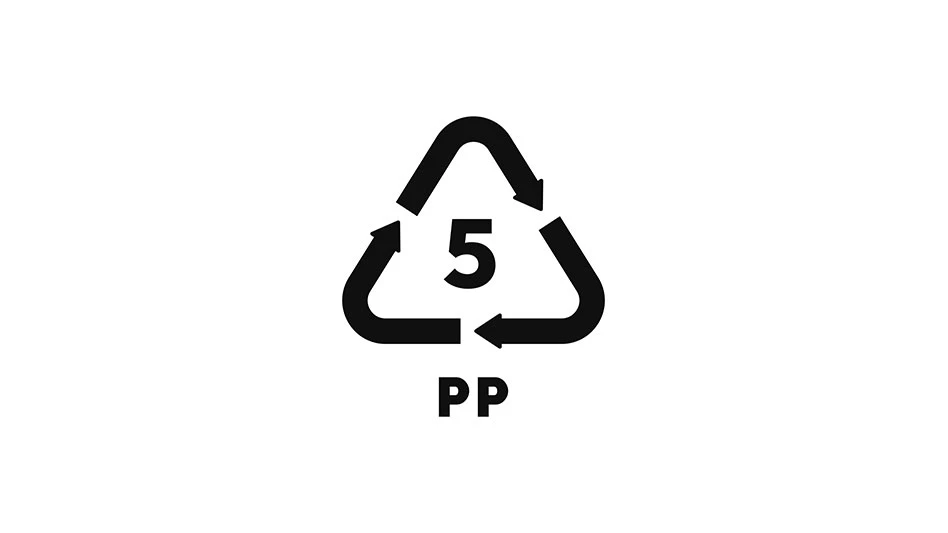
Vandhira | stock.adobe.com
The latest report on the climate crisis by the Intergovernmental Panel on Climate Change (IPCC) highlights the dire consequences to humanity if we don’t drastically address the issue of carbon dioxide emissions (CO2e) into our atmosphere.
This scientific consensus combined with the fact that most solutions to avoid the worst consequences of climate change exist provide a unique opportunity for us to address the gaps and take action.
This message is further reinforced by the United Nations Environmental Program’s (UNEP’s) recent report that examines the economic and business models needed to address the impacts of the plastics economy.
As the report points out, the world currently produces 430 million tons of plastics per year, two-thirds of which are short-lived products that soon become waste. Worse still, this figure is set to triple by 2060 based on current trends.
By focusing on the plastics and packaging industry, we can make a significant contribution to reducing the CO2e associated with this sector. Each ton of recycled plastic saves at least 1 ton of CO2 and, in the case of food-grade recycled polypropylene (FGrPP), an estimated 1.6 metric tons of CO2e can be saved compared with using virgin PP resin.
This has been our goal since launching NextLoopp Europe in 2020. With the 48 major organizations that have joined our multiparticipant project, we are on track to produce a world-first: FGrPP that is U.S. Food and Drug Administration (FDA) and European Food Safety Authority (EFSA) approved.
This will have a dramatic impact on reducing our CO2e, given that one 20,000 metric tons per year plant would save 32,000 metric tons of CO2e annually.
Why polypropylene?
As multiple innovative solutions around the world continue to be deployed to reduce carbon emissions and manage the growing waste stream, it is worth honing in on why NextLoopp is so focused on PP.
PP makes up 20 percent of global plastics production, a figure that is growing at rate of 6 percent annually.
In 2018, 56 million metric tons of PP were produced, valued at $97 billion. According to estimates, by 2025 we will produce 83 million metric tons annually worth $147 billion.
PP is present at a critical percentage in the packaging stream, which means it can be readily recycled once it is collected.
Importantly, the biggest market for consumer-focused plastics is food packaging, and PP plays an invaluable role in protecting and storing food. It most often is used for single-serve containers, such as soup pots, ice cream tubs and takeaway food containers. In addition to being one of the FDA-approved food-contact materials, it is microwave safe and nonvolatile, which means it will not react with any type of food, whether it’s acidic, basic or liquid.
The downside of food-grade PP is that until recently we have been unable to produce recycled FGrPP, which has meant all PP food packaging is made only from virgin plastics.
These complexities are a global challenge that has been driven in part by the industry’s focus on recycling PET drink bottles and single-use plastics, such as bags and straws.
Relooping vs. recycling
With the acceleration of climate change, it is vital we update our perspective on recycling. To date, recycling entails converting used products into recovered materials that can be used in other products, which historically, have been lower-value products. Now, we have the technological know-how to reloop used products into equal-value materials and products. In so doing, we simultaneously reduce waste and our reliance on virgin resources.
Harnessing a range of cutting-edge technologies to sort and decontaminate postconsumer PP packaging, the NextLoopp project is turning postconsumer PP packaging into high-quality food-grade resins.
Guided by the carbon budget
As the world transitions from a linear to a circular economy model, organizations increasingly find themselves wading through complex legislation and responding to consumer pressure. This should be countered with the deep understanding that all future decisions relating to plastics and recycling must be driven by CO2 emissions.
As such, the recent swing toward using rPET should be seen as increasing the environmental impact given that rPET has a higher carbon footprint than rPP.
Plastics Europe’s Life Cycle Assessment flagged this up when it compared the carbon footprint of a range of different recycled plastics, showing that recycled high-density polyethylene, or HDPE, (such as milk bottles) and recycled PP (such as most pots, tubs and trays that contain food) have a 25 percent lower carbon footprint than recycled PET.
Keeping our limited carbon budget top of mind is the driving force of the NextLoopp project that is trialing two key grades of rPP. The first is a high-purity FGrPP decontaminated to be food-contact compliant, and the other is INRT, a high-quality polymer developed specifically for packaging that requires no odor and no migration, such as cosmetics, personal care packaging and low-VOC [volatile organic compound] automotive applications.
Now NextLoopp is setting its sights on replicating this success in the Americas, inviting expressions of interest as it fine-tunes a game-changing NextLoopp Americas venture scheduled to launch in the third quarter of this year.
This venture is being tailored to respond to America’s unique requirements.
PP in the USA: A missed opportunity
According to Science Direct, approximately 2 billion metric tons (Bt) of municipal waste were collected in the U.S. in 2018, with a global recycling rate of 18 percent (362 million metric tons), while the rest of the waste was sent to composting/energy recovery, landfill or the surrounding environment. Of all end-of-life plastics, PP is one of the most converted polymers, with a market share of about 20 percent in 2018, but it is also one of the least recycled (3 percent to 5 percent) mainly given its use in nonbottle products such as pots tubs and trays.
The Recycling Partnership’s “2020 State of Curbside Recycling” report highlights the fact that PP is not broken out as a separate polymer in the United States. To date, it largely has been collected in curbside programs and sorted in material recovery facilities (MRFs). Many MRFs have specific polymer sorting capacity focused on PET and HDPE because these polymers have more market demand. They are also more readily recognized mainly as bottles and are currently available in higher quantities than PP, which appears in pots, tubs and trays in the household stream rather than in bottles.
Yet this same report suggests as much as 17 pounds of PP could be available per year from a single-family household. This would place PP at higher generation rates than natural and colored HDPE, with United States single-family households generating an estimated 827,000 tons per year.
Joining the new plastics economy
NextLoopp is very much part of the global transition to a new plastics economy, which, ultimately, is the most cost-effective way to ensure plastic pollution is substantially reduced by 2040.
The solutions at hand require vigilance, determination and creativity, however, as UNEP’s report clearly states that the investment costs of the required systems change are less than the current investment trajectory, around $65 billion per year through 2040 as opposed to $113 billion per year.
Crucially, time is of the essence. According to The Pew Charitable Trusts and Systemiq 2020, a five-year delay could lead to an increase of 80 million metric tons of plastic pollution.
As NextLoopp Americas gears up to address these challenges, it is worth noting that recovering PP will not only reduce waste and our reliance on virgin PP but will also offer increased economic benefit and jobs, importantly, and contribute toward keeping our carbon budget within a liveable range.
Please send expressions of interest in NextLoopp Americas to info@nextloopp.com.
Edward Kosior’s expertise in the plastics recycling sector spans nearly 50 years, including time as an academic and time working in plastic packaging recycling. He has been instrumental in designing numerous modern recycling plants and has achieved a number of patented recycling breakthroughs. In 2004, Kosior founded U.K.-based Nextek Ltd. to provide consultancy services to assist in the strategic approaches to sustainable packaging, waste reduction and minimal life cycle impact. He is Nextek’s managing director and is involved with many industry associations, universities and research organizations. He can be contacted at edkosior@nextek.org.
Latest from Recycling Today
- APR, RecyClass release partnership progress report
- Clearpoint Recycling, Enviroo sign PET supply contract
- Invista expanding ISCC Plus certification program
- Redwood partnership targets recycling of medium-format batteries
- Enfinite forms Hazardous & Specialty Waste Management Council
- Combined DRS, EPR legislation introduced in Rhode Island
- Eureka Recycling starts up newly upgraded MRF
- Reconomy Close the Gap campaign highlights need for circularity