
A good example of this is flexible packaging. Over the past few decades, flexible packaging has offered more sustainability benefits than its more rigid counterparts because of its lightweight and its ability to protect products during shipment. Plastics have been a material choice when it comes to flexible packaging.
Even with all the sustainability benefits of flexible plastic packaging (FPP), the end-of-life stage remains a challenge because, today, FPP typically cannot be mechanically sorted in material recovery facilities (MRFs). So, in the United States, it ends up in landfills.
For consumers, the end-of-life stage of packaging is
As sustainability professionals, we know that plastics, including those used in FPP, have the potential to be recycled or converted into a wide range of other products—including durable goods, new packaging, composite lumber and fuels or feedstocks for manufacturing. Sending an item to a landfill means we lose that potential.
That is why several companies and trade organizations that are committed to increasing the sustainability of today’s packaging have come together to develop and test innovative processes that will expand end-of-life options for flexible packaging. They have formed the research collaborative Materials Recovery for the Future (MRFF), which is working to develop processes to efficiently and economically capture FPP for recycling using existing sorting equipment.
MRFF’s vision is simple yet important: FPP is recyclable, and the recovery community can capture value from it.
Why flexible plastic packaging?
FPP offers a wide range of sustainability benefits. From a life- cycle perspective, FPP uses fewer raw materials and has a smaller environmental footprint in manufacturing than many other types of packaging. It is lightweight, which reduces the amount of fuel needed to transport the goods contained in the packaging. This helps to lower greenhouse gas emissions. Yet, FPP is durable, which helps protect the products it contains. And FPP helps keep food fresher longer, leading to a decrease in food waste. Simply put, FPP allows us to do more with less.
FPP is not commonly recycled for a variety of reasons. Some FPP is made with multiple materials—such as those multilaminate pouches that contain food like tuna or nuts—and it is a challenge to separate these layers. Some FPP is made with just a single resin—such as the wrap around paper towels or cases of bottled water—but can get tangled in sorting equipment in many of today’s MRFs, damaging the equipment and causing downtime at the MRF. And some FPP—such as granola bar wrappers—is so small that it is a challenge to recover it at
Despite these challenges, reverting to older packaging choices is not a smart option; FPP has too many sustainability benefits that no other packaging type has.
Yet, we also know that we want FPP to be recycled—and to make it super easy for consumers, it needs to be recycled through their curbside collection programs.
Phase I research

From 2015 to 2016, MRFF funded the first round of research with Resource Recycling Systems (RRS), Ann Arbor, Michigan, as the technical research partner to find out whether FPP that is currently not recycled at MRFs could be separated in residential single-stream recycling facilities. Assessing whether FPP could be separated through single-stream recycling programs instead of in a separate stream (e.g., through retail takeback or a film-in-bag system) was important because it provided data pointing to the easiest option available for consumers to recycle FPP: curbside recycling.
The research focused on existing automated MRF sorting technologies, particularly optical sorters, separation screens and ballistic air separators. The MRFF collaborative wanted to find out if these existing technologies could be optimized to effectively sort FPP. Using existing equipment instead of introducing new equipment would make implementation of curbside-collected FPP sorting easier for MRFs.
The research also looked at additional technologies required for plastics reprocessing to align higher value mechanical recycling of resins with current end markets.
To measure sortation, the MRFF collaborative conducted flow studies, performing tests at three MRFs and five equipment labs (part of Phase II) to identify the adjustments necessary to optimize existing sorting equipment. The MRF tests seeded a representative mixture of preconsumer FPP in a manner that mimicked actual conditions into a standard single-stream material mix at these facilities. This mix included a wide variety of the most common forms of FPP, such as flexible pouches, chip bags, overwraps, food storage bags, laundry detergent pod bags, baby food pouches and pet food bags.
The baseline test found that the majority of FPP (88 percent by weight) flowed with the fiber stream, which matched the hypothesis for this test. After establishing the baseline, MRFF conducted additional flow studies to capture the FPP in the fiber stream. MRFF made modifications to the sorting equipment, including reducing loading on the optical sorters, increasing sorter belt width and adjusting targeted optical sorter programs.
As MRFF continued with its testing, it was able to capture more FPP from the fiber stream, reducing the amount of FPP in the fiber stream to 2 percent by weight. In doing so, MRFF created a new stream of material and significantly reduced contamination to an existing stream of material. (The reduction in contamination in the fiber stream to 2 percent by weight met the Institute of Scrap Recycling Industries [ISRI] specification for nonpaper in Grade 56 and Grade 58 residential paper coming from
The researchers concluded that existing optical sorting and MRF separating technology can be used to effectively and efficiently sort FPP in single-stream recycling.
More details about the research findings are available at http://bit.ly/2cwDxVw.
Phase II research
With the knowledge of how FPP flows through
In March 2017, MRFF, with the help of RRS as the research partner, solicited qualified MRFs to partner in this pilot project. MRFF developed specific criteria, available at http://bit.ly/2DEuj72, required for a potential MRF partner, including the amount of material coming into the MRF and the MRF and community’s interest in adding FPP to its incoming material stream. At the end of 2017, MRFF visited and discussed the pilot project with MRF finalists.
The results of the community pilot demonstration will be used to inform a
Recovering FPP at MRFs is just the first step in the process of diverting this material from landfills. In addition to preparing for the pilot, MRFF began to research additional components for recovering and recycling FPP. Some of MRFF’s additional components include:
rFlex bale characterization (http://bit.ly/2HJouIg) – Using the results of its flow studies, MRFF developed specs for this new FPPbale, or “rFlex” bale. The specs will inform potential buyers of the resin makeup of this new rFlex bale.- equipment testing (http://bit.ly/2Iz1RHy) – MRFF continued its equipment testing in Phase II to refine information on useful practices for capturing FPP at MRFs.
- end-market mapping (http://bit.ly/2GGHNlW) – MRFF conducted a survey of potential end markets for
an rFlex bale in the United States. These markets included recyclers and energy-recovery options, such as pyrolysis facilities and cement kilns. - economic modeling (http://bit.ly/2G3n7a5) – MRFF developed an economic modeling tool to assist MRFs interested in adding FPP to their incoming material streams. The tool allows MRFs to make more informed economic decisions on adding FPP.
Next steps

Today, MRFF is preparing to announce its pilot project partners. From there, the collaborative plans to use the findings from the pilot project to inform a guide for MRFs to follow to implement FPP recovery.
This work is incredibly important, and not just to the future of FPP. It is believed to be the first and only of its kind in North America. It has implications for recycling operations at MRFs, emerging end markets
For more information: Materials Recovery for the Future (MRFF), 202-249-6127, www.materialsrecoveryforthefuture.com
Get curated news on YOUR industry.
Enter your email to receive our newsletters.
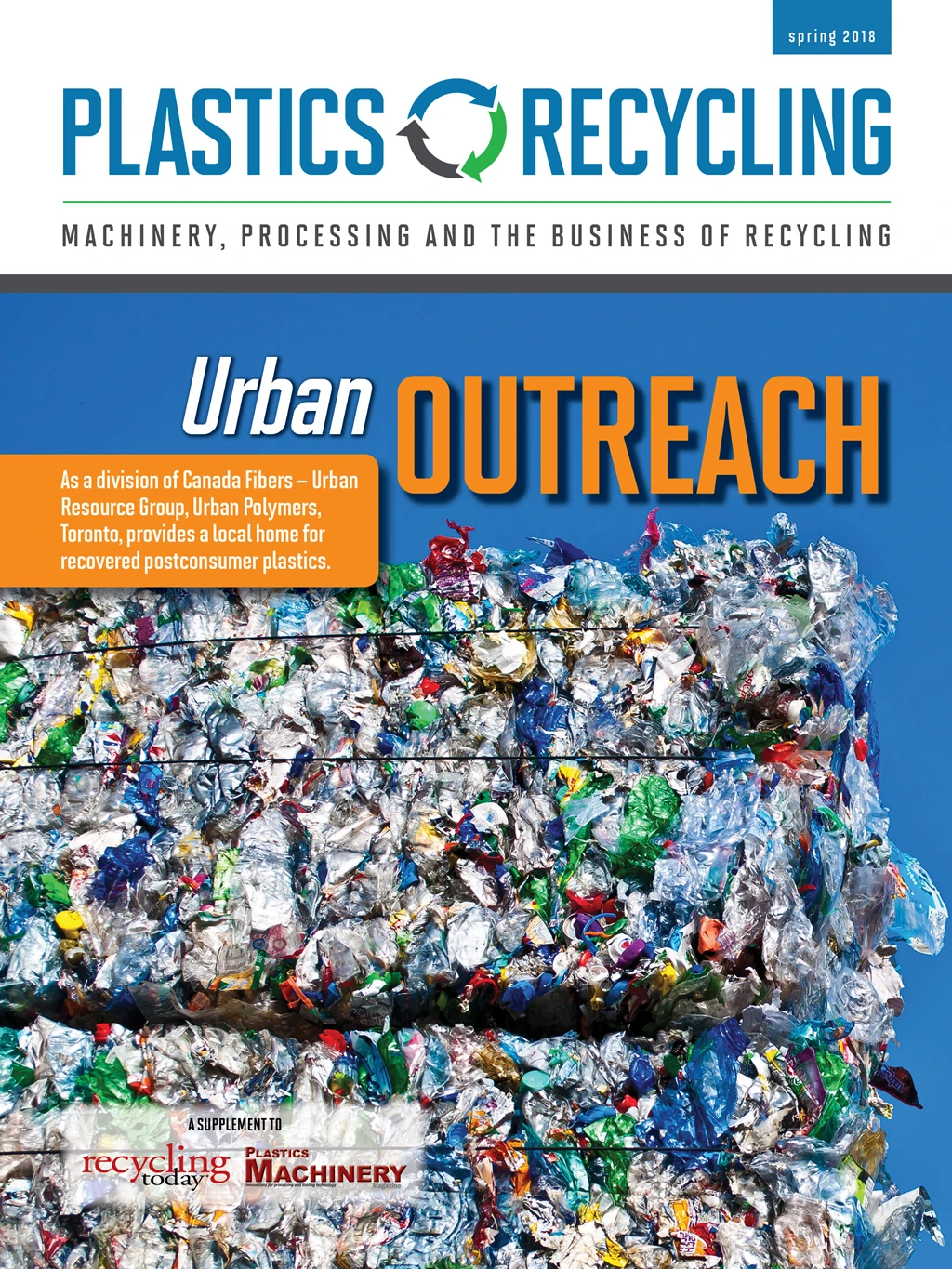
Explore the May 2018 Plastics Recycling Issue
Check out more from this issue and find your next story to read.
Latest from Recycling Today
- Aurubis CEO says its metals play vital role
- Steelmakers await impact of tariff policy
- Radius loses money, says merger on track
- Electrostatic technology vies for role in ASR sorting
- ReMA board to consider changes to residential dual-, single-stream MRF specifications
- Trump’s ‘liberation day’ results in retaliatory tariffs
- Commentary: Waste, CPG industries must lean into data to make sustainable packaging a reality
- DPI acquires Concept Plastics Co.