
BHS has been on a continuous multiyear journey to industrialize the process of sorting and purifying recyclables. The latest evolution is the introduction of the Automated Processing System. The automated system reduces CAPEX, eliminates labor, and provides high recovery rates with customizable purity levels by utilizing intelligent decision-making programs combined with real-time data.
The Max-AI® Visual Identification System (VIS) captures the material stream’s composition as it enters its first sorting stage, an AQC-2 robotic sorter. That data is shared with the BHS Total Intelligence Platform while this sorting stage removes any oversize contaminants. The stream then passes through a magnetic separator, removing all ferrous material.
The material composition data guides the system as it autonomously determines the commodity recovery material targets and sequencing based upon operator defined parameters.
Batch sorting
The material stream is conveyed to the systems first bunker. It aggregates there until processing begins. Once the system identifies enough material in the bunker it releases it for further recovery.
The stream is conveyed to a NRT SpydIR® optical sorter equipped with Max AI® VIS and a NRT MetalDirector™. This combination allows material to be identified by shape, color and molecular composition. This advanced detection system allows for the sorting of complex materials throughout a variety of stream scenarios.
Here, the initially prioritized material is ejected. The ejected stream then passes through another Max-AI® AQC-2 robotic sorter to remove any potential contamination before the material is deposited into its respective commodity bunker.
The remainder of the original stream is conveyed to the system’s second bunker, to await further processing.
Bunker one material continues processing until bunker two fills. Once bunker two is full, the system allows bunker one to fill and begins processing material from bunker two. As material is released from bunker two it is conveyed to the same SpydIR® optical sorter system, which begins recovery of the next prioritized material.
The process continues until all targeted materials have been recovered. As the recovered commodity bunkers fill, they also are sequenced to be released for baling.
Industrialized recycling
Creating the continuous flow, loop processing allows the system to work with little human intervention. Each step in the process is monitored through the BHS Total Intelligence Platform. This provides the plant operator with clear visibility.
Through the plant’s HMI system, the operator can see if any issues arise. They can also monitor material composition, fill rates, recovery rates and production rates. The system operates as an autonomous sub-system within the MRF and can run independently 24/7.
By processing a range of materials through one highly-advanced, redundant separation line, plant operators can reduce the total number of magnets, optical sorters and identification cameras needed throughout the plant. This reduces CAPEX as well as ongoing maintenance.
To learn more about the BHS Autonomous Processing System please contact the BHS sales team at sales@bhsequip.com.
Sponsored Content
Redefining Wire Processing Standards
In nonferrous wire and cable processing, SWEED balances proven performance with ongoing innovation. From standard systems to tailored solutions, we focus on efficient recovery and practical design. By continually refining our equipment and introducing new technology, we quietly shape the industry—one advancement at a time.
Sponsored Content
Redefining Wire Processing Standards
In nonferrous wire and cable processing, SWEED balances proven performance with ongoing innovation. From standard systems to tailored solutions, we focus on efficient recovery and practical design. By continually refining our equipment and introducing new technology, we quietly shape the industry—one advancement at a time.
Sponsored Content
Redefining Wire Processing Standards
In nonferrous wire and cable processing, SWEED balances proven performance with ongoing innovation. From standard systems to tailored solutions, we focus on efficient recovery and practical design. By continually refining our equipment and introducing new technology, we quietly shape the industry—one advancement at a time.
Sponsored Content
Redefining Wire Processing Standards
In nonferrous wire and cable processing, SWEED balances proven performance with ongoing innovation. From standard systems to tailored solutions, we focus on efficient recovery and practical design. By continually refining our equipment and introducing new technology, we quietly shape the industry—one advancement at a time.
Sponsored Content
Redefining Wire Processing Standards
In nonferrous wire and cable processing, SWEED balances proven performance with ongoing innovation. From standard systems to tailored solutions, we focus on efficient recovery and practical design. By continually refining our equipment and introducing new technology, we quietly shape the industry—one advancement at a time.
Sponsored Content
Redefining Wire Processing Standards
In nonferrous wire and cable processing, SWEED balances proven performance with ongoing innovation. From standard systems to tailored solutions, we focus on efficient recovery and practical design. By continually refining our equipment and introducing new technology, we quietly shape the industry—one advancement at a time.
Sponsored Content
Redefining Wire Processing Standards
In nonferrous wire and cable processing, SWEED balances proven performance with ongoing innovation. From standard systems to tailored solutions, we focus on efficient recovery and practical design. By continually refining our equipment and introducing new technology, we quietly shape the industry—one advancement at a time.

541-485-0999
Get curated news on YOUR industry.
Enter your email to receive our newsletters.
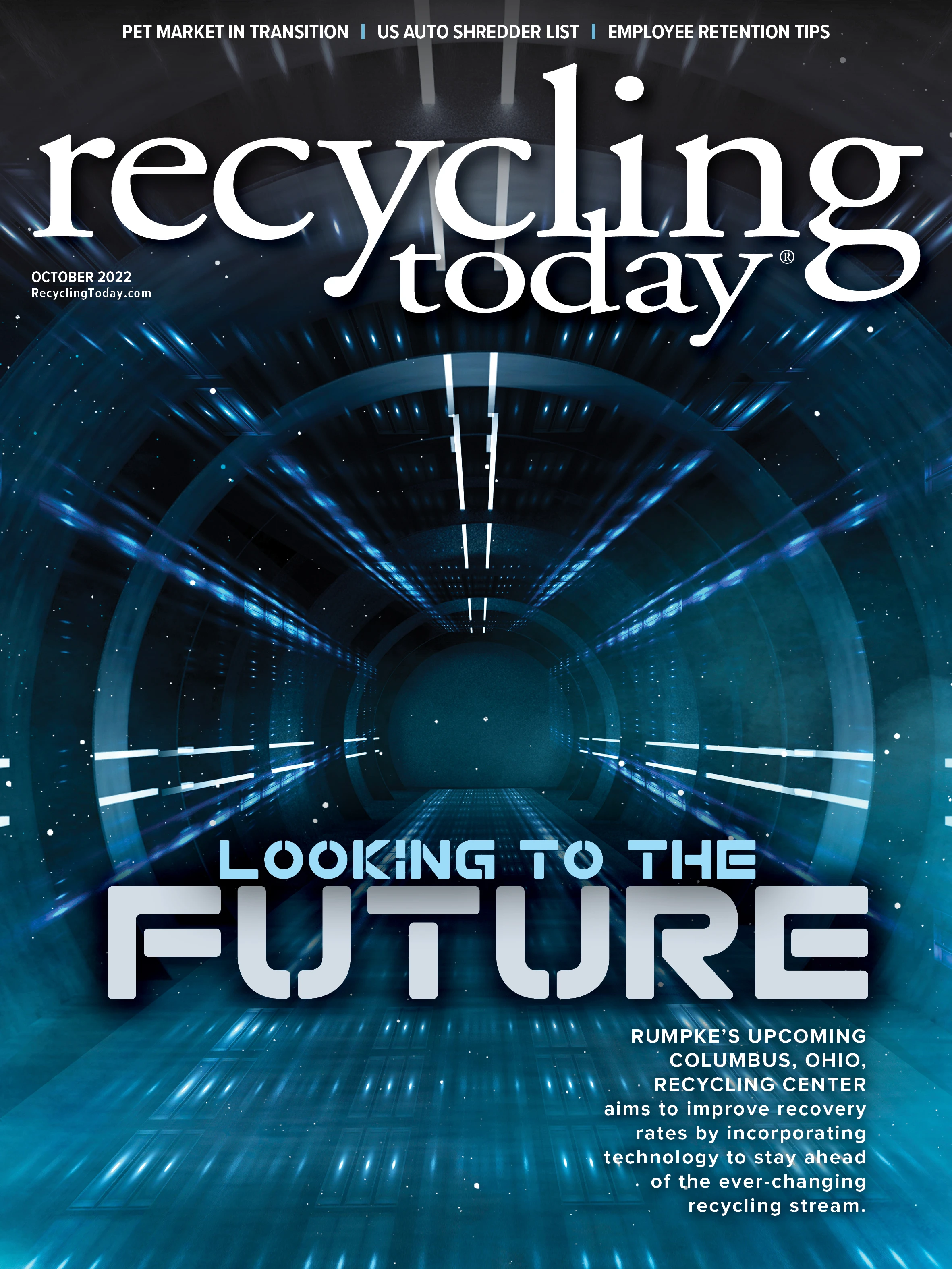
Explore the October 2022 Issue
Check out more from this issue and find your next story to read.
Latest from Recycling Today
- APR, RecyClass release partnership progress report
- Clearpoint Recycling, Enviroo sign PET supply contract
- Invista expanding ISCC Plus certification program
- Redwood partnership targets recycling of medium-format batteries
- Enfinite forms Hazardous & Specialty Waste Management Council
- Combined DRS, EPR legislation introduced in Rhode Island
- Eureka Recycling starts up newly upgraded MRF
- Reconomy Close the Gap campaign highlights need for circularity