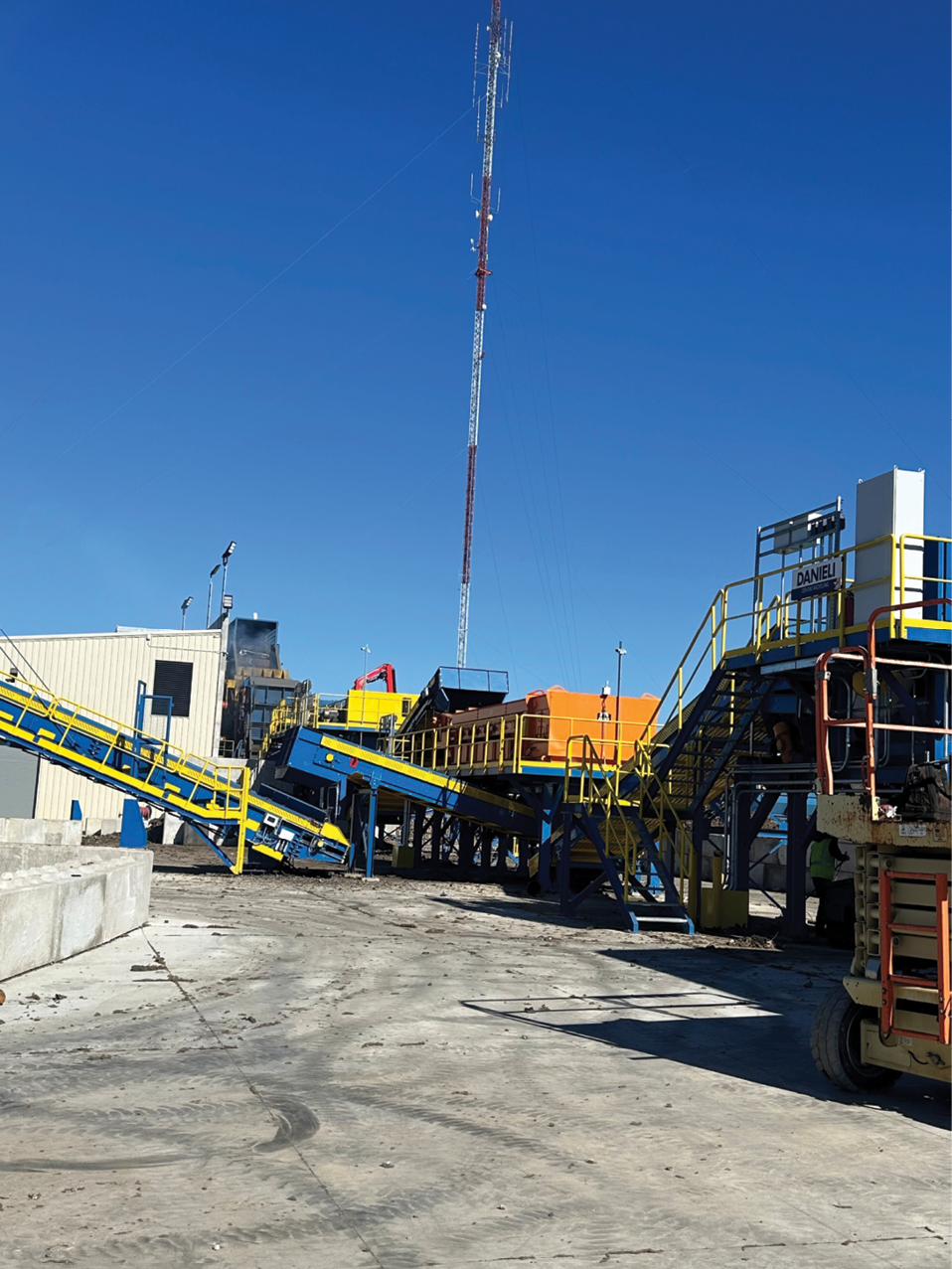
The last two years have been a bit of a whirlwind for Neil Morris, co-owner of NuCycle LLC, which operates an auto salvage yard and full-service scrapyard in Rock Hill, South Carolina.
Morris recently achieved a long-term goal with the installation of an automobile shredder and the addition of ferrous and nonferrous downstream processing systems to maximize the value of recyclables entering the facility.
“I’ll tell you what, it’s different,” Morris says of the addition of the Danieli Centro Recycling DCR Series shredder. “With that in the yard, we basically have gone from Single-A ball to the major leagues. … When you run a shredder, it never stops. Right now, it’s a full-time job.”
Morris has spent a lifetime in the recycling industry and is the third-generation owner of Morris Scrap Metal Co. Inc., a full-service scrapyard in Kings Mountain, North Carolina, that primarily works with industrial accounts and does some retail trade. NuCycle is his venture with business partner Charles Saleh.
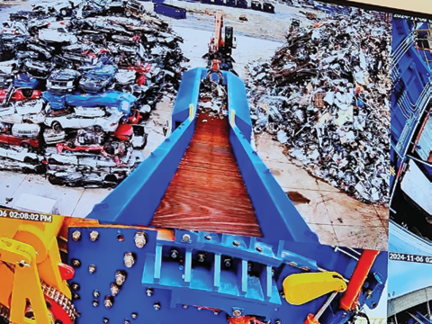
NuCycle accepts metals such as steel, copper, aluminum, brass, tin and more, as well as items such as appliances, industrial equipment, batteries, radiators and catalytic converters.
The company provides gondola trailers, flat beds and containers ranging in size from 20-60 yards to help its customers manage recyclables.
NuCycle’s auto salvage yard has more than 1,200 different vehicles in stock for parts harvesting, including all types of cars, trucks, vans, SUVs, lawn and other equipment.
Despite Morris’ vast experience in scrapyard operations, the addition of new equipment in Rock Hill admittedly has been an adjustment as NuCycle continues to test its ferrous and nonferrous systems and gradually ramp up the processing capability of its 4,000-horsepower shredder with its 80-inch-by-108-inch box, designed by Italian equipment company Danieli.
“We’ve got to hire some more people, and it’s been a learning curve for all of us,” Morris says. “We’ve [had to learn more about] bookkeeping, payment terms for different customers—things like that. But down the road, I’m sure it’ll smooth out.”
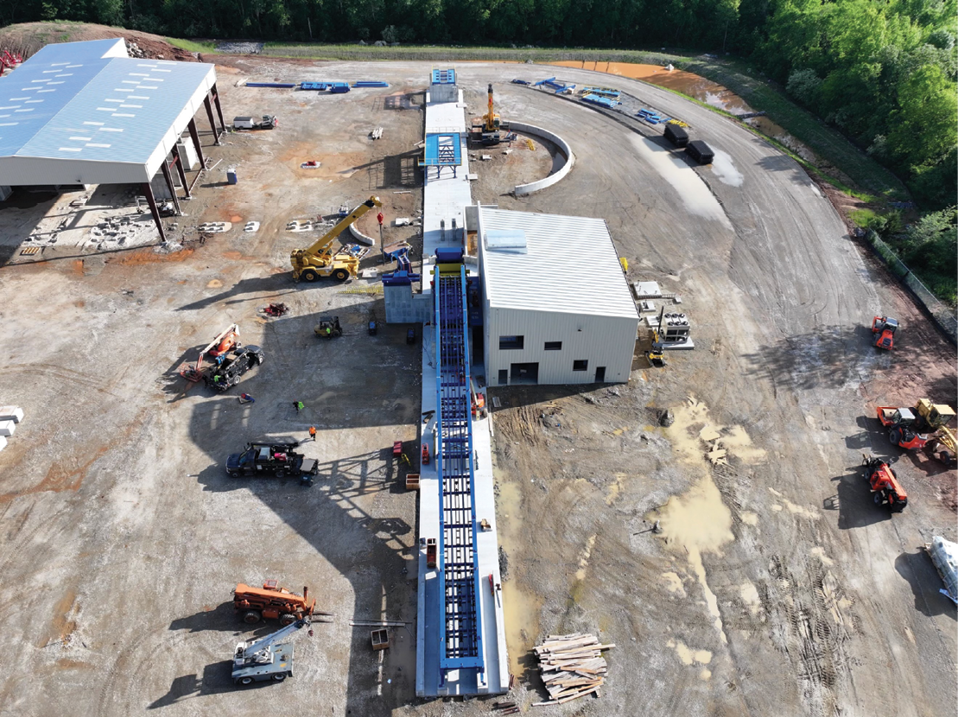
Thorough prep
Before purchasing the new equipment, Morris and Saleh traveled across North America to do homework. In 2022, Morris started contacting shredder manufacturers and scheduling trips to view installations.
“[Saleh] probably went to about 10 installations across the [U.S.], and I probably went to 15,” Morris says. “We’d just get on an airplane, take off and spend a couple days at a yard.”
The business partners met with operators in Arkansas, Ohio, Wisconsin, Texas, Georgia and Florida, among other U.S. locations, and even toured several installations in Canada. At each stop, they’d take copious notes outlining what they liked about each piece of equipment and the flow of each scrapyard in hopes of incorporating those positives into their Rock Hill facility.
“Out of the 15 installations I went to, no two were the same,” Morris says. “We’d go out and ask questions, look at setups and logistics and how trucks are handled and how yards handled nonferrous coming in, [for example].”
Morris and Saleh began purchasing equipment in early 2023, and pieces began arriving in the spring. Before their installation, NuCycle hired a process engineer to help adjust the yard’s layout to accommodate the new machines.
“[The process engineer] made sure everything was streamlined, so you’re not crossing paths with trucks, for example, and everything runs on its own,” Morris says. “He took everything we liked about the installations we saw, laid it out and got drawings made that outlined the way material would flow in, how different trucks were going to come in and get loaded without getting in the way of everything else.
“We told him about our equipment, and then he basically set everything up so inbound trucks are not getting crossed up with outbound material trucks and things like that. If you’re loading zorba, for example, your zorba loading’s not interfering with your scrap loading. … Once he got to know the flow [of the scrapyard], he could streamline anything.”
Fourteen acres of the 35-acre site were designated for the new equipment. Before it could be assembled, NuCycle had to bring in new dirt and pour more than 12,000 yards of concrete to cover the 6-acre surface the shredder and nonferrous system would sit on.
Once the surface had been prepared, Chicago-based Sargent’s Equipment & Repair Service Inc. began the installation in December 2023, which took approximately five months to complete, and the equipment began operating during the summer of 2024.
Ultimately, Morris says he chose the Danieli shredder because it was designed specifically for the American market. It features an inverted drive system that contributes to lower power consumption and less downtime if an issue arises.
“It’s more heavy-duty,” Morris says. “We had the opportunity to go see one on the ground, and when we looked at it, it was like, ‘Wow, that’s a beefy shredder.’ … The inverted drive system was a big benefit for us. And Danieli is a huge company. I figured if steel mills can trust them, then a scrap guy can trust them. A lot of steel mills around here have Danieli equipment in them. We like their product.”
To keep a watchful eye on the shredder, NuCycle also added a control room to its facility, equipped with a wall of TVs that enable a full view of the system. The shredder itself has been outfitted with thermal and infrared cameras throughout so employees can scan for issues if they develop.
Currently, NuCycle feeds the shredder with four material handlers, processing approximately 70 tons per hour of mainly vehicles and light iron. At full capacity, NuCycle will be able to shred about 100 tons per hour.
Since the installation, NuCycle has hired a shredder manager and is looking to expand its 15-person team to 20. Morris says the shredder has run for up to nine hours per day as the company runs tests and irons out startup issues.
The addition of the shredder has allowed NuCycle to tread new ground in terms of outgoing products. Morris says he is shredding plate for one company in the region and hopes to begin developing other specialty grades for foundries, among others, in the future.
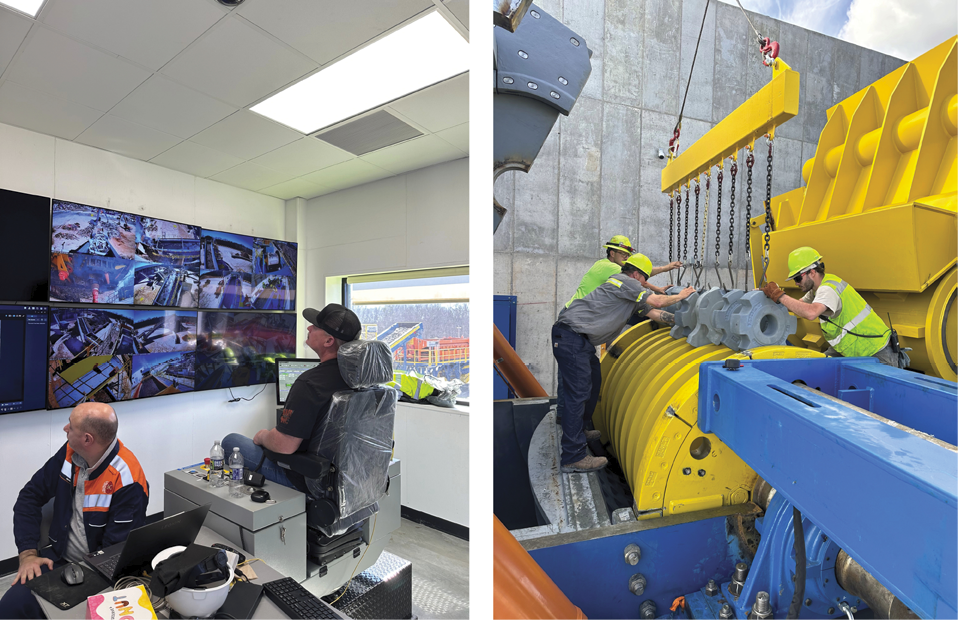
Adding ferrous processing
During his travels to different shredder installations, Morris also took stock of ferrous downstream equipment. In particular, he noticed several yards used the Shred-1 ballistic separator manufactured by Pennsylvania-based Eriez.
“Most of the yards we went to did not have [the Shred-1 ballistic separator],” Morris says. “In the yards that didn’t have one, I’d heard that in the next five to 10 years, if you’re not making low-copper shred, you’re out of the market.”
NuCycle went with several equipment manufacturers to complete its ferrous downstream system. After material is shredded, it heads to an Eriez poker sorter, then to a pair of Eriez P-Rex permanent drum magnets. Ferrous material then heads to the Shred-1 ballistic separator, which removes materials such as meatballs and copper-bearing scrap. After the ballistic, material heads to a polishing magnet designed by German equipment company Steinert GmbH before reaching the picking line.
“I went to a lot of places that had a ballistic separator, and the picking guys were picking as much trash as they were valuables out of the picking line,” Morris says. “That’s one reason we added the polishing magnet, to keep pickers picking valuable items versus picking trash. … If there’s a little bit of fluff left in the system, it’s separated before it gets to the picking line. About 90 percent of what’s being picked is valuable [as a result].”
The nonferrous side
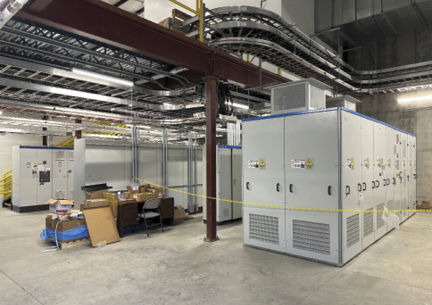
Morris calls his nonferrous downstream system “the moneymaking side” of the shredder operation.
NuCycle’s system is designed to process as much as 32 tons of material per hour but is still in the ramp-up phase as the company continues to batch feed it on a part-time basis.
To process nonferrous, NuCycle purchased a screening system developed by Germany-based Spaleck. The system produces four cuts: a ½-inch-and-under cut for ultrafine material, a 1 ½-inch-and-under cut for midsize fractions and a 4-inch-and-under cut for large fractions, while oversize material heads out the end of the system.
“We also put picking stations in our nonferrous area,” Morris says. “I’ve got a picking station near the oversize [material] and a picking station near the mid- and large-size fractions to pick any large copper or brass that’s coming down the line.”
After the Spaleck equipment makes its cuts, material heads to three Steinert eddy currents, then to a Steinert induction sorting system that uses air jets to eject any remaining metal in the stream.
Morris is excited about the nonferrous system because of its potential to increase NuCycle’s revenue. “The ferrous pays the bills, and you make money on the nonferrous side.”
Explore the March 2025 Issue
Check out more from this issue and find your next story to read.
Latest from Recycling Today
- ReMA opposes European efforts seeking export restrictions for recyclables
- Fresh Perspective: Raj Bagaria
- Saica announces plans for second US site
- Update: Novelis produces first aluminum coil made fully from recycled end-of-life automotive scrap
- Aimplas doubles online course offerings
- Radius to be acquired by Toyota subsidiary
- Algoma EAF to start in April
- Erema sees strong demand for high-volume PET systems