Some are operated by existing demolition contractors who see a way to expand their businesses. Others are run by landfill operators who realize they can save landfill space and make money processing and selling materials such as concrete and wood rather than burying them.
“You’re seeing more and more people getting into it (C&D recycling facilities), even in areas where landfill space is adequate and they shouldn’t have any problem, like Texas,” says Michael Taylor, executive director of the National Association of Demolition Contractors, Doylestown, Pa. “But what they’re discovering is, once they develop the system, markets grow, and the next thing you know, they’ve got a separate entity that sells recyclables.”
No one has yet done a study of how many mixed C&D debris processing facilities exist, but it is clear that the number is growing. Some facilities process a mix of materials such as wood, brick, concrete and sheetrock, producing several distinct marketable products.
Others mainly reduce concrete to a smaller size for sale as aggregate (see sidebar). While that is also an increasingly common type of recycling, it is not comparable to a MRF.
“I don’t know that anyone has a firm number on how many of these facilities exist,” says Taylor, “but there’s a number of things that lead me to believe there’s a lot of them. One is that the number and the viability of firms producing recycling equipment continues to grow. And obviously people aren’t buying these plants because they like the color of them – they’re buying them because they have a need and there’s a market.”
C&D recyclers are “coming out of the woodwork,” agrees Robert Brickner, senior vice president of Gershman, Brickner & Bratton Inc., Falls Church, Va. “There are more all the time.”
Taylor points to the increasing availability of small, mobile recycling plants as evidence that the technology is gaining acceptance among all sizes of processors. “Even the smallest guys are buying these plants,” he says.
Just as many curbside collection programs have found it to be more cost-effective to collect commingled materials rather than requiring source-separation, it is generally more cost-effective to operate a mixed-material C&D MRF than to source-separate all materials on the job site, which is labor-intensive, says Taylor.
Landfills containing only C&D debris have traditionally faced less stringent regulations than those governing municipal solid waste landfills. But recently, some states have been looking into regulating C&D monofills to a greater extent, which could be one of the motivations behind the increase in C&D MRFs. New York and New Jersey have already passed some increased regulations regarding the material, and states such as Maryland, Ohio and North Carolina are considering more defined C&D regulations, according to Taylor.
“The U.S. EPA was thinking of upgrading C&D landfills to Subtitle D status, but we were able to convince them with good hard data that basically a well-regulated, well-maintained C&D landfill is a good place for the industry’s waste,” he adds. “So I think the next battleground in this area is going to be in the individual states.”
GREAT OPPORTUNITY
Matthew Senior, general manager of the Epping Resource Recovery Facility, Epping, N.H., says he saw a great opportunity in his region for a mixed C&D recycling facility. “In our service territory there’s almost four times our permitted capacity of material available to process. And we are a very large facility – we are a 175,000-ton-per-year facility, which correlates into 675 tons per day. In the first few months of operation we’re already at half capacity.”
Senior agrees that his facility is similar to a municipal MRF, in that materials are brought in and then processes through a series of picking belts, conveyors, shredders and screens, along with water separation systems. “It’s much like a MRF in that it categorizes by size, and also has the human factor of some manual separation of material,” he says.
His facility produces a wood chip product for fuel, a mulch chip product for composting, an aggregate product for further crushing and recycling for road base and compaction material, and a dirt fines material which gets composted and turned into a loam product. About 15 percent of the material from the facility is metal, which is sold for scrap. The residue rate is only about 5 percent.
“We offer a much lower tipping fee than a landfill because there’s more up-front source-separation that needs to be done in order to make it acceptable here at our facility,” says Senior.
A landfill company that branched out into C&D recycling, attracted by the profit potential, is Modern Recycling Inc., Collier County, Fla., according to Brent Minet, project operations manager for Modern.
“We handle materials by the ton in Florida, so basically we get some of the gate money back, plus what we’re able to sell the product for,” says Minet. “We also get recycling credits for the material that is recycled.”
Some of the products produced in the C&D MRF are used at the adjoining landfill, replacing the need to purchase new materials, he adds. The fines are used for various applications – the one-inch minus material is used for daily landfill cover; and the three-inch minus aggregate material is used for building and repairing roads within the landfill.
“Then we have a couple of wood products that currently go to an energy plant as fuel,” he says. “We also have a magnet and capture a lot of steel, which is hauled away and sold on the scrap market; and corrugated cardboard we bale and sell.”
The Collier County C&D recycling facility handles about 90,000 tons of material annually, says Minet. Another interesting endeavor Modern Recycling took on was partial mining of the nearby landfill for usable wood and aggregate, a project which Minet says the company may continue in the future.
PORTABLE TO STATIONARY
Re-Tech, Myerstown, Pa., manufactures a range of equipment from the “entry-level, portable system” to elaborate stationary C&D separation and processing systems, according to Peter Logan, vice president of Re-Tech.
“The mobile systems would probably entail one of our portable, heavy-duty trommel screens to take out the dirt, because that’s sort of like entry-level C&D processing,” says Logan. “Just take the dirt out, and if you can defer that from a landfill situation, you can save 25 percent in tipping fees a lot of times. A lot of people do just that step.”
Re-Tech also has a portable line of picking stations that can plug onto the portable trommel and run as a system, says Logan, providing for a more complex sort. More people have portable rather than stationary equipment, according to Logan, because it is easier to get started with the portable processing and requires less permitting and less capital. But Re-Tech designs systems that can be added onto.
“We design our portable entry-level systems so that you can add onto them, so eventually you can make that as complex as you would like,” he says. “There are some limitations if you start out that way, but they’re not so drastic that they would really hurt you. We’re one of the only companies I know of right now that does it in a portable modular way.”
The company also offers the larger, stationary systems for mixed material processing. These would start with an initial screening of materials by size, and might incorporate grinding of the wood and the concrete, brick or block, along with other forms of processing.
“It may include air separation to separate the wood from the rock; it may include flotation to separate the wood from the rock using a water float tank,” says Logan. “It certainly would have magnets in it for pulling out metallics. Depending on the throughput we’re looking for, the types of end products we’re looking for, we would design a customized system for each individual project.”
The comparison to a municipal MRF is an apt one, says Logan. “It’s the same type of thing. We might go about it differently because it’s a different type of material. But the goals are all the same. It’s a series of different processing components that maybe fit in depending on the level of complexity that the owner may want to go with and the type of end products that he’s looking for.”
In the past few years, the company has installed at least 15 entry-level trommel picking systems, and about six of the complex systems, which are in the $2 million range, says Logan. In part, this is because of landfill restrictions and because C&D debris is becoming a more recognized commodity, with more markets available.
Hauling companies are the most likely to buy this type of plant, says Logan, although some demolition contractors get involved with C&D debris recycling. Landfill operators are also primary buyers of this type of system, adds Don Schendel, vice president and general manager of Grasan, Mansfield, Ohio, another producer of the mixed C&D processing equipment.
The Grasan system uses an impact crusher, self-cleaning magnets, conveyors with picking stations, vibrating screens and air separation.
“We’ve got a lot of interest in this system,” says Schendel. “We have about five out in operation now, and some of them are quite large. The interest is growing steadily in this kind of operation. Right now it’s mostly in the Eastern U.S. where landfills are filling up. The only problem material is wood. If they can find a market for wood, the system is usually justified.”
Whether or not people invest in a mobile of stationary system depends on the amount of material they have to process, he adds. “A portable plant can only handle so much tonnage per hour, and after that the equipment just gets too big to put on a mobile chassis.”
MORE MARKETS
Local markets for processed C&D materials (such as aggregate and wood chips) are developing, but not to the extent that the NADC would like, says Taylor. “It’s so dependent on what the market is and the location,” he says. “Markets are the biggest problem we have.”
The industry is developing increasing numbers of C&D MRFs, says Taylor, and he is confident that markets for the materials will continue to develop. “When you let people know you have material available, if you’re aggressive enough, markets will develop. It is the wave of the future. In Europe they’ve mandated C&D debris recycling, and here in the U.S. they’re letting market forces handle it.”
Despite his agreement that market forces can do the job, Taylor says a preference for recycled C&D materials in federal projects would provide a needed boost in marketing the materials.
“President Clinton mandated that by the end of his administration 60 percent of the paper that the federal government uses has to be recycled paper,” says Taylor. “That’s a huge push for the recycled paper industry, and it would be nice for constituents of C&D material – we’re not saying mandate it or compete with virgin, but look at it as an alternative thing to specify. If the government were address this, it would help the technology develop and the markets improve.”
There is still some resistance on the part of government officials – both state and federal – to using some recycled C&D material, says Taylor. “It’s a hard row to hoe,” he says, “but each little stride that we make is less stuff put in a hole in the ground.”
There is also resistance from the producers of raw materials, he adds, but this is really unnecessary as the quantity of recycled material produced would hardly make a dent in the virgin material side.
“I honestly believe that the impact the demolition debris, such as aggregate, for example, would have on the total aggregate industry would be minuscule – nobody would notice it,” says Taylor. “Nobody is looking for it to be top course and bearing course; you’re looking for it to be subbase and fill. There’s always going to be a huge market for virgin aggregate.”
Another factor spurring C&D recycling is the current public opinion against siting new landfills or other facilities – known as the “not in my back yard” syndrome.
“If these C&D landfills are constantly filling up and closing, you’re not going to be able to site new ones or expand them so you are going to have to re-use the material,” says Taylor, “or you’re going to have midnight dumpers.”
CRUSHING CONCRETE |
An activity that has been around far longer than sorting mixed C&D materials is the crushing of clean streams of concrete and asphalt for sale as aggregate or for use in recycled asphalt pavement. A company that produces crushing equipment this purpose is Cedarapids, Cedar Rapids, Iowa. Some of its products include jaw cone combination crushers and jaw impact crushers, says Dave McLaughlin, assistant sales manager for the company’s aggregate division. This type of equipment is currently very much in demand. “It’s the landfill problem, the scarcity of virgin aggregates in certain areas, and the acceptance of government people of recycled materials for their product mixes for concrete and asphalt pavement,” says McLaughlin. “Everyone wants recycled products.” Cedarapids has been producing this equipment for 18 years, according to McLaughlin. He says it used to be in greater demand in large metropolitan areas such as New York, Detroit or parts of California, where landfill space is particularly limited. “But lately everyone’s into it,” he says. “Whether you have a landfill problem or not, if there’s something to be crushed, somebody’s going to crush it and get a dollar out of it rather than throwing it into the landfill.” W. Hargrove Recycling Inc., Camden, N.J., a spin-off from a 30-year-old demolition firm, crushes clean concrete, brick, block and asphalt and sells the product, according to Kathleen Hargrove, president. The company, which produces 150,000 tons per year of finished product, is not likely to expand into sorting mixed C&D debris, says Hargrove. “There’s such a big market for what we’re doing now I don’t think we’ll have to. We may expand to processing wood in the future, but that would be a year or two down the road. Business is really good, and we think it will continue.” |
THE NEXT LEVEL
Currently, most C&D debris is only processed minimally and then is sold for low-value uses, such as concrete into aggregate or wood waste into wood chips for fuel or mulch. The next step in market development would be producing higher value end products, according to GBB’s Brickner.
“We’re looking at a wood study for Southeast Wisconsin to make panelboard out of C&D and other scrap wood waste in the region,” he says. “We’ll identify the technology, the economics, and how much material there is, and if it ends up looking good, the natural thing would be for someone to pick up on the paperwork and consider implementing something.”
One barrier to implementing higher value-added uses of wood material is the sheer effort it could require. Wood generators are eager to move the material, and if there are fuel or mulch outlets nearby, they don’t look for other markets, says Brickner – especially those that require a lot of permitting and development.
“If people have already sweated through developing a C&D facility, they want to do the marketing as expeditiously as possible to keep the material moving,” he explains. “But it’s time to start evaluating some higher uses of the material, to see what the economics are and try to push the envelope of technology end uses. So, instead of being put on the soil or used for energy content, we might be able to remanufacture that previously utilized material into something that will last another 20 or 30 years in another construction project.”
The author is editor of Recycling Today.
Last in a three-part series on construction and demolition debris recycling for 1995.
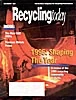
Explore the December 1995 Issue
Check out more from this issue and find your next story to read.
Latest from Recycling Today
- AF&PA releases 2023 paper recycling rate, unveils new methodology
- ARA names new president
- Aurubis invests in Lünen, Germany, site
- ILA, USMX negotiations break down
- Van Dyk hires plastics industry vet to expand footprint in PRF sector
- Li-Cycle closes $475M loan with DOE
- Report highlights consumer knowledge gaps in lithium battery recycling
- AMP names CEO