PET depolymerization. A patent application filed by the University of Wyoming and Washington State University describes a high-efficiency, low-energy and environmentally friendly method to recycle polyethylene terephthalate (PET) scrap.
Current methods of PET recycling have drawbacks. According to the patent application, separating and classifying plastics can be hurdles to efficient mechanical recycling; chemical recycling relies on toxic organic solvents; and incineration releases harmful gases into the atmosphere.
The patent application says its described method works by attacking the –O– ester linkage in PET. This is accomplished by loading a supercritical, high-temperature reactor with PET and deionized water. CO2 is injected into the reactor, and then the reactor is heated to a reaction temperature for a specified time.
The application explores the relative merits of varying input levels, investigating feedstock weight ratios of PET to deionized water ranging from 1:10 to 1:30, injection pressures of up to 700 psi, temperatures as high as 464 F and time intervals ranging from 15 minutes to two hours.
The results showed that CO2 can be an effective hydrolysis catalyst for PET. After the reactor tank returned to room temperature and was unsealed, terephthalic acid and ethylene glycol, which may be liquid products, solid products or both, were collected from the reactor.
The patent application notes that the degradation ratio of the PET can reach as high as 100 percent with a PET-to-water feedstock weight ratio of 1:30 at 428 F, with an initial CO2 pressure of 700 psi for 1.5 hours.
As an added benefit, experiments found that the recovered CO2 could be used for subsequent reaction cycles, reducing consumption of input materials.
Patent application 20210340351; published Dec. 16, 2021
Washing and separation. The U.S. Patent and Trademark Office has awarded a patent to Previero N. Srl, Anzano del Parco, Italy, for a system and method for washing plastic flakes that is more efficient at removing metal contamination than previous technologies. According to the patent, the invention also is structurally and functionally simpler than traditional systems, produces more usable recovered plastic and uses less washing fluid and energy.
Hydrocyclone units often are used to separate postconsumer plastic pieces from heavy contaminants, such as metal. The vortex the units generate causes the plastics to separate from the contaminants, which drop to the bottom of the tank. However, such systems might not remove contaminants that adhere to the plastics, requiring the use of a washing unit downstream. This setup can be structurally and functionally complex to create and manage.

The apparatus described in the patent features a washing container with an inlet and an outlet, as well as at least one vertical rotor shaft with a series of impeller units mounted one above the other. Each impeller unit comprises a group of blades tilted in the opposite direction from the blades of the impeller above or below it. The blades create a turbulent stirring action to mechanically remove contaminants from pieces of plastic that are in a washing fluid.
“The tilt of the blades and the rotation speed of the stirring device are chosen carefully to generate an upward thrusting action to maintain the plastics material with a specific weight that is greater than the specific weight of the fluid in a floating condition,” the patent states. “The plastics material is retained inside the container for sufficient time to obtain a desired degree of purity and decontamination for the plastics material, after which it is evacuated by controlled overflow.”
The method and apparatus “enable high levels of purity to be obtained in the recovered plastics material in reduced time, owing to the immediate continuous removal of the contaminants from the washing container,” the patent states.
Patent 11,179,729; issued Nov. 23, 2021
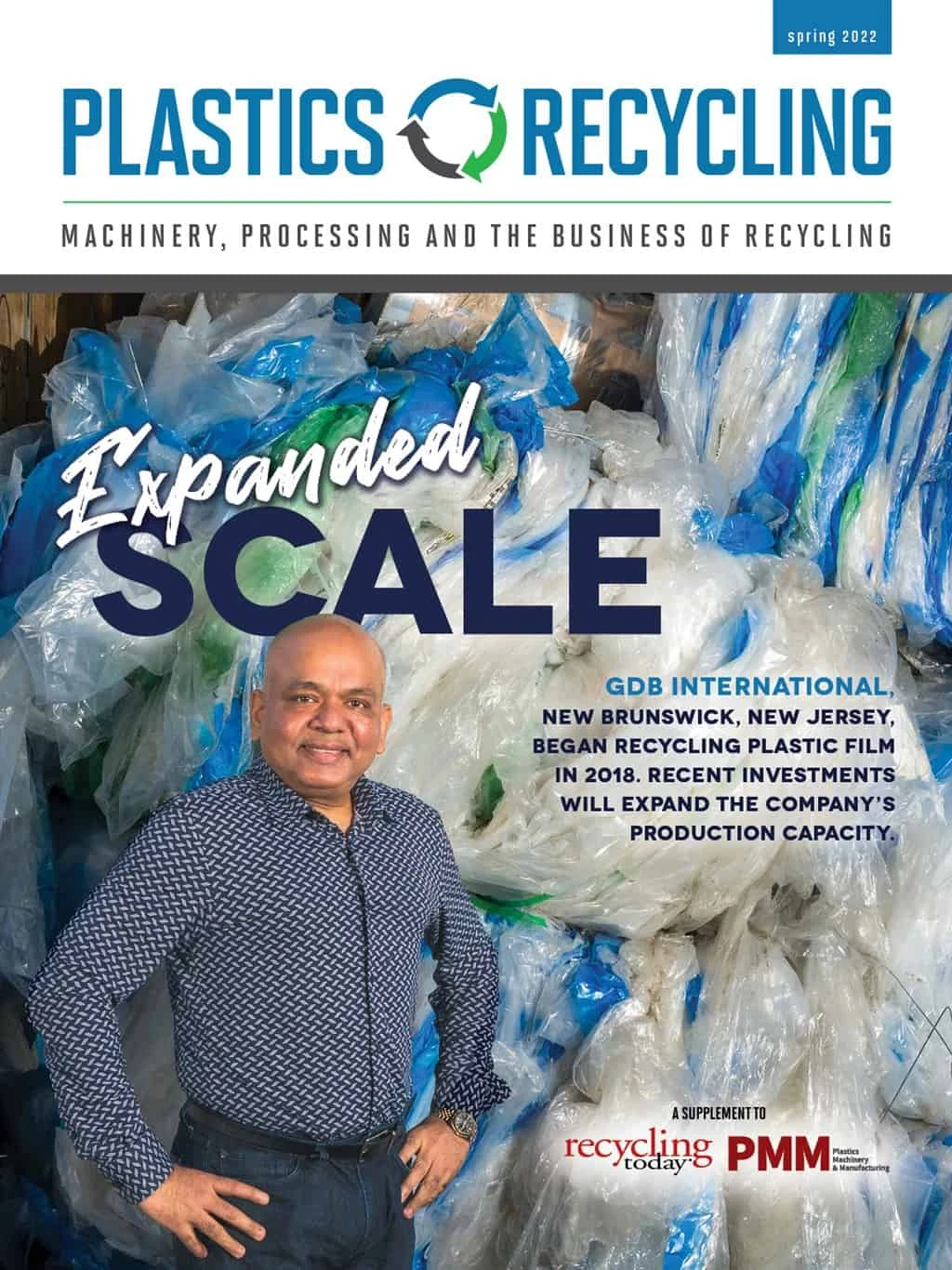
Explore the Spring 2022 Plastics Recycling Issue
Check out more from this issue and find your next story to read.
Latest from Recycling Today
- AF&PA report shows decrease in packaging paper shipments
- GreenMantra names new CEO
- Agilyx says Styrenyx technology reduces carbon footprint in styrene production
- SABIC’s Trucircle PE used for greenhouse roofing
- Hydro to add wire rod casthouse in Norway
- Hindalco to invest in copper, aluminum business in India
- Recycled steel price crosses $500 per ton threshold
- Smithers report looks at PCR plastic’s near-term prospects