
For the past decade, Newco Metal & Auto Recycling, St. John’s, Newfoundland and Labrador, has experienced significant growth and change. From 1985 until 2001, the company operated a single facility in St. John’s, processing automobiles, light iron, white goods and heavy steel, along with some nonferrous metals.
Bob Anstey became the company’s owner in 2011. Since that time, he has spearheaded a handful of mergers and acquisitions. As a result, the company has grown to operate nine facilities across the province of Newfoundland and Labrador. Newco processes and exports scrap metal for customers in more than 100 municipalities throughout the province.
In recent years, Newco also has been focused on modernizing its operations. For many years, the company simply crushed and baled automobiles and white goods for resale. However, export transportation can be expensive for the company because it’s situated on a sparsely populated island with little trucking activity. Nick Henderson, project engineer at Newco Metal & Auto Recycling, notes that the company’s headquarters is about “as far east as you can go in North America.”
Henderson says, “Transporting scrap in the province has logistical challenges. To transport a load of material from the west side of the island to our headquarters in St. John’s is a full day trip. In terms of export, loading unshredded scrap [materials] on trailers for export is challenging, given the nature of the material as well as costs associated with shipping for further processing.”
To reduce transportation-related costs, Newco installed a shredder and a downstream nonferrous separation plant at its St. John’s facility in March.

New benefits
Since the installation, Henderson says Newco’s operations have changed “quite a bit.” The company had to hire 20 employees to operate the auto shredding facility. The shredder, which is a M6090 supplied by Wendt, Buffalo, New York, processes up to 60 tons per hour. It can be used to process scrap automobiles and light iron. The shredder includes a dual magstand with electromagnetic drums for separating ferrous shred, and it has a Shred1 ballistic separator manufactured by Eriez, Erie, Pennsylvania. The Shred1 uses ballistics to separate iron-rich ferrous from much of the mixed metals in the postdrum magnet flow. This separator is designed to deliver a premium low-copper ferrous product (in the range of 0.16 to 0.20 percent copper) and a traditional No. 2 ferrous shred.
The company also installed a Wendt nonferrous separation plant to process auto shredder residue (ASR). Newco recovers and separates zorba, insulated copper wire and zurik. The plant sorts the ASR into three size fractions using a Bivitec screen. The ASR then is passed through two eddy current separators to separate the zorba. From there, a Jost wind sifter removes light particles—fibers, cardboard or paper—from heavy particles. The product then goes to three Tomra Finders, which use sensor-based technology to separate the remaining metals from the ASR, generating insulated copper wire and zurik.
“The shredder opened the door to new market opportunities,” Henderson says. “Feasibility of the installation was driven by a market for the ferrous and nonferrous products generated by the equipment as well as giving new options for efficiently transporting the new products.”

Installation considerations
Installing the shredder and nonferrous separation plant took Newco about a year. If a company operates multiple yards, Henderson says it’s important to select the best facility to place the shredder and nonferrous separation plant.
“The shredder generates noise,” he says. “If there are any residential areas nearby, they could be impacted by the noise. You have to be strategic in choosing the location of the facility.”
Newco selected its St. John’s facility for the shredder and nonferrous separation plant. The site is about 3 kilometers (or roughly 2 miles) away from residential areas. Henderson says the closest industrial neighbors are about 300 meters (or nearly 1,000 feet) away.
Determining where to place a shredder and nonferrous separation plant at an existing scrap yard can be challenging. The company eventually decided to develop part of the property behind its warehouse to make room for the shredder and nonferrous plant.
“Shredding and separating allows for uplift in the value of the product.” – Nick Henderson, project engineer, Newco Metal & Auto Recycling
“We had a warehouse parking lot and some other facilities on the site that we had to work around,” Henderson says.
He adds that his team talked to the team at Wendt to determine efficient placement for the equipment. He says Newco visited other scrap facilities in Canada and throughout North America to get a better idea of what might work best for the company.
Ensuring the St. John’s facility had adequate power for these new machines took additional time. Newco hired a contractor to construct underground electrical service to power the new equipment, which took a few months to complete.
Permitting the shredder also was a six-month process for Newco. Henderson says the company worked with local consultants to complete this task. Newco had to demonstrate to the local government how the technology works to minimize pollution.
The time and capital investments appear to be paying off for Newco. The new equipment was commissioned in April. In the past few months since, Henderson says the company has noticed the financial benefits of adding the processing equipment.
“Shredding and separating allows for uplift in the value of the product,” he says. “It was a big upgrade to the company and also a big change. But it was necessary to keep up with the future of processing and export.”
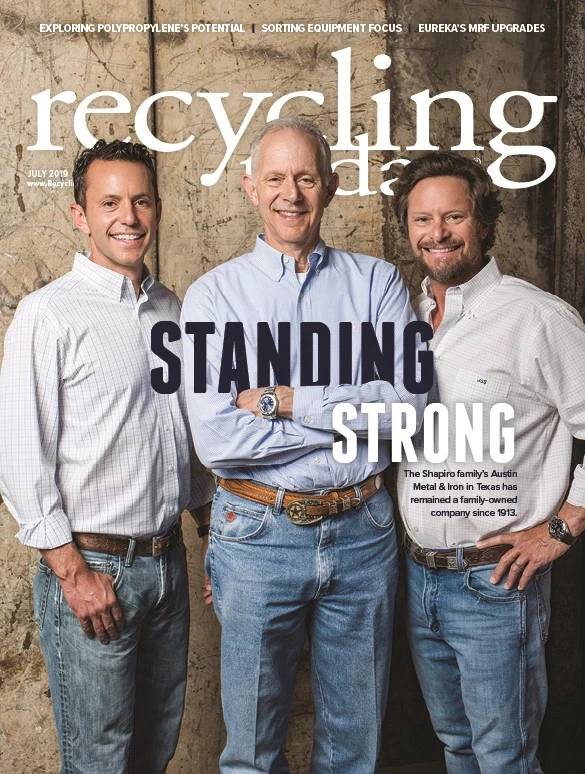
Explore the July 2019 Issue
Check out more from this issue and find your next story to read.
Latest from Recycling Today
- AF&PA report shows decrease in packaging paper shipments
- GreenMantra names new CEO
- Agilyx says Styrenyx technology reduces carbon footprint in styrene production
- SABIC’s Trucircle PE used for greenhouse roofing
- Hydro to add wire rod casthouse in Norway
- Hindalco to invest in copper, aluminum business in India
- Recycled steel price crosses $500 per ton threshold
- Smithers report looks at PCR plastic’s near-term prospects