There have been very few millionaires created from the tire recycling industry. Some entrepreneurs may enter with that hope, while many others recycle tires for altruistic reasons.
The physical process of recycling tires and producing marketable secondary commodities has proven to be a challenging one. Within a tire there is steel, polyester threads, carbon black and vulcanized rubber—intertwining materials that are hard to separate.
Persistence and creative research, however, may finally be paying off. Persistence and creativity, combined with a continuing need to simply dispose of massive piles of scrap tires, are beginning to create some established methods and sustained progress in the tire recycling industry.
But can demand actually equal (or exceed) supply in the tire recycling industry? Such situations are beginning to occur in markets where tire-derived fuel is widely used to stoke industrial boilers. Certainly, tire recyclers hope strengthened demand will be beneficial to the long-term health of their industry.
With the tire piles finally beginning to grow smaller in size and number, recyclers will be anxious to see if scrap tires and the products created from them can become commodities that can produce profit margins up and down the chain from collection to end markets.
CURRENT MARKETS
Tire-derived fuel (TDF) users remain by far the most consistent consumers of scrap tires. Certain industrial and utility customers have found that burning chips derived from scrap tires has been a cost-effective energy source.
One reason the fuel is affordable is because the supply of “raw materials” (scrap tires) is not in question right now. Abatement projects continue in several states to remove large piles of scrap tires that have accumulated in the past decade and beyond.
Only this September a removal order was issued by the California Integrated Waste Management Board (CIWMB), Sacramento, to remove a 40-acre tire pile estimated to contain seven million scrap tires.
“Our experiences with this site over the past few years have been a frustrating disappointment,” says CIWMB chairman Don Eaton. The 40-acre site is just off Interstate 5 in Stanislaus County. According to CIWMB, in some places the pile is estimated to be six stories deep with tires pancaked flat at the bottoms of ravines and swales throughout the parcel. The owners of the gigantic pile had allegedly been acquiring the tires for the purpose of recycling them.
While such piles continue to bring notoriety to the recycling industry, their total number may finally be declining.
Robert Davis is CEO of GreenMan Technologies Inc., Lynnfield, Mass., one of the nation’s largest tire recycling companies. According to Davis, the abatement of tire piles makes up an increasingly smaller portion of his company’s feedstock, while obtaining newly-generated scrap tires becomes more critical.
“We don’t base our business on abatement,” notes Davis, who adds that, “85% to 90% of our business comes from the current generation of scrap tires.” The company does still sign abatement contracts, however. “We’re working on a 1.3 million tire pile in Georgia, a three million tire pile in Iowa and another in South Dakota with just under one million tires. We sometimes have to go a little further afield to find large piles. The piles near our facilities are dwindling.”
As far as procuring newly-generated scrap tires, Davis says GreenMan “works with retailers to put collection equipment there, or we’ll pick up the tires if they don’t have room for a roll-off cage or trailer.” He says the company also works with some county and municipal governments to locate centralized drop-off points for scrap tires.
According to Davis, the company’s product is in great enough demand that the processing capacity at all three of its facilities (in Georgia, South Carolina, and Minnesota) has been expanded. “We’ve increased the number of markets we supply chips to,” he says, listing TDF (the largest), along with some civil engineering and crumbing applications. “Our problem is not so much end markets as it is supply. We have to find the tires or chips to meet the demand we’ve established. We’re in a very good position—our chips move to market continuously.”
For a tire recycler to be more concerned about the supply side rather than the demand side seems like an extraordinary development in the industry, but Davis is not alone. At Tire & Rubber Recyclers Inc., Pompano Beach, Fla., David W. Squier has found it increasingly difficult to procure tire retreaders’ buffings in a highly competitive market.
“We have seen raw buffings become scarcer and the demand for processed buffings increase,” says Squier. “The playground surfacing and rubber mat makers like process buffings, but they also really shop for price.”
He notes that the profit margins for processors like his company are narrowing. “Manufacturing is where the money is at,” he contends. “Their profit margin is much greater. We’re at a penny or two per pound while theirs might be at 10, 12 or even 20 cents per pound.”
Squier says he would not be surprised to see more processors get into the manufacturing side, although GreenMan’s Davis has done just the opposite, spinning off all of that company’s manufacturing “side ventures” that were part of the corporation when he came on board.
With consolidating processors like GreenMan acquiring more facilities and recording profits, and an increasing number of manufacturers creating a demand for rubber chips, buffings or crumb, the tire recycling market may be showing long-awaited signs of maturing.
BEYOND TDF
By volume, tire-derived fuel remains the largest end market for scrap tires. (Some recycling advocates, it should be noted, contend that incinerating the tires—even for energy use—does not necessarily constitute recycling.) There are entrepreneurs who have other ideas, however, for ways to reuse processed scrap tires.
Green Edge Enterprises LLC, St. Louis, is marketing a mulch product made from shredded and colorized scrap tires. According to Green Edge’s Lee Greenberg, the company has been researching and developing the product for five years, and was issued a patent for its colorizing process this June.
“The technical challenge was getting a colorant to bind with vulcanized rubber,” says Greenberg. “That is something that had not previously been done with results that promised any type of longevity.”
The patented process allows Green Edge to convert black shredded tire chips to the color of redwood bark mulch or other popular mulch colors.
The company had been distributing the product as both mulch and loose-fill playground cover. This year, Green Edge has also bagged the colorized chips and sold it through such retail outlets as Home Depot, Lowe’s and at plant nurseries. “It has been in retail bags since the first of the year,” says Greenberg. “We’ve been selling very well to stores here in Missouri as well as in Illinois, Texas, Arizona and other states.”
Greenberg is setting up expansion plans for Green Edge, with distributorships and manufacturing facilities in other parts of the country a possibility in the near future.
Several companies have been marketing crumbed or chipped rubber for use as athletic turf treatment, playground surfacing, floor covering, or as some other ground cover product.
In Scottsdale, Ariz., American Surface Technologies International Inc. (ASTI), has developed a product called “SafetyPlay.” The company describes SafetyPlay as “ready-mixed, pre-packaged rubber surfacing,” and compares the product’s preparation and use to ready-mix concrete “SafetyPlay’s ease of application will position the company to lead the way in the rubber surfacing industry and open the doors to a market that is predicted to become a multi-billion dollar revenue generator.”
TECHNICAL ADVANCES
Maximizing the material recovery value from scrap tires has proven to be a vexing problem, and one that researchers continue to try and tackle.
Goodyear Tire and Rubber Co., Akron, Ohio, has made a recent announcement concerning a possible breakthrough in recovering rubber polymers from scrap tires. The company is developing a solvent that can extract the rubber polymers without degrading them for re-use value.
If the process really can achieve an 80% rubber polymer recovery level, it could greatly change the way tires are recycled. Questions still remain, however, about the wide-scale applications and cost-effectiveness of the process.
Other companies have been setting up systems to recover the non-rubber portions of scrap tires. Titan Technologies, Albuquerque, N.M., has developed a process and equipment that can process 10,000 tires per day and extract from those tires three commodity streams: 250 barrels of “fuel-grade extender oil,” 13.5 metric tons of steel, and 10,450 pounds of carbon black.
Between processing improvements and heightened demand for scrap tire-derived products, tire recyclers may have an improved market outlook heading into the year 2000.
“As of right now, we’re pleased with the profitable mode that we are in,” says GreenMan’s Robert Davis. “I believe we can continue growing. We think we’ve got ourselves past a certain critical mass stage, which is why we’re now showing a profit. Our goal is to help lead the industry as it progresses,” he states.
The author is the editor of Recycling Today.
(sidebar)
DEVULCANIZATION AT LAST?
Skepticism has greeted most attempts to market a process to devulcanize the rubber found in scrap tires. However, when an announcement about devulcanization comes from Goodyear Tire and Rubber Co., Akron, Ohio, it may be carry some weight. The company has announced that it has received a patent for a devulcanization process that may produce a significant step forward for tire recycling.
“A number of devulcanization techniques have been developed over the years, but none have been commercially viable,” says Goodyear’s Larry Hunt. “This process, however, appears to offer considerably higher recovery rates than any earlier attempts and could ultimately reduce the amounts of petroleum and natural rubber needed to manufacture rubber goods.”
Hunt and co-inventor Ron Kovalak say their new process yields far more usable base products than previously attempted devulcanization methods. “Initial tests resulted in a 40% recovery rate of the raw polymer with its structures essentially preserved, and through process improvements we’ve been able to achieve an 80% recovery level,” according to a Goodyear spokesperson. Goodyear claims existing devulcanizing processes typically have no more than a 1% to 2% recovery rate.
What sets the Goodyear process apart from other tire recycling processes is a new solvent that extracts the needed polymer without degrading it, Ron Dill, director of analytical and materials testing at Goodyear, says in a Reuters report. The new process preserves the rubber’s chemical composition and molecular weight, which leaves it able to be recycled into new products.
The company has acknowledged that the process is still in the laboratory stage, and no timetable exists to bring the technology to market.
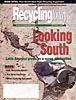
Explore the October 1999 Issue
Check out more from this issue and find your next story to read.
Latest from Recycling Today
- Indiana county awarded $65K recycling grant
- Mixed paper, OCC prices end year on downward trend
- Updated: CAA submits final draft program plan in Oregon
- Enviri names new president of Harsco Environmental business
- Survey outlines ‘monumental challenge’ of plastic packaging collection in UK
- Nippon Steel acknowledges delay in US Steel acquisition attempt
- BASF collaborates to study mechanical plastic recycling
- Commentary: navigating shipping regulations for end-of-life and damaged batteries