TRADITIONAL PACKING PEANUTS BEWARE
Free-Flow Packaging Corp., Redwood City, Calif., has introduced a new recycled-content product, a loosefill designed specifically for shipping heavy items. Called Super 8 loosefill, the product is manufactured from 100 percent recovered polystyrene. Between this product and the company’s other recycled loosefill, called FLO-PAK, Free-Flow Packaging has recycled more than 30 million pounds of expanded polystyrene.
"Super 8 is our strongest product yet," says Arthur Graham, president of Free-Flow Packaging. "We see it as a ‘safety cushion’ for our clients’ heavier items, but it also provides excellent protection for the most delicate items."
CANADIAN RECYCLER OPENS TWO PLANTS IN MARITIMES
Tire Recycling Corp., Manitoba, Canada, plans to build two new plants in the eastern Canadian Maritime provinces of New Brunswick and Nova Scotia.
The company, which currently employs 40 people in its one Manitoba plant, uses a process developed in Europe to turn scrap tires into rubber mats and sidewalk and paving blocks. Tire Recycling uses close to 50 percent of the scrap tires generated in Manitoba. The finished products are marketed throughout Canada and the U.S.
In expanding eastward, the company is working closely with the Manitoba-based Mennonite Central Committee, an international development organization whose focus in this case is to help create jobs in economically depressed areas of Canada. The MCC will be investing $100,000 (about $72,000 U.S.) in each of the new Tire Recycling Atlantic Canada Corp. plants. Tire Recycling will put up $150,000 (about 108,000 U.S.) in cash. The remaining $2.1 million (about $1.5 million U.S.) in start-up funding will be raised through private investors.
The new plants will employ about 75 people in each province. A site has been selected in New Brunswick near Moncton, but to date no location has been chosen in Nova Scotia. The products produced in the new plants will differ from those made in Manitoba, although exactly what products will be produced has yet to be determined, according to a company spokesman.
MACMILLAN BLOEDEL MAKES NEW LINERBOARD
MacMillan Bloedel Packaging Inc., Montgomery, Ala., has introduced a new 100 percent recycled linerboard product. Called Enviro-Mac, the product is made from old corrugated containers and recovered paper. The linerboard is produced at MacMillan Bloedel’s new Henderson, Ky., plant, which recycles 450 tons of OCC and recovered paper daily.
OLD SHOES, TIRES MAKE NEW SURFACE
The first basketball court in the country made of recycled athletic shoes and tires has been installed at the Puget Sound Christian College in Edmonds, Wash. SATECH, Kirkland, Wash., the company which developed the project, has pioneered the recycling of whole used sneakers into athletic playing surfaces.
Working in partnership with Scougal Rubber, Seattle, and GACO Western, Tukwila, Wash., SATECH uses post-consumer sneakers and tires to make molded pads, which are then covered with urethane coatings that simulate a traditional wood finish. Performance tests have been conducted on the surface by the University of Michigan, Detroit Testing Lab and researchers from the athletic footwear industry.
"Initial data has been very positive," says Mary Fabien, recycling technology specialist with Clean Washington Center, Seattle. Full reports on the testing will be available shortly from CWC.
ROUSE URGES TIRE RECYCLERS TO KNOW MARKET; DELIVER A QUALITY PRODUCT
Appearing as the keynote speaker at the International Tire And Rubber Association’s 39th World Tire Exhibition in Louisville, Ky., last April, Michael Rouse, president of Rouse Rubber Industries Inc., Vicksburg, Miss., urged scrap tire processors to "know the market, and know the equipment" that is out there to process scrap tires. Rouse said that there are currently several different methods to process tires – from ambient to cryogenic grinding – and pointed to advances in producing smaller mesh sizes of crumb particles and new surface treatments that manufacturers claim enhance the marketability of crumb rubber.
These newer treatments, some which have had their validity questioned by many in the industry, include devulcanization via a chemical additive, microbe action and high-pressure pulverization; or altering the rubber’s surface with gases to enhance adhesion for manufacturing.
Rouse also urged those processors that are targeting the crumb rubber market to invest in test equipment to accurately determine gradation and chemical make-up of the final material, and not to procure crumb that contains a wide range of compounds. "There are sieve, surface and chemical analyzers available to processors at reasonable prices so that they can ensure that they are delivering a quality product to the marketplace," he said.
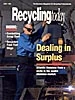
Explore the June 1996 Issue
Check out more from this issue and find your next story to read.
Latest from Recycling Today
- New recycling grant program launches in Massachusetts
- Tire Recycling Foundation names executive director
- Dock 7 named 2025 Exporter of the Year at New Jersey International Trade Awards
- Waste Connections reports ‘better than expected’ Q1 results
- Commentary: How EPR is transforming the packaging industry
- Acerinox names new North American Stainless CEO
- Greenwave closes 2024 books with red ink
- Steel Dynamics nets $217M on record shipments