The company name pretty much tells it all—Kroeker Inc. Demolition & Enviornmental. "Not only can we knock it down," says Jeff Kroeker, son of the company founder, "but we can recycle just about everything that comes off the jobsite."
That is because in addition to the usual demolition equipment and a small C&D landfill, Kroeker Inc. Demolition & Environmental, Fresno, Calif., has invested in recycling machinery to crush concrete and to process mixed C&D materials and land-clearing debris as well.
That is a far cry from when the company started 21 years ago as Kroeker Custom Tractor Service, providing lot discing and finished grading work at new subdivisions.
"The company started to expand when the land developers asked us to clear and grub the property for the next subdivision," says Jeff Kroeker. "So with some rented equipment and the opportunity to prove ourselves, we worked seven days a week, but we got it done. We kept getting asked to do a little more with each project."
Today the demolition company employs about 180 people, involved in a variety of activities including concrete crushing, tree and orchard removal, a division dedicated to full-service concrete cutting and core drilling and a roll-off service with more than 250 boxes. About 70 percent of the company’s revenue comes from demolition work, with the rest from recycling.
A MILITARY SITUATION
Most of Kroeker Inc.’s jobs are commercial/industrial, though a current project—maybe the most high profile job the company has ever had—is predominantly residential.
The decommissioning of the sprawling Fort Ord military complex beside Seaside, Calif., near Monterey, is a huge project covering thousands of acres. For several miles the base is on beautiful seafront property. The former base is in an area experiencing a housing shortage, so there is a lot of local pressure to get the land cleared of the thousands of military structures on the site to allow for development.
However, extensive troop training took place at the site over the years, and contamination of all types is present. In addition, because the land is very valuable and because of environmental concerns, many governmental agencies are involved in the reclamation and development project. Says Kroeker, "Everyone wants to play a role in this project, and for good reason, as this is just the beginning of private development at Fort Ord, so they want everything to go smoothly."
Kroeker Inc. has always prided itself on keeping its demolition and recycling jobsites clean, says Jeff Kroeker. It is a practice that is paying off at Fort Ord. Concrete is separated out into one pile, metal into another and building debris into a third. "We try to keep all of our jobsites that way," says Kroeker. "We systematically tear down each structure with the thought of recycling. We segregate the different commodities for ease of loading and transport, keeping the end product in mind at all times."
"Demolition is considered a dirty job," he says, and then sweeps his arm across the site. "But as you can see, it doesn’t have to be dirty; it can be neat and clean."
The Fort Ord job has included demolishing more than 350 concrete structures that formerly housed many soldiers and their families. The buildings themselves seemed relatively unremarkable—concrete, single and double-family units built on concrete slabs in the early 1940s. But as might be expected, there was more to it than just yanking them down and sending the concrete over to the company’s crusher for recycling.
"What was different about these houses is that all of the walls and ceilings were concrete panels that were tied together with a lot of steel," says Kroeker. "Even though these buildings are mostly concrete, there was a need for a strip-out beforehand. We sent laborers in to remove all of the wood and organics prior to knocking down the concrete structures."
That still left the concrete, which had lead-based paint (LBP) on it. The abatement contractor had to remove all the loose paint on the buildings, but some remained. The local air board questioned whether the concrete could even be recycled with LBP on it, even though the amount present was below EPA tolerances. After some negotiation, an extra fee was assessed to the crushing operation. Kroeker was allowed to mobilize its Eagle Crushing Co. Model 1400 horizontal impact crusher to a site at Fort Ord within five miles of the demolition jobsite. There, more than 100,000 tons of concrete was processed into a Class II roadbase product that meet all CalTrans specifications, rather than being hauled off to a landfill.
ARMED AND READY
For demolition excavators, Kroeker Inc. "uses a little bit of everybody’s", according to Jeff Kroeker. Caterpillar, LinkBelt and John Deere machines are all at the Fort Ord site. They are fitted with LaBounty concrete processors, grapples and thumbs, and one is fitted with an Allied breaker.
The roof and wall concrete is processed on the slab, removing as much rebar as possible before being transported to the crusher. Another excavator with a processor attachment is located there, as well. The slabs are then removed and processed in the same manner, sizing the footings for loading and transport, Kroeker says.
Land clearing debris is also recycled. "Before [the project] is over, about 900 trees of all shapes and sizes will be removed and processed through our Morbark Model 1300 tub grinder," says Kroeker. "It still makes the hair stand up on the back of my neck to hear that 1,000 hp engine go to work on those stumps.
"Once the trees and houses are removed, we’ll work our way out, removing the streets, curbs and gutters and, finally, the utilities," Kroeker continues. "After the streets are removed, you can’t get back into the work area because of all the beach sand that blows in from across the highway, so we will finish everything prior to street removal." The developer will start over with new infrastructure at the site, according to Kroeker.
Sponsored Content
Labor that Works
With 25 years of experience, Leadpoint delivers cost-effective workforce solutions tailored to your needs. We handle the recruiting, hiring, training, and onboarding to deliver stable, productive, and safety-focused teams. Our commitment to safety and quality ensures peace of mind with a reliable workforce that helps you achieve your goals.
Sponsored Content
Labor that Works
With 25 years of experience, Leadpoint delivers cost-effective workforce solutions tailored to your needs. We handle the recruiting, hiring, training, and onboarding to deliver stable, productive, and safety-focused teams. Our commitment to safety and quality ensures peace of mind with a reliable workforce that helps you achieve your goals.
Sponsored Content
Labor that Works
With 25 years of experience, Leadpoint delivers cost-effective workforce solutions tailored to your needs. We handle the recruiting, hiring, training, and onboarding to deliver stable, productive, and safety-focused teams. Our commitment to safety and quality ensures peace of mind with a reliable workforce that helps you achieve your goals.
Sponsored Content
Labor that Works
With 25 years of experience, Leadpoint delivers cost-effective workforce solutions tailored to your needs. We handle the recruiting, hiring, training, and onboarding to deliver stable, productive, and safety-focused teams. Our commitment to safety and quality ensures peace of mind with a reliable workforce that helps you achieve your goals.
Sponsored Content
Labor that Works
With 25 years of experience, Leadpoint delivers cost-effective workforce solutions tailored to your needs. We handle the recruiting, hiring, training, and onboarding to deliver stable, productive, and safety-focused teams. Our commitment to safety and quality ensures peace of mind with a reliable workforce that helps you achieve your goals.
Sponsored Content
Labor that Works
With 25 years of experience, Leadpoint delivers cost-effective workforce solutions tailored to your needs. We handle the recruiting, hiring, training, and onboarding to deliver stable, productive, and safety-focused teams. Our commitment to safety and quality ensures peace of mind with a reliable workforce that helps you achieve your goals.
Sponsored Content
Labor that Works
With 25 years of experience, Leadpoint delivers cost-effective workforce solutions tailored to your needs. We handle the recruiting, hiring, training, and onboarding to deliver stable, productive, and safety-focused teams. Our commitment to safety and quality ensures peace of mind with a reliable workforce that helps you achieve your goals.
Dust control at the Fort Ord jobsite has been very important. The Monterey Air Pollution Control District wanted a water truck with each working excavator, from the demolition to the loading process. "During the majority of the job, we had seven water trucks working alongside of our excavators, and virtually no dust went airborne," says Kroeker.
The company also operates a recycling yard in its home base of Fresno, where it recycles concrete and asphalt, in addition to processing mixed C&D materials. The C&D is processed by a system that starts out with a concrete pad for the material to be dumped on and inspected, with some recoverable materials immediately hand-picked.
According to Rodney Aimsworth, general manager, a Bobcat skid steer pushes the material onto a conveyor that leads to a trommel screen, followed by a double-deck screen to further remove the fines. Then the oversized material enters a picking station where metals, OCC and trash are pulled for recycling or disposal. Wood is left on the line.
All of the leftover material falls off the end of the belt into a float tank, separating the wood from the heavies. The latter material is carted off to the company’s inert landfill, while the wood is further processed into a hog fuel by a horizontal Peterson Pacific 2400. This fuel is a mainstay of the central California recycled wood market.
Similarly, Kroeker Inc. Demolition and Environmental could be considered a mainstay of that area’s recycling and demolition industries.
The author is associate publisher of C&D Recycler and executive director of the CMRA. He can be contacted at turley@cdrecycling.org.Get curated news on YOUR industry.
Enter your email to receive our newsletters.
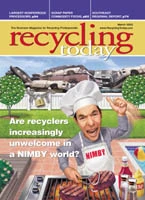
Explore the March 2003 Issue
Check out more from this issue and find your next story to read.
Latest from Recycling Today
- LumiCup offers single-use plastic alternative
- European project yields recycled-content ABS
- ICM to host colocated events in Shanghai
- Astera runs into NIMBY concerns in Colorado
- ReMA opposes European efforts seeking export restrictions for recyclables
- Fresh Perspective: Raj Bagaria
- Saica announces plans for second US site
- Update: Novelis produces first aluminum coil made fully from recycled end-of-life automotive scrap