
Metals
Wieland purchases Aurubis site in Buffalo, New York
Aurubis AG has sold its Buffalo, New York, flat-rolled products production site to the Wieland Group, headquartered in Ulm, Germany. The sale closed Aug. 30, with both parties agreeing to keep the sale price confidential.
The sale enables fellow German company Aurubis to further its concentration on primary copper production, recycling and the multimetal portfolio of its smelter network, the company says, and is the most recent in a number of transactions to reduce the scope and complexity of its flat-rolled product area.
In mid-2022, Aurubis sold production sites in Zutphen, Netherlands, as well as slitting centers in Birmingham, U.K.; Dolný Kubín, Slovakia; and Mortara, Italy, which had a total of about 360 employees, to Germany-based KME SE.
In June 2022, Aurubis began building a new production site in Augusta, Georgia, that is focused on processing complex recyclables as part of its growth strategy. In 2019, the company also bought the former Metallo Group, a recycling specialist, integrating that company’s operations into the group.
The former Aurubis Buffalo Inc., with about 500 employees, produces copper and copper alloy strip and sheets that are used to manufacture a wide range of product lines, including electrical products, electronic connectors, heat exchangers and architectural products. The site supplies a number of customers, primarily in the U.S. According to the company, Aurubis Buffalo’s production and business activities largely were independent of the Aurubis Group in relation to the growing recycling business at the Georgia site and the Aurubis sites in Europe.
Wieland says the purchase of the flat-rolled products production site is consistent with its strategy to strengthen its North American footprint and expand capabilities and capacities for semifinished products. In combination with the modernization project underway at Wieland’s rolled products facility in East Alton, Illinois, and the commissioning of Wieland’s recycling center in Shelbyville, Kentucky, Wieland serves its U.S. customer base and enables closed-loop supply chain opportunities and the highest recycled-content products.
Metals, International
Aurubis opens recycling plant in Belgium

Bart Craane and Aurubis’ Dirk Vandenberghe
Aurubis opened its ASPA, or Advanced Sludge Processing by Aurubis, plant at its site in Beerse, Belgium, in early September.
The company broke ground on the addition in late 2022.
A hydrometallurgical process that was developed in-house, Aurubis COO of Multimetal Recycling Inge Hofkens said the plant “is another prime example of Aurubis’ innovative strength.”
“We are pioneering sustainable multimetal production and are now taking recycling to the next level,” she said.
The ASPA facility will process anode sludge, an intermediate product from electrolytic copper refining produced at the Aurubis recycling sites in Beerse and in Lünen, Germany. The new process delivers faster extraction of more precious metals as well as the full recovery of tin from the anode sludge, according to the company.
With this investment of roughly 33 million euros (more than $36 million), the company says it is committing to further developing Aurubis Beerse and to connecting the European sites even more strongly.
Aurubis’ plant in Beerse processes more than 200,000 tons of multimetal scrap annually, ranging from complex residues to higher-grade scrap types, producing metals, metal products and minerals.
“I am proud to be opening the new ASPA facility today; it is a true achievement for the Aurubis Beerse team after years of dedication,” Managing Director of Aurubis Beerse Dirk Vandenberghe said Sept. 4. “The successful startup of ASPA directly results from the expertise and metallurgical know-how but also from team spirit and a profound commitment to the circular economy.”
Hofkens added, “Metal recycling is a growth area for Aurubis, and Aurubis is increasingly distinguishing itself as an essential cornerstone in the European circular economy.”

Paper
White Birch Paper starts up recycled paper machine at Quebec mill
White Birch Paper, a Greenwich, Connecticut-based paper and packaging company, has entered the recycled kraft paper market with the startup of a new paper machine at its Stadacona Mill in Quebec City, Quebec.
The machine is expected to produce 120,000 metric tons per year of 100 percent-recycled kraft paper in a variety of basis weights aimed at serving the e-commerce mailers, packaging medium, retail counter markets and other packaging applications.
White Birch’s recycled kraft paper is made exclusively using postconsumer recycled material via “proprietary techniques” that the company says offer “exceptional” burst and tear strength as well as affordability and eco-friendliness.
“We believe in creating products that are not only functional but also environmentally responsible,” the company says on its website. “By choosing recycled kraft paper, you’re contributing to a greener future and supporting a company that values sustainability.”
The Stadacona Mill produces newsprint, commercial paper, paperboard and now recycled kraft paper, with a combined annual production capacity of more than 250,000 metric tons. It originally was built in 1927 and purchased by White Birch in 2004.
The site also runs a paperboard machine that produces 45,000 metric tons per year of 100 percent-recycled chipboard as well as specialty paperboard products.
White Birch has two other mills in Quebec—the F.F. Soucy Mill that produces newsprint and specialty papers and the Papier Masson Mill that produces approximately 240,000 tons of newsprint annually.

Plastics, Mergers & Acquisitions
GDB acquires former Myplas USA plastics recycling plant in Minnesota
New Jersey-based GDB International Inc., through its subsidiary GDB Circular Inc., is reopening the former Myplas USA plastic film recycling plant in Rogers, Minnesota.
Myplas USA, the U.S. subsidiary of South Africa’s Myplas, opened the 170,000-square-footsite in late 2023.
The original facility was designed to recycle nearly 90 million pounds of end-of-life plastic per year, and Myplas founded it in collaboration with leading global businesses to catalyze a regional circular economy in the Upper Midwest for flexible film and packaging materials. It originally was funded by a $13 million joint equity investment by General Mills, Schwan’s Co. and Chicago-based film manufacturer Charter Next Generation, along with supporting investors Target and Ecolab.
The Alliance to End Plastic Waste (AEPW), Closed Loop Partners and the Minnesota Department of Employment and Economic Development provided financial support to the facility.
However, according a report from The Minnesota Star Tribune, citing a lawsuit filed in April, Myplas USA had not paid rent on the facility since the start of this year and owed more than $389,000. An electrical contractor also filed an $895,000 lien for unpaid bills in March of this year.
Following the grand opening of the $30 million recycling plant in December, Myplas furloughed staff and shut down machinery earlier this year.
However, under its new ownership and backed by continued commitments across multiple stakeholders to strengthen plastics recycling infrastructure in the U.S., the Rogers facility now has an experienced management team with a deep understanding of recycling technology. It also will be adding new technology to increase the efficiency of materials recovery.
GDB International, established in 1993, operates a network of plastic recycling facilities across Wisconsin, Ohio, Tennessee and Florida that includes processing facilities in New Brunswick and Mount Holly, New Jersey.

Metals
Ecovery commissions new furnace at aluminum processing site in Alabama
Metal recycling firm Ecovery LLC has commissioned a 60,000-pound-capacity secondary aluminum furnace at its processing facility in Loxley, Alabama.
The unit is its second on-site rotary furnace and marks the company’s second major capital expenditure project in 2024. Earlier this year, Ecovery installed an X-ray sorting line designed to supply furnace-ready aluminum shred to rolling mills in the Southeast and Midwest.
Ecovery, which is based in Loxley, says its new furnace will allow it to increase its melting capacity while also expanding the dross processing and toll conversion services it can offer its customers.
Ecovery CEO Brock Norris says the family-owned and -operated business, located near Mobile, Alabama, has diversified and expanded several times in its 16-year history.
Originally incorporated to process electronic scrap, Ecovery pivoted to nonferrous scrap and now specializes in the shredding, granulation, separation, X-ray sorting and melting of aluminum and copper-bearing scrap, providing products to mills throughout the U.S., Europe and Asia.
Ecovery describes itself as one of the largest consumers and processors of copper-aluminum radiators in the country and operates other processing equipment.
Plastics
APR updates position, recyclability category for degradable additives

of Plastic Recyclers
The Association of Plastic Recyclers (APR) has released updates to the recyclability category and formal position for degradable additives, nutrients and supplements. Based on the organization’s definition of “recyclable,” they are now included in the category of “renders the package nonrecyclable” in its APR Design Guide for Plastics Recyclability.
According to the APR Design Guide, a design feature renders a package nonrecyclable if most material recovery facilities (MRFs) or reclaimers cannot remove such features to the degree required to generate a marketable end product.
The organization says a package including degradable additives, nutrients or supplements cannot be detected using commercially available technologies and will affect both the quality and yield of postconsumer resin (PCR) when they perform as designed. An item, package or film containing any of these design features renders the entire item, package or film nonrecyclable.
“This change in categorization is based on research and reports published by independent research groups and better aligns APR with other NGOs [nongovernmental organizations] in the recycling and circularity space, as well as international manufacturers and retailers,” APR President and CEO Steve Alexander says. “This update clearly reflects APR’s mission to improve all aspects of the plastics recycling process and protects the quality and yield of the PCR stream.”
The “renders the package nonrecyclable” category includes degradable and biodegradable materials that are not certified compostable, including, but not limited to, bio-assimilating, oxo-degradable, oxo-biodegradable, enzymatic, anaerobic and photodegradable materials used in plastic packaging and film to accelerate degradation.
“The latest updates to the APR Design Guide are a positive move toward global harmonization of recyclability principles,” says Paolo Glerean, chairman of RecyClass. “Aligning recommendations on different packaging features, especially those with negative impact for recycling, is essential for boosting widespread circular innovation of plastic materials.”
Degradable additives could present technical challenges for the mechanical recycling process and future uses of products produced from that process. The APR says it is possible the integrity and/or useful life of plastic packaging or durable products made from recycled resins containing these additives could be compromised.
“We applaud APR’s decision to categorize degradable additives as ‘renders the package nonrecyclable,’” Berry Global Vice President of Sustainability Rob Flores says. “As noted by APR, there is a clear consensus from the broader environmental and packaging communities that degradable additives are expected to negatively affect plastic recycling. At Berry Global, we believe the most effective solution to address plastic waste is to create a circular economy for plastics by designing products for recycling and reuse, incorporating recycled content and investing in recycling and waste management infrastructure.”
APR says encouraging the recycling of containers that include degradable additives could be contrary to the goals of the recycling process for plastics and cautions companies to carefully review the U.S. Federal Trade Commission Green Guides, state laws and European directives when considering whether to label these traditionally recycled containers as both degradable and recyclable.
“As we continue to move toward a circular economy, it’s essential that we carefully consider the impact of all packaging materials on the recycling process,” U.S. Plastics Pact CEO Jonathan Quinn says. “APR’s updated position on degradable additives is aligned with the U.S. Plastics Pact’s Problematic and Unnecessary Materials List and offers important guidance to help ensure the quality of recycled plastics. We support efforts that bring clarity to the recyclability of materials, helping to inform decisions that benefit both the industry and the environment.”
Municipal/IC&I
Texas Disposal opens mini MRF inside Austin stadium

Texas Disposal Systems
Texas Disposal Systems (TDS), an Austin, Texas-based solid waste collection, processing and disposal company, has opened a custom material recovery facility (MRF) inside Q2 Stadium in Austin, home to Austin FC, the city’s Major League Soccer (MLS) team.
As part of the team’s ongoing commitment to making Q2 Stadium the “greenest stadium in all of MLS,” TDS created a custom sorting system that meets the stadium’s needs. All materials discarded throughout Q2 Stadium are being processed and sorted into recycling, compost and waste streams through the mini MRF.
The mini MRF has the capability to process about 1.5 tons per hour of materials such as glass, food waste, cardboard, paper products, aluminum cans, plastic bottles and more.
“The Austin FC fans are fantastic and do a great job at keeping materials in the right container; however, to truly maximize recovery of organics and recyclables, it was necessary to create a system that enables Austin FC staff to look at each stream and sort it for quality control,” says Adam Gregory, vice president of TDS and Okapi Environmental Services. “The automated conveyor and compaction system we came up with accomplishes that as efficiently as possible in a small footprint. I commend Austin FC for going the extra mile and working with us to create an innovative solution.”
The company had to develop a compact system to fit inside the stadium service area with very limited space.
Sponsored Content
Still relying on manual sorters?
Let AI do the heavy lifting. Waste Robotics delivers reliable, high-performance robots tailored for complex waste streams. They require minimal maintenance, are easy to operate, and are designed to boost your recovery rates. Smarter sorting starts with the right partner. Waste Expo Booth #1969 & REMA #2843
Click here to see our robots in action!Sponsored Content
Still relying on manual sorters?
Let AI do the heavy lifting. Waste Robotics delivers reliable, high-performance robots tailored for complex waste streams. They require minimal maintenance, are easy to operate, and are designed to boost your recovery rates. Smarter sorting starts with the right partner. Waste Expo Booth #1969 & REMA #2843
Click here to see our robots in action!Sponsored Content
Still relying on manual sorters?
Let AI do the heavy lifting. Waste Robotics delivers reliable, high-performance robots tailored for complex waste streams. They require minimal maintenance, are easy to operate, and are designed to boost your recovery rates. Smarter sorting starts with the right partner. Waste Expo Booth #1969 & REMA #2843
Click here to see our robots in action!Sponsored Content
Still relying on manual sorters?
Let AI do the heavy lifting. Waste Robotics delivers reliable, high-performance robots tailored for complex waste streams. They require minimal maintenance, are easy to operate, and are designed to boost your recovery rates. Smarter sorting starts with the right partner. Waste Expo Booth #1969 & REMA #2843
Click here to see our robots in action!Sponsored Content
Still relying on manual sorters?
Let AI do the heavy lifting. Waste Robotics delivers reliable, high-performance robots tailored for complex waste streams. They require minimal maintenance, are easy to operate, and are designed to boost your recovery rates. Smarter sorting starts with the right partner. Waste Expo Booth #1969 & REMA #2843
Click here to see our robots in action!“As Austin FC’s official waste and recycling partner, TDS has been the biggest help I could possibly imagine, not just with this project but since the existence of our stadium and our club. Their team has helped us form our zero-waste goals [and] develop our Eco Stations and our hauling systems,” says Nick Otte, Austin FC senior director of stadium operations. “I think this mini MRF project ... is way above and beyond what we could have expected, and it’s going to help us meet our goals.”
TDS played a vital role in helping make Q2 Stadium the first soccer-specific stadium in the world to achieve Total Resource Use and Efficiency precertification. With the new sorting process and equipment in place, Austin FC’s goal is to sustain 90 percent diversion and increase efforts with a goal of achieving zero waste.
Metals
Algoma Steel OK’d for EAF power line
Algoma Steel Group Inc. electricity providers have been authorized to construct a new 230-kilovolt transmission line and related transformation components to serve its under-construction electric arc furnace (EAF) mill in Sault Ste. Marie, Ontario.
Power companies PUC Transmission LP and Hydro One Sault Ste. Marie LP received approval pursuant to the Ontario Energy Board (OEB) Act.
“The combined local transmission project improves the city’s access to Hydro One’s planned regional grid infrastructure upgrade as previously prioritized by the province of Ontario,” Algoma says.
“This milestone marks a significant advancement in enhancing Sault Ste. Marie’s power infrastructure, which is vital for supporting sustainable economic growth and our transformation to electric arc steelmaking—a key part of our commitment to environmental sustainability,” Algoma Steel President and CEO Michael Garcia adds.
Algoma has been involved in a multiyear project this decade to convert its hot steelmaking operations from blast furnace/basic oxygen furnace technology to EAF production. The conversion will allow the company to make higher recycled-content steel.
“This achievement was driven by the combined efforts of PUC Transmission and Hydro One in their applications, as well as Batchewana First Nation and other supporting interveners, and underscores the strong commitment by the province of Ontario to enable investment in critical infrastructure that underpins the economic growth of our city and region,” Algoma Steel says.
The OEB confirmed the transmission project consists of network facilities and that no capital contribution from Algoma is required. Additionally, the OEB determined the transmission rate impacts anticipated from the projects are “reasonable,” the steelmaker says.
“The collaboration between these organizations highlights dedication to ensuring that Sault Ste. Marie has reliable power needed to support both industrial advancement and community prosperity,” Garcia says.
“Algoma Steel is proud to contribute to the sustainable development of Sault Ste. Marie and to support the future of green steel production in Ontario,” he continues. “We remain committed to delivering innovative and responsible steel solutions that benefit both the community and the environment.”
Plastics
Trex makes progress on Arkansas plant

Trex Co., a Winchester, Virginia-based maker of recycled-content composite plastic and wood residue decking and railing, held a “topping out” ceremony at its under-construction manufacturing facility in Little Rock, Arkansas.
The production facility represents an estimated $400 million investment by Trex and has been designed to increase capacity as well as its ability to meet the strong demand for its products.
“We are thrilled to reach this important milestone in the development of our new facility,” Trex President and CEO Bryan H. Fairbanks says. “We continue to experience broad-based demand driven by strong consumer interest in outdoor living. This new campus will enable us to provide our customers with significantly better access to Trex products while strengthening our position for future growth.”
At the ceremony, company executives were joined by Arkansas Gov. Sarah Huckabee Sanders, Arkansas Economic Development Commission Executive Director Clint O’Neal and Little Rock Regional Chamber President and CEO Jay Chesshir, among others.
During the event, the final structural steel beam, signed by project stakeholders, was placed atop the new decking facility, symbolizing what Trex calls “the collaborative effort and dedication of all involved in the project.”
The plant sits on nearly 300 acres of land in the Port of Little Rock district. The facility will be Trex’s third U.S. manufacturing location.
The Little Rock campus will feature buildings dedicated to decking and railing production, plastic film recycling and processing, reclaimed wood storage, warehousing and administrative offices.
Lexington, Kentucky-based Gray Construction is developing the site.
“The facilities will be equipped with state-of-the-art equipment [and] employ proprietary technologies and energy-efficient systems designed to drive optimal output with a focus on sustainability and circularity,” Trex Executive Vice President Adam Zambanini says.
Trex says the Little Rock facility will bring more than 500 jobs to the region. The firm has begun hiring for management roles at the facility, and recruiting for hourly employees will begin soon.
Get curated news on YOUR industry.
Enter your email to receive our newsletters.
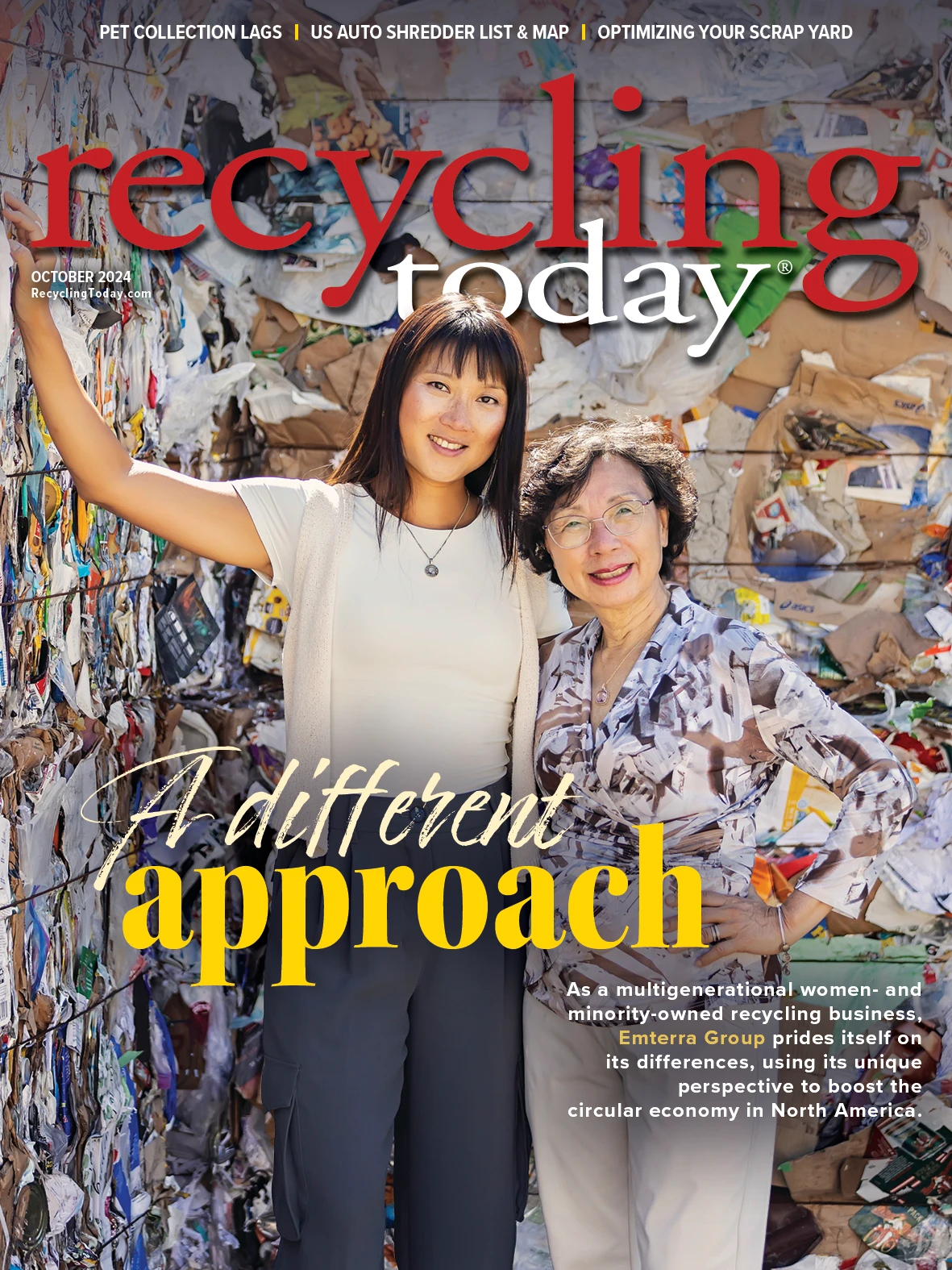
Explore the October 2024 Issue
Check out more from this issue and find your next story to read.
Latest from Recycling Today
- Japanese scrap can feed its EAF sector, study finds
- IRG cancels plans for Pennsylvania PRF
- WIH Resource Group celebrates 20th anniversary
- Ecobat touts commissioning 3 LIB recycling plants in a year
- NWRA: NIOSH cuts a step in the wrong direction
- Novelis announces plant closures
- ABTC reports production increase at LIB recycling facility
- ReMA contributes comments in Commerce Department investigation into copper