While there is some variation depending on the size of the facility and the population served, material recovery facilities in general appear to be going more to private ownership and are tending to increase the use of automatic sep-aration equipment, where feasible. One new technology involves a device to automatically sort corrugated cardboard from mixed paper. In addition, some paper recyclers are stepping up their acquisition of both MRFs and paper processing facilities.
Weyerhaeuser, for example, is currently in “an aggressive growth pattern,” says Jason Plut, spokesperson for Weyerhaeuser Co., Federal Way, Wash. “Many of the facilities we acquire handle glass, plastic and aluminum, but I like to make the distinction that we are not in the business of recycling those ourselves – we make them available to other people and we remanufacture the paper.”
Weyerhaeuser does not use any automatic paper sorting equipment, says Plut, but would certainly investigate the possibility of more automation in the future.
“Our plants are traditional, with a sort belt, a sorting line where people pull the different grades out,” he says. “It’s still labor intensive. We would go to a higher-tech system – we’re always looking at new technology and trying to improve our process.”
The company is mainly interested in acquiring paper recycling facilities, but will be flexible if other opportunities present themselves, says Plut. For example, Weyerhaeuser acquired a number of Alcoa’s aluminum processing facilities in areas where paper could easily be added to an existing collection and processing infrastructure.
PAPER SEPARATION |
One company that is very excited about automatic paper separation technology is Laidlaw Waste Systems, Hurst, Texas, according to Roy Dooley, market recycling manager for Laidlaw’s Dallas and Fort Worth recycling facilities. “In the three facilities I oversee, we have three automatic paper sorting systems,” says Dooley. “They are working well, and I am modifying them so they’ll work even better. I also designed my own disk screen system.” Laidlaw’s Dallas plant processes mostly fiber, as well as some commingled containers from blue bag programs, which is sent to other Laidlaw recycling plants. Automation is important in this plant, he says, as it saves labor costs. “The only problem with the paper sorting system is that film plastic wraps around the disk screens, so you have to cut it out every now and then,” says Dooley. “We capture everything that falls through the screen and re-sort it, so there’s no loss. Trash is handpicked off. If 60 percent of the feedstream is OCC, and 40 percent is trash, we reverse the conveyor and send it to a dumpster. If the feedstream consists of OCC and mixed paper, we send the conveyor the other way to sort the office paper.” The sorting system Laidlaw uses consists of numerous shafts that run across the conveyor belt. Several 72-inch-long disks are welded to shafts, spaced 10 inches apart. “The corrugated goes over the top to be sorted, then two men do quality control,” Dooley explains. “What you get off the end of the screen is about 90 percent pure OCC, and the rest is sorted out. Without the system, you’d have to hand pick every bit of office paper out of the stream, as corrugated mills don’t want the mixed paper. When you hand pick, you have to run the conveyor two or three feet, stop, sort, and keep repeating that – the production per man hour kills you. It’s less than a quarter ton per hour, whereas ours can go 20 tons per hour.” |
PRIVATE MRFS
As recycling becomes an increasingly central part of municipalities’ waste handling strategies, private companies and traditional waste haulers are making sure to have part of the action. For example, WMX Technologies Inc., Oak Brook, Ill., has made several acquisitions of recycling companies this year, including Resource Recycling Technologies and CRInc, according to Laura Fields, manager of media relations for WMX.
“We now own and operate 160 MRFs throughout North America, and that does not include our international offering,” says Fields. “We operate more facilities than anyone else.”
Privately-owned MRFs are the way of the future, according to Jeff Young, senior vice president of operations for RRT. “You really see the typical municipal bids falling off – private companies are building the MRFs. Even in municipal bids, they are looking for the private entity to provide the capital and operate the facility.”
RRT has been a pioneer in automating MRFs. In its facilities, an average of 75 percent to 80 percent of materials in a commingled container stream are not physically handled, says Young. In addition, the company’s Philadelphia paper plant, scheduled to start up this month, may be “the highest-tech paper facility in the country,” he says.
“We’ll be doing automatic separation of multiple grades of both low- and high-grade paper,” says Young. “It’s designed to achieve upwards of 85 percent efficiency on each entity that it sorts. It will process 250 to 300 tons per day on a single shift, depending on the mix. That’s based on a predominantly office paper mix. If we were in the lower grades like corrugated and news, then we’d have a higher throughput.”
The facility has two lines, one that runs at 30 tons per hour, and another at 15, so the overall capacity is 45 tons per hour. Its automated paper separation system consists of a series of rotary screening devices, and air separation by size and density, according to Young, along with some proprietary elements.
WMX is also installing an optical glass sorting system in CRInc’s Rhode Island facility that will color-separate mixed broken glass.
“That will be a big item of revenue, since mixed broken glass at best is worthless,” says Young. “We will take a portion of the mixed glass and turn it back into usable cullet, as opposed to its current uses as aggregate, landfill cover and pipe bedding. We normally have to hustle to find a place to market mixed cullet, which we do at all our MRFs. It usually has a value somewhere between minus $5 and $5, and if you can bring it up so that at least a portion of it can be worth $30 or $40 a ton, that’s a major accomplishment for MRFs.”
Plastic sorters tend to work well, but at a slow speed, according to Young, so more of them may be seen in the MRF of the future.
In terms of other future automation, Young says the limit has almost been reached. “If you got the plastic done, on the commingled container side you’d be left with quality control and glass sorting. You’re never going to give up your Q.C. and your gross contamination people.”
RRT will install more such paper sortation systems in other plants if the need is there, says Young, depending on what happens with paper programs and the market. But another trend may be that mills change the definition of their grades and become able to accept more contaminants.
“For instance, Bowater in their Maine facility have what they call a Maine Pack, where they have a very plastic-tolerant system for deinking newsprint,” he explains. “They’re accepting a product up there that allows newspaper, junk mail, magazines and phone books. All they want out is brown paper and chip board. Frankly, if the news manufacturers go in that direction, no one’s going to put in the tech-nology to do the separating. On the commercial high grade side, that’s where systems like the one we’re putting in at our Philadelphia facility will make sense, and there the question will be whether you have the tonnage source.”
Almost every curbside recycling program in the country will eventually start collecting residential paper, says Young. “That’s where the decision will be made as to one of three options: whether you upgrade systems to do what we’re talking about; the mills that deink for pulp, they’ll upgrade their technology so they can handle the contaminants in the grade, and so the specifications for a #8 news will actually change; or the facilities will drop down to making a #6 news, and that’s going to depend on the economics that the board mills put out there.”
This is unlikely to happen, he adds, because all the new mills that have the capacity to use deinked newspaper are not going to let their supply vanish. “I think they’re going to get scared of that, though, and they’ll try to upgrade their technology,” says Young. “If Bowater can do this in Maine, that means it’s possible, and if it’s possible then other mills can do it.”
NEW OCC SORT TECHNOLOGY |
One company that manufactures a system to automatically sort OCC from office paper is Bulk Handling Systems Inc., Eugene, Ore. “It’s a patented product, with patented disk shapes,” explains Sean Austin, sales representative at Bulk Hand-ling. “It creates a lot of agitation that releases the office paper through the screen, and the OCC is carried over the top. It’s fed from the end by an in-feed conveyor, and then usually there’s a quality control station before the OCC is baled. Anything that’s not OCC gets picked off there.” After the OCC is sorted out, the office paper stream is either conveyed to bunkers or to a sorting line where the different paper grades are sorted. “This is a first line of defense, but it’s highly effective,” says Austin. “It saves a tremendous amount of labor.” The company offers several models, with the standard one capable of running at a speed of 15 tons per hour. But models are available at speeds from four tons to 25 tons per hour. “We’ve sold a total of 10 units so far, and there are four already in use,” says Austin. “There’s a good demand for it by MRFs, and anyone processing fiber. More automation may be the way of future. The first screen we installed replaced about eight workers. It did in half an hour what it normally took eight workers six hours to do. They were thrilled.” The cost of the OCC/paper separator depends on the size, says Austin, with the 25-ton-per-hour model costing in the six-figure range, and the smallest unit at about $45,000 to $50,000. Bulk Handling Systems also offers automated commingled plastic sort systems and bag openers. |
MAXIMIZING RECYCLING
Another private recycling company, Resource Recovery Systems Inc., Centerbrook, Conn., operates eight MRFs in the U.S., according to Elizabeth Karter, president.
Although RRS is a private company, Karter is interested in working closely with cities and holds waste reduction as a high priority. RRS will either own and operate a facility or merely contract to operate a facility owned by a city.
“We’ll do it either way, but what’s really important is that both a municipality and a region make a commitment to do recycling,” she says. “When that commitment is in place, who owns the facility doesn’t matter.”
In the spirit of maximizing recycling, RRS takes some less common materials in at least its Michigan MRFs, including all types of clean paper, textiles and all types of plastic bottles.
“One thing in recycling that is absolutely, 100 percent true is that supply drives demand,” she says. “If you don’t have it, you aren’t going to sell it. We’re working on test markets and trying to get people to use these materials. It’s a tiny fraction of the market compared to other materials we’ve added, such as paper milk cartons – we were one of the first companies in the country to add those on a full-scale curbside basis – and small household scrap metal.”
In the company’s Ann Arbor, Mich., MRF, some waste is sorted as well as commingled recyclables, says Karter. “The commercial garbage goes though a sorting line. And that’s good because we’re getting a lot of stuff out that was somehow missed. We have two sorting lines, the regular curbside collected material – both commercial and residential – and we have another sorting area that feeds a garbage compactor and goes off to a landfill when we’re done. But before it goes there, it goes through a series of sorting stations and magnets to make sure that anything that’s usable in there is getting pulled out, and that’s very effective.”
Even with workers sorting more materials manually at RRS MRFs than manual sorters at many other facilities, Karter says her operations are cost-effective because of the way RRS MRFs are designed. The key, she says, is having each person sort for more than one material at a time.
“Most people design the MRF so that a worker can only throw one or two items, which is crazy, because there might not be the one or two items, so then you have a dead hand sitting there doing nothing,” she says. “We design MRFs so that a person can throw several different items, which maximizes the chances of them having something to throw at all times, and also gives them the flexibility to pick more or less depending on their particular level of attention or capability at that moment. So, by having people be really flexible and back each other up, we’ve been able to add different items that are less prevalent in the waste stream and still maintain very efficient sorting.”
Despite the high degree of manual labor employed in RRS plants, Karter says she is very excited at the prospect of more improved technology for automating MRFs. “Labor is certainly a big cost in a MRF,” she admits.
“The key to being cost-effective with these technologies is the ability to run fast enough and accurately enough so that everything does not have to be inspected afterwards,” she says.
The author is editor of Recycling Today.
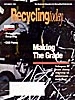
Explore the November 1995 Issue
Check out more from this issue and find your next story to read.
Latest from Recycling Today
- Indiana county awarded $65K recycling grant
- Mixed paper, OCC prices end year on downward trend
- Updated: CAA submits final draft program plan in Oregon
- Enviri names new president of Harsco Environmental business
- Survey outlines ‘monumental challenge’ of plastic packaging collection in UK
- Nippon Steel acknowledges delay in US Steel acquisition attempt
- BASF collaborates to study mechanical plastic recycling
- Commentary: navigating shipping regulations for end-of-life and damaged batteries