toward recyclers seeking a primary shredder that can handle a mixed stream of materials.
Dorscht has found that demand is out there for high-volume machines. "We started with a small machine and have built increasingly larger models," says Dorscht.
Steady demand has come from mixed C&D recyclers, he notes. "Most C&D recycling facilities accept commingled materials in containers. It comes in all shapes, sizes and lengths."
Dorscht says most of these recycling facilities will hand-pick larger pieces of metal, cardboard and other recyclable material, but that further size reduction is needed before sorting can continue. "The whole idea behind SchredMax is to reduce material to a size such as 12 or 6 inches and under where it can go on a conveyor and be magnetically and hand-sorted at a manageable size."
While to some observers making pieces smaller before pulling them off a conveyor may seem to make the task more difficult, Dorscht says it is necessary to make it safer. "You don’t want pickers trying to pick off 80-pound pieces of debris," he remarks.
The number of manufacturers serving this emerging market has multiplied, with primary machines having different configurations and specifications.
FOR MAMMOTH TASKS |
With its 610-hp DaimlerChrysler diesel motor, the Doppstadt Mammoth offers as much shredding power to the C&D industry as anything on the market, according to promotional material from DoppstadtUS, Haslett, Mich. The Mammoth is capable of processing up to 90 tons per hour of a mixture of infeed materials, including C&D debris, railroad ties, wood waste, tires and other green waste, according to the company. The machine features a single bolted-tooth shaft working through a hydraulically actuated, sensor-controlled comb that can open and close at adjustable pressures, depending on the specific application. This flexibility is designed to eliminate the need for pre-sorting and the risk of downtime from bridged material, especially when processing mixed C&D materials or railroad ties. Unshreddable steel items that pass through the comb are separated from the material flow by a large, self-cleaning permanent magnet. Power is transferred through a direct, reversible gear drive to the slow-turning, 35 rpm shaft, giving the machine sufficient power to reduce large stumps and other bulky infeed to a 6-inch sized product. The Doppstadt Mammoth joins the ranks of all-purpose shredders marketed to appeal to users with a variety of material to be reduced in size. |
Most of them, such as Hammel North America, Fort Wayne, Ind., or Dopp-stadtUS, Haslett, Mich., market their machines as offering the ability to handle a wide range of materials while creating minimal dust and noise.
The Hammel Shredder is advertised as being able to handle "whatever you grab," including brick and block, wood and metal framing, appliances, carpeting, furniture and green waste.
These all-purpose models are finding buyers, with the crowded field being joined by Morbark in 2003. "We believe the growth market for shredders will be with the slow-speed, high-torque machines," says Foote. "The advantages for the contractor are lower operating costs and [the ability to process] contaminated debris."
The author is editor of
C&D Recycler and can be contacted via e-mail at btaylor@cdrecycler.com.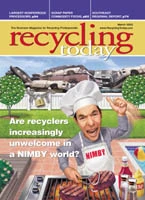
Explore the March 2003 Issue
Check out more from this issue and find your next story to read.
Latest from Recycling Today
- Nucor receives West Virginia funding assist
- Ferrous market ends 2024 in familiar rut
- Aqua Metals secures $1.5M loan, reports operational strides
- AF&PA urges veto of NY bill
- Aluminum Association includes recycling among 2025 policy priorities
- AISI applauds waterways spending bill
- Lux Research questions hydrogen’s transportation role
- Sonoco selling thermoformed, flexible packaging business to Toppan for $1.8B