The quest to find better ways to do the myriad of tasks around a scrap yard is never-ending. For a long-time suburban Washington, D.C., operation, that quest involves new, reliable and well-maintained heavy equipment—and some unique uses for that equipment.
The company receives material from other dealers, peddlers and salvage companies located within a 100-mile radius of its facility.
"Like everyone else, we’re constantly looking at a better way, a new way," says Bill Bukevicz, executive vice president of Davis Industries in Lorton, Va. "It never stops, but right now we’re pleased with the way things are going."
DEALING FOR DEALERS |
Competition by equipment makers to line up regional dealers has been noticeable in the improved scrap market of 2003 and 2004. U.S.-based Caterpillar has a long-established dealer network in place here, as does German equipment maker Liebherr, which has had a long-standing relationship with master distributor Republic Equipment in Charlotte, N.C. The Fuchs line of scrap handlers made in Germany is now part of the U.S.-based Terex family of companies. The German-made machines are distributed through a Fuchs Terex office based in Wilmington, N.C. And for the past several years, German equipment maker Sennebogen has been operating a U.S.-based distributor/subsidiary in Charlotte, N.C. Other competitors remaining in the market include LBX (Link-Belt), based in Lexington, Ky., John Deere Co., based in Moline, Ill., and the Illinois-based U.S. office of Japanese equipment maker Komatsu. Sierra International Machinery Inc. in Bakersfield, Calif., is now offering Italian-made material handlers from the Tabarelli line. Another Italian equipment maker, Colmar, is offering scrap handlers through its U.S. headquarters based in North Tonawanda, N.Y. Among some of the recent moves, Florida’s Briggs Equipment has agreed to carry the Sennebogen line for its customers in the Sunshine State. Fuchs pumped up its dealer network in 2003 with several high-profile agreements, including adding Mitchell Crane and Continental Equipment in Texas and Colton Equipment in California. —Brian Taylor |
NEW ON THE JOB. Among the things that Bukevicz can be pleased with has been the operation of the medium-sized yard’s Vezzani 1,760-ton shear, purchased about one year ago. While the shear represents a major jump in capacity from its old 1,000-ton model, Bukevicz is quick to point out that effectiveness—and profitability—of the shear is partially dependent on the process involved in getting the scrap to the shear.
"Our old shear had a 20-foot charging bed, so we had to prep material down to 19 feet to use it," he recalls. "We had to use two people—a crane operator and a shear operator—who could only communicate by radio."
Today, however, operations are different—and more efficient—at Davis Industries. Thanks to a larger charging bed, scrap up to 60 feet in length quickly becomes prepared steel. And thanks to the versatility of one of Davis’ two Caterpillar 350 material handlers, the operation involved in that familiar transformation is done at a lower cost.
The grapple-equipped material handler feeds the shear, but that process now takes just one operator. That operator sits atop a 40-foot tower and uses remote controls to operate the Caterpillar machine. That lofty perch allows him to see into the gravity-fed shear and eliminates the need for a separate shear operator.
To improve his visibility, the operator looks straight at the material handler, hence the controls are backwards. That hasn’t been a problem. Neither has an inability to "feel" the weight of the load. Use of a grapple instead of a magnet helps in that process.
"Not only does the new Cat machine give us reliability and productivity, we have a versatile atmosphere," says Bukevicz. "If operations at the shear are slow, we can move the material handler to help in other areas of the yard."
The company also processes some 4,000 vehicles per month as part of the material stream heading to its shredder.
ROLLING STOCK. Often, the 350 assists another Cat 350 material handler that is used to unload customer trucks. That latter machine came equipped from the dealer with a generator and a 71-inch magnet.
One possible use of that machine is to assist the larger Caterpillar 365B material handler Davis Industries recently purchased. The 365B is used exclusively to load the more than 100 rail cars that leave the business each month. Equipped with a 76-inch magnet and the necessary generator, the 365B handles the chore with ease, Bukevicz says.
"We’re geared to move rail cars," notes Bukevicz. "We have a shuttle wagon, two tracks and can handle up to 14 cars. The 365B has the capacity and reach to make that process smoother than it’s ever been."
Besides material handlers, a workhorse machine in any scrap yard is the wheel loader. At Davis Industries, two Caterpillar 950 wheel loaders are on the go continuously moving materials around the yard, as well as loading containers with nonferrous metals and byproducts bound for a landfill.
Skid steers have also been added to the Davis Industries fleet. The additions were the result of a conversation Bukevicz and CEO Ben Ettleman had with colleagues at an industry convention.
"They told us that they had recently added Caterpillar skid steer loaders to their operation and found them to be invaluable," recalls Bukevicz. "They were particularly impressed with the versatility provided by the variety of work tools available."
Bukevicz and Ettleman contacted their local dealer and arranged a demonstration. Quickly, Davis Industries purchased two Caterpillar 248 skid steer loaders. They had each equipped with a grapple bucket and purchased a broom that could be used on either machine. One is used as a "general workhorse" around the yard, and the other spends its time primarily loading intermodal containers with nonferrous metals.
ROOM FOR MORE? "We’ve been impressed with the work these machines can do and I’m sure we’ll be adding more work tools as we start to appreciate the value they add to the operation," says Bukevicz.
To look after this diverse fleet of equipment and the variety of machinery in the yard, Davis Industries employs just one technician. He handles hydraulic inspections and general maintenance. The firm relies on Alban, its dealer, to keep the equipment running.
"We use the dealership to do everything, even the oil changes," says Bukevicz. "That quick and responsive service is the main reason we purchased the Cat machines. On top of that, we know that parts will always be available."
The author submitted this story on behalf of Caterpillar Inc.
Get curated news on YOUR industry.
Enter your email to receive our newsletters.
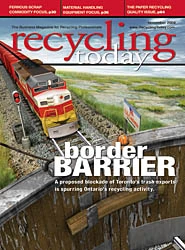
Explore the November 2004 Issue
Check out more from this issue and find your next story to read.
Latest from Recycling Today
- ReMA opposes European efforts seeking export restrictions for recyclables
- Fresh Perspective: Raj Bagaria
- Saica announces plans for second US site
- Update: Novelis produces first aluminum coil made fully from recycled end-of-life automotive scrap
- Aimplas doubles online course offerings
- Radius to be acquired by Toyota subsidiary
- Algoma EAF to start in April
- Erema sees strong demand for high-volume PET systems