In many regions across the United States, highway and airport runway reconstruction projects are popping up like wildflowers. With more planned, the outlook for recycling concrete and asphalt – the two main items recovered in highway and airport C&D projects – is solid if it can be done efficiently and profitably. And there are processes and equipment being developed for recycling highway materials which promise to do just that.
Business in general in most sections of the country is reported as being good, but the real opportunities in a C&D debris recycling boom may come down the road. Assessment of the current situation in construction and asphalt recycling and consideration of new techniques will position the industry to capitalize on that boom.
RECLAIMED ASPHALT
Reclaimed asphalt pavement is a big factor in highway construction. About 80 percent of the RAP available in the U.S. is reclaimed and recycled, according to the National Asphalt Pavement Association, Lanham, Md. Not all of that goes into the new hot mix. Much of the RAP material is used in the base course or on the shoulders, but it goes back into the highway in some form.
“Asphalt recycling is done as a matter of course,” agrees Michael Taylor, executive director of the National Association of Demolition Contractors, Doylestown, Pa. “There are buyers almost everywhere.”
“We need to understand better the emerging Super-pave technology,” adds Dale Decker, vice president of research and technology with NAPA. Superpave came out of the Federal Highway Administration’s Strategic Highway Research Program to develop designs for super-performing pavements.
“The mix design is similar to what we do; however, there are some new materials requirements,” Decker says.
He says that reuse of asphalt materials will continue to grow, especially in areas of the country where good aggregate is not available.
While difficulties with material under 75 microns continues to be an ongoing problem, there are projects underway to help municipalities and contractors better understand their use.
The Federal Highway Administration presentation, “Practical Guidance on the Reuse of Existing Pavements,” given at the mid-year meeting of the American Road and Transportation Builders’ Association, spelled out the U.S. government’s views on pavement recycling. Jim Sorenson, applications team leader at the FHWA, says that one of the key advancements detailed in the presentation was the award of a new contract with Auburn University to develop a four-day, state-of-the-practice course on recycled pavement. The course should be available late in 1996.
“Transportation is doing an excellent job, but we could do more,” Sorenson says. “We hope this will persuade people to take a fresh look at the situation.” The policy in FHWA Notice N-5080.93, issued October 6, 1981, remains FHWA’s official stand: “Recycling should be one of the options considered at the design stage of all rehabilitation projects.”
Recent FHWA field evaluations indicate that recycled hot-mix asphalt has performed comparable to conventional HMA, when the recycled HMA was properly designed and constructed. These evaluations will be detailed in a report soon to be released.
“Our members have always supported the use of RAP,” Decker says. “From the hot-mix producer’s point of view, it is sound technology. Many producers say they get better performance with RAP than with virgin material.”
Support is not so universal in areas of Canada, where some municipalities still shun RAP, either from environmental concerns, like leaching; or from a lingering fear that recycled material is not as good as primary material.
“Some municipalities just don’t want RAP in the hot mix,” says John Emery, president of John Emery Geotechnical Engineering of Etobicoke, Ontario, which is near Toronto. A study by the Ontario Hot Mix Producers Association of Mississagua, Ontario, found that as many as 40 percent of municipalities were not permitting use of RAP in hot mix. Overall, the group found 21 percent do not allow aggregate recycling, 11.6 percent allow general use, and the remaining two-thirds allow limited uses.
COLD IN-PLACE RECYCLING
A move to adopt cold in-place recycling for asphalt may change that. Originally developed in Oregon and New Mexico 15 years ago, this method has both technical and strategic advantages. Cold in-place recycling eliminates most of the thermal cracking problems associated with hot systems used in climates like Canada’s.
Emery pointed out the feasibility of taking the cold process from feeder routes to main highways with higher traffic demand and to airports.
“Cold in-place asphalt recycling has been shown to be a technically sound, cost-effective, environmentally friendly method of strengthening and maintaining a wide range of deteriorating asphalt pavements,” he says.
The process involves cold milling, screening, crushing (sizing), mixing, windrowing, pick-up, paving and compaction. The processing trains run from 50 feet to nearly 100 feet in length.
“For suitable pavement sections, cold in-place asphalt recycling results in a ‘new’ pavement at significant life-cycle cost savings compared to conventional flexible pavement reconstruction,” Emery says. Figures of 30 percent to 60 percent are not atypical over a hot-mix asphalt process. In addition, a single lane requirement for the process is involved, minimizing road user inconvenience. And there is significantly less reflective cracking of the overlay, he adds.
In the U.S., a joint committee consisting of representatives from the CIPR industry and owner agencies is working to “develop analysis criteria to aid in the evaluation of aged asphalt pavements and its potential to be rehabilitated via the cold recycle method.”
The CIPR method is one of several the Asphalt Recycling and Reclaiming Association, Annapolis, Md., has studied. Other methods the association has reviewed include cold planing, hot recycling, hot in-place recycling and full depth reclamation. ARRA notes that all of the methods allow use of existing materials with the elimination of disposal problems. The asphalt mix may be improved through changes to the aggregate or asphalt binder, the pavement profile can be corrected and the users’ ride improved. Best of all, from the municipality’s point of view, there often are cost savings.
ARRA warns against looking just at initial cost when assessing recycling options. “Initial cost is important, but the long-term performance, that is, cost effectiveness or life-cycle cost, are of great importance in determining the reclamation method,” ARRA says.
CONCRETE
“Any existing concrete pavement is fully capable of being recycled whether it is mesh, continuous reinforced or plain construction,” assures Clint Solberg, vice president of market development for the American Concrete Pavement Association, Arlington Heights, Ill. He notes that, as far back as 10 years ago, the Atlantic City, N.J., airport was paved with recycled material. Today, in North Dakota and Wisconsin, the course aggregate produced is being successfully used in the mix.
“It’s the green thing to do,” he continues. “Most state highway departments have a policy to maximize the use of materials: if there is no engineering reason not to do it, they recycle it.”
NADC’s Taylor would like to see a more formal arrangement. While he agrees that concrete is a hot item in aggregate-poor areas like the Los Angeles basin or Southern Florida, he says he would like to see states or municipalities mandate a 1 percent or 2 percent use of concrete in sub-base or base material.
Some states, like Hawaii, have mandated or are considering mandating the use of a fraction of glass in paving material, providing some steady markets for glass cullet. When President Bill Clinton approved a measure requiring the U.S. government to use recycled paper, the recycled paper industry experienced a boost. Taylor would like to see the same for recovered concrete C&D debris.
“Transportation has a big effect on its value,” he notes, pointing out that virgin material can be cheaper than recycled in some locations depending on how far it has to be hauled.
One creative solution to the transportation question is a system called Paradigm. Developed by a group of Midwestern firms, the system basically recycles concrete on site, using the old highway as a quarry.
Jim Duit of Duit Construction in Edmond, Okla.; Mike Manatt of Manatt’s Inc., Brooklyn, Iowa; and his cousin Tony Manatt of Wendling Quarries, DeWitt, Iowa, figured there had to be a better way than the traditional breaking of material, hauling it offsite to be crushed, and bringing it back. “It simply made more sense to do it on grade,” Manatt says.
Starting with a 4.8-mile project on
I-80 in Jasper County, Iowa, the system has proved itself in several other locations, including a 187,500-square-yard removal and recycling project on I-30 near Little Rock, Ark.; and a 27-mile job on I-80.
“Capacity of the system varies depending on the amount of steel in the highway and how fine you break the concrete,” Mike Manatt explains. However, under decent conditions an operating speed of 2,000 feet per day would be expected.
Under the Paradigm system, concrete is broken either in half- or full-width. A truck-mounted guillotine breaks the material into 18- to 24-inch chunks. A rhino horn further breaks up the concrete. A crew then can easily pull out rebar or mesh steel, which also is recycled.
A trackhoe loads the rough concrete material into the primary crusher. A secondary crusher or screening operation completes the process.
The Paradigm system (patent pending) is about 10 feet wide and, including the primary and secondary crushers, about 80 feet long. The operation makes no more noise than any other crushing operation, Manatt says.
“In addition to the trucking tonnage saved, you don’t need to find a plant site for crushing on every job,” he says. “The job is not as dirty since you don’t have 15 or 20 trucks hauling material up and down the roads.”
The author is an environmental writer based in Strongsville, Ohio.
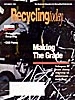
Explore the November 1995 Issue
Check out more from this issue and find your next story to read.
Latest from Recycling Today
- Indiana county awarded $65K recycling grant
- Mixed paper, OCC prices end year on downward trend
- Updated: CAA submits final draft program plan in Oregon
- Enviri names new president of Harsco Environmental business
- Survey outlines ‘monumental challenge’ of plastic packaging collection in UK
- Nippon Steel acknowledges delay in US Steel acquisition attempt
- BASF collaborates to study mechanical plastic recycling
- Commentary: navigating shipping regulations for end-of-life and damaged batteries