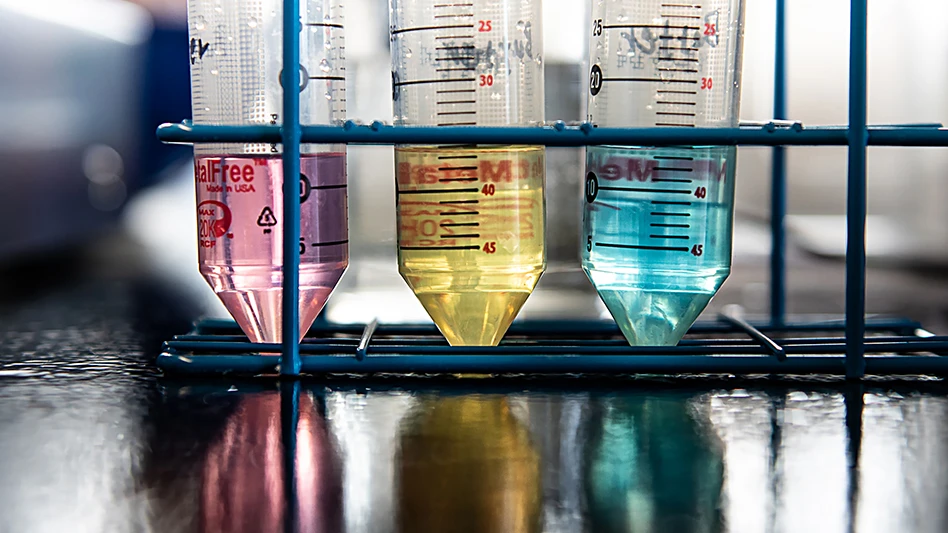
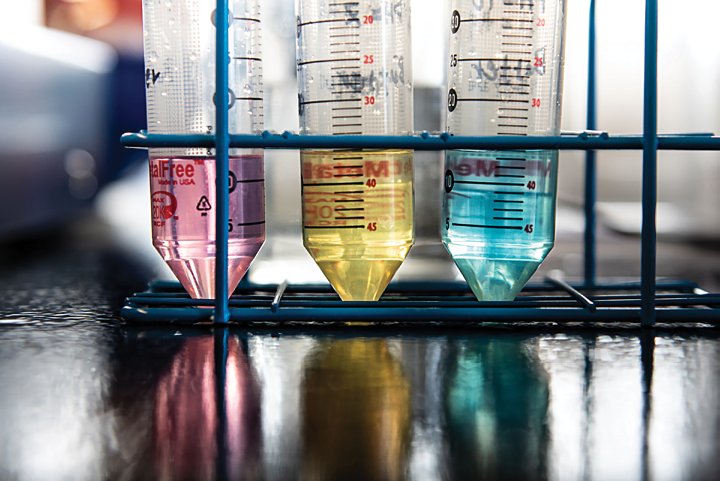
Amid a flourishing lithium-ion battery market, more than $2.8 billion in funding through the Bipartisan Infrastructure Law (BIL) are anticipated to boost battery component manufacturing, processing and recycling in the United States. In May 2022, President Joe Biden’s administration pledged to strengthen those sectors with the announcement of Battery Materials Processing and Battery Manufacturing and Electric Drive Vehicle Battery Recycling and Second Life Applications funding opportunities.
According to a news release from the Department of Energy (DOE) detailing the announcement, the programs were established to encourage sustainable domestic sourcing of materials used to make lithium-ion batteries (LIBs), including lithium, cobalt, nickel and graphite. and to expand domestic manufacturing of batteries for electric vehicles (EVs) and the electrical grid.
For the Battery Materials Processing and Battery Manufacturing provision, 20 companies were selected in October 2022 for negotiation of awards to receive a combined $2.8 billion. The money primarily will go toward facilities that extract and process lithium and other battery materials. The funding aims to support the development of enough battery-grade lithium to annually supply around 2 million EVs, enough graphite to supply approximately 1.2 million EVs and enough nickel to supply roughly 400,000 EVs.
Last November, the DOE announced 10 companies that were selected for negotiation of awards from the Electric Drive Vehicle Battery Recycling and Second Life Applications provision, which is being funded with $73.9 million from the BIL. This provision specifically targets research and development to promote LIB recycling and second-life demonstration projects.
David Howell, acting director and principal deputy director of the DOE’s Office of Manufacturing and Energy Supply Chains, says the provision will boost the country’s ability to recover critical minerals in a more profitable and environmentally friendly way by reducing emissions and energy and water use.
“What we’re trying to do with these research, development and demonstration projects is make it profitable to collect spent batteries and get [them] to this next level, whether that’s a second use or to a recycling center,” Howell says.
Although the battery recycling market in the U.S. is growing, Howell says batteries from consumer electronics have only a 5 percent recycling rate.
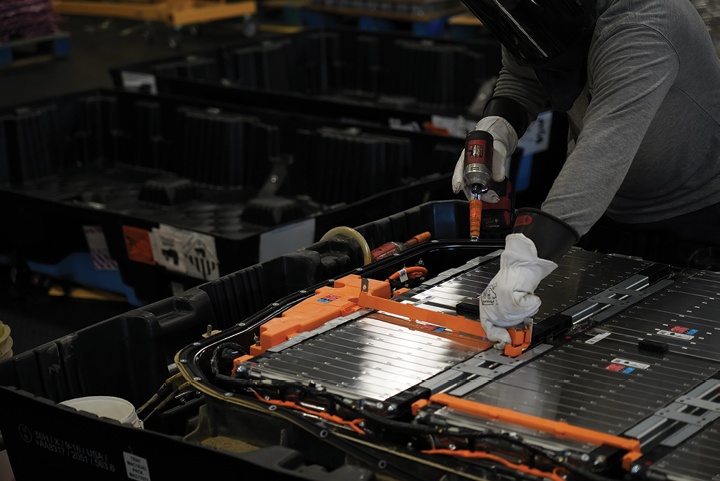
“In order to actually have a robust battery supply chain, we’re going to have to change that,” Howell says. “Our goal at the Department of Energy is to recover 90 percent of spent lithium-ion batteries, and that includes consumer electronics, electric vehicle batteries and stationary batteries, as well, and then, once they’re recovered, to develop the processes that would allow us to recover 90 percent of the minerals in those batteries.”
Research and development efforts also will advance the workforce in local communities by generating manufacturing and processing jobs at recycling centers.
With the growing prevalence of LIBs, Howell says the DOE is determined to reinforce businesses that provide opportunities to safely dispose of batteries.
Various criteria were considered when selecting companies. Howell says applicants were chosen based on technical merit, expected impact on recycling technology and community benefits.
Reno, Nevada-based American Battery Technology Co. (ABTC) was selected to receive awards through both funding opportunities. The first, worth $57 million, will support the company’s plan to build a commercial-scale refinery to make battery-grade lithium hydroxide.
CEO Ryan Melsert says the currently deployed design and data will be implemented into ABTC’s field demonstration plant, funded in part by the DOE, then eventually into its new refinery in Tonopah, Nevada. ABTC and its partners will provide another $57 million to fund the five-year project.
A $10 million award will assist ABTC and its partners in developing three advanced battery recycling techniques that are in the research and development stage. Melsert says the funding will allow ABTC to take its new technologies through bench-scale development in the project’s first year, to pilot-scale validation in the second year and, finally, to the building of commercial versions to integrate into its Global Development Center in Fernley, Nevada—and possibly into its new recycling facility in McCarran, Nevada—in the third year. This process and preparations for the new refinery are expected to kick off immediately following the execution of final agreements with the DOE.
Melsert says ABTC is prepared to contribute to a closed-loop system by extracting lithium deposits at its Tonopah Flats Lithium Project, bringing them into the supply chain. ABTC says the project encompasses one of the largest known inferred lithium claystone resource deposits in the U.S., located in Big Smoky Valley near Tonopah, and has 517 unpatented lode mining claims covering about 10,340 acres of land administered by the Bureau of Land Management.
“Because the industry is growing so quickly, we also need primary materials to do that first fill of the loop, and [then] eventually [be] supplied through recycling,” Melsert says. “Our primary lithium work is about developing a low-cost, low-environmental impact domestic resource to help provide these materials to domestic industry.”
Instead of using what Melsert calls “brute force” methods of recycling that place batteries in high-temperature furnaces or into a grinder, ABTC relies on an automated deconstruction process combined with a hydrometallurgical process to deconstruct packs, modules and cells in a more organized way, Melsert says.
Though battery cell plants are being built at a considerable rate in the U.S., Melsert says these multibillion-dollar factories are almost 100 percent reliant on feedstock sourced from outside the U.S. He points to security, cost and environmental impact as three supply challenges inhibiting the industry.
In terms of acquiring feedstock outside the U.S., a supply chain disruption would put factories in jeopardy. Melsert says the expenses associated with buying materials abroad, including export and import tariffs, reduce the competitiveness of U.S. facilities. Lastly, the countries where the desired metals are produced could have less-strict environmental regulations, and the process of shipping across continents has a significant environmental impact.
Cirba Solutions, based in Charlotte, North Carolina, has been selected for negotiation of a $75 million award and an additional $7 million. The $75 million project will expand its existing LIB recycling facility in Lancaster, Ohio, while the $7 million in funding will enhance the site’s hydrometallurgical process to recover battery-grade salts for cathode manufacturing.
Cirba Solutions Vice President of Marketing and Digital Engagement Danielle Spalding says the company plans for the 150,000-square-foot Lancaster facility to have the capacity to provide enough cathode production for more than 200,000 EVs annually. The expansion likely will take three years, starting in the third quarter of 2023 or sooner. It is expected to create around 150 jobs in the Columbus, Ohio, area, and Cirba will add permanent jobs as each phase proceeds.
Cirba Solutions includes Heritage Battery Recycling, Retriev Technologies and Battery Solutions and has more than 30 years of experience in the battery recycling industry. Spalding says this gives the company a depth of knowledge handling different types of batteries, whether lead-acid, nickel metal hydride or lithium-ion.

Spalding says Cirba Solutions aims to invest more than $1 billion during the next decade, and a crucial part of this goal to increase the availability of critical minerals in the domestic supply chain is to help grow regional resources.
“We do truly believe as we enhance these regional processes for hydrometallurgical processing to produce battery-grade salt, they support the larger national approach of ensuring that we’re securing that,” she says. “But then we’re also encouraging and attracting additional manufacturing locally.”
Nth Cycle, a Beverly, Massachusetts-based battery recycler, announced it is working with Cirba Solutions and is planning a $2.15 million project to advance its commercial operations of its electro-extraction technology.
Co-founder and CEO Megan O’Connor says Nth Cycle’s Oyster electro-extraction unit offers a modular solution to chemical refining, adding that requiring critical materials and end-of-life electronics to be transported to a single facility for processing is not economical. As an alternative, the Oyster can be installed in various locations, from recycling facilities to mining sites, to process material where it is generated.
Another distinct feature of the Oyster is its versatility in refining a wide range of metals, including mixed nonferrous metals; copper-bearing material; nickel; precious metals such as silver, gold, palladium and platinum; stainless; high-temp and specialty metals; tin; and zinc.
O’Connor says if the desired amount of nickel, for example, cannot be acquired by recycling electronics alone, Oyster can pull nickel out of other industrial scrap sources, such as spent catalysts used in the oil and gas industry or slag from the steel industry.
“We specifically designed our system to handle this wide funnel of materials all the way from lithium-ion batteries to the slag, which I would say are polar opposite of each other in terms of the two ends of the spectrum of what we can process, so that we can pull as much nickel back into the supply chain as possible,” O’Connor says.
By the end of this year, Nth Cycle will be producing nickel mixed hydroxide product (MHP) from its electro-extraction process, O’Connor says, and grant funding will help accelerate construction of a facility for MHP production that is likely to be operational in the third quarter, though an exact location has not yet been determined.
These projects, among others, indicate a bold effort to focus on battery manufacturing and recycling in the U.S. The BIL funding marks a bold step for innovation as LIB demand grows.
Get curated news on YOUR industry.
Enter your email to receive our newsletters.
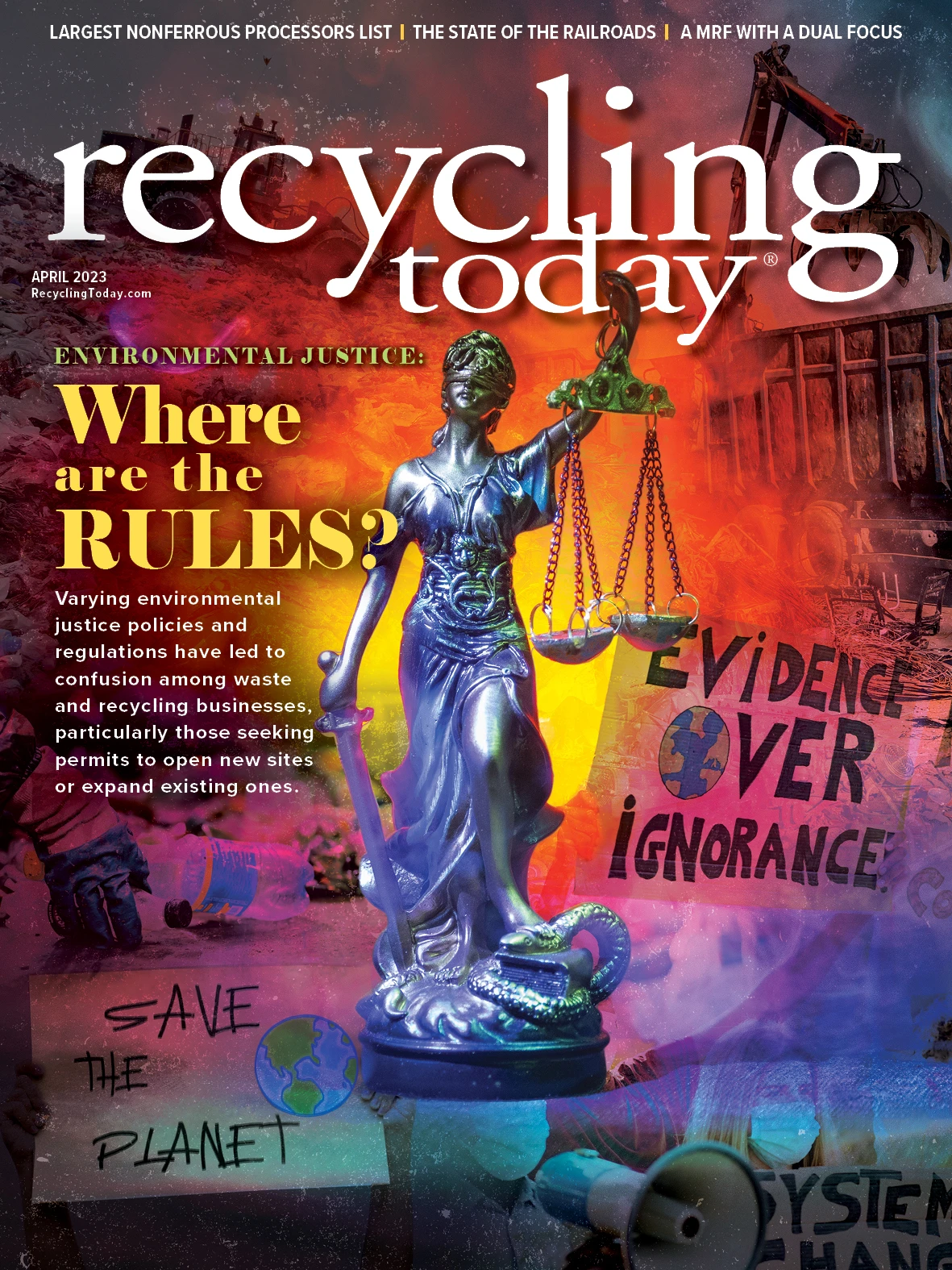
Explore the April 2023 Issue
Check out more from this issue and find your next story to read.
Latest from Recycling Today
- ReMA opposes European efforts seeking export restrictions for recyclables
- Fresh Perspective: Raj Bagaria
- Saica announces plans for second US site
- Update: Novelis produces first aluminum coil made fully from recycled end-of-life automotive scrap
- Aimplas doubles online course offerings
- Radius to be acquired by Toyota subsidiary
- Algoma EAF to start in April
- Erema sees strong demand for high-volume PET systems