
© shèng zhāng | stock.adobe.com

Metals
Ternium to build sizable EAF mill in Mexico
The board of directors of steelmaker Ternium SA, based in Luxembourg, has approved the construction of a 2.6-million-ton-per-year electric arc furnace (EAF) steel slab production facility in Mexico.
The large-capacity melt shop could be located at or near Ternium’s Pesquería industrial center facility in Neuvo León in northern Mexico, the company says, adding that its new EAF mill also will complement and support its new hot rolling mill, which began operations at Pesquería in mid-2021.
The steelmaker says direct-reduced iron (DRI) will have the potential to play a large role in supplying metallics to the EAF mill, adding that while the EAF will be able to produce up to 2.6 million tons per year, an accompanying DRI “module” will have an annual capacity of 2.1 million tons.
Ternium says it expects to commission the mill in the first half of 2026.
“The implementation of the USMCA [United States-Mexico-Canada] trade agreement and recent trends of nearshoring manufacturing capacity in the steel value chain have made the USMCA region an attractive destination for continued investment,” Ternium CEO Máximo Vedoy says.
“Importantly, the new EAF-based steel shop will also accelerate Ternium’s progress toward achieving our previously disclosed 2030 decarbonization target and support our ongoing compliance with the USMCA’s ‘melted and poured’ requirement. The new DRI module will also include carbon-capture capabilities and readiness to switch from natural gas to hydrogen use.”
In its 2021 sustainability report, Ternium says 7 percent of its steelmaking output consisted of scrap-fed EAF technology. Another 30 percent was steel made using DRI fed into an EAF, while the remaining consisted of iron ore-based basic oxygen furnace production.
Ternium made the announcement at the same time it released its 2022 financial results. For the year, the steelmaker reported adjusted earnings before interest, taxes, depreciation and amortization of $3.4 billion, down nearly 42 percent from the more than $5.8 billion it earned in 2021. The company also shipped nearly 11.9 million tons of steel last year, down slightly from the 12 million tons it shipped in 2021.
In addition to its Neuvo León, operations, Ternium operates 18 production centers in Argentina, Brazil, Colombia, Guatemala, Mexico and the United States.

Legislation & Regulations
Study: EPR laws could boost US recycling rates
A recent study conducted by The Recycling Partnership, Washington, claims states can expect significant increases in recycling rates for packaging—including plastic, glass, aluminum and steel—and printed paper with the adoption of extended producer responsibility (EPR) programs.
The study, “Increasing Recycling Rates with EPR Policy,” explores the impacts of EPR programs in seven jurisdictions worldwide and results from six U.S. states to assess the potential effects of EPR on state recycling rates and other metrics.
The research focused on EPR’s impact on seven paper and packaging recycling programs around the world. The organization says the findings showed that across the board, EPR policy drove the collection and recycling of target materials to more than 75 percent in British Columbia, Belgium, Spain, South Korea and the Netherlands, with Portugal and Quebec at more than 60 percent. Across all materials, the study shows U.S. state programs performed far lower.
U.S. states tracked by The Recycling Partnership included Washington, Connecticut, Maryland, Wisconsin, Colorado and Florida. Using the most recent recycling rate data provided by those states between 2019 and 2021, Washington had the highest rate at 52 percent, while Florida was sixth amongst those studied at 17 percent.
The report notes that performance gaps exist across the U.S. when it comes to recycling rates for packaging and printed paper (PPP). Mixed plastics and films and flexibles continue to be a drag on recycling performance, with both categories composing a significant amount of PPP material by weight; however, except for Washington’s polypropylene recycling (6 percent in 2021), very little of the material was meaningfully recycled.
Additionally, mixed paper, cardboard and glass continue to dominate the weight of generated material. The organization concludes that if just cardboard and mixed paper in Colorado performed at the levels seen in PPP EPR programs, Colorado’s existing recycling rate would almost double to 42 percent. The report also indicates that access data suggests a significant gap in U.S. state recycling performance likely is driven by the lack of comprehensive multifamily recycling.
“Lack of sustainable funding is one of the greatest challenges for U.S. residential recycling systems,” The Recycling Partnership CEO Keefe Harrison says. “EPR provides a huge opportunity to unlock the environmental and economic benefits of recycling.”
With EPR, companies that produce packaging materials are required to fund local recycling programs by paying fees, shifting the financial burden away from local governments and taxpayers. EPR fees also can incentivize companies to make packaging more recyclable and use a greater percentage of recycled content.
California, Colorado, Maine and Oregon all have adopted EPR legislation, while several other states currently are considering these programs. An EPR proposal in Washington recently failed to advance through the state legislature.
The organization says implementing EPR programs in the U.S. would yield a number of benefits:
- increasing overall residential recycling rates by as much as 48 percentage points;
- creating recycling access that is nearly universal;
- increasing participation in recycling;
- boosting the amount of recycled content by millions of tons; and
- recapturing between $13 million and $91 million in lost material economic value in EPR states.
“With this research, we can see that these international programs drive dramatic improvement in recycling rates and that EPR policy has a significant impact,” says Dylan de Thomas, vice president of public policy and government affairs at The Recycling Partnership. “It’s clear that well-designed EPR policy is key to growing and improving recycling and achieving a circular economy.
“EPR has the potential to close gaps in recycling rates for all materials, create jobs, reduce greenhouse gas emissions and deliver even more benefits to support people and planet,” he adds.
Metals
Matalco begins operations in Franklin, Kentucky
Matalco, a large independent secondary aluminum billet producer headquartered in Brampton, Ontario, has completed construction of its new facility in Franklin, Kentucky, which produces aluminum ingot slabs. The facility began operations in December 2022.
Matalco invested about $65 million in the facility, which can produce 135,000 tons per year. The company says it is looking to invest in another furnace to bring the annual capacity to 195,000 tons.
Matalco is sourcing secondary aluminum for the new site from its preexisting customer base as well as from Triple M Metal. Matalco is part of the Giampaolo Group Inc., Brampton, which also owns Triple M Metal.
The company tells Recycling Today it decided solely to focus on aluminum ingot slab production because it is an underserved product group.
“With a lack of green solutions in the market pertaining to aluminum ingot slab, this Franklin, Kentucky, site is able to fill that gap,” Matalco says, adding that it aims to better serve its customers through this new site, which also strengthens the company’s geographic footprint.
“There is a thriving aluminum sector in the Kentucky, Tennessee and Alabama corridor that Matalco is now able to take part in while offering better services to our customers in the southeastern states,” Matalco tells Recycling Today. “Matalco will continue growing by following our long-term strategic growth plan. We are committed to servicing our customers better and committed to providing made-in-North America solutions to the world of aluminum production.”
Matalco says the new plant in Kentucky, combined with its six existing aluminum facilities, will produce more than 1.9 billion pounds of recycled aluminum annually.
The Giampaolo Group says it is one of the largest fully integrated metal management organizations in North America, with expertise in scrap metal recycling; aluminum remelting; electronics recycling and reuse; and steel and aluminum coil processing, blanking and distribution.
Batteries, Events
Battery and Critical Metals Recycling Conference launching in June
The Recycling Today Media Group, a business unit of GIE Media in Valley View, Ohio, has announced the launch of the Battery and Critical Metals Recycling Conference, set for June 12-13 in Atlanta. The event serves the ballooning market for environmentally responsible management of end-of-life batteries from electric vehicles, consumer electronics and the developing stored power sector.
The proliferation of electronic consumer goods, industrial and commercial equipment and, increasingly, electric vehicles [EVs] is creating an enormous flow of end-of-life batteries,” says James Keefe, Recycling Today Media Group publisher. “Only a small percentage of these batteries are collected and recycled.
“Our event will examine the issues surrounding battery and critical metals recovery and recycling.”
Projected demand growth for critical metals such as lithium, cobalt, nickel, copper, aluminum and others required for battery production is, in some cases, expected to grow threefold by 2030. This demand-side curve creates a tremendous economic incentive for recovering and marketing the materials from existing batteries, event organizers say.
End-of-life batteries that end up in the general waste or traditional recycling streams have been linked to tragic fires, creating a terrible societal cost in human life and property damage and destruction. Proper recycling of end-of-life batteries safeguards the environment and produces valuable raw materials essential for green power to thrive.
The event is geared to a variety of stakeholders, including auto recyclers; battery, electronics and EV manufacturers; recycling companies; scrap metal processors; private equity and other investors and more.
Registration information and additional details will be available at www.BatteryRecyclingConference.com.
A limited number of sponsorship opportunities also are available by contacting rt-sales@gie.net.
Metals
US Steel to supply General Motors with sustainable product

United States Steel Corp., Pittsburgh, has announced it will supply General Motors (GM) with its advanced and sustainable steel solution called Verdex. The company says the steel is manufactured with up to 75 percent fewer emissions compared with traditional blast furnace production, is made with up to 90 percent recycled content and is endlessly recyclable without degradation.
Verdex steel will be manufactured at Big River Steel (BRS), a Leadership in Energy and Environmental Design-certified facility that also meets the ResponsibleSteel site certification, and at a new advanced technology mill under construction in Osceola, Arkansas. The company says it expects the steel produced at the BRS site to begin shipping to GM manufacturing facilities starting this year.
“We are pleased to join GM in its mission to promote a world with zero emissions by providing such an advanced and sustainable steel product,” U.S. Steel Senior Vice President and Chief Commercial Officer Ken Jaycox says. “As part of our Best for All strategy, we are committed to helping our customers reduce their carbon footprint by providing American-made advanced steel products that are manufactured with fewer emissions and can be recycled repeatedly. Our Verdex steel offers both the advantages of advanced high-strength steel and low manufacturing emissions.”
GM Vice President of Global Purchasing and Supply Chain Jeff Morrison says, “This agreement is an example of how we are innovating with our suppliers to create lower-emission products for our customers. It also highlights how strong supplier relationships can help build a better future.”
Sponsored Content
Labor that Works
With 25 years of experience, Leadpoint delivers cost-effective workforce solutions tailored to your needs. We handle the recruiting, hiring, training, and onboarding to deliver stable, productive, and safety-focused teams. Our commitment to safety and quality ensures peace of mind with a reliable workforce that helps you achieve your goals.
U.S. Steel says the $3 billion facility currently under construction in Osceola will use advanced technology to expand production of sustainable advanced high-strength and electrical steels, including an expansion of its Verdex steel offering, which will be made widely available to manufacturers with the aim that it can help lower their carbon footprints.
Paper, Financial
Kruger invests in Montreal mill

Kruger Inc. has announced an investment of more than CA$30 million ($22.5 million) in the Place Turcot Containerboard Mill, part of the Kruger Packaging business unit, in its home city of Montreal.
With the investment scheduled to be completed in 2025, Kruger says the Place Turcot facility will be the first in North America to manufacture 100-percent-recycled saturating kraft board, which is used to make high-pressure laminates for furniture, countertops and decorative paneling.
The investment was announced during a February news conference attended by several Canadian and Quebec elected and appointed officials, including Jonathan Wilkinson, Canada’s minister of natural resources, and Maïté Blanchette Vézina, Quebec minister of natural resources and forests.
One aspect of the Place Turcot mill investment will be the implementation of machine learning and artificial intelligence (AI) technology. “The implementation of AI technology at the mill is to optimize production and automation and to reduce waste,” François Richard of Kruger tells Recycling Today, adding that the automation is not being deployed to inspect or sort scrap feedstock.
Additionally, “One of the main goals of the modernization of our mill is to diversify the portfolio of products that are manufactured there,” Richard says, adding that the saturating kraft board will be an additional grade to be made at the mill and not a replacement for any existing grades.
In addition to the saturating kraft board, Place Turcot will continue to make recycled-content gypsum board paper, customized board for residential construction, folding boxboard for Food and Drug Administration-compliant food packaging and white top linerboard. According to Kruger, the Place Turcot mill will be the only consumer of old corrugated containers (OCC) in the greater Montreal area and the investment will allow it to “consolidate its role as a crucial player in the circular economy” of the region.
The Place Turcot Containerboard Mill is next to Kruger’s Sorting and Recovery Centre near downtown Montreal and consumes the equivalent of all the OCC generated in the region.
The mill also is expected to reduce Kruger’s greenhouse gas emissions by more than 2,200 metric tons per year once the project is completed, according to the company.

Plastics
Nova Chemicals launches circular solutions business
Nova Chemicals Corp., based in Calgary, Alberta, has established Nova Circular Solutions, a new line of business that focuses on lower-emission, recycled solutions. Nova Circular Solutions will be the home of the Syndigo brand, the company’s newest portfolio of recycled polyethylene (rPE).
Recycling Director Alan Schrob leads Nova Circular Solutions. He has nearly 30 years of experience in plastics, manufacturing, health, safety and the environment. His team includes experts in plastics development, recycling technology, additive science, packaging design and regulatory compliance.
“Plastic products play a critical role in our daily lives, and industry and consumers are placing higher value on products that contribute to the circular economy,” says John Thayer, Nova Chemicals senior vice president of sales and marketing.
Three products are available under the Syndigo brand, and Nova says the rPE products are designed to support growing demands for recycled content and the decarbonization goals of converters and brands.
EX-PCR-WR3 is a mechanically recycled resin sourced from PE agricultural film for use in e-commerce mailers, can liners, carry-out bags, protective packaging and shrink film.
EX-PCR-NC4 is a mechanically recycled resin sourced from back-of-store distribution center PE stretch film and front-of-store consumer drop-off. It can be used to manufacture heavy-duty sacks, e-commerce mailers, stretch wrap, collation shrink, protective packaging and industrial films.
EX-PCR-HD5 is a mechanically recycled resin sourced from high-density polyethylene milk jugs for use in flexible packaging, heavy-duty sacks and small-part blow molding.
“Converters and brand owners are incorporating more recycled materials into their packaging and products to meet their sustainability goals and the demands of consumers,” says Greg DeKunder, Nova Chemicals vice president of polyethylene marketing and circular polymers. “These important steps support our customers and drive towards a plastic circular economy, helping to protect the planet for future generations.”
Get curated news on YOUR industry.
Enter your email to receive our newsletters.
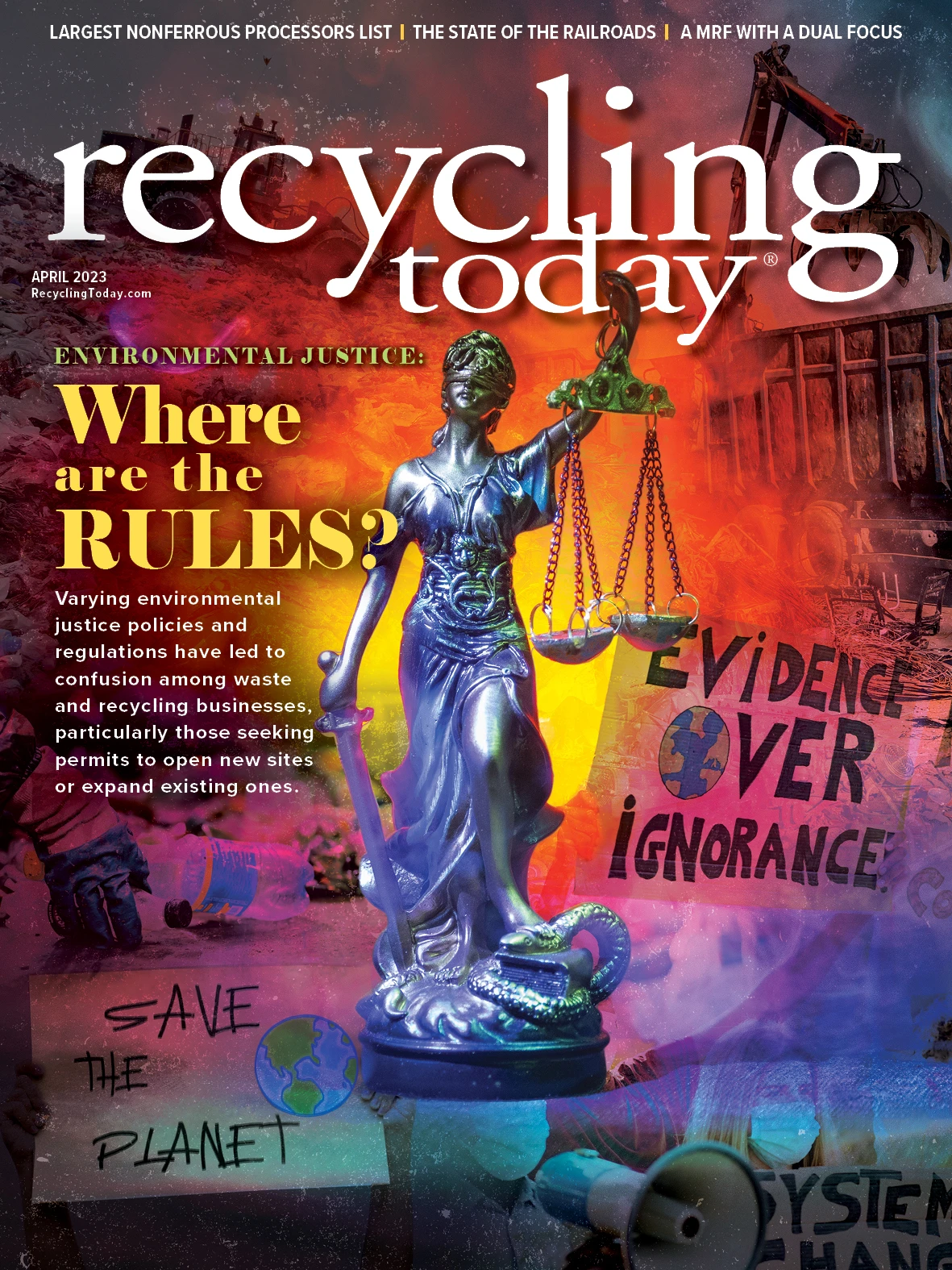
Explore the April 2023 Issue
Check out more from this issue and find your next story to read.
Latest from Recycling Today
- RRS adds to ownership team
- S3 Recycling Solutions acquires Electronics Recycling Solutions
- Nextek, Coveris to recycle food-grade plastic film
- Recyclekaro expands recycling capacity
- USTR hears comments on port fee proposal
- C&D World 2025 hits record attendance and exhibitor numbers
- Denali now offers mobile depackaging service
- Hyundai confirms Louisiana as EAF mill site