SJF RECEIVES $2.25 MILLION
The Sustainable Jobs Fund (SJF), Durham, N.C., has received an award of $2.25 million from the Community Development Financial Institutions (CDFI) Fund of the U.S. Department of the Treasury.
The funding “will help us fulfill our mission of investing in sustainable businesses in the eastern U.S. that creates quality jobs for former low-income individuals in their neighborhoods,” says David Kirkpatrick, co-founder and a managing director of the fund.
Initial SJF investments include R24 Lumber, a scrap lumber remanufacturer in Charlotte, N.C., and EMPower Corp., an electric vehicle producer in Everett, Mass. The fund anticipates making six additional investments and business development grants in the fall of 1999.
Of the total CDFI award, $250,000 is an operating grant, and the remaining $2 million is an investment. The $250,000 has been fully matched by private foundation funds raised in conjunction with the National Recycling Coalition from the First Union Regional, Citicorp, Z. Smith Reynolds and Turner Foundations. These funds will be used to provide technical assistance to promising fund candidates and portfolio companies and to strengthen the community development impacts of the fund.
The $2 million from the CDFI Fund joins the existing $7 million in investments from MBNA America Bank (Delaware); Citibank, a member of Citigroup; the John D. and Catherine T. MacArthur Foundation; and the Dakota Foundation.
Subsequent awards are expected to bring the Sustainable Jobs Fund up to a total capitalization of $15 million by early 2000. The goal of the fund is to make about 35 investments over the ten-year life of the fund. After that, work will begin to find investors for a second Sustainable Jobs Fund.
CLEVELAND DIRECTORY PRINTED
The Cuyahoga County Solid Waste District, Cleveland, has put together a directory of financial and technical resources designed to assist area enterpreneurs interested in creating or expanding a recycling-based business.
The Resource Directory for Recycling Enterprises provides a list of more than 80 government financing programs, local business assistance programs, and recycling-related information sources.
The agency published the directory “to help facilitate local business development and expansion through the use of recyclable materials in Cuyahoga County,” says Diane Bickett of the Cuyahoga County Solid Waste District.
The directory’s introduction states that “developing local markets for recyclables is key to ensuring the long-term stability of recycling collection programs in Cuyahoga County.”
Among the financing options listed in the directory are bonds, “brownfield” incentives, grants, loans, tax incentives and venture capital.
FUEL PELLETS COULD HELP REDUCE TRASH
Landfill tonnage could drop by as much as 50% at a Medina, Ohio, facility due to trash being turned into fuel pellets. The pellets are made of paper and plastic that can not be recovered by traditional recycling methods and are typically landfilled instead of recycled. The paper and plastic will be shredded and molded into the fuel pellets, which are then used by power company Ohio Edison.
The pellets, known as refuse derived fuel (RDF), are mixed with coal at a 90% to 10% pellet ratio. The pellets will be made and used at Ohio Edison’s Niles, Ohio, plant pending completion of the air pollution control permit process.
In 1992, the $8.2 million central processing facility was built in Medina and fuel pellets were part of the plan, but it has taken seven years for that goal to become a reality.
A long permitting process by the Ohio Environmental Protection Agency was one reason for the delay. Concerns about the safety of the process may have contributed to that delay.
Unlike previous fuel derived operations, which burned everything that fit through the shredder—plastic, UBCs and organic materials—only paper and plastic film will be used to make the pellets, according to the project’s backers.
The change to using pellets could result in 150 tons of trash being diverted from landfills, which would mean that about 60% of what arrives at the Niles facility is being recycled.
SOLID WASTE FURNACE SLAG RECYCLED INTO ASPHALT
A method has been developed by Ishikawajima-Harima Heavy Industries Co., Tokyo, to reuse slag produced in waste-processing gasification fusion furnaces by crushing the material and mixing it with asphalt paving.
The system uses a crusher to pulverize the slag into small particles about two millimeters in size. The crushed slag is used in place of sand and added to the asphalt paving. Recycling the slag is expected to cost less than the its most common disposal method—burying it.
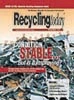
Explore the November 1999 Issue
Check out more from this issue and find your next story to read.
Latest from Recycling Today
- Fitch Ratings sees reasons for steel optimism in 2025
- P+PB adds new board members
- BlueScope, BHP & Rio Tinto select site for electric smelting furnace pilot plant
- Magnomer joins Canada Plastics Pact
- Out of touch with reality
- Electra names new CFO
- WM of Pennsylvania awarded RNG vehicle funding
- Nucor receives West Virginia funding assist