
Plastics, Legislation & Regulations
Latest Global Plastics Treaty talks yield progress, frustration
The fourth session of the United Nations Environment Program’s (UNEP’s) Intergovernmental Negotiating Committee to develop a Global Plastics Treaty, also called INC-4, concluded April 30 after a week of negotiations in Ottawa with an advanced draft text of the treaty and an agreement on intersessional work that will take place before the fifth session, INC-5, in November in Busan, South Korea.
More than 2,500 delegates participated in INC-4, representing 170 members and more than 480 observer organizations, including nongovernmental organizations (NGOs), intergovernmental organizations and UN entities—the largest gathering to date, with observer participation increasing by approximately 50 percent.
Delegates negotiated the revised the draft text of what is intended to be an international, legally binding instrument and discussed a range of topics that included emissions and releases, production, product design, waste management, problematic and avoidable plastics, financing and a just transition.Intersessional work will focus on the financial mechanism of the treaty, plastic production, chemicals of concern in plastic products and product design reusability and recyclability. Member states will include observers’ participation during this work. Also, members have decided to create an open-ended legal drafting group in time for INC-5 that will serve in an advisory capacity by reviewing elements of the revised draft text to ensure legal soundness.
“We came to Ottawa to advance the text and with the hope that members would agree on the intersessional work required to make even greater progress ahead of INC-5,” UNEP Executive Director Inger Andersen says. “We leave Ottawa having achieved both goals and a clear path to landing an ambitious deal in Busan ahead of us.”
However, there was frustration amid the progress. Two points of contention among members—whether the treaty will have common or voluntary global rules and whether it will include measures to reduce production and consumption of plastics—were left undecided, and neither topic has been included in intersessional plans.
In a statement from the Center for International Environmental Law (CIEL), the Washington-based group claims nearly 200 fossil fuel and chemical industry lobbyists registered for the talks, including at least 16 on country delegations. CIEL says INC-4 failed to sufficiently advance the plastics treaty ahead of the final talks and instead led to many countries accepting “a compromise that played into the hands of petrostates and industry influences.”
“From the beginning of negotiations, we have known that we need to cut plastic production to adopt a treaty that lives up to the promise envisioned in UNEA [UN Environment Assembly] two years ago,” CIEL Director of Environmental Health David Azoulay says. “In Ottawa, we saw many countries rightly assert that it is important for the treaty to address production of primary plastic polymers. But when the time came to go beyond issuing empty declarations and fight for work to support the development of an effective intersessional program, we saw the same developed member states who claim to be leading the world towards a world free from plastic pollution abandon all pretense as soon as the biggest polluters look sideways at them.”
At the conclusion of treaty talks, NGO Break Free From Plastic released its analysis, saying that while the draft text has been somewhat streamlined, more additions than deletions were made, “leading to a text riddled with a large number of options and bracketed words and sentences.”
Questions also were left unanswered for those promoting a circular economy for plastics. Virginia Janssens, managing director of trade association Plastics Europe, says while her organization is encouraged by the number of proposals addressing how best to define and avoid problematic and high-leakage plastic applications, as well as discussions of financing and the potential for global extended producer responsibility programs, concern about the lack of progress and a regulatory framework required to accelerate the development of a circular plastics economy remains.
Patrick Krieger, vice president of sustainability at the Washington-based Plastics Industry Association, says in a news release that the industry remains committed to keeping plastic out of the environment and in a circular economy.
“We need more support of circularity, not caps or eliminating the production of an essential material,” he says. “We must increase our recycling rates worldwide through improved infrastructure and greater accessibility to recycling for more people. We know there are solutions available to meet our shared sustainability goals and we look forward to reaching them together.”
In Memoriam:
Stanley Kramer

Martijn Reintjes
of Recycling International
Stanley Kramer, chairman and CEO of Los Angeles-based Kramer Metals Inc., died at the age of 86, having spent his last days at ISRI2024, the convention and exposition hosted by the Institute of Scrap Recycling Industries (ISRI), now known as the Recycled Materials Association.
Stanley, who continued to work at Kramer Metals six days per week, spent that time with his son Doug, president of Kramer Metals, and his grandson Jonah. According to the family, they were “very good days” that Stanley spent surrounded by old friends and learning what was coming in the industry.
Doug says his father meant “absolutely everything to him,” adding, “I am what I am and where I am because of him. He was central to my life and my family’s life, and he will be so greatly missed.
“If you want to know who my father really was, the answers are not to be found in his success in the scrap metal recycling industry nor as a successful entrepreneur nor in the things or wealth he amassed. It is in a successful marriage of 61 years. It is the success of my brothers and me and it is to be found in the love and admiration of his six grandchildren.”
Stanley was born in 1937 in the old Los Angeles Jewish neighborhood of Boyle Heights as one of 10 children. His parents, Moshe and Rina, had come from Latvia, through Ohio, settling in LA, where Moshe made a living by buying old scrap metal and selling it.
Professionally, Stanley became an important figure in the scrap metal industry, serving on and chairing committees for ISRI and one of its predecessor organizations, the Institute of Scrap Iron and Steel. He was a chapter president and earned the ISRI Lifetime Achievement Award in 2014.
Metals, Personnel
Alter appoints president, CEO

Alter Trading Corp.
Alter Trading Corp. has appointed Jack Grundfest as president and CEO, succeeding Jay Robinovitz, who retired as CEO at the end of April and continues to serve on the company’s board of directors.
Grundfest joined the St. Louis-based company with its acquisition of Tenenbaum Recycling Group (TRG) in August 2018 and initially served as senior vice president and chief administrative officer before becoming president in 2021.
Prior to joining TRG, Grundfest was managing director and CEO of the Mitchell, Williams Law Firm in Little Rock, Arkansas, and has more than 35 years of experience in management, business transactions and corporate and tax law. Grundfest earned his bachelor’s degree from the University of Arkansas, his juris doctor from the Bowen School of Law at the University of Arkansas at Little Rock and his master of laws in taxation at the University of Denver School of Law. He has been an active member of the business, charitable and civic communities in Arkansas, having served on the boards of various for-profit and nonprofit entities.
“Congratulations to Jack as he takes the lead into the next era, which we are certain will be an exciting and rewarding one for Alter Trading,” Chairman Rob Goldstein says. “We are looking forward to experiencing much success under Jack’s leadership.”
Founded in 1898, Alter is a privately owned, fifth-generation company and ISO 9001 and 14001 certified. Alter provides a direct supply of metal products, raw materials and related services to customers in the Unites States and throughout the world. The company boasts 71 locations in nine states, a sales office in Singapore, 18 automobile shredders and 1,600 employees.
Plastics
Brightmark plans $950M plastics circularity center
San Francisco-based global circular solutions company Brightmark LLC recently announced plans to develop a 2.5 million-square-foot circularity center in Thomaston, Georgia, with the capacity to repurpose more than 400,000 tons of plastic per year.
Brightmark says it selected Thomaston for its flagship facility because of its desire to grow alongside a strong community partner and responsible corporate actor, and the company says this $950 million investment will bring about 200 jobs to the area.
Brightmark notes that extensive planning and investment will be undertaken to ensure strong measures to mitigate environmental risk are in place. The company plans to invest more than $1 million to enable a “zero-liquid discharge” technology to ensure all process wastewater is managed and processed on-site, preventing contact with the municipal water supply that includes drinking water, groundwater, the Flint River and other local waterways. Brightmark says its circularity center will be considered a synthetic minor emitter and will implement the best available technologies to reduce emissions.
It also plans to implement detailed procedures to ensure employee safety, including training in critical areas such as operating procedures, emergency response, remediation and lifesaving protocols. Its health and safety team will establish a detailed emergency action plan for Thomaston that goes beyond regulatory requirements.
Additionally, Brightmark plans to invest $20 million in additive infrastructure projects pursuant to agreements with the city and state as part of the total investment, including upgrades to utilities, roadway improvements, rail access extensions and other resources.
“Over the years, Brightmark has invested heavily in talent and innovation required to build and refined a circular solution capable of tackling one of the most complex issues of our time: recycling,” says Brightmark founder and CEO Bob Powell, a Georgia native. “This investment in Georgia represents a commitment to supporting economic longevity and playing an integral role in building a sustainable future together in my home state.”
Brightmark’s Plastics Renewal solution repurposes material on a large scale, including hard-to-recycle plastics from a variety of sources, such as industrial sites, manufacturing facilities and schools. It also works with material recovery facilities to capture postconsumer plastic, then converts it to materials used to create new products. Brightmark says the new facility will provide a unique waste management capability to the Southeast region that has not existed in the past.
Paper
Paper cup acceptance at US mills reaches new milestone
As demand for recovered fiber grows in the United States, the NextGen Consortium, a multiyear consortium managed by New York-based Closed Loop Partners that addresses single-use foodservice packaging, along with the Falls Church, Virginia-based Foodservice Packaging Institute (FPI), are reporting a “major milestone” in their efforts to further paper cup recycling.
According to the organizations, multiple U.S. paper mills now will accept single-use polyethylene-coated paper cups in bales of mixed paper or polycoat cartons and aseptic packaging, bringing the total of North American mills accepting paper cups to more than 40.
Sponsored Content
Labor that Works
With 25 years of experience, Leadpoint delivers cost-effective workforce solutions tailored to your needs. We handle the recruiting, hiring, training, and onboarding to deliver stable, productive, and safety-focused teams. Our commitment to safety and quality ensures peace of mind with a reliable workforce that helps you achieve your goals.
The new mills to accept paper cups include a Newman and Co. mill in Philadephia; a PaperWorks Industries mill in Wabash, Indiana; a Resolute Forest Products mill in Menominee, Michigan; and Greif mills in Austell, Georgia, and Milwaukee.
“The mix of recovered paper we receive has changed dramatically over the last several years, now including much more plastic that we have to separate in the repulping process,” says Jeff Hilkert, vice president of paperboard sales at Greif Mill Group. “Paper cups contain good fiber and are no more difficult to recycle than many of the other prominent packaging categories we see today.”
Paper cups traditionally have been deemed unrecyclable because of their plastic lining, but as mills compete for shrinking supplies of newspaper and office paper in the recycling stream, interest in recovering material that contains high-quality fiber has grown. Many mills have undertaken repulpability studies to determine whether they can successfully recover the fiber from coated paper packaging for use in recycled-content products, and NextGen says positive outcomes of those studies have led to higher acceptance of paper cups at North American mills.
According to FPI, the mills that now accept paper cups in mixed paper bales represent more than 75 percent of U.S. mixed paper processing demand.
In addition to working with mills that now accept paper cups, NextGen and FPI note they continue to work with other interested mills to run studies that can help determine the viability of paper cups in their systems. They also are working with groups throughout the value chain to ensure more cups can be recycled, especially where viable and robust end markets exist.

Plastics
Blue Polymers selects Arizona for recycled plastics facility
Blue Polymers LLC has announced plans to build its second recycled plastics production facility in Buckeye, Arizona, to advance plastics circularity and support sustainable packaging.
The 162,000-square-foot facility is expected to create more than 60 permanent local jobs upon its anticipated opening in the second half of 2025, according to Blue Polymers. This facility joins the previously announced Indianapolis location as part of the firm’s network of four regional recycled plastics production facilities.
Blue Polymers says it will specialize in processing polyethylene (PE) and polypropylene (PP) recycled products suitable for sustainable packaging and other applications requiring increased recycled content. PE, commonly found in milk jugs and laundry detergent containers, and PP, used in consumer packaging such as margarine tubs and yogurt containers, will be processed and formulated into high-quality drop-in solutions for the packaging industry. Its product offerings also will include custom-blended and compounded materials for individual customers to help achieve sustainability goals and comply with federal, state or local requirements for recycled content.
Phoenix-based waste and recycling company Republic Services, a joint venture partner in Blue Polymers along with Luxembourg-based polymer recycling and distribution company Ravago, concurrently is developing a network of recycling sorting facilities called Polymer Centers, which produce high-quality, color-sorted recycled plastic feedstock directly from Republic’s national curbside collection business. Each Polymer Center will be linked with a Blue Polymers facility to promote plastics circularity and sustainable packaging. These sorting plants each will have a line dedicated to polyethylene terephthalate and another for high-density polyethylene and PP.
The Buckeye facility will process feedstock from Republic’s Las Vegas Polymer Center, which has been operational since late 2023.
In November of last year, Blue Polymers also broke ground in Indianapolis on a complex that will house a Polymer Center and an advanced polymer production facility, both of which are expected to start up late this year.
“As demand rises for domestically sourced, high-quality recycled plastics, many consumer packaged goods companies are committing to incorporating more recycled content into their packaging designs,” Blue Polymers says in the news release announcing the Arizona plant. “At the same time, five states have implemented minimum recycled content standards for single-use packaging. Blue Polymers’ facilities aim to support genuine package-to-package circularity, with an annual production target of 300-plus million pounds of recycled resins.”
Get curated news on YOUR industry.
Enter your email to receive our newsletters.
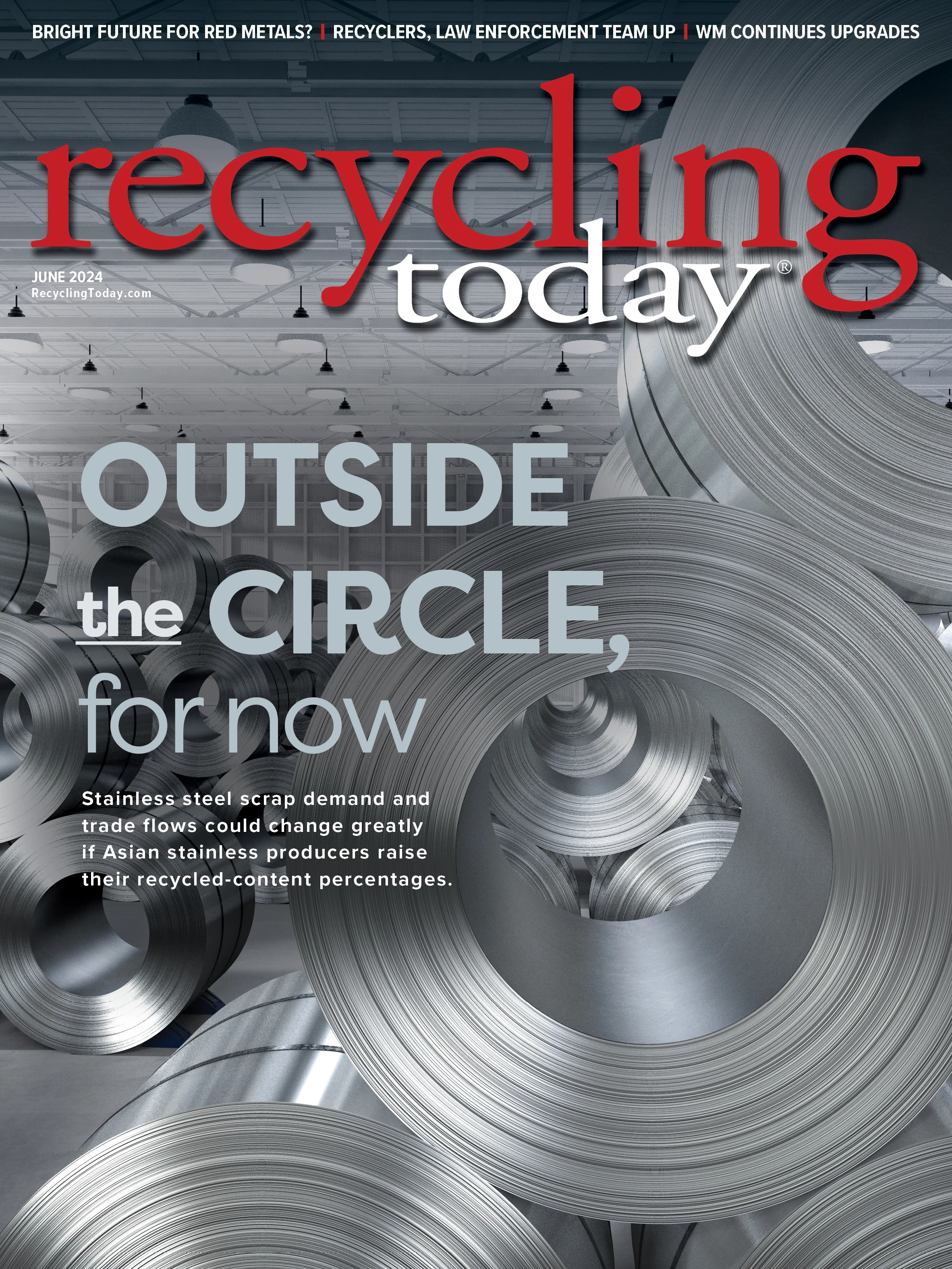
Explore the June 2024 Issue
Check out more from this issue and find your next story to read.
Latest from Recycling Today
- Toppoint Holdings expands chassis fleet
- Lego creates miniature tire recycling market
- Lux Research webinar examines chemical recycling timetables
- Plastics producer tracks pulse of wire recycling market
- Republic Services, Blue Polymers open Indianapolis recycling complex
- Altilium produces EV battery cells using recycled materials
- Brightmark enters subsidiaries of Indiana recycling facility into Chapter 11
- Freepoint Eco-Systems receives $50M loan for plastics recycling facility