DRUM MAKER NOW USING RECYCLED PLASTIC
U.S. Coexcell, Maumee, Ohio, is now using recycled plastic in the manufacture of its 55-gallon plastic drums because of a breakthrough in its processing technique. Company officials say that until recently, producing large moldings of recycled plastics was not possible due to material degradation of the recycled plastic – it has been done with soft drink bottles, but not in larger applications.
The company is currently in full-scale production of drums that use post-consumer regrind, along with virgin HDPE. Coexcell’s process begins with the manufacture of a 55-gallon plastic drum. Then, after it is shipped to the customer, used and emptied, the container is returned to a Coexcell network company for reconditioning. Once cleaned, the drum is returned to the original customer for repeated use until the end of its service life. At that point, the drum is returned to Coexcell, and the company then grinds it, forms the PCR into pellets and uses them to make new drums.
It is at the remanufacturing stage that Coexcell says its unique process enables previously used material to be melted again. The company has a co-extrusion, blow-molding process that molds three layers at the same time, so the PCR can be used in the middle layer. Each drum will contain about 7.5 pounds of PCR. Currently, Coexcell produces 225,000 drums per year, which will require 1.7 million pounds of recycled material.
“This breakthrough paves the way for major chemical manufacturers and fillers to practice environmental stewardship and comply with the recycling legislation that confronts the industry,” says Robert Huebner, president of U.S. Coexcell.
FIBERGLASS WON’T CONSUME MUCH CULLET
Despite recycled-content laws, the use of glass cullet in fiberglass is not likely to increase much during the next few years unless there are significant improvements in the quality of cullet available at an affordable price, according to spokesmen from several major fiberglass producers, who addressed the Institute of Scrap Recycling Industries’ September glass cullet roundtable.
“Owens-Corning’s historical use of cullet has increased since the mid-1970,” said Joe Kaplan, manufacturing support engineer for Owens-Corning Fiberglass Corp., Toledo, Ohio. “The three hundred thousand tons of cullet we purchase each year is used as a cost-control measure. It is also used for environmental and marketing reasons.”
Although 100 percent cullet could theoretically be used to make fiberglass, he says, this is not practical, in part due to the cullet’s geographical availability and the relative cleanliness of the cullet. Owens-Corning works with just a handful of processors across the continent to supply cullet that meets the company’s specifications.
“We are unable to use more cullet at this time because of the cost,” says Kaplan. “We can’t get the material we want at the price we want. There are opportunities for recyclers to supply the fiberglass market, but they have to meet our quality and cost requirements.”
SMUCKERS SWITCHES TO PAPER RING
Smucker Quality Beverages, Chico, Calif., is switching to a paperboard ring carrier made of 33 percent recycled fiber in place of a plastic one on more than 50 of its carbonated juice beverages. The company made the move because of concerns that the plastic ring carrier, if disposed of improperly, could be a danger to various wildlife that get caught in the holes of the rings, then die from strangulation.
The new paperboard carrier, developed by International Paper, can be recycled with corrugated material and biodegrades over time. Smucker’s expects to use more than 10 million carriers per year based on last year’s sales.
“We have a company policy to reduce waste whenever possible,” says Bill Knudsen, general manager of SQB. “For instance, much of the pulp from fruit we press is fed to livestock rather than discarded. We also have an extensive company recycling program.”
DOMINO PLASTICS DELIVERS 20 MILLION POUNDS OF SCRAP
Domino Plastics Co., Trenton, N.J., has marked its half-year anniversary by delivering 20 million pounds of scrap plastic globally. “These numbers are outstanding for any established business in the scrap industry,” says Michael Domino, founder of the company, “and we’ve achieved these levels in only six months of operation.”
Domino estimates that 50 percent of the company’s current business involves customers abroad, particularly in the Pacific Rim.
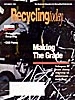
Explore the November 1995 Issue
Check out more from this issue and find your next story to read.
Latest from Recycling Today
- Indiana county awarded $65K recycling grant
- Mixed paper, OCC prices end year on downward trend
- Updated: CAA submits final draft program plan in Oregon
- Enviri names new president of Harsco Environmental business
- Survey outlines ‘monumental challenge’ of plastic packaging collection in UK
- Nippon Steel acknowledges delay in US Steel acquisition attempt
- BASF collaborates to study mechanical plastic recycling
- Commentary: navigating shipping regulations for end-of-life and damaged batteries