
Realizing the challenges that recovered glass creates for material recovery facilities (MRFs) throughout North America, Éco Entreprises Québec (ÉEQ) began a rigorous program in 2015 to identify superior processing technologies and to develop end markets in Quebec, Canada.
The organization did an exhaustive global search to identify the best processing technology available for glass, which led them to U.K.-based Krysteline Technologies. ÉEQ then selected Machinex (Plessisville, Quebec), who decided to partner with Krysteline to integrate the technology and deliver a complete solution in North America.
Delivering Clean Glass
Recovering MRF glass and converting it into a clean, salable product has been an ongoing challenge for MRF operators. This new partnership delivers a proven, cutting-edge solution.
The process is unique in that at its heart is a proprietary implosion technology that fragmentizes the glass, minimizing the fines associated with traditional pulverizing.
The system has the ability to create a clean material in both fine and coarse fraction. The purity is tremendous with the finer material being 99% glass and the course material delivering a 95% purity.

“Nonglass residue is just not an issue for us. The system has consistently delivered clean material that’s readily marketable,” says Jean-Sébastien Daigle,
Mixed MRF glass recovered in
The unique
The shockwave, which travels back and forth, causes
This method dramatically reduces maintenance costs and uses less energy than conventional processing. An added benefit is the edges of the treated glass are rounded, not sharp.
A Production Process
As material proceeds through the system, intense separation is conducted through a zig-zag separator, a flip-flow
The ÉEQ production process is designed in a modular fashion that allows Machinex to deliver glass processing production rates beginning at 1 ton per hour and exceeding 10 tons per hour. “We are ready to serve any MRF customer with this technology, regardless of their throughput,” says Chris Hawn, executive vice president of sales and business development at Machinex.
“We participate in a detailed implementation study with our customers to configure the system based
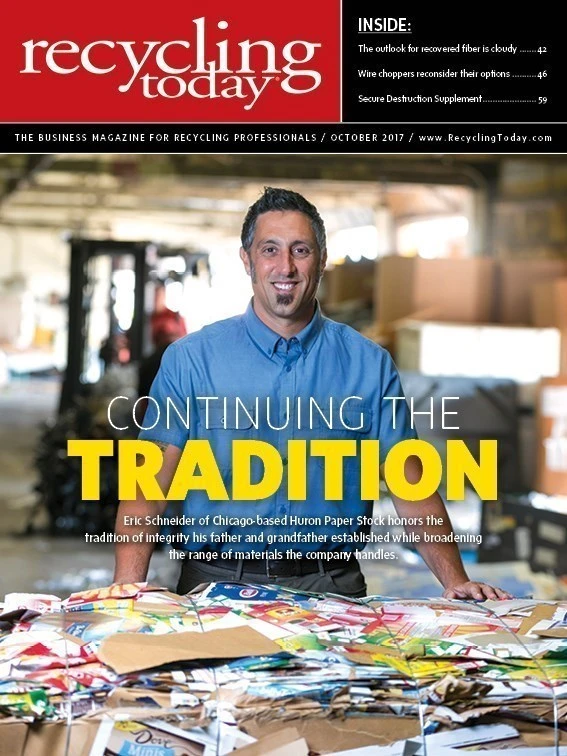
Explore the October 2017 Issue
Check out more from this issue and find your next story to read.
Latest from Recycling Today
- Acerinox names new North American Stainless CEO
- Greenwave closes 2024 books with red ink
- Steel Dynamics nets $217 million on record shipments
- Massive Chinese steelmaking rebound recorded in March
- LME looks into sustainable metal pricing
- OnePlanet Solar Recycling closes $7M seed financing round
- AMCS launches AMCS Platform Spring 2025 update
- Cyclic Materials to build rare earth recycling facility in Mesa, Arizona