
Plastic bags tend to get a bad reputation in the United States. Many material recovery facilities (MRFs) across North America view them as contamination because they get tangled in sorting equipment. For more than a decade, some city and county governments in the U.S. have proposed and implemented taxes on plastic bags or banned them in an effort to reduce plastic litter and consumption.
Yet, Novolex, Hartsville, South Carolina, sees opportunity to close the loop on plastic bags. The company started its Bag-2-Bag recycling program in 2006 to reduce the amount of litter caused by plastic bags and to turn those old bags into new bags at its Novolex Hilex Poly recycling center in North Vernon, Indiana, or its recycling facility in Shawano, Wisconsin. The company also has about a half dozen other recycling partners to help. Phil Rozenski, senior director of sustainability and corporate affairs at Novolex, says the program offers a sustainable solution to the country’s plastic bag concerns.
Through Bag-2-Bag, Novolex connects with grocery stores and other retailers. Collected bags are gathered into bales that are transported to one of Novolex’s recycling facilities in North Vernon or Shawano. The recycling center then processes the used bags into recycled pellets. The pellets are used to manufacture new plastic bags.
“As a company, we consume more than 100 million pounds of recycled polyethylene film in a year,” Rozenski says. “We’ve gotten good with recycled content, and we’ve helped to mentor other companies to help us meet the demand for recycled content. We hope we can set the example, and more companies will do the same thing—that’s really who we are.”
Recycling process
Novolex contracts with a few regional and national retail chains in the U.S. and Canada. These retailers will collect and bale plastic bags and plastic packaging film from consumers and their warehouses. A retailer informs Novolex when it has a trailer full of plastic bag and film bales, and Novolex hires a firm to haul the trailer to one of its facilities or recycling facility partners.

“We determine where to send it depending on our workload,” Rozenski says. “We work with about a half dozen [third-party recycling partners]. Some partners are on the West Coast, some are in the central U.S., some are in the South. Part of sustainability is reducing how much you move stuff, so we feel it’s key to own two facilities and have partners.”
Once Novolex receives the bales, Rozenski says the company or its partners load them into a bale breaker. “We have a guillotine that shaves off layers and opens up the bale. Then, we do a visual inspection to see if anything doesn’t belong. It then gets shredded.”
One common contaminant is grocery store receipts. To remove the receipts, Novolex places the shredded polyethylene (PE) into a tank. The PE floats, while the receipts and any other contaminants sink.
“The magic of polyethylene floating is all it takes,” Rozenski says.
From there, Novolex performs an extrusion process and turns the PE film into pellets. Finally, those pellets are used as feedstock for plastic bag products. The company’s plastic bags typically use about 25 to 40 percent recycled content.
“We use a mix of content in the bags,” Rozenski adds. “Typically, we have 30 percent recycled content. Some are higher, some are lower. We could do 100 percent, but there’s not enough supply. We’re looking at how to grow our recycled content and are constantly looking for new partners to meet that demand.”
Reaching retailers
To ensure contamination remains low in bales, Novolex regularly communicates with its retail chain partners. Rozenski says the company works with partners to educate them and their employees on what is considered contamination.

Through the Bag-2-Bag program, Novolex can accept plastic retail bags, produce bags, newspaper bags, dry cleaning bags, cereal box liners, paper towel film wrap, toilet paper film wrap, wrap on cases of soda and canned vegetables, sealed air pouches in mailed packages and Ziploc or other zipper-style bags (provided the zippers are removed prior to recycling).
The program does not accept salad bags, frozen vegetable bags, pet food bags, polyvinyl chloride, polystyrene, polyurethane foam, polypropylene, polyethylene terephthalate trays, plastic bottles, metals or potentially hazardous materials, such as medical waste.
Rozenski says the quality of bales Novolex receives is typically good; however, some level of contamination is usually present. If the company notices a trend, it works to educate the retail location.
“Every now and then, someone in the back end of a retail store’s distribution center will see plastic material, like nylon strapping, and they add it,” he says. “We mark these bales. If we find something, we work with that retailer to educate employees not to put that in there, and it changes.”
“Everyone in the value chain has to work together. That’s the key to being more sustainable.” – Phil Rozenski, senior director of sustainability and corporate affairs, Novolex
To maintain good partnerships with the regional and national retail chains, Rozenski adds that it’s important to connect with four types of people: procurement personnel who buy the bags, operations personnel who collect the bags, marketing personnel and sustainability personnel.
One of the biggest challenges in the program is educating retailers that plastic bags don’t have to be just one color. Recycled plastic bags aren’t usually the vibrant colors some retailers are used to; they are usually gray or brown as a result of mixing plastic film together.
“It’s a different color,” Rozenski says. “It’s easiest to make a tan or gray bag. Once the retailer understands that gray or brown bags communicate sustainability, they get it.
“Partnering with your customers is key,” he continues. “Everyone in the value chain has to work together. That’s the key to being more sustainable. Get everyone involved together, and you can solve more complex problems.”
Get curated news on YOUR industry.
Enter your email to receive our newsletters.
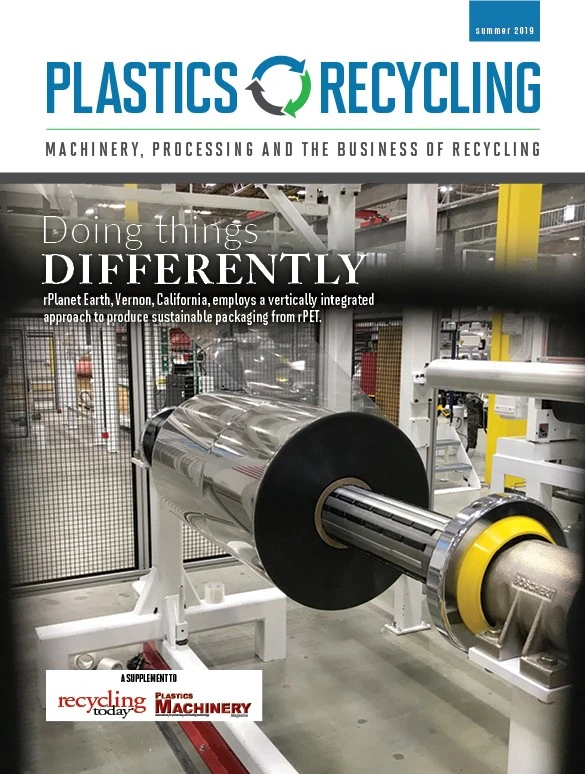
Explore the June 2019 Plastics Recycling Issue
Check out more from this issue and find your next story to read.
Latest from Recycling Today
- GFL opens new MRF in Edmonton, Alberta
- MTM Critical Metals secures supply agreement with Dynamic Lifecycle Innovations
- McClung-Logan Equipment Company joins Tana’s authorized dealer network
- Grede to close Alabama foundry
- Plastics Recycling Conference 2025: Working toward their targets
- SWACO rolls out new commercial recycling and food waste programming
- Updated: Matalco to close Canton, Ohio, plant
- Metso launches electric Anode Weighing and Casting Machine