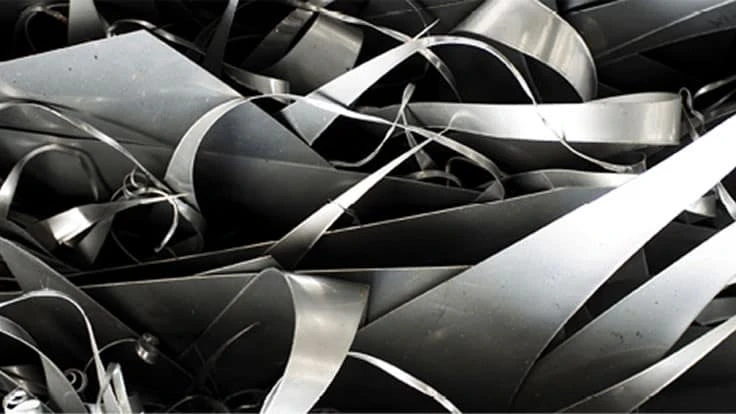
© Ramin / stock.adobe.com

The phrase “It’s complicated” can apply to many endeavors in the scrap industry, but perhaps the foremost example is tied to the collection, sorting and marketing of stainless steel and other nickel-bearing alloys.
Producers and recyclers of this expanded family of metals have long used the adjective “specialty” as a descriptor. Based on presentations given at the ISRI2021 online convention hosted by the Washington-based Institute of Scrap Recycling Industries (ISRI) in late April, this specialization is poised to continue.
The two stainless steel and nickel industry analysts who spoke at the ISRI2021 Nickel and Stainless Spotlight described a stainless steel market with a very different production method in China versus most of the rest of the world. Additionally, they said nickel, stainless steel and specialty alloys applications could face significantly different prospects if the global electric vehicle (EV) revolution picks up speed.
A tale of two hemispheres
China makes about half of the world’s stainless steel, but it imports very little of the rest of the world’s stainless scrap because of the production method decided upon by its large-volume producers.
Stainless steel in China is made predominantly by melting nickel pig iron (NPI) made from ores mined most often in Indonesia, the Philippines and other nearby nations. When it comes to major stainless steelmaking nations’ scrap usage rates, Markus Moll of Austria-based Steel & Metals Market Research GmbH (SMR), said “two worlds” exist.
While China uses less than 25 percent scrap as feedstock because of its NPI reliance, scrap carries from 70 to 75 percent of the metallics load in stainless production in Europe. The United States and India, meanwhile, can consume as much as 80 percent scrap in their stainless production. In the U.S., this is because of electric arc furnace (EAF) technology, and in India it is because of induction furnace methods.
The result for U.S.-based scrap processors and exporters is that stainless steel scrap has not been exported in the same volumes as aluminum or copper scrap, even before the Chinese government introduced quotas and restrictions in 2019.
Moll said “11 percent of stainless steel scrap was consumed on a different continent [from] where it was generated” in 2020. Common trading patterns include Russia and some of its neighboring nations supplying scrap to Western Europe, with the U.S. predominantly sending scrap to Asian nations, including India, South Korea and Taiwan.
Of the stainless scrap generated last year, Moll estimated 36 percent was obsolete scrap, 32 percent was prime or factory-generated scrap, 23 percent was revert scrap that never left the melt shop and 9 percent was marketed as blended scrap, making its origin difficult to determine.
Demand for nickel-bearing scrap has been ramping up in the U.S. as North American Stainless, based in Ghent, Kentucky, and other producers return to output levels closer to those they enjoyed before the COVID-19-related downturn.
On the scrap export front, it is not clear whether West Coast recyclers in the U.S. could start receiving inquiries from mills in China since that nation has approved the shipment of three grades of stainless steel scrap for importation in 2021.
Although scrap prices might not always reflect it, Moll said a “higher availability of high-quality scrap is needed” as stainless steel producers and the manufacturers that use stainless steel seek lower carbon footprints.
While better scale pricing could fetch some additional stainless scrap (or prevent it from being blended with carbon steel scrap), Moll said the future also could lead to “green ferroalloys” produced similarly to how hot-briquetted iron (HBI) and direct-reduced iron (DRI) are made for the carbon steel sector.
Revving up or winding down?
The transition from internal combustion engine (ICE) vehicles to electric vehicles (EVs) that appears to be gaining momentum globally will yield winners and losers in the nickel and stainless steel sectors.
More has been written about nickel content in EV batteries than about several other aspects of how either nickel or stainless steel might fare if ICE vehicle production plummets. SMR’s forecast calls for stainless steel demand from the transportation sector to drop during the next five years.
“This is very clearly the e-car issue,” Moll said. “If you look at a car today, it has about 40 kilograms (88 pounds) of stainless steel for a normal passenger car. Out of that, 30 kilograms (66 pounds) is the exhaust system. Other applications are fuel lines and engine valves, the head gasket—all these applications depend on the combustion engine.”
He added, “So, in an e-car, you still have hose clamps and trim, but it’s probably only 20 percent of what you have in a combustion engine car.”
Moll said he did not see a particularly bright future for hybrid cars, which retain some of the stainless components, calling the hybrid powertrain “just a bridge technology. In five years, the [EV] batteries will be so good, nobody needs a hybrid car. In 10 years, nobody will [buy] a hybrid car.”
The alternative energy market holds some good news for stainless producers when the attention shifts to ships, trucks, buses and heavy vehicles that use larger battery cells. The housings for these cells typically are made of stainless steel.
Moll’s fellow presenter, Alina Racu, a Switzerland-based market analyst with Russia-based Nornickel, said EV sales globally rebounded in the second half of 2020, with Europe and China being “the epicenters of growth,” while North America exhibited modest growth. The global figures demonstrate EV momentum, with 26 percent year-on-year growth in 2020 compared with 2019 and a 78 percent jump in sales in December 2020 compared with December 2019, Racu said.
She cited legislation and stimulus plans as among the drivers behind the switch to EVs. While Europe and its Green Deal point to that continent’s intentions, whether Joe Biden and his “Build Back Better” plan or CLEAN (Climate Leadership and Environmental Action for our Nation) Future Act can make it through the U.S. Congress with some of their electrification incentives intact remains to be seen.
Follow the green brick road
The growth of EV sales represents just one aspect of a potential “decarbonization” effort tied to the Paris Agreement and its target dates to reduce greenhouse gas (GHG) emissions.
Moll and Racu referred to national and global goals to reduce GHG emissions as factors that seem poised to alter the dueling hemispheres model.
Moll said making stainless steel with primary materials predominating, as in China, produces carbon dioxide (CO2) at a ratio of 4.3 to 1. That contrasts with the 1.1 to 1 ratio belonging to scrap-fed production. Policies such as the Green Deal in Europe and others being made in response to the Paris Agreement are leading to a “border adjustment mechanism to prevent CO2 leakage,” he said.
Racu said the conversion processes often used by Chinese companies to produce nickel pure enough to use in EV batteries also are problematic in creating large amounts of CO2, sulfur dioxide and other GHGs.
As in stainless steel production, nickel refining methods also are being influenced by corporate goals and government mandates. “While there are multiple sources of nickel supply coming up, their usage in the batteries sector will depend on compliance with ESG (environment, social and governance) standards,” she said. “Western [original equipment manufacturers] will likely prioritize ESG-compliant nickel over alternatives with high carbon footprints,” Racu added.
On the battery front, she predicted that the low-nickel lithium iron phosphate batteries being manufactured in China will not win out over emerging, upgraded nickel cobalt manganese batteries or other lithium-ion configurations that are being used around the world.
To what extent can scrap recyclers expect to get involved with recovering nickel and other metals from these emerging batteries? The answer could depend on whether EV makers insist upon closed-loop systems for their batteries. Repurposing, or finding a second use for EV batteries, also could disrupt collection.
Racu said forecasting how EV battery recycling will take shape is difficult in part because current volumes of such end-of-life batteries “are very small,” with EV recycling “in its very early stages.”
She showed three different scenarios, however, tied to varying levels of EV sales, the percentage of batteries that are repurposed and the collection rate. In the most aggressive scenario, EV battery makers could reach a point where from 42 to 49 percent of the nickel used in new batteries consists of recycled-content nickel. The other scenarios, however, placed this percentage in a more modest 12 to 21 percent range.
How the EV market influences nickel and stainless steel demand provides just one more fault line that could lead to the end of some scrap flows and the creation of new ones.

Explore the June 2021 Issue
Check out more from this issue and find your next story to read.
Latest from Recycling Today
- Lautenbach Recycling names business development manager
- Sebright Products partners with German waste management equipment company
- WasteExpo transitions to biennial format for enhanced experiences
- Study highlights progress, challenges in meeting PCR goals for packaging
- Washington legislature passes EPR bill
- PureCycle makes progress on use of PureFive resin in film trials
- New copper alloy achieves unprecedented high-temperature performance
- Gränges boosts profits and sales volume in Q1 2025