Gardeners and landscapers love the look of mulch near shrubs and trees, but are also aware of its shortcomings. The ground up green waste tends to break down and turn gray as the summer progresses, it can carry a pungent odor when first applied, and unfortunate users may bring home termites or carpenter ants with their mulch.
Green Edge Enterprises LLC, St. Louis, is making a product that it believes addresses these problems: mulch made from shredded and colorized scrap tires. According to Green Edge’s Lee Greenberg, the company has been researching and developing the product for five years, and was issued a patent for its colorizing process this June.
“The technical challenge was getting a colorant to bind with vulcanized rubber,” says Greenberg. “That is something that had not previously been done with results that promised any type of longevity.”
The patented process allows Green Edge to convert black shredded tire chips to the color of redwood bark mulch or other popular mulch colors.
The company had been distributing the product as both mulch and loose-fill playground cover. This year, Green Edge has also bagged the colorized chips and sold it through such retail outlets as Home Depot, Lowe’s and at plant nurseries. “It has been in retail bags since the first of the year,” says Greenberg. “We’ve been selling very well to stores here in Missouri as well as in Illinois, Texas, Arizona and other states.”
Greenberg is setting up expansion plans for Green Edge, with distributorships and manufacturing facilities in other parts of the country a possibility in the near future.
TIRE RECYCLER INCREASES PRODUCTION
GreenMan Technologies Inc., Lynnfield, Mass., has increased production capacity by 40% at its Jackson, Ga., facility. The plant can now process 10 million scrap tires annually. The increased capacity allows the company to fully consolidate tires from the Lawrenceville, Ga., facility as well.
“We’ve expanded business down there in an extraordinary fashion,” says Bob Davis, CEO of GreenMan. “We needed the increased capacity to serve our customers and allow ourselves to continue to grow.”
Tires at the recycling plant are shredded and the bead wire and steel are removed. The remaining rubber is in two-inch by two-inch square chips. The chips are used for energy and civil engineering applications.
The start of several major projects may be a factor in GreenMan’s expansion project.
Nearly one million scrap tires in Roberta, Ga., have been cleaned up by GreenMan Technologies Inc., and the company next will begin clean-up of a 1.35 million scrap tire pile near Savannah, Ga.
SENTENCED TO TIRE RECYCLING
In a three-year joint agreement, the Quantum Group Inc., Tustin, Calif., will train and educate minimum security inmates in the tire recycling industry. According to the agreement between Quantum subsidiary QCAL Inc. and the California State Department of Corrections Sacramento Joint Venture Program, initially 12 inmates will be employed in a 10,000 square foot warehouse. A pilot tire recycling processing plant will be completed over three phases and 3.5 tons of California tires will be granulated into 2.2 tons of rubber granules.
The plant will continue to expand over the next nine months and will eventually employ up to 40 inmates. Phase Two will include the installation of the SuperCollider, a machine that processes rubber buffings. Phase Three will include the installation of the company’s continuous roll presses to manufacture flooring materials.
TARGET IMPLEMENTS RECYCLING, REDUCTION PROGRAM
Returning hangers to the manufacturer for reuse, wrapping pallets of merchandise in recyclable plastic wrap, and selling products without excess packaging are just some of the steps Target stores are taking to reduce waste and increase recycling. Target is a division of Minneapolis-based Dayton Hudson Corp.
To make other companies aware of its efforts, Target hosted a “Talk and Tour,” sponsored by WasteCap Wisconsin, Target and the American Plastics Council, in July at Target’s distribution center in Oconomowoc, Wisc.
“The American Plastics Council is showcasing Target stores for their initiative in the Wisconsin area, and nationwide,” says Rob Krebs, director, the American Plastics Council, Washington. “Their example should convince other companies that it is possible to be active in the effort to reduce waste at its source and improve the business bottom line.”
Jenna Kunde, of WasteCap Wisconsin, says many companies are finding that recycling and reducing packaging can be profitable for the business.
“Many businesses are, like Target, finding that they can save money through reducing waste.”
Steps Target Stores are taking to reduce packaging materials include:
• Issuing vendors a manual detailing how to pack materials without tape, tissue, clips, pins or individual bags.
• Returning hangers to the manufacturer for reuse.
• Recycling plastic safety devices on CDs and cassettes.
• Recycling the plastic stretch wrap into plastic lumber for reuse in decks. In 1998, Target recycled 164,000 pounds of stretch film.
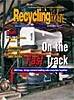
Explore the September 1999 Issue
Check out more from this issue and find your next story to read.
Latest from Recycling Today
- Reconomy brands receive platinum ratings from EcoVadis
- Sortera Technologies ‘owning and operating’ aluminum sorting solutions
- IDTechEx sees electric-powered construction equipment growth
- Global steel output recedes in November
- Fitch Ratings sees reasons for steel optimism in 2025
- P+PB adds new board members
- BlueScope, BHP & Rio Tinto select site for electric smelting furnace pilot plant
- Magnomer joins Canada Plastics Pact