
With annual production capacity of more than 200 million pounds across its three production facilities and the ability to process materials of widely ranging bulk densities simultaneously to create finished compounds with fairly tight specifications, Ultra- Poly Corp., headquartered in Portland, Pennsylvania, is one of the largest asset-based plastics recycling companies in the United States.
To reach this point, Kevin Cronin, vice president of sustainability and R&D, says Ultra-Poly designs, engineers and builds all of its equipment in-house. “We have developed proprietary processes and equipment that allow us to efficiently process streams that others cannot,” he says. “Our knowledge of polymers and plastics manufacturing in general allows us to continually produce branded products from changing raw material streams.”
EARLY DAYS TO NOW
Alan LaFiura, who serves as chairman of Ultra-Poly, founded the company in Newark, New Jersey, in 1974 to provide toll processing of LDPE (low-density polyethylene) film scrap.
Later in that decade, the company moved to Hackettstown, New Jersey, expanding its processing capacity and capabilities further. Ultra-Poly then began purchasing LDPE scrap for compounding and sale under the Ultra-Poly brand of recycled resin.
Today, toll processing accounts for a “reasonable percentage” of Ultra-Poly’s business, Cronin says, adding that it amounts to 30 percent to 40 percent of the company’s overall material volume.
Ultra-Poly even performs embedded toll processing at a client’s plant. Cronin says this operation serves one of Ultra-Poly’s largest consumers, reprocessing some engineering grade resins. “It made logistical sense to co-locate,” he says.
The company also progressed from processing LDPE film into processing all types of polyethylene (PE) scrap as well as polypropylene (PP) scrap in virtually any form, from baled fibers to car-sized purgings. “It was a natural progression within the olefin chain,” Cronin says. “We had lots of demand pulling us in that direction,” he says of the company’s expansion into PP scrap processing. “As recycling took on a stronger and more strategic position in the thought processes of some companies, they were looking at polypropylene.”
Today, roughly 50 percent of the resins Ultra-Poly processes are PP, while 50 percent are PE.

“We’ve worked very hard to diversify our supply and customer base, and we operate in a broad range of plastics related markets,” Cronin says. “We grew up in postindustrial film recycling, but today we purchase postindustrial scrap in every form from a wide variety of industries, as well as postconsumer film [and] baled No. 2 bottles.”
He says Ultra-Poly serves a wide variety of consuming markets, including automotive, packaging, storage, dunnage, industrial and consumer goods.
Ultra-Poly’s product marketing efforts “focus on marrying the right material at the right price point with the right application,” Cronin says.
PURPOSE BUILT
Ultra-Poly’s Berwick, Pennsylvania, plant was purpose built to tackle a challenging application: the reclamation of postconsumer film used in the oil and gas industry. “It is the only facility of its kind in the U.S.,” Cronin says, adding that it also provides additional processing capacity for the company’s core business.

Specifically, Ultra-Poly is processing 200-square-foot-by-200-square-foot pads made of medium- to high-density PE film with a minimum thickness of 40 mils that are used to line containment areas around natural gas wellheads that have proliferated in certain areas of the country in light of advances in hydraulic fracturing.
Prior to Ultra-Poly establishing this facility, the pads were cut into three or four strips prior to being buried in landfills, Cronin says. However, the material was problematic for landfills because it caused instability and trapped landfill gas.
He says Ultra-Poly worked with the state of Pennsylvania, which is home to part of the Marcellus Shale formation, to bring in this film for recycling.
The company’s Berwick plant uses a dry process Ultra-Poly developed to clean the film, removing contaminants using a mechanical process.

This challenging application is made even more challenging by the current state of PE markets, Cronin says. “Where PE pricing is at right now, there is not a lot of profitability currently,” he says. However, Ultra-Poly continues to process the material.
The good news is that the company’s process can be used for other postcommercial and postconsumer scrap streams that require cleaning and separation, Cronin says. “We have a great deal of flexibility to deal with streams that others find difficult and that would require wet processing,” he adds.
Agricultural film, lumber wrap and injection-molded parts and other films used in the oil and gas industry are examples of the additional material streams that Ultra-Poly’s Berwick plant can process.
Cronin says the black pellets Ultra-Poly produces using the two extruders it operates in Berwick are used to manufacture garden edging and other products used in the landscape industry.
While he says the “holy grail” would be to use the recycled pellets the company produces here to manufacture new pad liners, the strict requirements of this application make that difficult.
Cronin adds that Ultra-Poly continues to invest in the plant to further refine its technology. This philosophy is in action across all of the company’s plants.
A WORK IN PROGRESS
“We look at our manufacturing capacity as a work in progress,” he says. “We are never quite satisfied with what we are doing.”
The company is currently preparing to install a new shredder at its Portland plant that will allow it to expand production on its newest extrusion line by 30 percent.
“We’ve worked very hard to diversify our supply and customer base, and we operate in a broad range of plastics related markets.” – Kevin Cronin, Ultra-Poly
“We have a disciplined approach to upgrading our facilities,” Cronin adds.
That discipline extends to designing its own processing equipment. “Necessity is the mother of invention,” Cronin says of what prompted Ultra-Poly to begin designing and building much of its own equipment. “We couldn’t find equipment to do what we wanted it to do.”
Ultra-Poly hasn’t purchased an off-the-shelf extruder in at least 10 years, he says, adding that the company may buy an older machine and modify it before it goes into service at one of its plants.
He says this area of the business “is driven by the need to improve the quality of our products and to improve the efficiencies of how we operate.”
Ultra-Poly currently is building a guillotine shear for rolls and nonwoven fabrics. Cronin says the machine will be unlike those commercially available in power and robustness. “Some may look at it and say it looks overengineered,” he says. “It is engineered exactly how we want it based on years of wearing out other ones.”
He adds that Ultra-Poly is in the process of adding entirely new processing capabilities as a result of its Extended Loop Recycling initiative. (See sidebar below.) “We are also continuing to invest in upgrading key existing production capabilities to keep pace with growth and improve efficiencies.”
POTENTIAL FOR GROWTH
Despite the downturn in pricing for many recycled resins, Cronin says demand for recycled plastics remains strong in some industry segments.
“A common misconception is that the end consumer is the major factor driving demand for recycled content in their products,” he says. “While this is a factor, in our view the main drivers for recycled materials are quality and price. Well-produced recycled resins replace prime resin in many market segments and reduce manufacturing costs without sacrificing performance, and for that there will always be demand.”
Cronin says Ultra-Poly continues to look for new opportunities to grow its core business and to expand its business model and effect in the industry.
“We are indeed bullish on the future of our industry,” he says. “We expect to grow a little faster than the industry itself.”
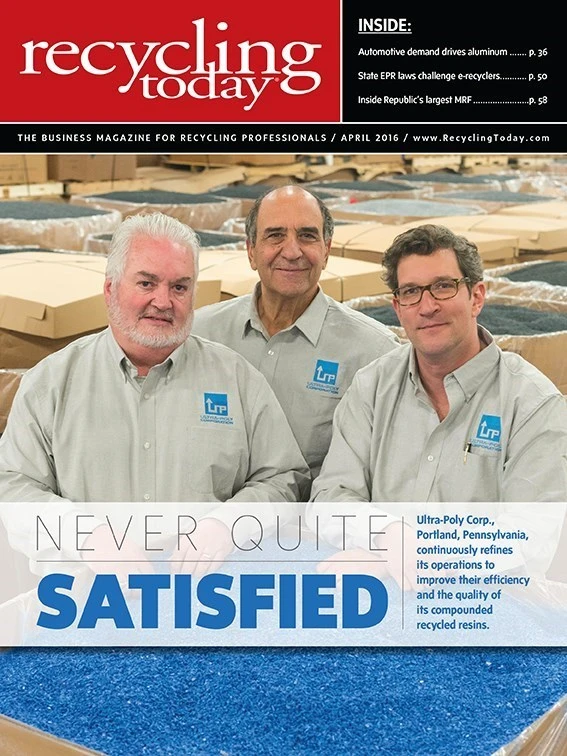
Explore the April 2016 Issue
Check out more from this issue and find your next story to read.
Latest from Recycling Today
- European Commission publishes material stream requests for non-OECD country applications
- Shapiro receives NATM Innovation Award for Sustainability Excellence
- EAF mill underway in California
- Constellium recycled feedstock rate holds steady in 2024
- Lamor buys remaining shares in plastic scrap-to-oil facility
- ReMA supports policy measures facilitating collection, safety and proper end-of-life management of small, medium batteries
- Balcones Recycling launches commercial recycling services in Phoenix
- Resynergi, Lummus Technology launch modular plastic recycling solution