
It’s been seven years since Northeast Metal Traders (NEMT) invested in wire chopping equipment at its Philadelphia yard. Competition has become fiercer in recent years as additional wire chopping lines have been installed in North America. (For details on North America’s wire chopping lines, see Recycling Today’s 2019 Wire Chopping list at www.RecyclingToday.com/article/2019-wire-chopping-line-list.)
“The wire chopping sector in the U.S. is currently plagued by massive overcapacity,” says NEMT CEO Mitchell Goldberg. “Chinese restrictions put in place in the past few years coupled with the popularity of smaller wire lines has allowed or caused many dealers to become processors of their wire rather than sellers to larger choppers or export markets.”

However, Goldberg says a number of attributes set NEMT apart from other operators.
“Northeast’s well-known reputation for honest grading and recoveries is a giant plus,” he says. “Additionally, we make high-quality, lab-verified chops, which allows us to make premium sales and consistently move our inventory.
He adds, “This in turn allows us to pay very competitive prices as compared to the new prices paid by a number of our competitors.”
While competition for wire products in the Northeast is “fierce,” Goldberg says NEMT has been able to purchase enough material to keep the line in full production. The scrap wholesaler and processor buys this material primarily from other scrap yards and industrial generators throughout eastern North America. “The main thrust of Northeast is nonferrous wholesale and brokerage,” he says. “The wire line has opened up new opportunities with our existing customers and brought new customers into our yards.”
Get chopping
The company decided to venture into wire chopping after reviewing its annual wire sales. Before the installation of the wire chopping line, NEMT stripped much of the wire and cable it was handling before selling it to domestic or overseas buyers.

NEMT’s system features an E2500C supplied by Eldan Recycling, which is based in Denmark with U.S. offices in Sanborn, New York.
Following the installations, “We were able to quickly achieve and then exceed our production goals,” Goldberg says. Shortly after the installation, NEMT was producing 6,600 pounds of chops per hour.
NEMT subsequently installed an electrostatic separator to further purify its outbound chops.
Today, the line has three cutting stages, multiple magnets and several air/gravity tables to perform final separation.
Buy quality, produce quality
NEMT says part of the reason for its high-quality output is because its suppliers provide material that lends itself to efficient processing and because the company itself has reliable preprocessing sortation techniques.
“We are fortunate to do business with a network of customers who are knowledgeable about sorting and packaging insulated wire and who care about quality,” Jeff Fisher of NEMT says.
“We currently process No. 1, insulated No. 2 copper, insulated aluminum wire and ACSR (aluminum conductor steel reinforced) and have the capability to process other products based on market conditions and material flow,” Goldberg says.
The company is producing No. 1 and No. 2 copper chops and electrical conductor, or EC, chops and straws.
“We utilize our in-house lab to certify the chemistry of the copper products we produce,” Goldberg says. “This allows NEMT to target our end users based on meeting and exceeding their required chemistry.”
Get curated news on YOUR industry.
Enter your email to receive our newsletters.
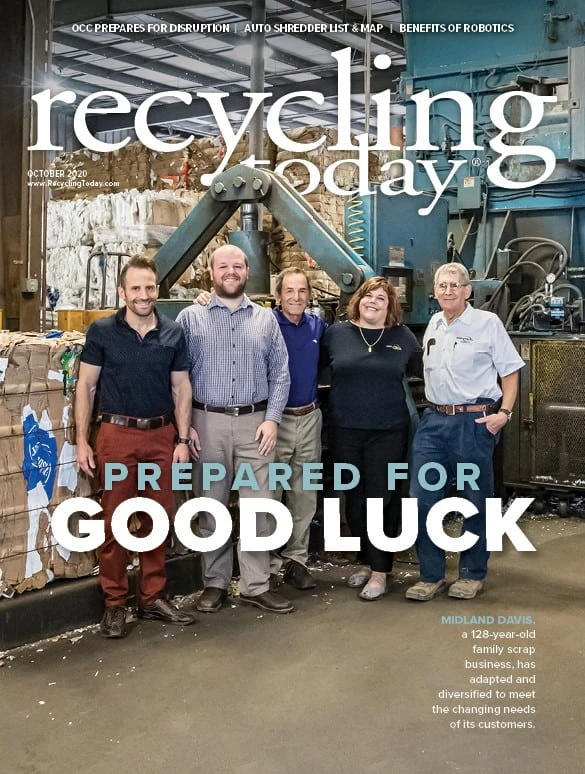
Explore the October 2020 Issue
Check out more from this issue and find your next story to read.
Latest from Recycling Today
- Construction, auto sectors show mixed signals
- Politics in Turkey threaten recycled steel outlet
- Toppoint Holdings expands chassis fleet
- Lego creates miniature tire recycling market
- Lux Research webinar examines chemical recycling timetables
- Plastics producer tracks pulse of wire recycling market
- Republic Services, Blue Polymers open Indianapolis recycling complex
- Altilium produces EV battery cells using recycled materials