IFC INVESTS IN MBA POLYMERS’ PLANT
The International Finance Corp., as administrator of the Environmental Opportunities Facility, has invested $1.2 million equity in MBA Polymers Inc. to develop and operate a joint venture plastics recycling facility in Guangzhou, China.
MBA Polymers, based in Richmond, Calif., has developed technology that can recycle highly mixed waste streams of high-value plastics on a commercial production scale. Raw material is converted for reuse into high-value engineering plastics, while also providing an environmentally attractive processing channel for a recyclable resource that would otherwise be destined for landfills or incineration.
"Choosing China for its first plastic recycling plant outside the United States was a strategic part of MBA’s international expansion," Karin Finkelston, IFC’s associate director for China, says. "The company’s efforts will help create more sustainable manufacturing activities for all connected industries which, without MBA’s technology, would end up producing waste streams that contaminate groundwater and pollute the air."
MBA CEO Mike Biddle says, "MBA Polymers is pleased to have IFC tangibly recognize the significant environmental and economic benefits of our technology." He adds, "We intend to build additional recycling facilities in countries where IFC is focusing its development efforts and we look forward to further projects together."
The Environmental Opportunities Facility was established in 2002 to provide flexible financing to innovative ventures that have a strong potential to increase environmental sustainability but that must overcome the uncertainty associated with new markets, new technologies and new ways of doing business. It is part of IFC’s Sustainable Business Assistance Program, which provides a platform for making highly selective, strategic interventions in key environmental sectors where the demonstration of sustainable business practices offers potentially significant benefits.
Key funders of the plant include the governments of Austria, Italy, the Netherlands and Norway, as well as IFC.
AERT ADDS WAREHOUSE FACILITY
Advanced Environmental Recycling Technologies Inc. (AERT), Springdale, Ark., a leader in composite building materials technology, has announced the opening of a new warehouse and reload facility adjacent to its Lowell, Ark., plastics recycling plant.
The new 25-acre site initially consists of two 100,000-square-foot warehouses connected by rail spurs and a 10-acre finished goods reload facility designed to load up to five railcars and 10 trucks at a time. The site also has room for an additional 200,000-square-foot warehouse. AERT is leasing the facility, with an option to buy, for $54,000 per month.
"The new facility will allow the company to bring in and stage recycled plastic by rail, prior to processing, from around the country," AERT Chairman Joe G. Brooks, says. "The additional finished goods storage will positively address the ever-increasing demand for AERT decking products by allowing us to ship large quantities of decking by rail to strategic reloads throughout North America."
AERT converts reclaimed plastic and wood fiber scrap into Weyer-haeuser ChoiceDek outdoor decking systems, MoistureShield door and window components, MoistureShield CornerLoc(TM) exterior trim and fascia components and MoistureShield outdoor decking. AERT operates manufacturing facilities in Springdale, Ark.; Lowell, Ark.; Tontitown, Ark.; Junction, Texas; and Alexandria, La. The company’s products are sold across North America. ChoiceDek Premium decking is marketed exclusively through Lowe’s Home Improvement Warehouses throughout North America.
WRAP TESTS COMMERICAL USES FOR RECYCLED
PLASTIC
U.K.-based Waste & Resources Action Program (WRAP) is conducting a series of commercial trials to assess the use of recycled PET (R-PET) plastic in retail packaging.
Coca-Cola Enterprises Ltd., Marks & Spencer and Boots are among the companies involved in the program.
Two of the three trials involve food and beverage packaging. Adhering strictly to food contact regulations, these are designed to prove the safety and suitability of R-PET.
"The project will also allow us to work more closely with the high volume suppliers of R-PET to help to secure supply and consistent quality and to improve our understanding of the economics of the market," Peter Skelton, WRAP’s materials development manager of plastic, says.
The project will be completed in March 2006 and the results made publicly available by early Summer 2006.
LME TO HOST PLASTICS SEMINAR
The London Metal Exchange will stage its inaugural plastics industry seminar called "A Perspective on Plastics," May 24, 2005, in London.
The event marks the LME launch of futures contracts for polypropylene and linear low-density polyethylene May 27, 2005.
The seminar features presentations from key figures from the plastics industry, including a keynote presentation on global economic outlook.
Additional information is available at www.lme.com/plastics-seminar.asp.
RPM COMPLETES ILLINOIS PLANT
RPM Technologies Inc., based in Plainfield, Ill., has announced the completion of its new grinding and processing plant in Park Forest, Ill.
RPM provides subcontractors with molds and resins for the manufacture of plastic pallets. RPM’s resin processing occurs at the company’s facilities and incorporates a system of grinding consumer and industrial plastic scrap into recycled resins.
RPM says its Park Forest expansion will accommodate growth in the company’s grinding and processing operations stemming from recent agreements with several large post-consumer plastic scrap collectors.
Initially, the company expects to receive and process more than 750,000 pounds of mixed-color HDPE scrap per month, approximately 37.5 percent of the facility’s monthly capacity of 2 million pounds.
"We are very excited about this expansion," says Randy Zych, CEO of RPM Technologies. "Installation of our custom-designed grinding and processing equipment was successfully completed as proven during our initial runs. We expect to bring this line up to speed quickly, approaching desired capacity sometime during the first quarter of 2005."
The Park Forest facility complements RPM’s other grinding and processing facility in Norman, Okla., which serves the Southwestern U.S. RPM expects to receive 400,000 pounds of post-industrial and post-consumer plastic scrap for processing and later resale. As a result, this facility is expected to reach profitably during the fourth quarter of 2004.
SAFETY-KLEEN CANADA LAUNCHES PROGRAM IN QUEBEC
Safety-Kleen Canada has launched a used oil recovery program in Quebec. The company says it guarantees to recycle used motor and lubricating oils it collects in the province to prevent them from being burned in facilities and polluting the air.
Used oil collected in Quebec is re-refined at Safety-Kleen’s facility in Breslau, Ontario, and returned for re-sale in Quebec.
Under the recovery and recycling program, any Safety-Kleen Performance Plus lubricating oil customer that designates Safety-Kleen as its collector for used oil and used oil containers will not be charged any environmental charges, fees or levies on its purchases of oil and oil containers, and Safety-Kleen will pick up the used oil and used oil containers for free.
"There are no up-front fees or back-end charges," Pierre Gendron, Safety-Kleen’s Quebec market manager, says. "In fact, customers actually save money by avoiding certain environmental surcharges and levies," he adds.
Safety-Kleen says its used oil recycling program is an environmentally friendly alternative to a used oil collection and burning program designed by the Canadian Petroleum Products Institute (CPPI) and recently proposed by Recyc-Quebec, a Quebec government agency, and Société de Gestion des Huiles Usagées (SOGHU), a group of large lubricating oil brand-owners, including major members of CPPI. If this program is implemented in Quebec, Safety-Kleen is concerned that it will lose its supply of used oil to those who would burn it.
"Quebec produces used oil that can be recycled back into high-quality oil, comparable in quality and performance to new oil," Gendronsays. "The SOGHU program encourages the burning of used oil as a one-time fuel, and that oil then has to be replaced. The choice for consumers and the environment is clear—reuse and recycling or pollution and continued dependence on imported oil."
Gendron says that Safety-Kleen has filed a legal challenge to the SOGHU program, alleging that it is inconsistent with the government of Quebec’s waste reduction policies, which promote the reuse and recycling of resources. He says the SOGHU program also ignores a Supreme Court of Canada ruling about environmental measures anticipating, preventing and attacking causes of environmental degradation.
OHIO EPA ORDERS CLEANUP
The Ohio Environmental Protection Agency has ordered the owner of Ray’s Wrecking, based in Toledo, Ohio, to clean up an estimated 15,000 scrap tires illegally disposed of on the property.
The business has been given 120 days to remove all the scrap tires from its property and to have them legally disposed of by a licensed transporter at a licensed disposal facility. The orders require the business to take immediate mosquito control measures to prevent breeding.
Violations of Ohio’s open dumping and scrap tire laws were discovered at the facility in April 1997 during an inspection conducted by the Toledo-Lucas County Health Department. The health department worked with the owner of Ray’s Wrecking for several years, but the violations went unresolved. Ohio EPA first inspected the property in July 1999 and cited a number of violations, however the owner did not comply with instructions to clean up the tires.
During the most recent inspection Nov. 12, 2004, Ohio EPA and the health department observed a large, elongated pile of scrap tires on the property. Violations cited were open dumping, failure to maintain fire lanes, failure to keep tire pile height and base area within maximum dimensions, failure to use mosquito control, operating a solid waste facility without a registration or permit and operating a scrap tire facility without a license.
GREENMAN MAKES ITS INTENTIONS KNOWN
GreenMan Technologies Inc., Lynnfield, Mass., has executed a letter of intent containing an exclusive option to acquire certain operating assets of Winston-Salem, N.C.-based Tires Into Recycled Energy and Supplies Inc. (TIRES Inc.).
TIRES Inc. is a crumb rubber producer with nearly 60 million pounds of yearly production capacity.
GreenMan can exercise the purchase option during the next 12 to 21 months if TIRES Inc. meets certain predetermined performance criteria.
In return for the exclusive purchase option, GreenMan says it has issued $200,000 of common stock to be applied toward the purchase price if the acquisition is successfully closed or to be forfeited if the company doesn’t exercise the option.
GreenMan has also agreed to lease certain pieces of processing equipment owned by TIRES Inc. with an option to buy. The parties have agreed to use a previously issued $350,000 good-faith deposit to prepare and to move the leased equipment to GeenMan’s Tennessee plant.
Additionally, GreenMan has executed a multi-year agreement to supply TIRES Inc. with rubber feedstock from its Georgia and Tennessee plants.
"This relationship allows us to immediately leverage each of our strengths with the potential for strong accretive performance by joining our two companies in a more permanent basis in the near future," Bob Davis, GreenMan president and CEO, says.
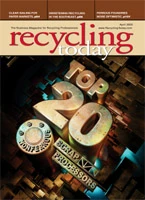
Explore the April 2005 Issue
Check out more from this issue and find your next story to read.
Latest from Recycling Today
- Fitch Ratings sees reasons for steel optimism in 2025
- P+PB adds new board members
- BlueScope, BHP & Rio Tinto select site for electric smelting furnace pilot plant
- Magnomer joins Canada Plastics Pact
- Out of touch with reality
- Electra names new CFO
- WM of Pennsylvania awarded RNG vehicle funding
- Nucor receives West Virginia funding assist