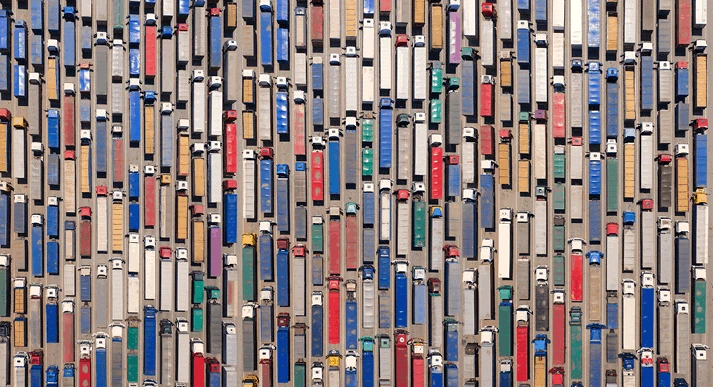

Demand is healthy for many recyclables this summer, but the No. 1 complaint from many recyclers is related to transporting those materials. Transportation has been a headache for many in the recycling industry since late last year.
With ocean shipping, containers and space on vessels have been very hard to come by this year.
“Space is tight. Even though you have a booking, at the last minute it can get rolled,” Steve Frank, president and CEO of Pioneer Recycling Services told Recycling Today in late December 2020. “It is very challenging in the Northwest. I’m hearing about this all over in our area.”
Fast-forward to May of this year, and many recyclers still faced issues securing containers and space on ships to transport materials. One recovered paper broker based on the West Coast told Recycling Today that month that ocean shipping backlogs had gotten worse as the year progressed.
“There’s very limited space on vessels, and bookings are getting more difficult to come by,” he said. “When you do have bookings, they are seemingly constantly changing.”
These freight-related complaints aren’t unique to the recycling industry; exporters globally are facing the same challenges and have been for a while.
Analysts and freight forwarders say a simple solution to these challenges is unlikely, mentioning a perfect storm of events is resulting in the challenges with ocean shipping.
Anupa Pradhan, vice president of import contracts at Plano, Texas-based Sealink International Inc., attributes some of today’s shipping challenges to the initial onset of the COVID-19 pandemic last year. Since the pandemic started, she says, freight rates jumped up regularly.
“The costs have been shooting through the roof every month,” Pradhan says. “Every month, I think, ‘This can’t go higher;’ but, the next month it goes higher. This is unprecedented. This is a situation brought about by the pandemic by the way things have been dealt with.”
Sealink International is a freight forwarder focused on handling primarily metal scrap from North America.
George Griffiths, the London-based editor of global container freight at S&P Global Platts, has been analyzing and reporting on ocean shipping and containers for the past three years. He says a combination of the onset of the pandemic, sudden pandemic-related demand restrictions being lifted, hiring shortages and subsequent COVID-19 outbreaks at ports and on shipping lines are all factors causing delays and high freight costs. Global demand for goods is not slowing down, either.
“We’re seeing this enormous pent-up demand finally coming to force at this stage,” he says. “That means we’re not able to shake off the equivalent imbalances and shortages of containers in the market. So, we’re stuck in this sort of perpetuating cycle at the moment.”
The COVID effect
At the onset of the pandemic in early 2020, demand for containers was low. China went into lockdown at the start of the year, and much of the world followed suit in subsequent months. No one was certain when demand for goods and raw materials would ramp up to prepandemic levels.
As some lockdowns started to lift in the summer of 2020, particularly in China and other parts of Asia, demand for containers increased. Around this time, Griffiths says companies around the globe started to restock their warehouses. Demand for shipping containers went from virtually nothing to prepandemic levels very quickly, though the coronavirus that causes COVID-19 was still spreading.
Pradhan says 2020 was a very strange year for ocean shipping.
“March 2020 is when we saw the first lockdowns and, to be honest, not long after that we started seeing increases in shipping demand,” she says.
She adds that freight rates began escalating then as well.
Going from low demand to high demand has shocked the ocean shipping industry. While consumer demand and spending can bounce back quickly, it takes more time for shipping lines to add containers to meet that demand.
David Lademan, the Houston-based associate editor of container markets at S&P Global Platts, says that in a normal year, shipping lines would order small batches of new containers to replace old ones and would expect the orders to come in about eight months later. Now, he says, most major shipping lines have placed very large orders for new containers, which can take months to manufacture and move to the shipping lines.
It also takes time for the ports themselves to rehire people who were furloughed or laid off because of the pandemic. With lower staffing levels, it takes longer to load and unload ships. Griffiths says before the pandemic, it would take about seven to 10 days to load and unload containers and get the goods to their final destinations. Today, that time could take closer to three to four weeks in some instances.
He says, “Suddenly there was this huge demand, and the ports struggled to rehire their staff back and bring them back in a timely manner because, obviously, that takes time. Further inland, you have other issues where there aren’t enough people out there driving the trucks and filling up warehouses. So, the market has been battered from all directions.”
Outbreaks haven’t stopped
With people receiving COVID-19 vaccinations this year, outbreaks have been reduced, and fewer places are enforcing lockdowns around the globe. But COVID-19 outbreaks still transpire and at times have affected major ports around the world.
In early 2021 before vaccines were widely available, the ports of Long Beach and Los Angeles experienced major COVID-19 outbreaks, significantly slowing operations. According to a Jan. 20 article from the Los Angeles Times, nearly 700 dockworkers at the Port of Los Angeles and the Port of Long Beach in California contracted COVID-19 that month, and hundreds of other employees were choosing to quarantine. The executive director of the Port of Los Angeles told the Los Angeles Times the port had more cargo than skilled labor, exacerbating shipping issues in the region.
“Those port capabilities really dropped significantly” with the outbreak, Griffiths says. “I think at one point there were 42 ships in a queue off the coast of California just desperate to try to get in there to offload these goods.”
More recently, the Port of Yantian in the province of Shenzhen, China, experienced a COVID-19 outbreak in May, which had a negative impact on global trade.
“That’s one of the largest exporting ports in the world, which has meant that there’s a huge delay there in an already really fractured market where there aren’t enough containers to go around,” Griffiths says. “That’s really caused rates to spike.”
Shippers in all industries are noticing extremely high freight costs. Lademan of S&P Global adds that the cost to ship goods between North America and Asia has increased by 110 to 120 percent this June compared with the same month last year. Compared with 2019, a more normal year, he says prices are about 300 percent higher.
Pradhan is seeing a similar price spike. “We are seeing freight rates of 300 to 400 percent more comparing it to 2019 on some lanes.”
She notes that the pricing situation for freight was very different a few years ago.
“It was a complete trader’s market the last few years,” Pradhan explains. “Every month, the rates would go down because shipping lines weren’t getting enough cargo. There was not enough export or import. Shipping lines were struggling. They had a slump for a very long time.”
But, she says, demand for containers is very high now, and that’s prompted rates to rise. Pradhan adds that she doesn’t expect rates or container availability to improve overnight. “What we see this summer is just the exact same thing we’re seeing in the past few months where rates are going to go higher, services will be lower, and space is going to be crazy tight,” she says.
Shipping empties
Another irritant bothering recyclers is the number of containers that steamship lines return to China or Southeast Asia empty.
“The steamship lines would rather send back empty containers for a faster turnaround, and the bookings are difficult to complete,” Michael Diehl, a senior vice president based in California for Coremet Trading Inc., which is based in New York, told Recycling Today in January.
Griffiths of S&P Global says the practice of steamship lines shipping empties is “nothing new.” He says it’s what that industry calls volume allocation to ensure flows of containerized goods from Asia to the United States or Europe.
But, he adds, what is new is that some carriers are opting to only take empty containers back rather than some loaded containers so they have a faster turnaround time in Asia to fill and reship goods.
“This makes financial sense for the carriers,” Griffiths says. “Just look at the freight rates. If you could get $17,000 [per] FEU (40-foot-equivalent unit) for a trip from Asia to Europe, you’d try as best you could to maximize as many of those trips rather than face a potential 28-day delay on $1,800 [per] FEU worth of goods. As a result, those with cargo to export from the U.S. or Europe to Asia are having some issues finding carriers willing to take their goods, but this situation is easing somewhat.”
Seeking solutions
The shipping industry hasn’t turned a blind eye to the freight challenges exporters have been experiencing this year. Griffiths says shipping lines have a few techniques they are applying to try to alleviate issues for their customers.
One way shipping lines are working to address container shortages is by ordering many more containers. As an example, Lademan says, Hapag-Lloyd has ordered about 210,000 20-foot-equivalent-unit containers this year, most of which will be delivered to the company by the third quarter of the year.
Some shipping lines also are adjusting their schedules to try to alleviate issues. For example, Griffiths says a shipping line might typically sail Monday, Wednesday and Friday. But to ensure ships are totally full, a shipping line might reduce its sailings to just Monday and Friday.
Although shipping lines are making changes, Pradhan suspects it could take the rest of this year or more before ocean shipping challenges noticeably improve.
“We’re going to come through this with some fundamental changes in the supply chain,” she says. “Things are going to change. People are going to have to get more technologically savvy—all of the shipping lines are going that way. But I think the world still needs more time before it gets out of this. It’s not done yet.”
With ocean shipping challenges here to stay at least for the near-term future, Pradhan says recyclers should be diligent about having their bookings in place.
“Know that you are definitely going to face a space constraint,” she says. “The successful recyclers plan their bookings properly. Forget about the just-in-time approach or stocking up. These recyclers have been pushing bookings out for a month or prebooking, making sure they have a dealer in hand to ship because space is of the utmost importance.”
Pradhan continues, “Shipping lines don’t take no-shows lightly. Have your bookings in place a month ahead of planning,” she advises.
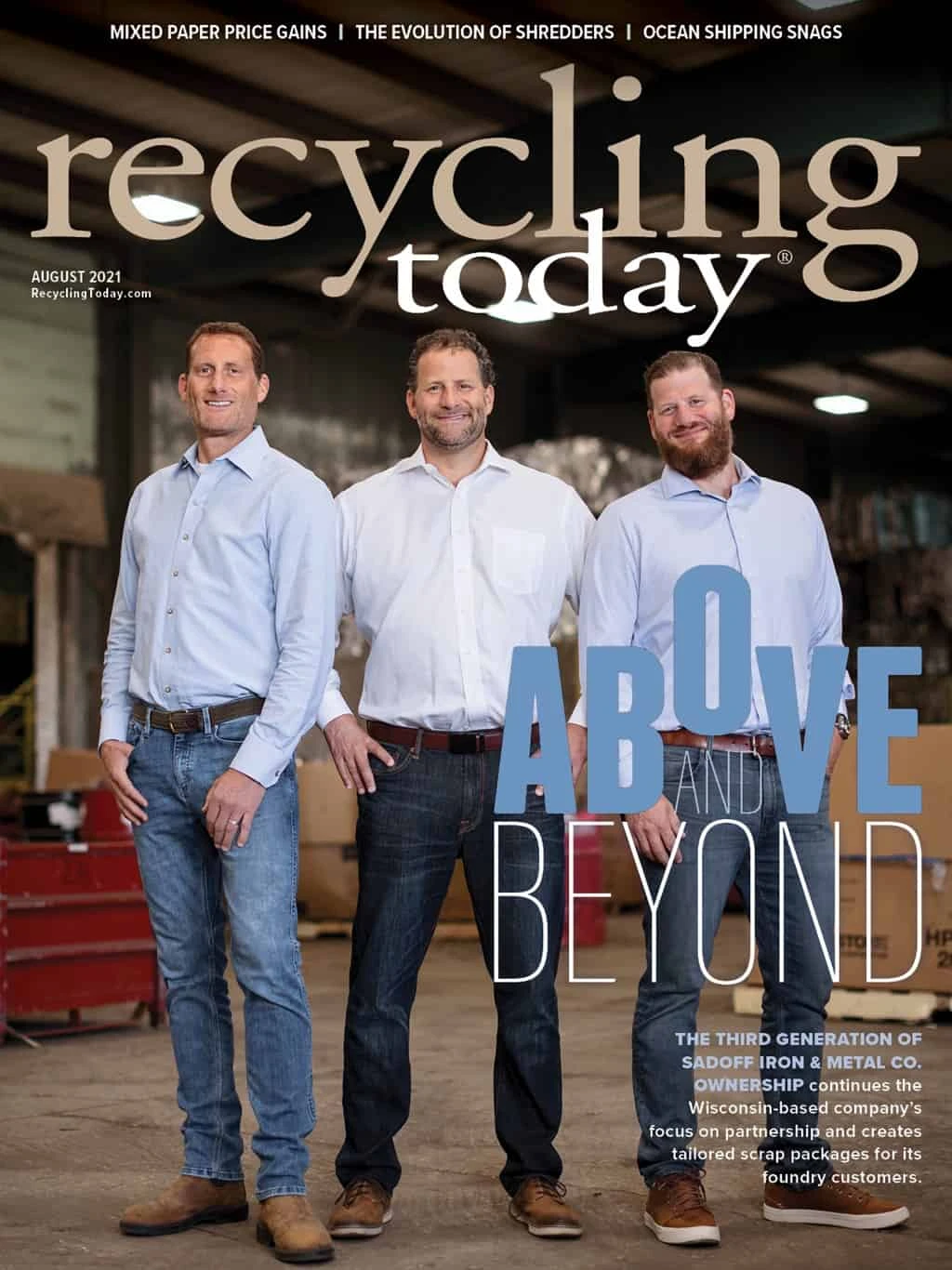
Explore the August 2021 Issue
Check out more from this issue and find your next story to read.
Latest from Recycling Today
- Nucor receives West Virginia funding assist
- Ferrous market ends 2024 in familiar rut
- Aqua Metals secures $1.5M loan, reports operational strides
- AF&PA urges veto of NY bill
- Aluminum Association includes recycling among 2025 policy priorities
- AISI applauds waterways spending bill
- Lux Research questions hydrogen’s transportation role
- Sonoco selling thermoformed, flexible packaging business to Toppan for $1.8B