
Municipal/IC&I
Rumpke opens largest MRF in North America
During the planning process for the Rumpke Recycling & Resource Center, a $100 million facility now open in Columbus, Ohio, Rumpke Senior Vice President of Recycling & Sustainability Jeff Snyder and his team visited material recovery facilities (MRFs) across the country, researching innovation and technological advancements in the industry.
Now open in Columbus, the Rumpke Recycling & Resource Center is the largest and most technologically advanced recycling facility in North America, according to the company, with the ability to process up to 250,000 tons of recyclables per year from more than 50 Ohio counties.
“This will be the model for future MRFs,” Snyder says.
Cincinnati-based Rumpke Waste & Recycling first expanded to Columbus in 1991 and, since 2011, operated a MRF with a processing capacity of 160,000 tons per year. The new recycling center was designed to have the capacity to accommodate growth in and around Columbus, one of the fastest-growing metropolitan regions in the country, which is expected to grow to 3 million residents in the next 20 years.
“What this region needed was more capacity to capture that growth,” Rumpke Waste & Recycling President Andrew Rumpke says. “We have this capacity that is going to be able to capture the growth in Columbus while also allowing us to continue to drive more recycled material into the circular economy.”
The 226,000-square-foot facility was custom-built for Rumpke’s desired equipment layout and is outfitted with a line designed by Plessisville, Quebec-based Machinex, featuring four ballistic separators, 19 optical sorters and 10 artificial intelligence (AI) units. Using AI, the company’s optical sorters can separate aluminum foil from used beverage cans (UBCs), segregate colored polyethylene terephthalate (PET) bottles and thermoformed containers from clear bottles and more, Snyder says.

Throughout the facility, nine vacuums suck plastic bags off the line at transition points along the conveyor belts. The facility also has been outfitted with two ceiling-mounted cranes that can be used for maintenance or to reconfigure equipment and a hydraulic lift “tipper” that can unload 50-foot trailers of material.
The facility processes 60 tons per hour and has an expected recovery rate of 98 percent. It employs 60 people, including 28 sorters and a full-time education staff.
With its Columbus Recycling & Resource Center, Rumpke also is rethinking how it interacts with the community and builds trust with the public.
The facility boasts a number of public spaces and educational areas, including an education center with interactive exhibits developed in cooperation with COSI (Center of Science and Industry) as well as a research center designed in partnership with The Ohio State University.
“We’re welcoming in communities, municipalities, schools [and] neighbors,” Snyder says.
Rumpke supplies recovered materials to manufacturers within a 250-mile radius of the site, with 80 percent going to companies with operations in Ohio, including Eastman, Pratt Industries and Owens-Illinois. In terms of commodities, Rumpke says end products will be consistent with what was coming out of the company’s original Columbus MRF.
“This facility is about scale,” Andrew Rumpke says. “It’s scaling up to meet the demands of the growing Columbus area, and we’re always looking at and researching what’s the next material type that we [can recover].”
To increase local sustainability efforts and create transparency, customers can use the recycling center’s Sample Station, equipped with a separate tipping floor. Sampling capabilities will provide a real-time recycling audit to help customers measure their recycling program’s success or identify necessary adjustments.
Rumpke Waste & Recycling is one of the nation’s largest privately owned residential and commercial waste and recycling firms, providing service to areas of Ohio, Kentucky, Indiana, Illinois and West Virginia. The company operates landfills, transfer stations and 15 recycling facilities, including material recovery facilities in Cincinnati and Columbus, as well as a glass processing facility in Dayton, Ohio.

Batteries
ERI opens alkaline battery recycling plant
ERI, based in Fresno, California, has opened its first alkaline battery recycling plant. The information technology asset disposition (ITAD) and cybersecurity-focused hardware destruction company opened the plant within its existing 315,000-square-foot electronics recycling and ITAD facility in Plainfield, Indiana.
ERI co-founder, Chairman and CEO John Shegerian tells Recycling Today the company has targeted alkaline batteries because it is responding to a need.
“ERI invests millions of dollars annually into research, development and automation, keeping us at the forefront of the ITAD and electronics recycling industry and constantly exploring synergistic opportunities in adjacent industries when they make sense for ERI, our customers and our mission of protecting people, the planet and privacy,” he says. “This brand new, state-of-the-art alkaline recycling plant checks all those boxes, and we couldn’t be more excited to be launching the first of what will be many alkaline recycling plants right at our flagship facility in Indiana.”
He says the new proprietary technology allows ERI to recycle millions of pounds of alkaline batteries in-house, a much greater capacity than it could handle previously.
ERI chose its Indiana location for its first plant for numerous reasons.
“First, it is geographically located centrally in the country, making it easy for us to handle logistics from customers and other ERI facilities from coast to coast,” Shegerian says. “Second, ERI is already heavily invested in Indiana, having one of our largest facilities in Indiana and one of our largest internal labor sources in Indiana. In addition, ERI has tremendous partners in Indiana, making it an easy decision to put our first alkaline plant here.”
The Indiana plant is the first of many alkaline battery recycling plants the company plans to open throughout the U.S. in 2025 and beyond.
“As we expand our alkaline recycling footprint, we will continue to utilize similar technology to what is now running at our Indiana facility,” Shegerian says of the other planned facilities.
He continues, “We are constantly evaluating where to open new facilities based on customer demand, shipping lanes and a variety of other factors to ensure we remain the leading brand in our space and continue to service all our customers in the areas they need us most.”
ERI accepts all types of alkaline batteries for recycling at its eight recycling locations in Arizona, California, Indiana, Massachusetts, New Jersey, North Carolina, Texas and Washington.
The company has long handled a variety of battery types, including alkaline and lithium-ion.
“We are proud and excited to take this latest significant step in the evolution of ERI and the services we provide our customers and the public at large,” Shegerian says in a news release announcing the facility’s opening. “Our innovative alkaline battery recycling process produces zero waste products, is circular-economy-focused and yields clean commodity outputs, creating a truly circular ecosystem. This is a natural progression for us to be able to offer a complementary service to ERI’s existing suite of e-waste, end-of-life and asset management services.”
Through many of its existing electronic recycling downstream processors and partnerships, Shegerian says ERI can handle the raw commodities generated through alkaline battery recycling.
“It’s genuinely rewarding to be able to help so many people and businesses do the right thing by conveniently and responsibly recycling their alkaline batteries and keeping toxins out of landfills,” he adds.
In Memoriam: Antonio ‘Tito’ Giampaolo

Vescio Funeral Home
Antonio “Tito” Giampaolo died July 29 at the age of 68.
Giampaolo served as vice chair of the Giampaolo Group of Cos., which includes recycled metals processing company Triple M Metal, headquartered in Brampton, Ontario; aluminum billet producer Matalco Inc., headquartered in Brampton; information technology asset disposition firm Quantum Lifecycle Partners, headquartered in Toronto; steel distribution center operator Venture Steel in Toronto; and Giampaolo Investments Ltd., which engages in financing, asset management and property management aspects that affect the Giampaolo Group.
He leaves his wife, Joanne; children, Nick (Alicia), Stefanie (Mike) and Alessandro; grandchildren, Marc-Anthony, Violet, Theo, Sebastian, Milo and Isabella; his brother and business partner Michele (Rosa); his sisters, Antonietta (Tony), Ines (Vittorio) and Marilena (Antonio); his brother-in-law Elio (Diane); and sister-in-law, Angela (Mario).
Donations in his memory can be made to The Giampaolo Foundation.
Legislation & Regulations
Oregon DEQ rejects first draft PRO plan
The Oregon Department of Environmental Quality has rejected the first draft of the producer responsibility organization (PRO) program plan submitted March 31 by the Circular Action Alliance under the Oregon Recycling Modernization Act (RMA). The plan outlines how CAA intends to administer Oregon’s extended producer responsibility program for packaging, paper products and food service ware.
The DEQ has requested CAA submit a revised plan to the agency on or before Sept. 27. The PRO program is set to launch July 1, 2025.
In its initially proposed plan, CAA outlines an approach to implementing the RMA that builds on the existing system by upgrading facilities and improving public participation, understanding and equity throughout the state’s recycling system. With this approach, CAA seeks to increase the diversion of recyclables from disposal and reduce the negative environmental, social and health impacts from the end-of-life management of products and packaging.
In its decision letter dated July 29 to CAA Chair Charles Schwarze, the DEQ says it appreciates the “constructive tone of the plan, its ease of navigability and the considerable knowledge of Oregon’s program requirements that it reflects.”
While the DEQ reviewed and approved 18 of the 36 sections of the plan individually, overall plan approval is contingent upon DEQ’s approval of all sections. The agency conditionally approved four sections and rejected 14.
The sections with conditional approval pertain to PRO description and qualifications, depot collection targets, education, outreach and material categorization for the producer fee schedule. If CAA revises the content to align with DEQ’s conditions, these sections will be considered approved upon resubmission. However, substantial changes to conditionally approved sections that do not align with the DEQ conditions of approval would initiate another full review.
For the 14 sections that were not approved, CAA must revise the content, incorporating feedback from DEQ, the Recycling Council and the public. The group then has two more opportunities to seek approval.
CAA tells Recycling Today: “DEQ’s response was an expected step in the Oregon program plan approval process. Due to the potential need for coordination among multiple prospective [PROs] earlier this year, CAA could only begin outreach to gather more information on system costs after the initial program plan was submitted in March. CAA launched the Oregon System Optimization Project in May and will extend this project through the fall to ensure we have the information required for the submission of the final program plan.”
Metals, Mergers & Acquisitions
Alter acquires Andersen’s Sales and Salvage
Alter Trading Corp., headquartered in St. Louis, has purchased substantially all the operating assets of Andersen’s Sales and Salvage Inc., headquartered in Greeley, Colorado, and its affiliates.
The purchase, which closed Aug. 2, adds the Greeley location, home to an automobile shredder, two other Colorado yards in Atwood and Windsor and a location in Cheyenne, Wyoming, expanding Alter’s geographic reach. Alter now operates more than 75 facilities and 19 auto shredders.
“We are very excited to place our business and history in the Colorado and Wyoming communities in the hands of our friends at Alter Trading and are comfortable knowing that Alter, like Andersen’s, will support the communities that have enabled our family business to flourish,” Andersen’s says.
The acquisition plays a key role in Alter’s continuing plan to be the first-choice provider of raw material to the largest steel-producing regions in the U.S., according to Alter, which also notes the companies share similar cultures.
Alter intends to continue operating all three of Andersen’s existing locations, emulating its focus on safety, customer service and quality.
“The Andersen family will be a tough act to follow,” Alter President and CEO Jack Grundfest says. “The company and its current leadership team, led by Dean Andersen and his daughter, Sarah Willcutts, are held in high regard in the industry and have built a remarkable company. We are excited that Dean and Sarah will remain with Alter.”
Acquisitions have played a significant role in Alter’s growth strategy.
From 1998 through February 2019, the company added 55 locations, primarily by purchasing existing family-owned scrap companies. Since early 2019, Alter has continued to expand using this strategy, adding yards previously owned by Schneider’s Iron & Metal Inc., headquartered in Kingsford, Michigan, and consolidating yards it purchased from A. Miller & Co. and Allied Iron & Steel of Peoria, Illinois, which were owned by the same parent company, into its existing sites in the city.
In February of this year, Alter purchased the operating assets of Martin Bros. Recycling, based in Mississippi, adding an auto shredding and nonferrous processing facility in Sardis and three full-service recycling centers in Clarksdale, Byhalia and Nesbit.
Plastics
PureCycle updates on progress at Ohio facility
PureCycle Technologies Inc. has provided an update for the second quarter of fiscal year 2024, detailing operations at its facility in Ironton, Ohio, as well as the identification of new markets for its recycled resin.
The Orlando, Florida-based company says it spent a significant portion of the second quarter making improvements to its Ironton plant, noting the upgrades led to greater reliability during the production runs from late May through June with feedstocks low in coproduct 2 (CP2). During that time, the company says the facility had multiple days with more than 100,000 pounds of pellets produced.
When it transitioned to a feedstock with higher levels of CP2 in late June and July, PureCycle says the rates were limited principally by reliability issues and the CP2 recovery and handling system.
The company reports that upgrades to the front end of the CP2 removal system made in April are working as designed, adding that material removed from the system now is consistent in form and density. The current primary limiting factor is reducing the size of the end product so it can be removed through an automated process. The company has begun implementing adjustments to the recovery and handling system and believes once this limitation is removed, production rates should improve.
“Our team made foundational progress in the second quarter in terms of production, improving our reliability and with higher levels of ... CP2,” PureCycle CEO Dustin Olson says. “All of this has provided a further understanding of how the plant behaves at higher rates. The many improvements made at the Ironton facility during the planned outage in April resulted in our highest production month in June. We understand there is more work to be done, but we have taken significant steps forward.”
In the meantime, PureCycle is continuing to pursue higher throughput by purchasing feedstock low in CP2 and sorting feedstocks for higher-quality material. The company already has installed one optical flake sorting line that helps reduce the CP2 in the feed and expects to have an additional larger flake sorting line installed by the end of September. The combined output of the two lines is expected to be more than 4 million pounds per month.
Additionally, production during the second quarter provided PureCycle the opportunity to introduce its recycled resin to more markets. Compounding PureCycle resin with postindustrial recycled material or virgin polypropylene provides a more consistent product, should simplify the customer-approval process and is expected to increase PureCycle’s ability to bring higher levels of recycled-content product to the market, according to the company.
Municipal/IC&I, Mergers & Acquisitions
Cards acquires 2 businesses in Oklahoma

“We are thrilled to welcome Harrah Disposal and Stacy’s Trash Service customers and employees to the Cards family,” Cards CEO Dan Christensen says. “These acquisitions are a testament to our ongoing efforts to expand and enhance our service offerings. By introducing new lines of business to these markets and opening our new MRF in Springdale, we are poised to deliver even greater value to our customers while supporting environmental sustainability.”
Cards Holdings LLC, headquartered in Springdale, Arkansas, has acquired two Oklahoma-based companies: Harrah Disposal in Harrah and Stacy’s Trash Service in Tahlequah. These purchases are the seventh and eighth for Cards this year and expand the company’s services in central and eastern Oklahoma, bringing approximately 5,000 new customers into the company’s service network.
The Harrah Disposal and Stacy’s Trash Service purchases introduce new residential and commercial service offerings for Cards in the Muskogee and Oklahoma City markets.
Cards Oklahoma City now offers municipal curbside, residential subscription and commercial front-load services to customers, while in the Muskogee and Tahlequah markets, the company will expand to include municipal curbside and residential subscription services.
Cards says it is proud to bring its fleets in these newly acquired areas 3rd Eye technology from Dover’s Environmental Solutions Group, which enhances the safety and efficiency of the company’s operations, providing valuable data and insights to better serve customers.
Additionally, Cards will open a new material recovery facility (MRF) in Springdale Sept. 9 that the company says will enhance its ability to process and recycle materials efficiently, contributing to a more sustainable and environmentally friendly waste management system.
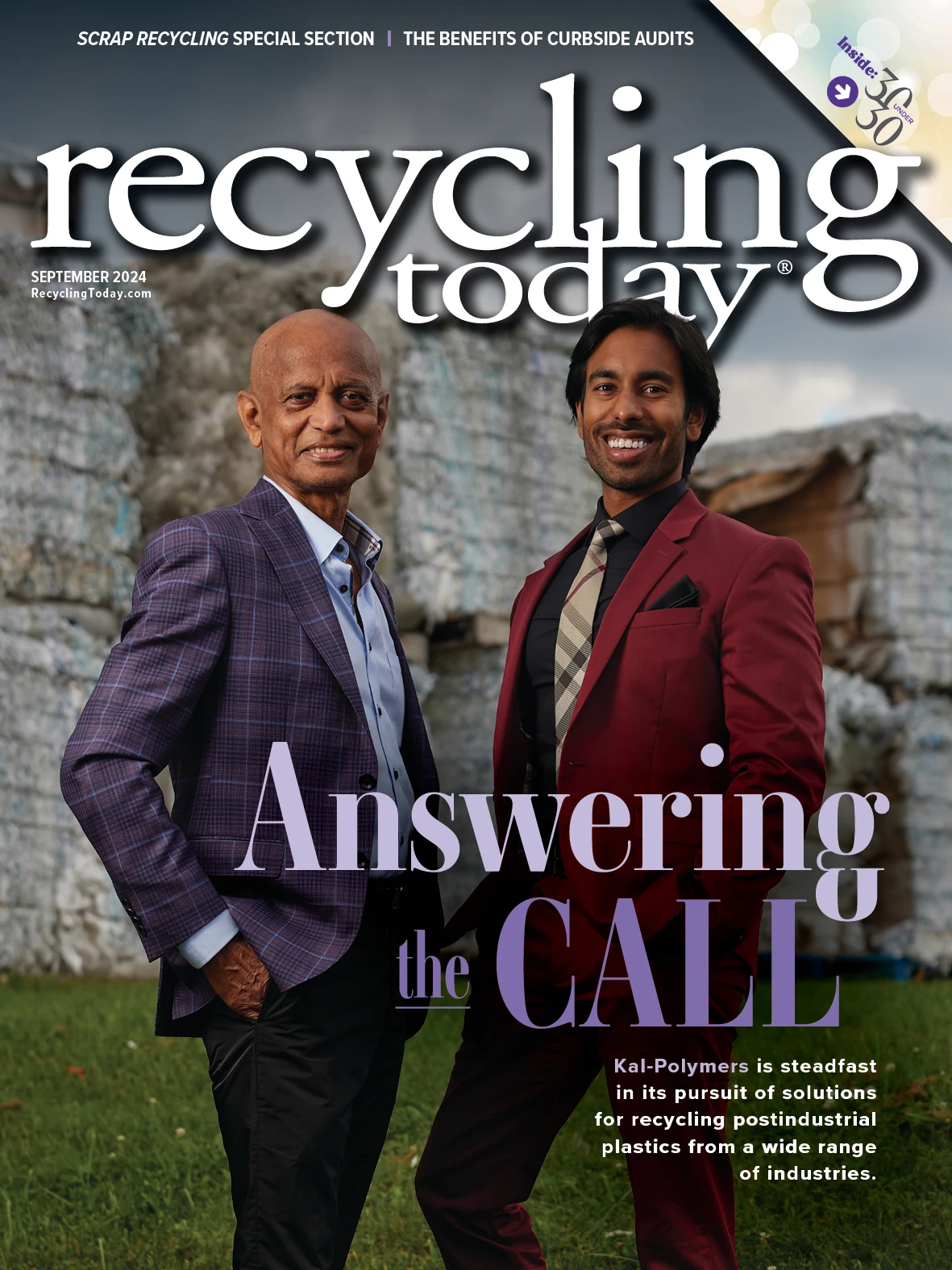
Explore the September 2024 Issue
Check out more from this issue and find your next story to read.
Latest from Recycling Today
- Steelmakers await impact of tariff policy
- Radius loses money, says merger on track
- Electrostatic technology vies for role in ASR sorting
- ReMA board to consider changes to residential dual-, single-stream MRF specifications
- Trump’s ‘liberation day’ results in retaliatory tariffs
- Commentary: Waste, CPG industries must lean into data to make sustainable packaging a reality
- DPI acquires Concept Plastics Co.
- Stadler develops second Republic Services Polymer Center