MICHELIN DEVELOPS RECYCLING BREAKTHROUGH
Michelin North America, Greenville, S.C., on a challenge from the Ford Motor Co., Dearborn, Mich., says it has completed initial tests indicating that new tires can use up to 10 percent of recycled rubber content without sacrificing tire durability or driving performance.
"Although scrap tires have been recycled into various products for years, recycling old tires into new ones has always presented a dilemma," says Clarence Hermann, Michelin’s vice president of product engineering. "This breakthrough will advance the entire industry’s efforts at keeping old tires out of landfills."
Michelin says that, historically, the problem with recycling old tires into new ones has been the lack of a way to break down the chemical components of a tire after it is manufactured. Once rubber has been cured, its chemical makeup changes dramatically, making it difficult to reuse in new tire making.
Michelin has already built prototype tires with recycled rubber content, and is in the process of refining the tire formulation, planning manufacturing processes and beginning long-term testing.
Both companies estimate that recycling scrap tires into new ones could divert up to 30 million tires annually from the scrap tire waste stream. That figure represents about 12 percent of the annual 250 million scrap tires generated each year in the U.S.
NEW PET PLASTIC RECYCLING PROCESS
United Resource Recovery Corp, Spartenburg, S.C., has discovered what the company describes as "a simple and inexpensive process" for recycling polyethylene terephthalate into its original monomers. The new process, trade named UnPET, requires less capital investment than other chemical recycling methods, is competitive with mechanical (melt-process) recycling, and is able to remove impurities even from heavily contaminated scrap.
The new process, which has been granted U.S. patent protection, has been demonstrated in a pilot plant operated by URRC as part of its successful business of refining silver from PET X-ray film. The company now plans to invest more than $5 million in a new facility based on UnPET technology. In addition to developing commercial use of the technology for its core business, URRC plans to license the process.
LARGE FLORIDA STOCKPILE ABATED
The Florida Department of Environmental Protection, in a joint effort with Polk County, Fla., has removed 2.2 million scrap tires from a 20-acre Polk City, Fla., site. The site was identified in 1990 as the largest waste tire site in the state. The $2 million project was financed through the $1 waste tire disposal fee charged on new tires.
The tires were shredded by Waste Management Inc., and are now fuel for the Ridge Generating Station in Auburndale, Fla. In addition, some of the tires have been ground into crumb rubber for use as an asphalt modifier and are targeted for paving of the Withlacoochee Trail, currently under construction.
CONSULTANT SHOWS PAPER SOURCES
With supplies of recovered printing and writing papers tightening and prices soaring, users of these paper grades for recycled fiber will be forced to dig deeper into the waste stream and rely on untapped sources.
A new study from Jaakko Poyry Consulting, Tarrytown, N.Y., titled Insights into Availability and Procurement of Recovered Printing and Writing Papers will analyze the recovered printing and writing paper situation to help buyers and users improve their procurement programs and better understand the marketplace.
"The study is intended to be the definitive guide for companies establishing a recovered printing and writing paper procurement program," says Mary Cesar, senior consultant for Jaakko Poyry. "It will give procurement officials the tools to create a cost-efficient recovered paper purchasing operation and at the same time understand the key components that drive the recovered paper market."
NEW PRODUCTS MADE FROM PLASTICS
The union of three new technologies has made possible the manufacture of useful products from previously virtually non-usable waste plastic, according to Schenectady International, Schenectady, N.Y.
The process is designed to remove expanded polystyrene and other expanded plastics from the waste stream and reprocess them into a variety of strong, light-weight, energy-efficient and flame-retardant thermal insulation products.
Developed by Dr. Benjamin Moser, president of the Institute for Research Inc., and called the ENCAP process, the new product line will first be manufactured by Clearvue Resource Management Ltd.
Get curated news on YOUR industry.
Enter your email to receive our newsletters.
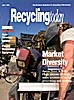
Explore the July 1995 Issue
Check out more from this issue and find your next story to read.
Latest from Recycling Today
- Returpack reports increased DRS activity in Sweden
- Trade groups align against European export restrictions
- Construction, auto sectors show mixed signals
- Politics in Turkey threaten recycled steel outlet
- Toppoint Holdings expands chassis fleet
- Lego creates miniature tire recycling market
- Lux Research webinar examines chemical recycling timetables
- Plastics producer tracks pulse of wire recycling market