
Proposals that call for minimum recycled content in consumer goods packaging, including food packaging, continue to circulate. Other proposals call for increasing recovery rates for consumer goods packaging to reduce plastic waste and increase the supply of feedstock for recycling. These proposals, as well as consumer demand, collectively are applying pressure on companies in the entire consumer packaged goods (CPG) industry value chain, including recyclers, packaging manufacturers and consumer goods manufacturers, to find suitable recycled plastic sources.
But simply legislating for increased recycled plastic content in CPG products does not address the requirement that the recycled plastic must be safe and legally compliant for its intended use in those products. This issue is of particular concern for postconsumer recycled plastics used by companies that manufacture food and food-contact materials, as well as other products such as cosmetics.
One source of guidance applicable to recycled polymers used in food-contact applications and that also can serve as a reference for recycled polymers used in other packaging or products is the U.S. Food and Drug Administration’s (FDA’s) Guidance for Industry: Use of Recycled Plastics in Food Packaging (Recycled Plastics Guidance), available at http://bit.ly/fdaguidancedocuments. This article (1) reviews the way that FDA regulates recycled plastic used in food-contact applications, (2) explains how to comply with FDA’s Recycled Plastics Guidance and (3) comments on other considerations that could be relevant for CPG companies incorporating recycled plastic into their products.
FDA’s regulation of recycled plastics
Two questions are critical for recycled plastic used in food-contact applications: is the plastic used in conformity with an applicable FDA clearance or exempt from the need for a clearance and does it possess a purity suitable for its intended use? Compliance with these requirements is assessed using the legal framework Congress established in the U.S. Federal Food, Drug and Cosmetic Act (FDCA) for food additives. Specifically, Section 201(s) of the FDCA defines the term “food additive” to include any substance that, under its intended conditions of use, could reasonably be expected to result in it becoming a component of food. Substances in contact with food (including food packaging), and those reasonably expected to become a component of food, are therefore food additives.
Substances qualifying as food additives not already authorized for their intended use are subject to premarket review by FDA under Section 409 of the FDCA. Substances that are the subject of an effective Food Contact Notification have undergone FDA premarket review and so have substances cleared in FDA’s indirect food additive regulations. Many exemptions to the food additive definition exist. These include (but are not limited to) exemptions for substances that are (1) generally recognized as safe, (2) prior sanctioned and (3) not reasonably expected to migrate to food under their intended conditions of use. These exempt substances are not required to undergo review by FDA before being placed on the market.
As noted above, all plastic also must be of a purity suitable for its intended use. This requirement flows from the general safety clause in section 409(c)(3)(A) of the FDCA and FDA’s Good Manufacturing Practices regulation for food-contact materials. In practical terms, this means that food-contact materials cannot contain any substances that could be injurious to human health, including impurities or other contaminants that could be introduced in the life cycle and recycling stream of a product.
Recycled Plastics Guidance document
FDA’s Recycled Plastics Guidance discusses the relevant criteria that the agency has established to determine whether recycled polymers that are incorporated into food-contact applications are compliant. While guidance documents, as a matter of law, are not binding, they do represent the government’s current views and thinking on a particular subject. FDA’s guidance document has become an influential and important resource, and companies often expect or require recycled polymers to comply with the provisions outlined in FDA’s guidance.
Forms of recycling and feedstock selection dictate requirements. FDA’s Recycled Plastics Guidance identifies and defines three types of recycling processes based on nomenclature developed by the Environmental Protection Agency in 1991: primary recycling, secondary recycling and tertiary recycling. Specifically, FDA considers primary recycling to refer to preconsumer scrap (i.e., industrial scrap), whereas secondary recycling refers to physical processing of postconsumer plastic, while tertiary recycling, which also is known as chemical recycling, involves breaking down the plastic to its starting materials (i.e., monomers) and regenerating the purified materials into “new” polymers.
The steps a company must take to establish FDA compliance for recycled plastics are dictated by the form of the recycling used and the source of the recycled material. Answering the two critical questions mentioned above is a more straightforward exercise for plastic derived from primary recycling. This is because (1) the source of the plastic can be controlled to ensure that it is compositionally compliant and (2) there is no opportunity to introduce contaminants from consumer misuse or from the postconsumer recycling stream. For this reason, the so-called surrogate contaminant and challenge testing that is discussed below is not needed.
FDA generally expects additional steps to be taken to ensure postconsumer plastic that is subject to secondary or tertiary recycling is suitable for use in food-contact applications. First, source control and sorting should be a focus, particularly for secondary recycling, to ensure the feedstock is derived from containers that were initially used to hold food. This helps to confirm the plastic is “food grade” in that it does not contain unauthorized components, including adjuvants. In addition, sorting techniques should be employed to ensure different polymer types are properly separated. This is important not only to ensure that the technical properties of the plastic are not unduly compromised during recycling but also that unauthorized adjuvants are not incorporated into the recycled plastic, as many adjuvants are only authorized by FDA for use in certain polymers or at certain use levels in a given polymer.
For secondary and most tertiary recycling processes, FDA expects companies to address potential contamination from consumer misuse (e.g., storing pesticide chemicals in an empty food container) or the presence of nonfood containers in feedstock through surrogate contaminant and challenge testing.
Surrogate contaminant and challenge testing for secondary and tertiary recycling. FDA believes that the possibility of exposure to chemical contaminants from secondary and tertiary recycled materials is low but is aware that the possibility for contamination exists. Thus, FDA recommends testing using “surrogate” chemicals, which are intended to mimic common potential contaminants, should be performed to “challenge” the ability of the recycling process remove the contaminants. Specifically, the recommended testing involves intentional contamination of the polymer of interest by soaking it in a cocktail of the surrogate contaminants, followed by storage and then running the contaminated polymer through the recycling process and measuring the levels of the contaminants thereafter.
FDA generally takes the position that a recycling process adequately removes contaminants if challenge testing supports a conclusion that the dietary concentration of the surrogate contaminants will be 0.5 parts per billion (ppb), corresponding to an estimated daily intake of 1.5 micrograms per person per day or less. In other words, FDA is unlikely to raise suitable purity concerns for the polymer (at least with respect to potential concerns associated with the use of recycled feedstock) if the dietary concentration to the contaminant is reduced to 0.5 ppb or less.
Establishing the dietary concentration to the surrogate contaminant can be assessed using various methods. By way of example, one typically begins such an assessment by using FDA’s model parameters that assume 100 percent of the residual contaminant (as quantified in the challenge testing) will migrate to food and, consequently, enter the diet. If these calculations do not demonstrate that the contaminant will enter the diet at acceptably small levels, then one may consider other options, including migration modeling, migration studies, dilution of the polymer with virgin material or the use of a functional barrier.
Special considerations for recycled polyethylene terephthalate (rPET). Much of FDA’s Recycled Plastics Guidance is geared toward rPET because PET is widely used in food-contact applications and FDA thoroughly studied information about rPET before it finalized the guidance.
For example, FDA was provided with information that all PET used in the U.S. is compositionally complaint with applicable FDA requirements. In addition, FDA has reviewed sufficient data to conclude that heavy metals salts do not readily sorb into PET and are readily washed out of PET. Therefore, use of a heavy metal salt is not required in surrogate testing for a PET recycling process. Finally, FDA has concluded that all tertiary recycling processes sufficiently remove potential contaminants in PET such that the surrogate contaminant testing data is not needed in the context of a no objection letter submission for PET that is subject to tertiary recycling.
Collectively, the existence of this information and its review by FDA has materially lessened the demands on companies that wish to use recycled PET in food-contact applications.
FDA’s voluntary no objection letter program
FDA also has established a voluntary process whereby a company can submit a summary of its recycling process. The agency will review the efficacy of the process to determine whether it results in the creation of a recycled polymer that is acceptable for its intended use. If FDA determines the process is acceptable, it will issue a “no objection letter.” Importantly, no objection letters are not akin legally to FDA “approvals” or “clearances” for the recycling process or polymer described in the filing. That said, FDA does not have a dedicated premarket review clearance process that can be used for recycled polymers, so the no objection letter filing route is the best option for companies looking to obtain some form of concurrence from the agency that their processes or polymers are acceptable for use in food packaging applications. An inventory of FDA no objection letters is available at http://bit.ly/FDAno-objection-letters.
Relevance of FDA’s criteria for recycled plastic used in nonfood-contact applications. The discussion above is geared toward recycled plastic intended for use in food-contact applications, but companies that make packaging or components of products that are highly regulated or that are otherwise intended for use in close contact with humans (e.g., cosmetics) can borrow from these concepts. Specifically, the fundamental concepts used by FDA to ensure the safety of recycled plastic, including source control and sorting and analysis of a recycling process’ ability to remove potential contaminants, also can provide assurances for other companies in the CPG realm. Of course, the target contaminant levels used by FDA might not be appropriate for those other applications, as different toxicological concerns can exist, depending on the product in question. For example, while oral toxicity is the focus of a food-contact safety assessment, dermal toxicity is likely to be a more relevant safety consideration for cosmetics.
Other practical considerations
Source control and sorting are important issues for recycled plastics used in food-contact applications, but the current system is not necessarily designed to facilitate use of recycled plastic in food-contact applications. Many material recovery facilities are equipped to separate PET and high-density polyethylene from other polymers using resin identification codes (RIC), density sorting, froth-flotation methods, near-infrared sorting, laser-aided identification, X-ray fluorescence or some combination of these technologies. But the existence of these technologies does not necessarily mean they are used to separate other polymer types from one another, as economic conditions do not currently incentivize separation of polymers with higher RIC numbers and available sorting technologies do not necessarily work equally well on all polymers. Further, some recycled polymers might not be well-suited for use in food-contact applications because their technical properties are compromised through recycling.
These issues highlight the potential benefits of sourcing recycled plastic using a closed-loop system or using a dual-stream system where consumers engage in some level of sorting prior to collection by a waste hauler, but these alternatives are not necessarily easy to implement. For these reasons, the policy debate surrounding potential changes to our nation’s recycling system should consider the somewhat unique challenges posed by using recycled plastic in food-contact applications.
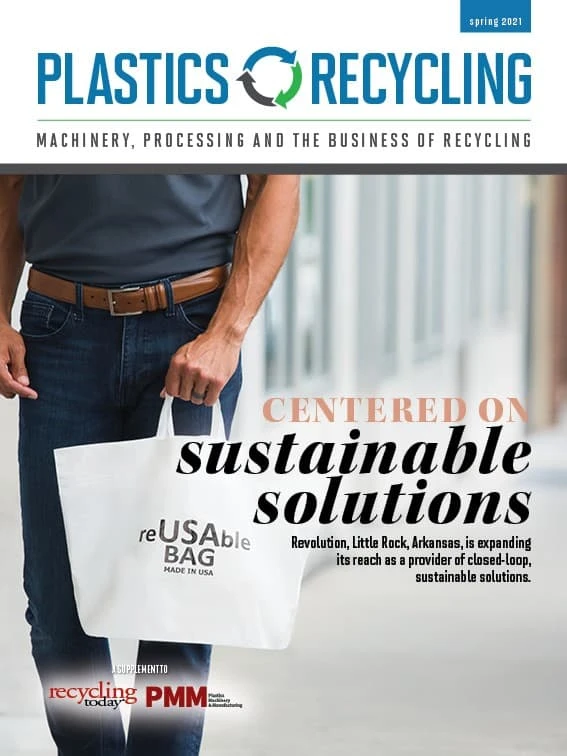
Explore the Spring 2021 Plastics Recycling Issue
Check out more from this issue and find your next story to read.
Latest from Recycling Today
- Recycled steel price crosses $500 per ton threshold
- Smithers report looks at PCR plastic’s near-term prospects
- Plastics association quantifies US-EU trade dispute impacts
- Nucor expects slimmer profits in early 2025
- CP Group announces new senior vice president
- APR publishes Design Guide in French
- AmSty recorded first sales of PolyRenew Styrene in 2024
- PRE says EU’s plastic recycling industry at a breaking point