After being written off as an industry in decline in the U.S., the integrated steel mill industry is battling back. Will it survive to flourish again? And if it does, what will it look like?
The last decade has not been kind to the domestic steel industry. As many as 30 steel companies have filed for Chapter 11 bankruptcy protection, with some of those eventually closing down operations all together.
These weren’t just the marginal players at the periphery of the industry. Rather, they were and are some of the largest steel companies in the U.S. Such former giants of the steel industry as Bethlehem Steel, National Steel and LTV Steel all ended up filing for bankruptcy, with LTV ultimately taking the final step of closing down its operations.
Smaller companies were also saddled with many of the same industry problems, succumbing to market forces and seeking Chapter 11 protection or closing down.
IN THE DUMPS. Steel companies complained that prices for finished steel were at 20-year lows in 2000 and 2001. Blame often settled on overseas steel companies who shipped finished steel products into the U.S. at prices far lower than what domestic mills considered market prices.
This "dumping" put the hard-hit domestic steel industry at a great disadvantage and helped accelerate the decline of the steel industry in the U.S. While the problems in the steel industry are not limited to integrated steel producers, the difficulties with steel production in the U.S. seem magnified at integrated steel companies.
After heavy debate about the benefits and drawbacks, President Bush signed into law a tariff known as Section 201 in early 2002. This policy sought to remedy many of the problems by slapping a tax on a host of finished steel products that were being shipped into the US.
The tariff, to be enforced for a three-year period, was seen as a way for the domestic steel industry to get its proverbial house in order.
While this policy was initially greeted with relief by the steel industry, at the same time a number of exemptions were included, and more have been added. These exemptions make it more difficult to determine if the overall policy will be enough to lift the U.S. steel industry, or whether the exemptions will work to further cripple the integrated steel industry.
While most domestic steel companies supported the President’s tariff decision, questions remain as to how effective the tariffs have been. According to recently released statistics by the American Iron and Steel Institute (AISI), Washington, total steel imports last year were 32.56 million tons, the fourth highest level in U.S. history, and 8.2 percent higher than 2001’s import figure.
Thomas A. Danjczek, president of the Steel Manufacturers Association, Washington, an association of electric arc furnace (EAF) steel companies, sees the importance of the federal government strengthening and enforcing the 201 steel tariffs passed last year as one step to protect both integrated and EAF mini-mill steel companies.
John Armstrong, a spokesman for U.S. Steel Corp., the large integrated steelmaker based in Pittsburgh, agrees that tariffs have helped improve the markets for both integrated steel companies and their mini-mill competitors. Armstrong says the tariffs have allowed prices to climb from 20-year lows.
RAISING THE STAKES |
Traditionally, automakers—because of their purchasing power—have been able to dictate many of the terms with steel companies. However, an example of a different scenario has unfolded. Recently, AK Steel announced that it would halt shipments to General Motors without some changes to the pricing structure. What brought matters to a head was the public announcement by AK Steel, a Middletown, Ohio, integrated steel maker, that it was filing a complaint against General Motors in an Ohio court that sought to recover at least $25,000 in costs related to increased testing and quality control measures. AK Steel spokesman Alan McCoy said the company estimates the costs to be "in the realm of millions of dollars." McCoy also said AK Steel would continue to fulfill its obligation to GM under the contract despite the dispute. A GM spokesman countered, saying it "will not pay a premium, however characterized, to AK or any other supplier to receive the quality of products that they previously agreed to provide." Regardless of who ends up on top in the dispute between GM and AK Steel, however, experts agree that after years of being the underdog, steelmakers are enjoying the upper hand. |
"What it (Section 201) has done is give integrated steel time to restructure. Also, the lever of tariffs will encourage foreign steel companies outside the United States to rationalize their capacity."
Looking at the steel industry from the other side, the SMA’s Danjczek says that while the tariffs have given the domestic steel industry a period of relief, "it is not a panacea for the import problems."
Says Danjczek, "We would have liked it if the tariffs were across more categories." A review of the tariffs and their exemptions is scheduled for this March.
However, Charles Bradford, a New York-based consultant to the steel industry, is less optimistic about the future of the integrated steel industry. One of the biggest issues that integrated steel companies will have to deal with is the high "legacy costs" (pension and insurance obligations) amassed by a predominately union workforce. The overhead created by these costs makes the finished steel price unprofitable.
In the form of pensions and soaring health care costs for retiring steelworkers, these legacy costs have driven up cash flow obligations for many of the steel companies still standing. Bradford also argues that even with the tariff in place, only a small percentage of the steel that is coming into the country has been adversely affected by the tariff.
STRUCTURAL PROBLEMS. According to Bradford, two other critical problems affect the U.S. steel industry: excess capacity and a strong dollar. While the dollar has weakened as of late, much of the anticipated reduction in capacity has yet to take place. In fact, of the more than 30 steel companies that have filed for bankruptcy protection over the past decade, only a very small number have permanently closed.
The Boston Consulting Group (BCG) echoes this statement on over capacity. In a report released last year, the group noted the following: "Basically, there is considerably more steel-making capacity than there is demand for steel. From 1991 through 2001, worldwide demand for steel grew only 2.1 percent per year. Over the next 10 years, we expect even slower growth, at just 1-1.5 percent per year. There will be significant growth in demand only in Asia (excluding Japan) and Latin America."
While excess capacity is one of the biggest problems confronting the U.S. steel industry, a relative newcomer to the domestic industry has nonetheless joined the fray. This company, International Steel Group, Cleveland, began nearly a year ago when it acquired the idled assets of LTV Steel after that company was shuttered.
The tack that ISG has taken is to take over idled or bankrupt steel operations for far less than the market value. As part of its acquisition of LTV Steel, ISG acquired only the assets and not LTV’s legacy costs.
The company is in the process of completing the acquisition of Bethlehem Steel, also in Chapter 11 bankruptcy protection.
CONSOLIDATE OR DIE. To fans of the Section 201 steel tariff, the law gives the integrated steel industry some breathing room. When the president signed the tariff, supporters of the policy expressed hope that during the three years when the tariff would be in place, the steel industry would be able to consolidate so there would be fewer, but stronger, companies.
The consensus was that the structure of numerous smaller steel companies selling to just a handful of automakers or appliance makers gave the steel industry very little in the way of pricing power. Both mini-mills and integrated steel companies have taken up this notion of consolidation with breathtaking speed.
AK Steel, Middletown, Ohio, and U.S. Steel both made offers to acquire National Steel, which is operating in bankruptcy protection. On the mini-mill side, Nucor Corp., Charlotte, N.C., has snapped up a number of other steel mills, including Birmingham Steel, and the Brazilian-based Gerdau S.A. firm has consolidated mills operating under the Gerdau, Co-Steel and AmeriSteel names, as well as picking up one of the former Birmingham facilities.
Although the tariffs have given integrated steel companies a chance to strengthen their balance sheets, further action might be needed. Shuttering inefficient operations and removing marginal tonnage is an essential step in shaping up the integrated steel industry, analysts agree.
According to the BCG report, the trend toward consolidation "will not culminate in the creation of regional monoliths, but in the formation of companies that will control some 30-40 percent of their respective regions. Such companies will achieve further cost reductions of 4 to 6 percent as compared with today’s players."
While consolidation and capacity reduction are essential moves, the BCG report notes that the steel industry should also look at specialization and downstream migration toward higher-margin businesses. "Those best positioned to pursue this path are the small and midsize players already occupying strategic niches."
However, with ISG’s immediate success in acquiring steel companies for their assets without absorbing the legacy costs, other companies are looking to emulate this strategy.
U.S. Steel’s Armstrong says that if a company had to take on the legacy costs as part of an acquisition, most purchases would not go through. "Now, what is happening is new interest in acquisitions." This new area of cooperation, Armstrong adds, has established a new model for labor/management relations.
ENSURING MARKETS. While the mini-mill sector of the industry has recorded much of the recent growth in the steel industry, many of the integrated mills feel there is still a significant role for their segment. "The key to business is becoming extremely competitive," Armstrong notes. He lists the automotive, appliance and parts of the construction industry as segments where integrated steel producers maintain strong market shares.
Despite this bullish outlook, some in the industry feel that it is only a matter of time before the lower cost producers take more of that share away. However, in the short term, some proponents of the integrated steel industry point to soaring ferrous scrap prices as a cautionary tale for the segment of the steel industry that is almost exclusively beholden to ferrous scrap as a raw material.
Another concern for integrated steelmakers is that while the auto industry, one of the largest end markets for the integrated segment, has been strong, many feel demand will start to cool. With commercial construction yet to show any noticeable sign of a pickup, there could be a sharp drop in the demand for steel later this year.
With many of the integrated steel companies having staked out markets in the automotive, appliance and some commercial construction categories, the short-term success of the remaining integrated steelmakers in the U.S. is increasingly dependent on these sectors. While the automotive industry has been fairly strong over the past several years, the construction industry has been more tepid.
The ability of a few remaining integrated steelmakers to bargain with the high-volume buyers in these markets is also becoming an issue.
In the past year AK Steel and U.S. Steel Corp. have raised contract prices on steel as a falloff in industry capacity and tariffs on imports of foreign steel helped prices rebound from 30-year lows.
Now, with ISG completing the acquisition of Bethlehem Steel, and bankrupt National Steel being acquired by either AK Steel or U.S. Steel, a shift in power from automakers to steelmakers could grow even stronger.
"Once the consolidation does go through and you end up with more or less three big integrated steel producers, they will be able to have much better pricing control," says HSBC analyst Peter Bures in an article by Reuters. "So basically the power will be shifted from the automakers to the steelmakers."
Nancy Gravatt, a spokeswoman from the American Iron & Steel Institute, agrees that the consolidation wave taking place in both the integrated and EAF steel sectors is "helping with negotiations on the customer side." Further, "the consolidation is helping the remaining steel companies improve their visibility in the financial community," she adds.
Over the past decade, as the domestic steel industry was hit with steel prices that dropped to 20-year lows, financial institutions did not deem the industry as a place for growth. Integrated steel companies did not have access to capacity to invest in new technologies and new systems to make themselves more competitive.
Despite the inability to access capital, Gravall says that the integrated steel industry has been very aggressive with its manufacturing technology.
Looking forward to a pending review of the tariffs, Gravall says that right now only 5 percent of the domestic steel consumed in this country is affected by the tariffs. This, she hopes, will minimize any additional exemptions to the tariffs.
The Boston Consulting Group, in its report, states that the best model to return the steel industry to an area of value creation is through a "division of labor approach based on deconstruction and global networking. In this approach, a low-cost offshore producer of slabs might collaborate with a highly differentiated conversion specialist, reducing the cost of steel product by 10-20 percent."
Despite the great promise of this approach, BCG notes that no company has yet made a significant move in this direction because of the high costs of closing upstream production capacity, the fear of a supply shortage, or the risk of political opposition.
The author, senior editor and Internet editor of Recycling Today, can be contacted at dsandoval@RecyclingToday.com.
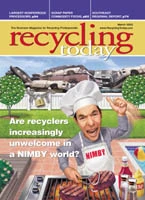
Explore the March 2003 Issue
Check out more from this issue and find your next story to read.
Latest from Recycling Today
- Green Cubes unveils forklift battery line
- Rebar association points to trade turmoil
- LumiCup offers single-use plastic alternative
- European project yields recycled-content ABS
- ICM to host colocated events in Shanghai
- Astera runs into NIMBY concerns in Colorado
- ReMA opposes European efforts seeking export restrictions for recyclables
- Fresh Perspective: Raj Bagaria