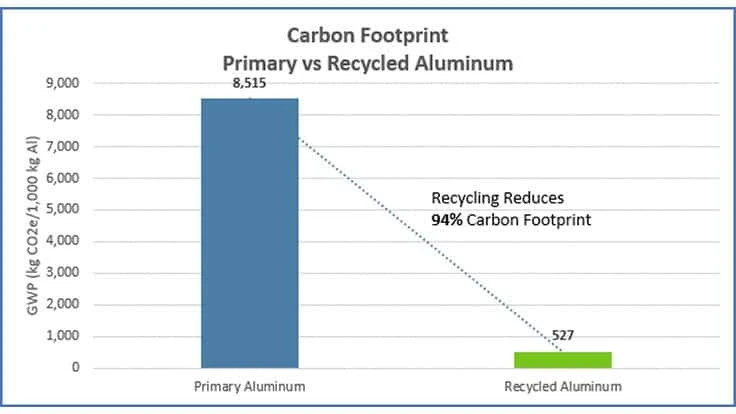
Image courtesy of the Aluminum Association
According to a new, third-party critical-reviewed life cycle assessment (LCA) report, the energy and carbon impact of aluminum production in North America has dropped to its lowest point in history. Since 1991, the carbon footprint of primary aluminum production declined by 49 percent, while recycled aluminum production’s carbon footprint declined by 60 percent. The energy needed to produce primary and recycled (or secondary) aluminum has been reduced by 27 percent and 49 percent, respectively, as well during the same time frame.
Between 2010 and 2016 alone, the carbon footprint of aluminum production (primary and secondary) declined between 5 percent and 21 percent. According to the report, “Environmental Footprint of Semi-Fabricated Aluminum Products in North America,” aluminum produced in North America, which relies heavily on renewable hydropower, is among the cleanest in the world.
The report was developed by the Aluminum Association in cooperation with Chicago-based sustainability consultancy Sphera. It quantifies material, energy use and environmental release impacts over the entire aluminum product life cycle, from raw material acquisition to end-of-life recycling and/or disposal. The study considers cradle-to-gate and cradle-to-grave life cycle stages and is based on aluminum and aluminum products manufactured in North America in 2016.
“The U.S. aluminum industry continues to innovate and find ways to produce this essential metal in as environmentally sustainable way as possible,” says Charles Johnson, president and CEO of the Aluminum Association, Arlington, Virginia. “And we’re nowhere close to done—every day, our members pursue new approaches to make this lightweight, durable and infinitely recyclable material using less energy and with lower emissions.”
According to the LCA report, primary and recycled aluminum production represents the largest element of the industry’s environmental impact for product manufacturing and has improved most substantially in recent years. The impact of semifabricated aluminum production also has improved. (Semifabricated aluminum is an "intermediate good" that has undergone significant processing but requires additional working before it is a finished product.)
However, cast products have seen their carbon footprint increase because of the difference in production technologies assessed between 2010 and 2016. According to the study, the ultimate reason for the increase is related to the difference in recycled metal content. In the 2013 study, which looked at the 2010 production year, cast product was represented by sand casting technology, and average recycled metal content was 85 percent. However, in this study, production is represented by die casting technology, and average recycled metal content is assumed to be 80 percent.
Technological advancements such as manufacturing process controls, efficiency improvements from economies of scale, the phasing out of old smelting technologies and the replacement of coal-fired for renewable electricity in smelting have contributed to this trend.
Recycled aluminum’s smaller carbon footprint can be attributed primarily to process efficiency improvement, the study states, including the improved efficiency of furnaces. Scrap feedstock quality also has improved because of better sorting and better pretreatment of scrap).
Regional variations in primary aluminum production also drive significant differences in the environmental footprint of various aluminum products, the Aluminum Association notes. The LCA includes energy use and carbon footprint analysis of product types that include extruded aluminum, aluminum sheet, aluminum foil, die cast aluminum and aluminum sheet and extrusions for the automotive market. Making these products in regions like China or the Middle East, which rely largely on coal and natural-gas-based electricity, can be two to three times as carbon-intensive as making similar products in North America, even assuming similar levels of recycled aluminum usage.
“The message is clear—bolstering domestic aluminum production is good for U.S. manufacturing jobs and good for the climate,” Johnson says.
“Beyond the upfront manufacturing impact, it’s also important to remember how much aluminum benefits products throughout their use phase,” he says. “Aluminum makes buildings greener and last longer; vehicles go further using less energy; and packaging lighter, more efficient to ship and easier to recycle.”
Increasing aluminum recycling also helps make the industry more sustainable. Making recycled aluminum is 94 percent less carbon-intensive than making primary aluminum. Improving the end-of-life recycling rate for aluminum also can have a major impact. Increasing the aluminum recycling rate by 1 percent can reduce the overall product carbon footprint by 80 kilograms of CO2 equivalent per 1,000 kilograms of aluminum produced, according to the study.
However, more than 1 million tons of aluminum end up in landfills annually in North America. The Aluminum Association says it is committed to increasing aluminum recycling rates and is working to accomplish this goal, including advocating for new investment in recycling infrastructure and other policy changes to incentivize the increased collection and capture of used aluminum. Last year, the Aluminum Association joined the Can Manufacturers Institute endorsing a target to achieve a 70 percent recycling rate for aluminum used beverage cans in the United States by 2030.
To review the full LCA report and to read additional life-cycle assessments on various aluminum products, visit www.aluminum.org/SustainabilityReports.
Get curated news on YOUR industry.
Enter your email to receive our newsletters.Latest from Recycling Today
- Unifi launches Repreve with Ciclo technology
- Fenix Parts acquires Assured Auto Parts
- PTR appoints new VP of independent hauler sales
- Updated: Grede to close Alabama foundry
- Leadpoint VP of recycling retires
- Study looks at potential impact of chemical recycling on global plastic pollution
- Foreign Pollution Fee Act addresses unfair trade practices of nonmarket economies
- GFL opens new MRF in Edmonton, Alberta