A proposed mill could help Northeast ONP markets, but nagging questions remain.
A company planning to spend more than $1 billion on a new project typically generates great fanfare within a community. Further, a project that promises to employ hundreds full time, and recycle hundreds of thousands of tons of recovered fiber, is generally viewed as an economic windfall for the state as well as the region.
Such is the scenario in Poughkeepsie, N.Y., just north of New York City. Last month Evergreen Pulp & Paper announced plans to build a recycled paper mill that, when complete, would employ 700 people and convert more than 700,000 tons of old newspaper, old magazines and office paper into 260,000 metric tons of 100-percent recycled newsprint and 310,000 metric tons of recycled lightweight coated paper.
Preliminary plans segment the project into two phases. The first phase would focus on building a recycled newsprint mill, while the second would produce recycled printing and writing paper.
Despite the possibilities the project holds, many in the industry harbor reservations about the company and its owner, Ronald Morgan. Some caution that Evergreen has a track record of shopping the mill concept from state to state, starting with a plan to build the mill in the middle of the desert in Arizona almost three years ago. After announcing plans and partial details, Evergreen sold the concept to Fletcher Challenge, a forest products company in Vancouver, British Columbia.
Evergreen then looked at a number of locations in the Northeast, including sites in Bow, N.H., and New Milford, Conn. In each of these projects, the company generated a significant amount of favorable publicity about the project before moving on, in some cases catching the state government agencies by surprise.
In New York, Morgan hopes to quell the suspicions held by many in the industry that he does not have the ability to take the project to completion. To demonstrate his commitment to the Poughkeepsie project, Morgan purchased the option to buy 95 acres of undeveloped land from IBM. According to the Poughkeepsie Journal, Morgan put down about $400,000 for the option, with the plan to complete the purchase within the next 12 months. The newspaper cites estimates of the property value around $10 million. According to a press release issued by Evergreen, the company has been discussing the project since last spring with the state of New York as well as IBM. As for announcing the project location in other states, Morgan claims that the Poughkeepsie site was one of a number of locations that were considered. One of the deciding points to persuade Morgan to site the mill in New York was the incentive package the state offered.
MONEY SOURCES. Already the state of New York, through the Industrial Development Agency, is offering $375 million in low interest financing which could fund most of the first phase of the project, which is expected to cost about $400 million. Costs for the second phase are expected to approach $800 million.
The incentive package offered by the state would be one of the largest ever offered to a company in the United States. However, before receiving any kind of incentives, the company must demonstrate the project has adequate financing and is otherwise viable, according to Steve Vitoff, a spokesman for the state Department of Economic Development. The incentive package includes tax abatements, utility discounts from Central Hudson Gas & Electric, and tax-free county bonds, which could save the company more than $10 million in interest payments over the next 15 years.
Other features of the project include $80 million in benefits as a result of Evergreen’s location in an economic development zone. Given the sizable amount of money being offered in the incentive package, a spokesman for the state says New York is approaching the project "very warily." Because of this, the state has only $650,000 invested in up-front costs, with the rest contingent on the project being completed.
One representative from the state of New Hampshire expressed disappointment that Morgan pitched the project in New Hampshire and then pulled out, blaming the Public Service of New Hampshire for his inability to go through with the plan. "The state’s bonding agency was prepared to make $75 million in bond money available for three years for the project," according to the spokesperson, who preferred to remain anonymous.
The timing of the project also is of concern. Amy McGowan, with Morgan Stanley, a financial services company headquartered in New York City, says that by 1997 newsprint prices should have hit their high-water mark. A mill expecting to come online that year would likely be faced with decreased prices, as well as softer demand for the finished product.
MARKET VIABILITY. The newsprint market has turned itself on its head over the past year. Following a devastating economic downturn which shuttered some newsprint machines and sent ONP prices into unprecedented depths in many cases, prices are now surging. Newsprint demand is strong, with finished product prices climbing.
On one hand, newspaper publishers, faced with escalating costs, would be interested in a low cost newsprint producer. An added benefit is location. Not only is the Northeast rich in ONP supply, but end markets for the material also are in abundance.
The downside, however, is that with strong demand for newsprint, prices for ONP have skyrocketed. On the East Coast, prices have climbed by around 400 percent. Higher prices are forcing some newsprint producers to back away from projects that they may have earlier considered.
What makes many people uncomfortable is Morgan’s limited experience in the industry. Many have observed that this could be an obstacle in obtaining financing for the project. Already a number of state officials are cautiously watching the Evergreen project to see if the company intends to stick with its plans.
Gordon Floe, with NLK Consultants, an engineering consulting firm based in Vancouver, British Columbia, working with Evergreen Pulp & Paper on the project, feels the project is viable. As for Morgan’s limited experience, Floe points out, "the advantage is he is very creative. He leaves no stone unturned, no door unknocked. . . He asks many questions, questions that a company already in the industry wouldn’t necessarily ask."
Floe adds that the project, at least in the preliminary stages, would be state-of-the-art, allowing the company to operate within a much cheaper manufacturing cost. The mill’s planned capacity -- about 250,000 tons per year -- would allow it to be a low-cost producer. In addition, because the mill would produce recycled material exclusively, energy costs would be much lower than from a virgin newsprint mill producer.
SUPPLYING MATERIAL. While many in the government side have jumped at the opportunity to bring the Evergreen Pulp and Paper project and its potential economic benefits into their respective states, paper stock dealers have been more skeptical. According to some of the largest handlers of ONP in the Northeast, Morgan’s company has not attempted to line up any sources of material. Without these preliminary arrangements, financing the project is impossible.
Under the best case scenario, the project is several years from opening its doors, but a number of paper stock dealers say they are not inclined to sell material to the mill. Citing relationships established with existing facilities as one reason, several vendors suggest that the proposed project has been flash before substance.
Richard Gordon, with Paper Recycling International, Buffalo, points out that before his company gets involved in selling any product to a mill, significant background research is conducted. "We want to know whether the company is a fly-by-night operation," Gordon says. For a company such as PRI to supply the mill, Gordon feels the mill must show that it is a viable entity.
With only a handful of companies able to deliver sizable amounts of material to the facility, other questions arise. Noel Prins, with Prins Recycling, Ft. Lee, N.J., says his company had preliminary dialogue with those in charge of the Evergreen project, although Prins feels better suited to work with much shorter contract periods.
Prins lists a number of issues that need to be addressed, such as consistency of the mill’s purchases, how payment is structured and length of contract. "We generally don’t work with longer contracts," he points out.
Allan Zozzaro, vice president of Zozzaro Brothers, Clifton, N.J., notes that with ONP markets as strong as they are right now, they could sell all of their excess tonnage to their regular buyers. As for working with new projects, Zozzaro says his company would need assurances from the mill about the longevity of any contract. "We would need a guarantee," says Zozzaro.
Other paper stock operations in the Midwest express similar sentiments, although several note that if the price is right, the mill could get tonnage. Even then, many suggest that other mills would respond in kind, raising their price. Several sources in the Northeast note that if the company would have come in and made arrangements to secure tonnage a year ago they would have a better chance to guarantee themselves a supply.
But given the current market upswing, many handlers of the grade are having a hard enough time satisfying increased demand for existing accounts.
Get curated news on YOUR industry.
Enter your email to receive our newsletters.
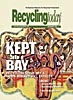
Explore the November 2001 Issue
Check out more from this issue and find your next story to read.
Latest from Recycling Today
- Astera runs into NIMBY concerns in Colorado
- ReMA opposes European efforts seeking export restrictions for recyclables
- Fresh Perspective: Raj Bagaria
- Saica announces plans for second US site
- Update: Novelis produces first aluminum coil made fully from recycled end-of-life automotive scrap
- Aimplas doubles online course offerings
- Radius to be acquired by Toyota subsidiary
- Algoma EAF to start in April