
Worse than a winter flu is the sickening feeling a recycler gets when a bale of aluminum is rejected by a consuming customer for not meeting specifications.
Jeff Arrow, vice president of purchasing at TST/Timco, a vertically integrated producer, buyer, trader and processor of aluminum scrap and dross based in Fontana, California, says his company might have to reject 1 load in 25 or 1 in 50. “Not every dealer can produce perfect segregation,” he says.
“Especially with the high-volume dealers, stuff gets missed,” says Eric Phillips, a trader with Kripke Enterprises, a nonferrous scrap metals brokerage firm based in Toledo, Ohio.
That said, Phillips says he finds that rejection rates are low. “Our customers do a phenomenal job getting it right,” he says. “They take pride in their work.”
The best way to avoid the pain of rejection and the associated costs are to have a healthy certainty as to what that bale of aluminum contains before it leaves the yard. In addition to acid tests and other identification methods, recyclers can employ hand-held analyzers to help avoid such costly mistakes.
“The handheld is best applied to the high-value alloys to quickly determine grade and, therefore, value,” says Jim Pasmore of Analytical Sales Training Inc., Bend, Oregon. He notes that this knowledge allows the recycler to buy at the correct price and, with existing inventory, to upgrade its value prior to selling.
However, “Low value or small parts (drill bits, etc.) may not warrant the cost and use of the handheld,” Pasmore says. He says these items can be sorted using traditional techniques into generic batches with similar families of alloys consolidated for average elemental (intrinsic value) instead of by specific grades with exact elemental content.
“Not everyone can afford a gun,” Arrow says of hand-held analytical devices.
While he says analyzers offer benefits, recyclers can take other steps to assure they are delivering an on-spec load of aluminum to buyers.
Back to basics
A recycler’s first line of defense against improperly sorted aluminum is at the scale. A lot of aluminum is painted, making it difficult to discern quickly. And quick is a key. One good way to lose customers is to have the word spread that scale waiting time is long at a yard.
“First of all, have a magnet,” Arrow says. “Be sure the metal is not iron.”
Arrow, who has spoken on the topic at Institute of Scrap Recycling Industries (ISRI) conferences, is a believer in using multiple tools, some of which are as basic as examining the look and color of the metal, noting its weight and looking for any identifying markings. Acid testing also can be employed.
“Look for mill markings or stampings,” Pasmore also suggests, noting that mislabeling is rare.
“Shape and application can be a great indicator of the grade for which the part was used,” he adds. For example, car wheels are usually aluminum alloy 356; cylinder heads, engine blocks and gear boxes are typically cast alloys (300 series); truck wheels commonly are 6061; beverage cans usually are aluminum alloys 3004/3104; structural material and extrusions, such as window frames, typically are 6061/6063; and electrical products, such as wire and coils, tend to be in the 1000/1100 series.
While it might seem a no-brainer that a soda can will be aluminum, other materials can show up at the scale painted or unpainted, in small loads or big ones. Many clues become second nature to an experienced scale operator. Weight can be a big tip-off. Magnesium is lighter than aluminum and both are much lighter than steel.
The material’s color also can help with sorting, though Pasmore says this can be a subjective indicator.
“If painted, anodized or oxidized, then it must be ground or filed,” he adds.
Arrow suggests, “Look at the flexibility of the material.”
Recyclers can check the material’s physical properties by bending thinner pieces or scratching them. Aluminum in the 1000 series, 7000 series, cast aluminum or 4000 series is brittle because of its high silicon content. Metal in the 5000 series will have less corrosion because of its high magnesium content. Softeners include zinc and copper; hardeners are magnesium, chrome, silicon and iron.
Hand-held analyzers are a big help. However, Arrow says that while they offer benefits, not every operation can afford one. That means falling back on the traditional lines of identification.
However, Pasmore advises using a hand-held alloy analyzer, if available, for best identifying aluminum alloys.
“Even though the hand-held analyzers are the best ID tool in the sorters’ arsenal of sorting methods, any sorter should be conversant with all the techniques so as to minimize time required to sort effectively when the handheld is not with him/her,” he says.
Sometimes these ID methods can be one of the traditional sorting methods mentioned previously or a combination of these methods. “This approach can sometimes provide an immediate on-site answer without going for the hand-held analyzer, which may be in use or not easily available,” Pasmore adds.
In his ISRI seminars, Arrow gives attendees samples of acids that will help determine whether a piece of metal is high or low in zinc.
Pasmore also recommends chemical spot testing. “The attack of acids will determine the presence or absence of specific elements,” he says. One drop of Timco Zinc Test Solution on a clean surface can reveal a lot. For instance:
- If the metal is high in zinc, it will turn gray to black.
- If the metal is zinc die cast, it will turn black.
- If the metal contains magnesium, the solution will boil rapidly.
Another physical test involves a grinder. “Stick an unknown piece of metal on a grinder,” Pasmore says. “Aluminum doesn’t spark with a grinder.”
To assist in future identification tasks, Arrow suggests building a library of samples. This involves designating a convenient spot in the yard where samples of various materials are available for reference. Using a piece of wire, recyclers can attach a label to the sample identifying the metal’s chemistry and relevant identification clues.
An analyzer assist
When it comes to hand-held analyzers, some units are better at identifying stainless steel than at identifying aluminum. Before going shopping, recyclers should know what they intend to use the analyzer for, sources suggest.
The old mantra about buying the best tool you can find applies. “You are only as good as your tools,” Phillips says.
To that end, he advises recycling yards to be sure to demo any tool at length in their own facilities, “not on the convention floor.”
Two technologies are commonly used today for sorting aluminum alloys. Most dealers have the older technology, XRF (X-ray fluorescence), which Pasmore says may not be optimal for identifying aluminum alloys.

The newer technology, LIBS (laser induced breakdown spectroscopy), offers greater accuracy for light metals, he says. It also may be able to do the job faster. These factors mean that LIBS analyzers potentially can increase a recycler’s profitability and minimize mistakes and penalties associated with rejected loads of aluminum, Pasmore adds.
However, Phillips cautions that some LIBS analyzers may not be as accurate as other units. “LIBS are the most hassle free and are more durable than other analyzers,” he says. “But they are not as accurate.”
All analyzers feature a library of alloying elements that will react to each shot and tell the user what its best guess is to the composition of the material.
However, Phillips cautions, if an analyzer’s library does not include the appropriate alloys, it cannot be expected to give accurate results.
Keeping the analyzer’s alloy library up to date, therefore, is key to ensuring accurate identification, he says. “All the guns are error-prone if you don’t have the library updated.”
When shopping for a hand-held analyzer, sources suggest selecting a lightweight unit—one that weighs less than 4 pounds. Remember, the operator is going to be lugging it around for a while.
Battery life is an important consideration, as well. Apart from analysis errors, nothing is worse than having a unit fade before a shift is completed. A good unit should provide at least 10 hours of battery life on a single charge, sources say.
The readout screen should be large enough and bright enough to read without causing eye strain.
While XRF units are known for their accuracy, most of them employ radioactive sources and require that recyclers perform radiation dose tracking and maintain health logs.
“Mobile sparkies are not as accurate, but you don’t need to mess with the health department,” Phillips says, referring to analyzers that use optical emission spectroscopy (arc spark OES or spark OES). With this technology, sample material is vaporized by an arc spark discharge, with the spectrometer reading the emissions.
LIBS units tend to be quite focused in terms of sample area—down in the 50-micrometer range. For this reason, when using a laser device, several spots should be tested and averaged. This is especially true for aluminum alloys.
Rejection hurts
Whether it is in love or in aluminum marketing, rejection hurts.
If the consumer purchasing your scrap mixes high-alloy content with a heat intended for low-alloy content, the heat can be contaminated and may be ruined. Pasmore says, “In such a case the recycler would be penalized or removed from the supplier list.”
The most common mistake is when a segregated aluminum alloy is labeled as a mixed shipment. The mill often will reject such mislabeled shipments.
Unfortunately, when checking bales with their hand-held analyzers, many recyclers may take only five or six samples. The buyer needs better accuracy than that. In most cases, the buyer’s people know their chemistry inside and out. “If they find three little pieces in 10 shots, they will kick the whole bale out,” Phillips says.
When a bale is rejected, the recycler has a few options. One is to have his or her broker scout around for the best price from another buyer. The other option is to accept the rejection and reclaim the bale.
“As a broker, I have to do what is best for my customer,” Phillips says, adding, “I will present options with the least economic pain.”
On the upside, the mill typically will inform the shipper what the actual content of the bale is.
“A primary dealer will say one bad piece will reject a load,” Arrow says. A secondary dealer might not reject the load but probably will renegotiate the price.
When producing ingot for the automotive sector, TST/Timco has a bit more room for error, Arrow says. As long as there is no iron or stainless in the load, the company probably can handle it. A load with iron, however, will be rejected.
Adhering to specifications is much more critical at the company’s aerospace site. “We will reject anything that is not to specification,” he says.
The best screw-up is the one avoided. Having a well-trained staff and the proper equipment will cut a scrap processing company’s number of errors markedly. And that will be good for the company’s bottom line.
Get curated news on YOUR industry.
Enter your email to receive our newsletters.
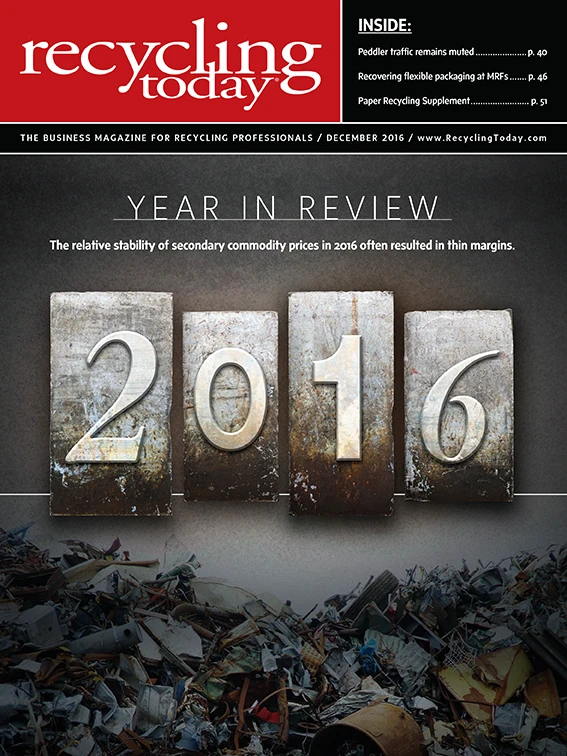
Explore the December 2016 Issue
Check out more from this issue and find your next story to read.
Latest from Recycling Today
- AF&PA report shows decrease in packaging paper shipments
- GreenMantra names new CEO
- Agilyx says Styrenyx technology reduces carbon footprint in styrene production
- SABIC’s Trucircle PE used for greenhouse roofing
- Hydro to add wire rod casthouse in Norway
- Hindalco to invest in copper, aluminum business in India
- Recycled steel price crosses $500 per ton threshold
- Smithers report looks at PCR plastic’s near-term prospects