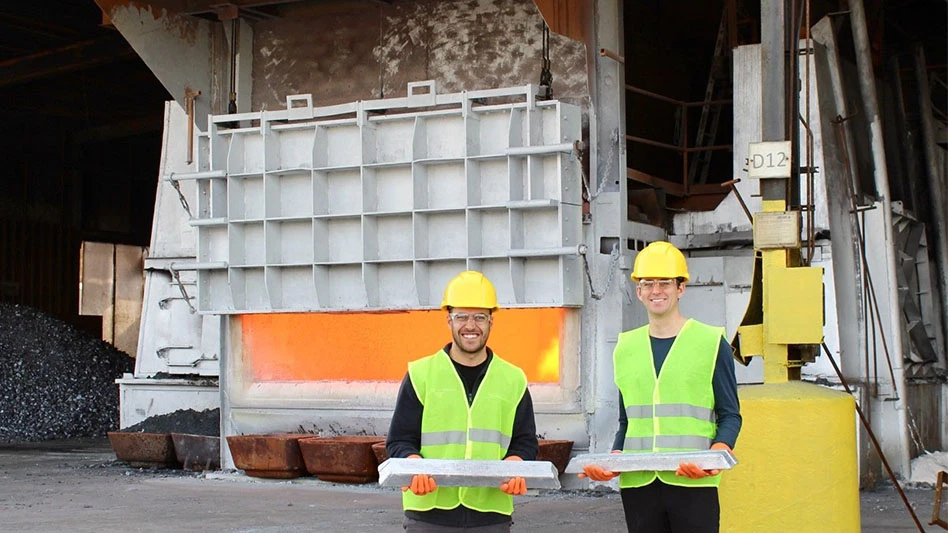
Photo courtesy of Hydrova

Metal
Hydrova technology helps to decarbonize aluminum, cement production
California-based Hydrova, a technology startup that spun out of the Massachusetts Institute of Technology (MIT), and California-based aluminum recycler TST Inc., have produced aluminum ingots using salt and aluminum recovered from dross, generating hydrogen during the recovery process, further enhancing the sustainability of aluminum recycling.
Hydrova was spun out of MIT in 2020. The company’s patent pending separation technology recovers aluminum, salt and oxide products from dross and salt cake while generating hydrogen for clean energy use on-site.
Hydrova says its process diverts 100 percent of waste otherwise destined for landfill while decarbonizing aluminum and cement production.
For more than 75 years, TST has been recycling aluminum to produce alloys for industries around the globe, including aerospace, automotive, appliance, lighting, building products and semiconductors. Hydrova says its technology enables TST to further cement its global sustainability leadership position while valorizing waste streams.
“Aluminum recycling is essential for sustainability,” says Andrew Stein, CEO of TST. “It saves over 95 percent of the energy to recycle aluminum versus creating new primary aluminum. However, the process of melting aluminum scrap creates dross and salt cake that is difficult to recycle without having waste end up in a landfill. [Hydrova’s] technology solves that problem by utilizing 100 percent of this co-product into valuable products.”
“What we are demonstrating with TST today is a circular economy for otherwise landfilled materials,” Hydrova co-founder and CEO Julian Davis says. “TST’s recycling furnaces use aluminum and salt as inputs and produce dross as a waste byproduct. By separating out the aluminum and salt from dross, Hydrova is able to put these materials straight back into the furnaces from which they came, creating a closed loop. And by producing hydrogen, we can provide a clean fuel to help decarbonize those same furnaces.”
The company says the hydrogen comes from its proprietary aluminum-water-reaction method, which occurs during the recycling process. This approach piqued the interest of the U.S. Environmental Protection Agency, which awarded Hydrova a $100,000 grant in December 2022. In addition to other grants from MIT and the 776 Foundation, Hydrova has attracted venture capital investment from firms such as the 1517 Fund and Climate Capital.
Hydrova says it plans to ramp up production at its pilot facility in partnership with TST. It also has built a partnership with Garden Grove, California-based CTS Cement, the inventors of Rapid Set cement. The oxide products Hydrova recovers from dross provide a high-quality source of aluminum oxide, a major ingredient of Rapid Set cement.
“Our goal is to prevent millions of tons of aluminum recycling waste from going to landfill every year,” Davis says. “To accomplish this, the economic incentive must be clear, and that is why our focus is on turning this waste into high-quality, low-carbon products like TST’s alloys, hydrogen and Rapid Set cement. This unlocks a new opportunity for sustainability to be achieved profitably.”
Plastic
The Recycling Partnership awards first PET Recycling Coalition grants
The Recycling Partnership (TRP) has awarded three grants to increase polyethylene terephthalate (PET) capture to two PET reclaimers and a material recovery facility (MRF) through its PET Recycling Coalition.
According to the Washington-based TRP, the initial round of grants will result in more than 2.5 million pounds per year of new PET captured and 50 million pounds per year of new reclamation capacity. Additionally, access to thermoform recycling will be provided in the Pittsburgh metropolitan area.
The exact amount of each grant was not disclosed.
“These projects will deliver the types of improvements that we view as being essential to the future of PET recycling,” says Adam Gendell, director of system optimization at TRP. “By helping MRFs and PET reclaimers capture and recover more of the material in their facilities, we will see meaningful gains in the amount of PET recycled in the short term, and by helping to grow reclamation capacity, we will ensure there is robust infrastructure ready to handle future growth in PET recycling.”
Dak Americas LLC, a Charlotte, North Carolina-based integrated PET resin producer, has received a grant to help with the implementation of a new robotic sorter at its PET reclamation facility in Richmond, Indiana. The sorter will be installed on one of the facility’s outbound lines, capturing PET bottles, thermoforms, pigmented opaque PET items that previously were commingled with undesired non-PET plastics and other byproducts, allowing the facility to improve efficiency and produce more recycled content.
The company previously invested $32 million to expand its Richmond plant in 2020 with help from a $140,000 Economic Development Income Tax grant to use toward equipment and machinery, building construction, adjacent land and employee training.
Direct Pack Recycling, an Azusa, California-based PET reclaimer and packaging company, received a grant to assist in the construction of a new PET reclamation operation in Mexicali, Mexico, which will source material from MRFs across the U.S. and produce a significant amount of recycled content for new packaging.
Dak Americas and Direct Pack Recycling specialize in recycling pigmented and opaque PET, and TRP says the grants enable both facilities to grow and improve their recycling of the entirety of the PET stream.
Direct Pack Recycling also specializes in recycling thermoformed PET packaging, including cups, clamshells and trays, and has the capacity to recycle 20,000 tons of PET per year. The company says it has recycled more than 74.4 million pounds of plastics since 2020 and repurposed the material back into new packaging.
Finally, Pittsburgh-based Recycle Source has received a grant to upgrade automated sorting technology at its MRF in Pittsburgh, increasing the efficiency of PET capture and, TRP says, resulting in a significant increase in the overall amount of PET the MRF delivers to reclaimers. The new technology also will improve the MRF’s ability to detect and sort thermoforms.
“We are pleased that these projects address the entirety of the PET recycling stream—bottles, thermoforms and pigmented and opaque PET—and we’re excited to build on these early successes with our next round of granted projects,” Gendell says.
The PET Recycling Coalition was launched in June 2022 and looks to improve PET circularity and transform the recycling system by increasing capture rates through improved efficiency, technology, infrastructure and access. Through its grant program, the coalition says it envisions a thriving PET recycling system that captures significantly more material, improving PET packaging circularity.
The National Association for PET Container Resources (NAPCOR) reported in December 2022 that the U.S. recycling rate for postconsumer PET increased to 28.6 percent in 2021, up from 27.1 percent in 2020, and the North American rate increased to 36.8 percent, up from 34.2 percent in 2020. 2021 saw a number of first-time achievements in PET recovery, with PET bottle collection in the U.S. exceeding 1.9 billion pounds and thermoforms collected for recycling in the U.S. and Canada reaching a record-setting 142 million pounds.
The coalition’s goals to further these achievements include increasing capture by 250 million pounds per year by 2027, increasing the PET bottle recycling rate to more than 30 percent, achieving more than 60 percent access for PET thermoforms by 2025 and creating “resilient recycling in proactive and at scale” for pigmented and opaque PET by 2025.

Metal, Financial
US Steel profits narrow in 2022
United States Steel Corp. closed 2022 with net earnings of $226 million in the fourth quarter. While remaining profitable, the Pittsburgh-based steelmaker’s quarterly net earnings fell by 84 percent compared with $1.43 billion in net earnings in the final quarter of 2021.
U.S. Steel cleared $2.52 billion in net earnings in 2022. That also represents a decrease of 39.5 percent compared with 2021, when the steel producer netted $4.17 billion.
The firm points to several one-time conditions or charges affecting its 2022 earnings, including the impact of asset impairments related to the permanent idling of the iron-making process at the company’s Great Lakes Works, near Detroit, and the impact of a one-time signing bonus related to the United Steelworkers labor agreement.
U.S. Steel President and CEO David Burritt says the fourth-quarter results exceeded guidance expectations thanks to domestic steelmaking, electric arc furnace (EAF) operations and the Tubular segment, which generated positive earnings before interest, taxes, depreciation and amortization in December in the Mini Mill segment. He adds that the company is set up well for 2023.
“Our record cash and liquidity support a balanced capital allocation approach,” Burritt says. “We returned approximately $900 million to stockholders in 2022 and plan to continue rewarding stockholders in 2023 while investing in the business. We are already delivering on strategic commitments, including the Gary Works pig iron machine that was commissioned ahead of schedule and on budget. Later this year, our nongrain-oriented electrical steel line at Big River Steel [an EAF mill in Arkansas] will begin producing advanced steel grades to meet the growing electric vehicle demand.”

Metal, Financial
Acerinox to increase North American Stainless capacity
Spain-based metals producer Acerinox has announced it intends to increase production capacity at its North American Stainless (NAS) mill in Ghent, Kentucky, by 200,000 metric tons per year, representing a 20 percent boost.
The mill is one of the largest consumers of stainless steel scrap in North America. A statement from NAS says its melt shop products contained an average of 82 percent recycled content in 2021. Considering an acknowledged melt shop capacity of 1 million metric tons, that means the facility could absorb some 800,000 metric tons of scrap annually in a high-volume year.
Regarding the planned expansion, NAS puts the price tag at $244 million and says it will include a new cold rolling mill, an upgrade to its annealing and pickling lines and enlarging the melt shop to include a 400-metric-ton crane, “among other equipment.”
“This is a strategic decision with which Acerinox will increase its positioning in the United States to accompany the expected growth in the American market,” Acerinox CEO Bernardo Velázquez says, adding that the decision “reinforces our leadership in the American market and our commitment to this factory, one of the most efficient in the world. We are proud to produce in NAS about 50 percent of the country’s stainless steel.”
Acerinox and Kentucky Gov. Andy Beshear announced the investment at a joint news conference in late January. Beshear said, “I am pleased to announce further growth in Kentucky’s steel industry with this latest investment by North American Stainless. I look forward to strengthening this collaboration in the years ahead.”
NAS CEO Cristobal Fuentes says, “We are proud to spearhead the stainless steel sector in the U.S., support national security of supply with our production and create quality jobs in our region.”

Safety, Legislation & Regulations
Dept. of Labor announces safety enforcement guidance changes
The U.S. Department of Labor says its Occupational Safety and Health Administration (OSHA) has issued new enforcement guidance to make its penalties more effective in stopping employers from repeatedly exposing workers to life-threatening hazards or failing to comply with certain workplace safety and health requirements.
OSHA regional administrators and area office directors now have the authority to cite certain types of violations as instance-by-instance citations for cases where the agency identifies “high-gravity” serious violations of OSHA standards specific to certain conditions where the language of the rule supports a citation for each instance of noncompliance. These conditions include lockout/tagout, machine guarding, permit-required confined space, respiratory protection, falls, trenching and for cases with other-than-serious violations specific to recordkeeping.
The Department of Labor says the change ensures OSHA personnel apply the full authority of the Occupational Safety and Health Act, where increased citations are needed to discourage noncompliance. The new guidance covers enforcement activity in general industry as well as in the agriculture, maritime and construction industries.
The Department of Labor says the new guidelines are effective 60 days from Jan. 26.
In a second action, OSHA is reminding its regional administrators and area directors of their authority not to group violations and instead to cite them separately to more effectively encourage employers to comply with the intent of the Occupational Safety and Health Act.
“Smart, impactful enforcement means using all the tools available to us when an employer ‘doesn’t get it’ and will respond to only additional deterrence in the form of increased citations and penalties,” Assistant Secretary for Occupational Safety and Health Doug Parker says. “This is intended to be a targeted strategy for those employers who repeatedly choose to put profits before their employees’ safety, health and well-being,” he says of the change. “Employers who callously view injured or sickened workers simply as a cost of doing business will face more serious consequences.”

Explore the March 2023 Issue
Check out more from this issue and find your next story to read.
Latest from Recycling Today
- Enviri names new president of Harsco Environmental business
- Survey outlines ‘monumental challenge’ of plastic packaging collection in UK
- Nippon Steel acknowledges delay in US Steel acquisition attempt
- BASF collaborates to study mechanical plastic recycling
- Commentary: navigating shipping regulations for end-of-life and damaged batteries
- Haber raises $44M to expand to North America
- Canada Plastics Pact releases 2023-24 Impact Report
- Reconomy brands receive platinum ratings from EcoVadis