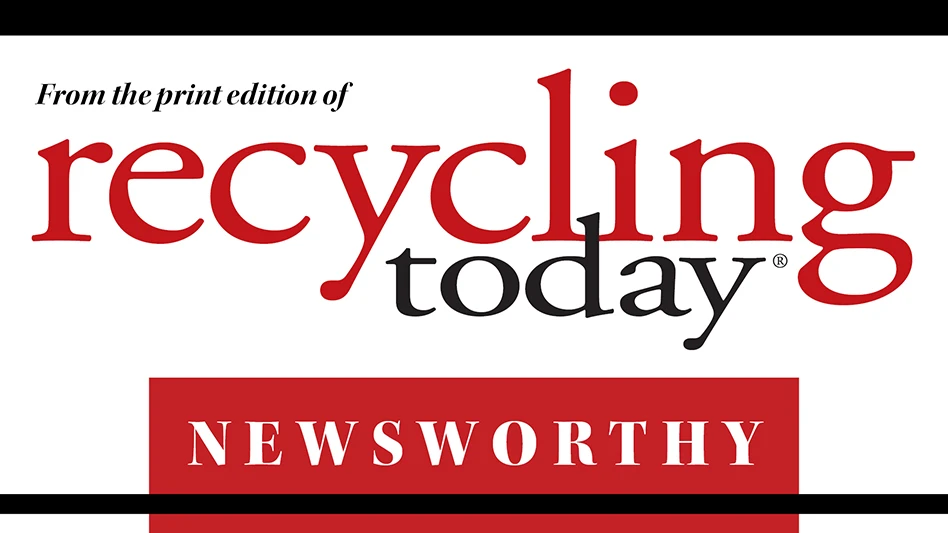

Metals
MetalX to partner on aluminum slab facility
Fort Wayne, Indiana-based scrap metal recycling and trading firm MetalX says it will work jointly with Manna Capital Partners to build a recycled-content aluminum rolling slab facility in the Great Lakes region.
MetalX and Manna Capital Partners, based in Louisville, Kentucky, say they plan to invest more than $200 million to build a greenfield aluminum rolling slab facility in either northeast Indiana, northwest Ohio or southern Michigan.
The facility will be designed to produce about 100,000 metric tons per year of what the companies call ultra-low carbon aluminum rolling slab with a higher percentage of recycled content than is currently available.
The partners say the facility’s end markets will be focused primarily on alloys for the beverage, packaging and auto industries and, to a lesser extent, on industrial and specialty markets. The plant is expected to become fully operational in the first half of 2026 and will employ approximately 100 people.
MetalX says the aluminum plant will be built near one of its scrap processing operations and a dedicated logistics center by Page Trucking to become part of a $300 million greenfield recycling campus where innovative closed-loop recycling solutions will support the aluminum industry’s sustainability and circularity goals.
The planned facility joins several major recycled aluminum melt shop investments announced last year, including those by can producer Ball Corp., steelmaker Steel Dynamics Inc. and Atlanta-based Novelis Inc.
MetalX is a privately held metals recycling business founded in 2012 by Danny and Neal Rifkin. The company sold its auto shredding plant and ferrous scrap-oriented business assets to the steel producer BlueScope in 2021. Last year MetalX acquired a secondary aluminum production site in Indiana.
Manna Capital Partners is a private investment firm founded by Junior Bridgeman and Kevin Attkisson.
Last year, Manna’s name was attached to the Ball Corp. announcement indicating that company intended to build a recycled-content aluminum can sheet rolling mill and melt shop in Los Lunas, New Mexico.

Paper
Cascades starts operations at Bear Island plant
Cascades Inc. has started operations at its new Bear Island containerboard plant in Ashland, Virginia.
With an annual production capacity of 465,000 tons of lightweight, 100 percent-recycled containerboard, the mill is equipped to strengthen the operational flexibility and geographic footprint of Cascades’ containerboard platform. The company, based in Kingsey Falls, Quebec, says the project created 700 jobs in the region during the construction phase and 180 permanent jobs at the onset of commercial production.
Cascades purchased the mill in 2018 from White Birch Paper, which originally operated a newsprint paper machine at the site. Although the company initially anticipated beginning operations in the first quarter of 2021, it experienced setbacks during construction related to labor and material availability.
According to a news release, the Bear Island mill is entering the ramp-up phase and gradually will increase its production until it reaches full capacity.
Cascades also says it plans to shut down paper machine No. 2 at its mill in Niagara Falls, New York, which has been temporarily shut down since November 2022. The machine has a production capacity of 90,000 tons per year, and the company says that machine would require investments to remain competitive.
The machine’s permanent closure will impact about 40 positions, most of which are currently vacant or will be subject to attrition to minimize the impact on the employees.

Plastics
Collaborative project shows feasibility of recycling automotive mixed plastics
A collaborative closed-loop recycling project for automotive mixed plastics has achieved positive results, demonstrating plastic recycling from end-of-life vehicle shredder byproduct.
Several companies collaborated on the project, including the United States Automotive Materials Partnership LLC (USAMP); Kingsport, Tennessee-based Eastman; Holland, Michigan-based Padnos; and global automotive interior supplier Yanfeng.
When automobiles are at the end of their lives, metals, tires and glass account for 80 percent to 90 percent of the materials that can be recycled through traditional mechanical recycling streams. The other 10 percent to 20 percent, referred to as auto shredder residue (ASR), consists of mixed plastics and other nonrecycled materials that traditionally end up in landfills or that are recovered using waste-to-energy technologies.
Eastman announced the project in July 2021 with plans to conduct research for about 15 months. Padnos supplied a plastic-rich fraction of ASR to be recycled using Eastman’s Carbon Renewal Technology (CRT).
Eastman says it successfully has demonstrated the conversion of that ASR feedstock into a synthesis gas, which is subsequently used downstream in the production of its polyester and cellulosic thermoplastics. The resins from this production process were further formulated and then supplied to Yanfeng.
According to Eastman, the parts molded by Yanfeng for the demonstration were tested to meet original equipment manufacturer requirements for Ford, GM and Stellantis, demonstrating proof of concept for a circular solution.
Eastman says the study proved the feasibility of its CRT, a molecular recycling technology that breaks down plastic-rich ASR into molecular building blocks. By recycling complex plastics using CRT, Eastman adds that it can replace fossil-based feedstock and create polymers to use in new automotive applications without compromising their performance.
Steven Crawford, executive vice president of manufacturing and chief sustainability officer at Eastman, says this project serves as an example of how collaboration across the value chain is essential for material circularity.
“Modern cars are made with approximately 50 percent plastics by volume, on average, and this number is only expected to increase as automotive manufacturers continue to seek lighter electric vehicles,” Crawford says. “We’re demonstrating a future where automotive hard-to-recycle plastics and fibers are diverted from landfills and recycled to produce new automotive parts.”
According to an Eastman spokesperson, the company plans to work independently with USAMP original equipment manufacturers to implement the closed-loop recycling concept into production applications.
“The collaboration on this project is indicative of the work that is needed to create closed-loop and circular economy solutions,” says Kari Bliss, principal of sustainability at Padnos. “Our purpose statement is on full display with this project—to continue to find ways to innovate, lead and make a positive impact in this world. We are proud to be the mechanical recycler involved in this complex endeavor, which is the first of its kind in North America.”
“We are pleased with the performance of the interior components we molded during the study and believe it would be a sustainable solution in production,” says Jeff Stout, executive director of global innovation at Yanfeng. He notes that his company sees potential with the resin developed during this closed-loop project.
In addition to diverting waste from landfills, USAMP, a subsidiary of the United States Council for Automotive Research LLC (USCAR), also sees potential for energy savings and reduced overall greenhouse gas emissions by applying this method.
“We are encouraged by the initial results of this study,” USCAR Executive Director Warwick Stirling says. “Innovative processes that enable ASR to be used in automotive parts can help bring us closer to more fully recycling end-of-life vehicles and enabling the possibility of a truly circular economy.”
Municipal
EGLE allocates $15.6M for recycling infrastructure grants
Michigan’s Department of Environment, Great Lakes and Energy (EGLE) says recycling in the state is at an all-time high. The total amount of residential recycled materials reported for fiscal year 2022 was 620,494 tons, about 66,000 tons more than what was reported in the 2021 fiscal year.
According to officials, Michigan residents recycled more than 339,000 tons of paper, 154,000 tons of metals, 71,000 tons of glass and 45,000 tons of plastics in the 2022 fiscal year.
EGLE has allocated $15.6 million in 2023 grant funding, available through public-private partnerships, to help fund recycling infrastructure investments and projects in the state. The recycling and remanufacturing industries in Michigan create 72,500 jobs and contribute more than $17 billion to the state’s total economic output, the department adds.
EGLE already has awarded some of the $15.6 million to companies and communities this year to help advance recycling efforts.
Houston-based WM is constructing a $35 million recycling processing facility in Detroit, and EGLE has awarded the company a $465,000 grant to help advance this facility, which is expected to process up to 40 tons of materials per hour. Once open, EGLE says WM plans to activate existing transload facilities in Traverse City, Kalamazoo, Tawas, Saginaw and Lansing.
EGLE also has awarded $1 million to Flint, Michigan, to help provide 96-gallon recycling carts to some 34,000 households. The Recycling Partnership, Washington, also has pledged to support the cart project with a $3.3 million grant.
EGLE has awarded $4 million to the Kent County Department of Public Works’ Sustainable Business Park project in Kent and Allegan counties, as well as a $499,999 grant to purchase baling equipment for old corrugated containers at its North Kent Transfer Station. A $406,000 grant will help to purchase robotic sorting equipment to automate the sorting line at its Recycling & Education Center.
In addition, VMX International, headquartered in Detroit, has received a $100,000 small business development grant from EGLE to recycle items ranging from office paper to batteries. The grant supports VMX’s plan to build a $50 million lithium-ion battery recycling facility in Detroit that is tentatively slated to open in 18 to 24 months. According to VMX, the facility will separate, dismantle and shred lithium-ion batteries.
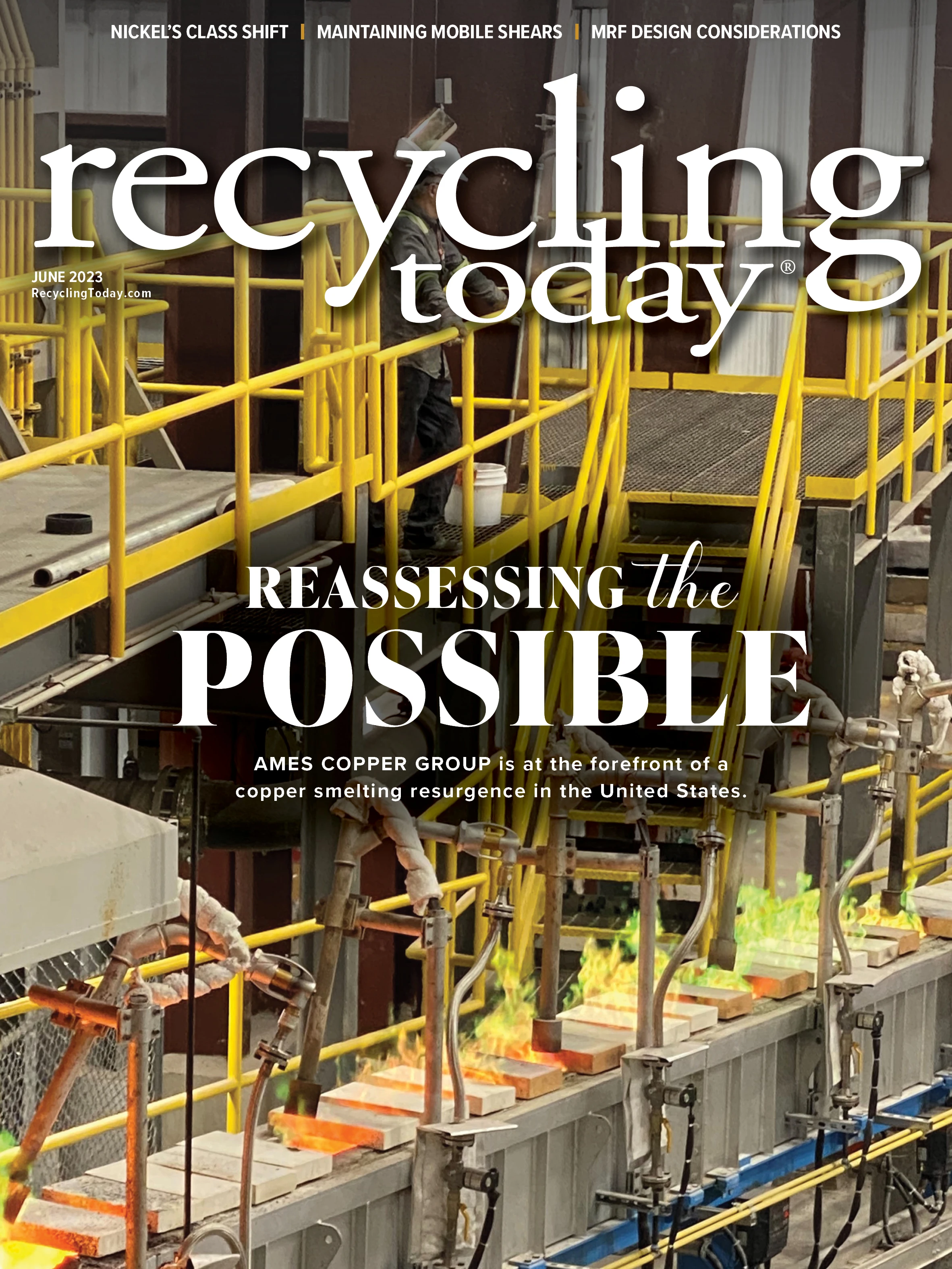
Explore the June 2023 Issue
Check out more from this issue and find your next story to read.
Latest from Recycling Today
- Nextek, Coveris to recycle food-grade plastic film
- Recyclekaro expands recycling capacity
- USTR hears comments on port fee proposal
- C&D World 2025 hits record attendance and exhibitor numbers
- Denali now offers mobile depackaging service
- Hyundai confirms Louisiana as EAF mill site
- ASCE sees infrastructure progress, but more to be done
- Global steel output tapers downward